作者:英飞凌半导体(深圳)有限公司:赵恺,张浩 ,苏州伟创电气科技股份有限公司:陈慧凯,何承曾,文章来源: 英飞凌工业半导体
原文发表于2021年电源学会第二十四届学术年会
摘 要:变频器在设计上不断的推陈出新,为了提高功率密度并降低成本,工程师更是绞尽脑汁。IGBT(绝缘栅型双极性晶体管)在变频器里属于关键器件,其选型和损耗直接关系散热器的大小,也直接影响着系统的性能、成本和尺寸。
本文从变频器的应用特点出发,结合第七代IGBT的低饱和压降和最大运行结温等特点,介绍了第七代IGBT如何助力变频器应用。
本文通过分析变频器的损耗组成,并通过热仿真对比第四代IGBT和第七代IGBT的性能,最后通过实验来验证结论。相同工况下IGBT7损耗和结温明显低于IGBT4,这样可以减小变频器的体积或是保持相同体积下增大输出电流,实现功率跳档,从而提高产品的功率密度。
1. 引言
电机在家电、传动、交通运输、新能源和工业机器人等行业有着非常广泛的应用。电机驱动着我们日常的工作和娱乐。低压变频器作为驱动电机的主要产品,因调速范围广、操作简单,能够实现节能、软起、提效等功能,应用非常广泛,如电梯、风机、水泵、纺织、冶金等行业。
2021年是“十四五”规划开局之年,中国敲定了碳中和的路线图,力争在2030年前达到二氧化碳排放峰值,2060年前实现碳中和。目前中国制造业正在开展新一轮转型升级,这对工业设备的性能提出了更高的要求,节能、绿色驱动的方式将成为主流,这又将推动变频器市场的增长,尤其是新一代更高功率密度的产品。
低压通用变频器市场竞争非常激烈,针对目前的市场需求,主要厂商加大研发投入降低产品成本、提升产品性能。而变频器电路拓扑主要采用交-直-交变频,电路拓扑固定,且发展相对缓慢。变频器产品的发展特点在硬件上就集中体现为减小尺寸、提高功率密度从而降低成本。
从硬件角度讲,低压通用变频器的特点主要有:
交-直-交:不控制整流+制动单元+三相逆变;
低开关频率:额定4KHz~6kHz,如提高开关频率会降额;
短时过载需求:150%过载/1分钟;
针对通用变频器的这些应用特点,英飞凌公司推出了第七代IGBT模块。那么第七代IGBT模块对比目前市场主要使用的第四代的IGBT模块在变频器应用中的优势体现在哪里呢?是如何做到提高功率密度的?本文将通过仿真和实验来探究。
2. IGBT7芯片技术
目前IGBT芯片技术已经发展到第七代的水平,以英飞凌的IGBT的芯片技术为例,从最开始的PT技术,到NPT平面栅,再到沟槽栅,现在到了第七代,也就是微沟槽栅(简称MPT,下同)技术。IGBT7采用了基于MPT的IGBT结构。在n-衬底的底部,通过p+掺杂实现了集电极区。在n-衬底和和p+之间,通过n+掺杂实现了场截止(FS)结构。它可以使电场急剧下降,同时会影响器件的静态和动态特性。
与IGBT4相区别的是,IGBT7里的沟槽除了包含常见的有缘栅极,还有发射极沟槽和伪栅极,后两种沟槽是无效沟槽。这三种沟槽单元类型能够精细化定制IGBT。通过增加有源栅极密度,能够增加单位芯片面积上的导电沟道。一方面,由于器件输出特性曲线更陡,可降低静态损耗[1][2] [3]。当然,带来的影响还有栅极-发射极电容(CGE)增加,代表着其开关参数也发生了变化。
图1.英飞凌芯片技术
到具体应用层面,IGBT7的优势总结为:
更低的导通饱和压降Vcesat;
最高短时工作结温可以到175℃;
针对电机驱动类应用的dv/dt特性优化;
3. IGBT7技术应用在变频器
IGBT7设计的初衷是针对电机驱动的应用。通过减少功率器件的总损耗和提高过载条件下的最高结温到175℃来提高功率密度、减少系统尺寸最终达到降低系统成本的目的。为什么IGBT7适合变频器应用呢?
1. 变频器应用中,一般情况下,额定开关频率范围4KHz~6KHz。在此工况下,总损耗中导通损耗占比最大。IGBT7通过降低Vcesat来减少导通损耗。从而达到降低总损耗的目的;
2. IGBT7支持最高175℃的运行结温,有效满足变频器过载的需求;
3. IGBT7 PIM模块集成有整流桥、制动单元和逆变桥,为变频器量身定做。
接下来,结合5.5KW变频器,通过仿真和实验来验证IGBT7在变频器应用中的优势。
首先我们可以通过仿真来评估IGBT7在变频器应用中的结温和损耗分布。PLECS涉及到电能转换系统的电气回路,磁性元件,散热回路和机械以及其控制部分可以提供快速的仿真。本文使用Icepak和PLECS混合热仿真实验,并计算损耗和结温。
图2.仿真和实验流程图
3.1. 建立PLECS器件模型
(1)双脉冲测试
虽然器件规格书上会有开关损耗的数据,但是母线电压、结温、主功率回路的杂散电感、门极回路的寄生电感和寄生电阻都会对开关损耗产生影响[4]。通过双脉冲测试可以得到IGBT7的开关损耗和二极管的反向恢复损耗。当然还可以得到各电压电流尖峰值,斜率变化值在内的动态参数。本次实验直接在整机的主功率电路板上做双脉冲测试,这样测得的数据更加符合实际。
本次测试选取了室温、35℃、75℃和125℃这四种不同的温度,得到IGBT7的关断损耗和开通损耗。因第七代IGBT使用了MPT技术,在维持较低dv/dt的情况下,驱动电阻可以选的更小[5],所以本次双脉冲测试驱动电阻(Rg)选取10欧姆和15欧姆,如图3和图4所示。
图3.Rg=15Ω时IGBT7关断损耗实测数据
图4.Rg=15Ω时IGBT7开通损耗实测数据
(2)创建器件模型
基于规格书的数据,将Vcesat与Ic(集电极电流)的输出特性曲线导入到PLECS器件模型里,再加上之前得到的开关损耗,就可以得到IGBT和反并联二极管的损耗模型。最后输入四阶的瞬态热阻,就可以得到IGBT7的PLECS热模型了,如图5所示。
图5.IGBT7器件模型
3.2. 3D和PLECS联合热仿真结果
采用3D和PLECS联合热仿真的目的是提高仿真结果的精度。IGBT和二极管芯片产生的绝大部分的热量通过图6中纵向的热阻传递到环境中;只有极少部分的热量横向传递,在本文中可以忽略不计。从热等效网络可见,Rth,c-h(散热器热阻,下同)的精度直接影响到IGBT芯片结温的估算。PLECS的优势是可以通过仿真得到损耗和芯片结温,而3D热仿真的优势是可以得到散热器热阻值。采用3D和PLECS联合热仿真的目的是提高仿真结果的精度。
图6.IGBT热等效网络
基于第七代IGBT FP25R12W2T7,使用PLECS仿真计算出损耗后,导入到3D热仿真可以得到散热器的热阻,再将散热器热阻导入到PLECS迭代后重新仿真,可以得到IGBT和二极管的晶圆的结温,具体结果请参见表1。表1和表2中“仿真模式”一列中的热阻指的是散热器热阻Rth,c-h。
仿真条件如下:
母线电压Vdc=540V;
调制比为1;
输出频率为50Hz;
散热器的时间常数为67s;
输出功率因数为0.85;
表1.IGBT7热仿真结果
接着再用相同的方法,针对25A的第四代IGBT FP25R12W2T4做仿真,得到其损耗。如下表2所示:
表2.IGBT4的热仿真结果
以上仿真均按照实际运行工况的运行参数,从仿真结果对比来看,相同工况下IGBT7的损耗明显低于IGBT4;并且随着电流的增加或开关频率的增加,损耗的差距越大,如表3所示。
表3.热仿真损耗对比
4. IGBT7和IGBT4在变频器应用中的性能对比
4.1 实验平台搭建
本文选用伟创AC310系列5.5KW变频器搭建测试平台。IGBT模块分别使用经过特殊处理的芯片粘有热电偶的第七代25A 的FP25R12W2T7和第四代同样是25A的FP25R12W2T4。因为两个模块是同封装同引脚,所以可以在相同的机器上测试;再加上这两个模块所粘温升线的芯片的位置相同,可以直接读出相同位置芯片上的结温,这样方便直接对比IGBT4和IGBT7的芯片结温。
图7.芯片粘有温升线的IGBT模块
对散热器进行打孔处理,分别在U相下桥IGBT、V相上桥二极管和整流桥二极管正下方打孔,将热电偶深入孔中,紧贴散热器基板侧面并与散热器表面齐平,用来测量散热器的温度。
图8.打孔散热器
4.2 实验结果
对应前文的仿真,在温升测试中仍然按照这四个工况测试:13A/2kHz、13A/4kHz、13A/6kHz和17A/2kHz。分别监测并记录:IGBT芯片的结温、U相下桥IGBT芯片正下方散热器温度,V相上桥二极管芯片正下方散热器温度和整流桥二极管芯片正下方散热器温度;监测记录输入电流;监测输出电流。记录并对比实验结果,如表4所示。
表4.IGBT7与IGBT4的热测试对比
4.3 实验结果分析
实验结果显示,IGBT7的芯片结温在相同工况下明显低于IGBT4;并且随着输出电流的增大,IGBT7和IGBT4的温升的差值在增加。从实验结果中还可以看到,随着开关频率的提高,IGBT7与IGBT4温升的差值也越来越大,这是因为目前工程师在使用IGBT4时,往往取的驱动电阻值较大,这一点从IGBT4的仿真结果就可以看出是一致的。
4.4 实验误差分析
本次实验两个模块同为热电偶模块,并且使用相同散热器。测试最终结果为其温升的差异,是相对值,这符合单变量原则。
但考虑到本次测试T7和T4模块都有内置热电偶,这是与标准模块的一个不同点;再加上散热器打孔,会增大散热器的热阻。这两点对于实验得出温度的绝对值的差异需要得到进一步探究。
设计如下两组实验来探究以上两点对温升绝对值的影响。
第一组:使用相同模块,不同散热器
表5.散热器误差对比测试
第二组:使用相同散热器,不同的模块
表6.模块误差对比测试
两组测试反应出随着工况的恶劣程度的加深,误差越大。这也解释了为什么随着损耗的增加,仿真得到的IGBT结温Tvj与实测得到的热电偶温度之间的差值越来越大。
4.5 设计总结
目前5.5KW变频器一般使用的是第四代35A IGBT模块如英飞凌的FP35R12W2T4,或类似电流等级和封装的其它模块。根据以上仿真和实验的验证,IGBT7可以从两个思路帮助变频器提高功率密度:其一,5.5KW变频器将模块更换为第七代同封装35A的IGBT模块,可以直接将5.5KW的变频器功率提到到7.5KW并保持整机尺寸不变,从而提高整机功率密度,相当于将功率密度提高40%~70%,如图9所示;其二,5.5KW变频器将第四代35A的Easy2B IGBT模块更换为体积更小的第七代25A的Easy1B模块,可以直接将变频器的外形尺寸降低25%~40%。
图9.IGBT7助力变频器功率跳档
5. 结论
通过一系列仿真和测试,可以明显的看到英飞凌第七代IGBT通过降低Vcesat来降低逆变器总损耗和降低芯片结温,在再加上可以做到最高到175℃的运行结温,这些给工程师带来了很大的设计裕量,从而助力变频器功率跳档。既可以通过减小变频器的尺寸,提高功率密度,降低成本;也可以保持原有变频器体积不变,增大输出电流,功率跳档从而达到提高功率密度、降低成本的目标。
参考文献
[1] Infineon AN2018-14 TRENCHSTOP™ 1200 V IGBT7 Application Note
[2] C. R. Mueller., “New 1200 V IGBT and Diode Technology with Improved Controllability for Superior Performance in Drives Application”, PCIM Europe, Nuremberg, Germany, 2018
[3] 论文|1200V IGBT7和Emcon7可控性更佳,助力提升变频器系统性能(上)?2019年2月19日
[4] 英飞凌工业半导体 双脉冲测试基础系列:为什么我测的损耗和规格书不一样?2021年4月22日
[5] 英飞凌工业半导体 突破—IGBT7的高功率密度设计实例, 2020年5月13日
[6] 伟创变频器官网
审核编辑 黄宇
-
芯片
+关注
关注
454文章
50677浏览量
423005 -
变频器
+关注
关注
251文章
6541浏览量
144493 -
IGBT
+关注
关注
1266文章
3786浏览量
248818
发布评论请先 登录
相关推荐
英飞凌推出基于1700 V TRENCHSTOP™ IGBT7芯片的EconoDUAL™ 3模块,大幅提升逆变器的功率密度
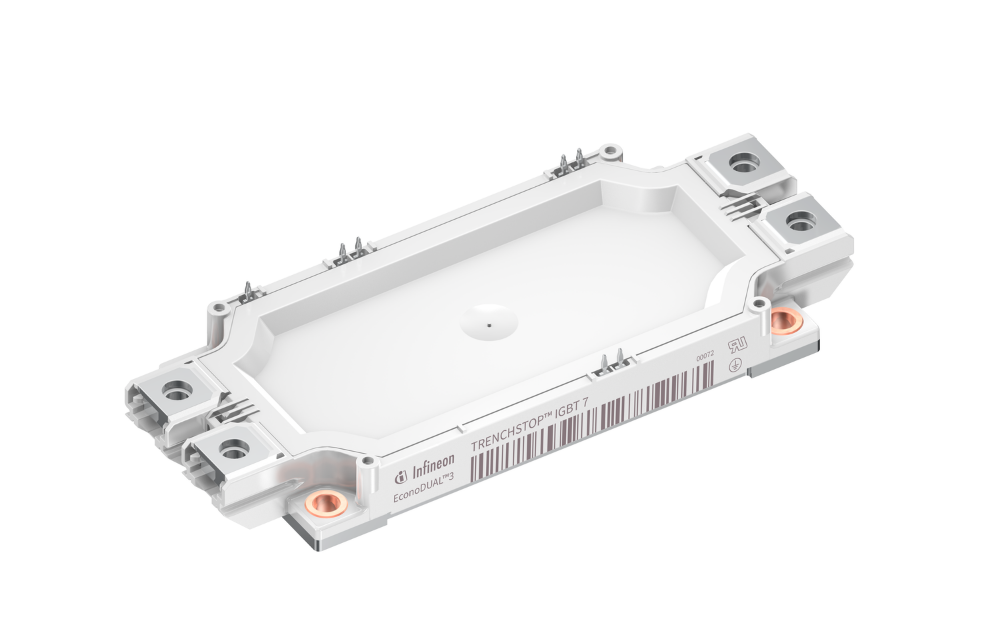
功率扩展:TRENCHSTOP™ IGBT7 Easy产品系列推出新的电流额定值模块
搭载1200V P7芯片的PrimePACK™刷新同封装功率密度
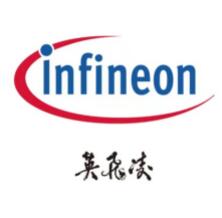
扩展 IGBT7 产品组合,实现bast-in-Class功率密度
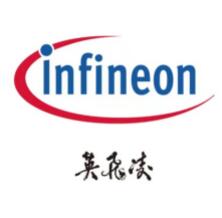
高压级联变频器和静止无功发生器
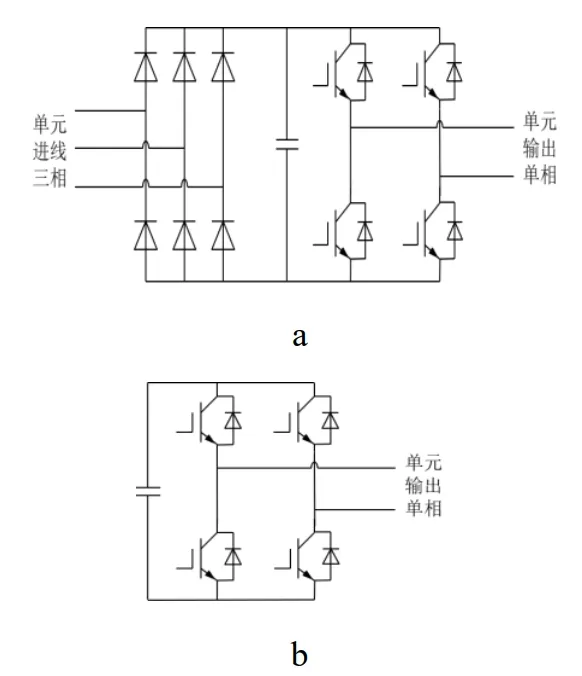
评论