随着SoC、Chiplet等技术的迅速发展和应用,贴片封装正在迈向“后摩尔时代”,焊接设备也由早期的回流焊一家独大,逐渐发展到气相焊、共晶炉、银烧结百花齐放。
相比之下,插件封装在近年来似乎没有太大的进展,封装尺寸并没有得到优化,焊接方式仍然停留在波峰焊为主,选择焊为辅的局面,仅在氮气保护方面稍有发展,难以进一步优化。
图1 Chiplet技术
与此同时,当前电子产品也越来越重视小型化多功能,为了提高元件密度,许多单面板和双面板都以表面贴装元器件(SMC/SMD)为主。
但是由于固有强度、可靠性和适用性等因素,在某些情况下,DIP元件仍然较贴片元件(SMC/SMD)具有优势,这种优势体现在连接器、电阻器、电感器等无源器件上更是无可取代的。
图2 插件式分立器件
在这种情况下,这些DIP元件因封装耐温等原因,为了避免元件主体遭受高温影响,只能采用波峰焊技术这种局部加热焊接技术。但有利也有弊,波峰焊存在着焊料损耗大,炉后不良率过高,焊接阴影效应等问题。
那么DIP元件的焊接有没有更优的方案呢?
小编认为应该还是有的,终究还得是回流焊!
回流焊在焊接贴片元件时,通常能将炉后不良率很好地控制在600PPM以内(波峰焊2000 ~ 5000 PPM),并且不受阴影效应所影响。所以自20世纪90年代开始,就不断有公司尝试使用回流焊技术进行DIP器件的焊接,但都因为元件本体不耐高温、回流焊炉腔隔热效果不好等原因,仅实现了部分耐温效果好的连接器焊接,而迟迟无法实现功率器件的焊接。
基于上述情况,金智为推出了针对所有通孔插装器件的专用回流焊--通孔回流焊,以便更好地满足客户生产需要。
本文将深入探讨通孔回流焊炉的特点,为您揭示这一卓越的焊接技术。
通孔回流焊(Through-hole Reflow Soldering)是一种使用回流焊接技术来装配通孔元件和异型元件的焊接工艺。首先通过印刷或喷涂的方式在焊盘上放置锡膏,然后将元件的引脚插入通孔中,再用热风吹拂,使焊料熔化,最后冷却使焊料固化,完成元件引脚与电路板之间的电气连接。
相较于传统波峰焊工艺,通孔回流焊具有以下优势:
1
炉后不良率低
通孔回流焊炉后DPMO能达到400~800PPM,相较于传统波峰焊的2000~5000PPM,不良率降低了80%以上。
2
元器件密度高
通孔回流焊工艺可以通过减少焊盘间距,进而缩小40%的PCB板面积,提高焊盘利用率,顺应电子产品小体积、高密度的发展趋势。
3
产品工艺性优秀
通孔回流焊延续了回流焊工艺性较好的优点,设计与回流焊要求基本一致,无需考虑阴影效应、盗锡焊盘等设计因素。降低了设计难度,提高了产品合格率。
图5 波峰焊工艺对PCB布局设计要求较高
5
治具设计简单
通孔回流焊的治具无需遮挡,设计简单通用性强,只要PCB尺寸相同即可兼容使用;而传统波峰焊即使PCB尺寸相同,还需进行掩膜版设计,使用的治具数量通常为通孔回流焊的2~3倍。使用通孔回流焊能够节省大量治具的费用。
6
辅料成本低
通孔回流焊仅需锡膏这一种辅料,相较普通波峰焊,焊接过程不会产生锡渣,无需喷涂助焊剂,并且无需使用红胶和洗板水,生产过程绿色环保。能减少整个制造流程将近50%的辅料成本。
图7 通孔回流焊和其他设备辅料成本对比
总结
展望未来,随着电子产品的功能日益丰富、性能不断提升,DIP器件的焊接方式也将持续创新和完善。一方面,随着环保意识的日益增强,绿色、环保的通孔回流焊工艺将成为发展趋势。另一方面,为了满足电子产品日益提高的集成度和性能要求,高精度、高效率的通孔回流焊将成为市场主流。
审核编辑:刘清
-
连接器
+关注
关注
98文章
14456浏览量
136402 -
DIP封装
+关注
关注
1文章
41浏览量
13606 -
SoC芯片
+关注
关注
1文章
610浏览量
34903 -
SMC
+关注
关注
2文章
85浏览量
20268 -
chiplet
+关注
关注
6文章
430浏览量
12582
原文标题:装配焊接新时代——DIP元件的更优选择
文章出处:【微信号:CEIA电子智造,微信公众号:CEIA电子智造】欢迎添加关注!文章转载请注明出处。
发布评论请先 登录
相关推荐
SMD与DIP元件的优缺点比较 SMD元件在LED灯具中的应用
PCB元件焊接的基本要点
如何选择合适的焊接方法
焊接方法选择指南
SMT元件焊接与维修:传统手工方法与激光技术的比较
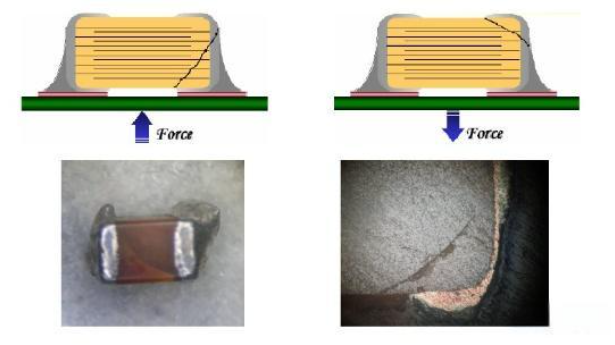
大研智造激光锡球焊接:攻克回流焊常见问题,定义PCB焊接新高度
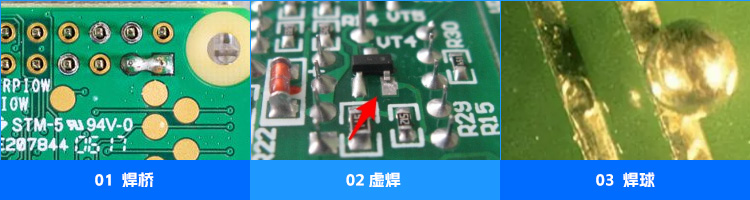
ESD对电子元件的影响 如何选择ESD保护元件?
光纤连续激光焊接机:焊接新时代的科技之光
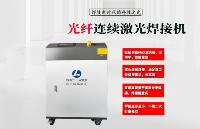
评论