正在被广泛使用的伺服技术使60年代的自动化工程师羡慕无比。这种体积小、精确且完全电动的技术反映了我们现在可以使用的半导体控制、传感器和电力技术的紧凑性。今天的最大挑战仍然是伺服和其控制器之间的布线。由于必须承受来自电机和控制信号的高电流,布线成本昂贵,且是电磁干扰(EMI)的重要源头。阻抗不匹配引发的反射波经常成为问题,对电机绕组的绝缘产生了破坏性压力。理想情况下,将驱动和控制器集成到伺服电机中将解决许多挑战。
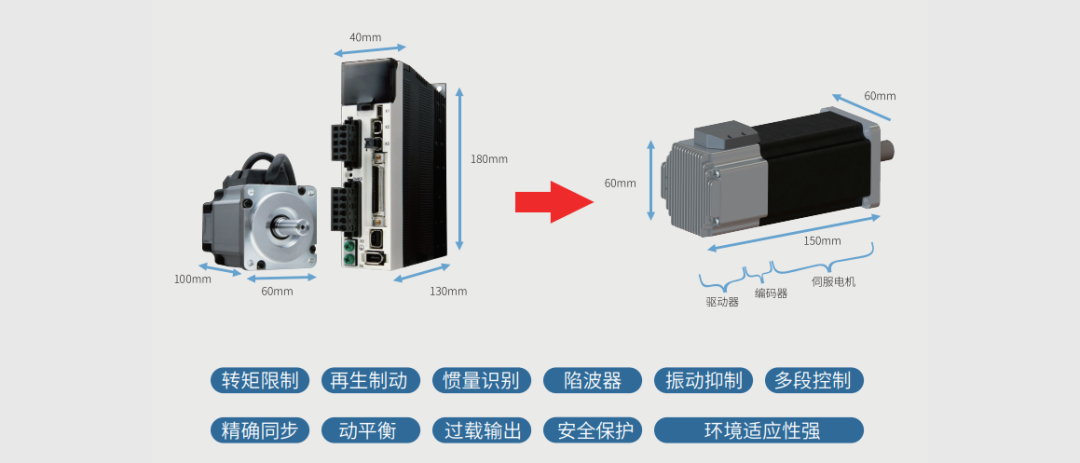
目前,硅基IGBT是伺服驱动电路的主流。随着制造商在近年来稳步降低损耗和寄生效应的影响,其出色的高电压性能得到了体现。另外,封装技术帮助减小了电路体积。然而,由于这些驱动系统必须处理200%甚至300%的超载条件,被动冷却和集成的基于IGBT的伺服电机仍然无法实现。
解决伺服驱动的挑战
引入宽禁带的SiC MOSFET,设计师现在可以将新工具应用到伺服驱动设计中。SiC MOSFET提供更高的工作温度,超越了IGBT,再加上更低的开关损耗和更高的源漏电压,它们对这种应用方面非常匹配。SiC MOSFET也可以从源引至漏极以非常低的电阻导电,允许使用节能的同步整流技术。
换用SiC还带来了一系列其他好处。发生的损失与温度关系不大,室温和175°C的操作条件之间的差别很小。由于dv/dt可以通过门电阻RG进行控制,电磁兼容性(EMC)更容易实现。这也开启了更高开关频率的大门。这允许将耗费大量空间的磁性组件进行缩小,并使伺服对动态负载变化的响应更快。相比于基于IGBT的设计,设计师可以降低操作温度高达40%,或者在相似的工作温度下提供65%更多的电力。
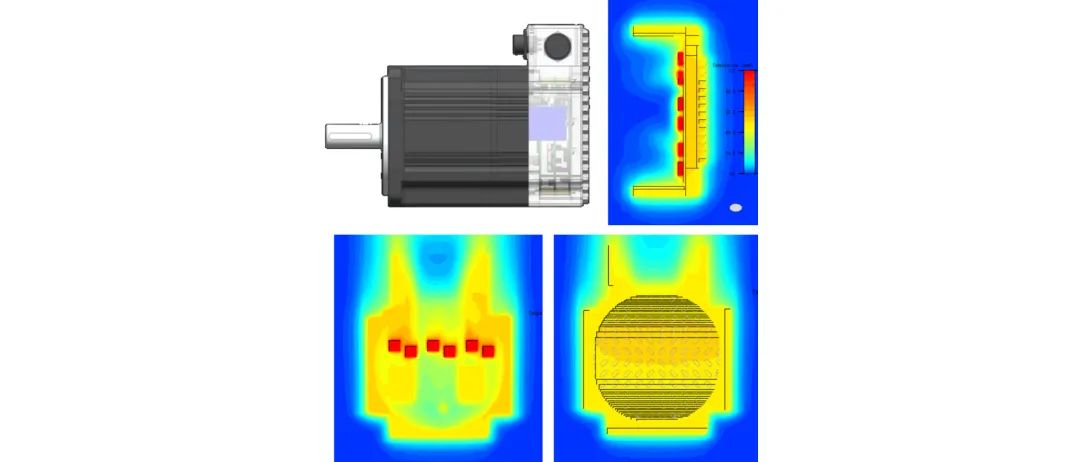
利用今天的金属核心印刷电路板(MCPCB)在集成伺服设计中,配合低损失的辅助电路和热导电环氧树脂,可以更简单地控制热挑战。热模拟显示,当使用300厘米²的齿背盖时,集成的SiC设计顶部温度只有113°C,后部保持在80°C以下。
全集成SiC的伺服
电源板被放置在最靠近外壳的位置,包装有助于设计的紧凑度和轻量化。包装包含一个Kelvin源引脚,可以用于实现EON损失的三倍降低。同时,扩散焊接方法也可以提供热阻的改善,优于在其他包装中使用的焊接工艺。堆栈的下一个板子承载驱动程序,要提供高达6A的典型峰值电流,满足使用的1200 V SiC MOSFET的需求。要使用无芯变压器实现电气隔离,也要集成Miller钳位来防止寄生接通。控制系统在最后一块板子上,并配备了DSP和MAC指令,要能应对三相电机控制算法和其数字反馈环的挑战。低延时通信总线的整合,同时使用各向异性磁阻(AMR)传感器获取转子位置,它的集成温度补偿功能,使伺服具有更高的精准度。
从600 V DC供电的评估集成伺服电机在测试条件下被证明是可靠的,这些测试条件使伺服在慢(150ms)和快(50ms)周期间加速到±1500 RPM。
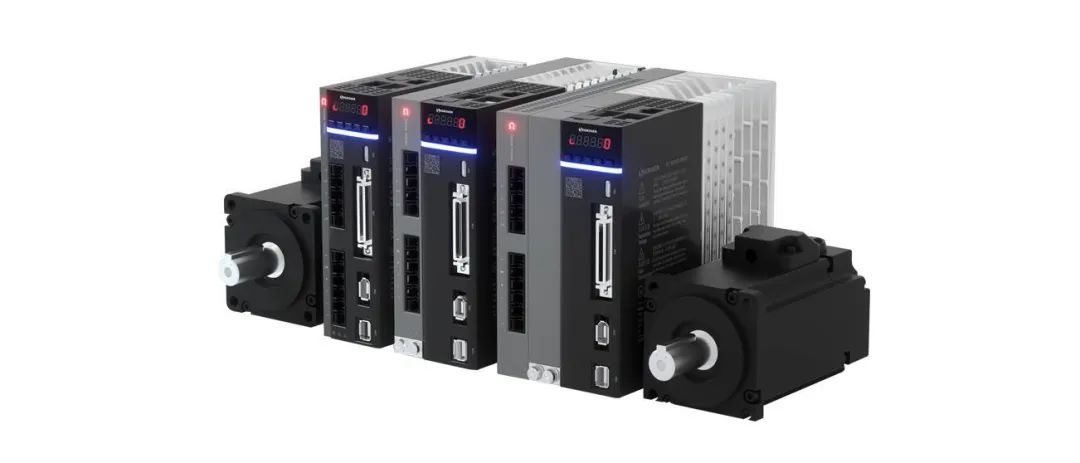
SiC的可用性让工程师们最后能将电机和驱动系统整合到一个解决方案中。结合紧凑且高度集成的微控制器和磁性传感器,以及热优化的MOSFET封装,这可能最终宣告了在伺服系统中布线的结束。
-
IGBT
+关注
关注
1266文章
3789浏览量
248888 -
硅基
+关注
关注
0文章
57浏览量
15672 -
伺服器
+关注
关注
1文章
151浏览量
19473 -
碳化硅
+关注
关注
25文章
2748浏览量
49019
发布评论请先 登录
相关推荐
碳化硅在新能源领域的应用 碳化硅在汽车工业中的应用
碳化硅SiC在光电器件中的使用
碳化硅SiC在高温环境下的表现
碳化硅SiC在电子器件中的应用
碳化硅SiC材料应用 碳化硅SiC的优势与性能
碳化硅功率器件在能源转换中的应用
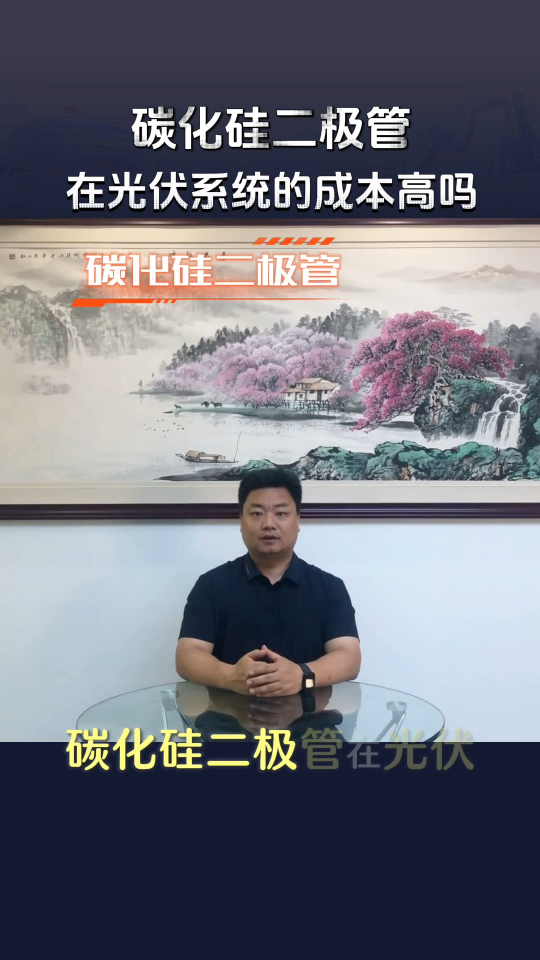
评论