0 引言
与传统半导体材料硅、锗相比,第三代半导体材料碳化硅 (Silicon Carbide, SiC) 具有禁带宽度大、击穿电压高、热导率高、高温稳定性好以及电子饱和漂移速度高等优势,满足抗辐射、耐高压、耐高温、高频及大功率等的器件应用需求,在新能源汽车、充电桩、轨道交通和电网等多个领域广泛应用[1-3]。SiC 的3种常见晶型包括3C、4H 和6H,其中4H-SiC 材料的各向异性较小、禁带宽度大、击穿电压高、电子和空穴迁移率大,成为行业主要研究和应用对象[4]。
根据器件设计要求,需要在4H-SiC 衬底上生长外延膜。目前,商业化SiC 外延薄膜主要通过化学气相沉积 (Chemical Vapor Deposition, CVD) 技术来制备[5], 该外延生长技术不仅可以有效控制掺杂浓度和薄膜厚 度以符合设计要求,而且可以减少衬底中的缺陷,提 高器件良率。SiC 外延是通过载气将反应气体输送到反应室内,使其在一定的温度和压力条件下分解并发生化学反应,形成中间化合物扩散到衬底表面,生长外延层[6-7]。因此,反应室内的气流场和温度场对SiC 外延生长至关重要。目前,SiC 外延生长速度能够达到60μm/h,外延层厚度可大于100 μm,能够满足百伏至万伏以上的高压器件需求[8]。
根据碳化硅外延设备反应室的结构设计进行分类, 目前有垂直热壁、水平温壁和水平热壁3 种主流类型。其中,垂直热壁反应腔采用垂直进气,晶圆高速旋转 可以把掉落物甩出反应区,大幅减少掉落物[5],但其高速旋转容易形成气体涡流,影响流场分布均匀性,并 且存在反应物利用率低、设备成本及运行成本高的问 题。水平温壁设备通过感应加热[9],可实现单腔多片外延生长,设备产能大;且采用多层水平进气,其上层 气流可抑制上顶板附近的沉积反应,减少颗粒产生;同时晶圆的行星式旋转能够提升外延生长的均匀性。由于该设备的空气流场没有进行水平分区设计,水平 气流的均匀性不易调控,影响外延片间均匀性,并且 外延生长速率低,设备成本及运行成本高。
水平热壁反应室具有较好的温度场和气流场环境, 晶圆被正面热辐射和背面热传导双面加热,加热效率 高、升温快、生长速率高[10]。因此,本文以水平热壁 反应室为研究对象,对温度场和气流场关键技术进行 分析,优化腔室结构设计,获得了具有优异工艺性能 的反应腔室。
1 设备关键技术
1.1 温度场研究
反应室温度场分布对碳化硅外延成膜质量至关重要,影响外延反应速度、表面粗糙度、缺陷分布以及掺杂浓度均匀性等。反应室温度分布的均匀性和稳定性与感应线圈结构、石墨腔结构、温度控制系统及测温精度等相关[9-10]。由于碳化硅外延反应所需温度较高,反应室常采用高精度红外测温仪测温。合理的石墨腔结构设计是升温的基础保障,温控系统是确保腔室平稳升温和对温度波动进行控制的关键[11-12]。
NAURA Mars 系列水平热壁设备的碳化硅外延反应室内托盘表面温度仿真分布如图1 所示。CVD 反应室温度场的均匀性决定了托盘表面温度的均匀性,优 化托盘表面温度分布是提高晶圆外延质量的关键。反 应室的热损失主要集中在进气端和尾气端,本文的研 究通过优化石墨腔结构来减少两端热损失,提高托盘 表面温度均匀性。由仿真计算可知,石墨腔长度增加 值在10 ~ 80 mm 范围内时,随着长度的增加,托盘表面温差降低幅度呈先增大后减小趋势。如图1(a)所示,在设定的石墨腔长度下,托盘中心-边缘温差较大(大于39 K);将石墨腔长度增大30 mm 后,托盘表面温差减少16 K,具体如图1(b)所示;石墨腔长度增大60 mm 后,托盘表面温差减少8 K,具体如图1(c)所示,由于此时托盘表面温度已经较均匀, 因此温差减少幅度变小。
(a) 未加长
(b) 加长30 mm
(c) 加长60 mm
图1 托盘表面温度分布图
Fig. 1 Distribution map of tray surface temperature
增加保温毡厚度能够减少热辐射损失,提高反应室温度场均匀性。为减少反应室在进气端和尾气端的热损失,将上、下游保温毡加厚5 ~ 30 mm,可使托盘表面温差降低1~9 K。保温毡加厚前后托盘表面温度分布曲线如图2(a)所示,保温毡加厚10 mm 后,托盘表面温差减少3 K。此外,水平热壁反应室是依靠外侧感应线圈的感应加热,因此感应线圈结构对反应室温度场均匀性影响较大。由于托盘在进气端和尾气端位置温度低,因而需要增加两端的感应线圈密度来提高两端温度,减小托盘表面温差。将进气端和尾气端线圈螺距各减小10 mm,加密两端线圈,之后通过仿真得出托盘表面温差减小了 4 K,其温度分布曲线如图 2(b)所示。
(a) 保温毡厚度
(b) 线圈结构
图2 托盘表面温度分布曲线
Fig. 2 Distribution curve of tray surface temperature
加长石墨腔长度会增加反应物到达晶圆表面的时 间,而为提高反应物输运能力则需增加载气流量(H2) 或降低腔室压力,这将增加外延工艺难度。石墨腔加 长前后托盘表面生长速度分布如图3 所示,由图3 可知在保持载气流量和腔室压力不变的情况下,随着石墨 腔长度的增加,托盘位置相对耗尽曲线后移,因此成 膜速度明显减小,工艺气体的利用率降低。但是这种 方案使得腔室的保温效果得到提升,即托盘表面温度梯度减小、生长速度均匀性增加,因此在气流场-温度场中找到平衡点来确定石墨腔长度尤为重要。同样,增加感应线圈密度会导致感应线圈电阻、所需电压和线圈功耗提高。
图3 石墨腔加长前后托盘表面生长速度分布
Fig. 3 Growth rate distribution of tray surface before and after graphite cavity lengthening
综合腔室长度、线圈结构和保温毡厚度对反应室温度场进行了整体优化,优化后的托盘表面温度分布如图4 所示,表面温差小于8 K。此外,在垂直气流场方向,托盘表面温度基本一致,在外延生长过程中,通过旋转即可提高晶圆受热均匀性,确保外延生长的稳步进行。
图4 优化后托盘表面温度分布图
Fig. 4 Distribution map of optimized tray surface temperature
1.2 气流场研究
碳化硅外延设备采用多路进气,腔内气体由载气、硅源气体、碳源气体和掺杂气体等组成,其中H2 载气流量最大。用于外延沉积的SiC 晶圆位于反应室内,因此腔室内稳定的气流场分布对外延成膜均匀性十分重 要。本文研究的水平热壁外延设备其反应室进气端由 石英方管连接,反应气体通过该方管进入石墨腔,因 此方管内气流场的分布决定了石墨腔内气流场的均匀性。方管内气流场分布主要与进气端法兰结构相关, 因此通过对法兰结构匀流孔尺寸、结构、分布、数量 的研究分析和仿真,可获得无涡流且均匀分布的气流 场。假设匀流孔直径为0.5 ~ 3 mm,数量为30~70 个, 结构形式为椭圆或圆形,分布为单层或多层结构设计, 对此进行仿真分析得出:随着匀流孔径的减小和匀流 孔数量的增加,气流场逐渐变得更加均匀。此外,匀流区长度对气流场的分布也有影响,当匀流区长度增 加10 ~ 60 mm 时,气流场同样会随着匀流区长度增加而变得更均匀。但是,孔径过小会增加前端管路压力, 影响气体的顺畅输运,因此本文研究通过对匀流孔径、数量和匀流区长度等参数进行综合优化,使得石英方 管内气流均匀流过,无涡流产生。优化前后的气流场 分布如图5 所示。
(a)优化前
(b) 优化后
图5 气流场分布
Fig. 5 Distribution map of airflow field
托盘旋转会产生水平气流场扰动,本文基于托盘边缘的线速度进行分析,得出托盘表面不同位置气体流速横截面图如图6 所示。由图6 可知,当旋转速度较低时(线速度小于 0.6 m/s),以 0.087 m/s 和 0.260 m/s为例,托盘的旋转对整体气流影响很小,虚线框内3 条线几乎水平;当旋转速度较大时,旋转对流动场有较大影响,虚线内3 条流速线开始倾斜,两侧气体流速不一致,因此旋转对气流场的作用不能忽略。目前,水平热壁设备托盘旋转线速度一般需小于0.5 m/s,以减少气流场扰动,满足工艺要求。
托盘不旋转时气流场扰动最小,此时碳化硅的成 膜厚度和掺杂浓度工艺数据如图7(a)所示。由图7(a)可知,由于反应源的逐渐耗尽,膜厚由进气端到尾气端 近似呈线性减小趋势,而掺杂浓度则呈线性增大趋势, 说明低生长速度更利于N 型掺杂。不同转速对膜厚的影响如图7(b)所示,在低旋转速度(氩气Ar2 流量小于0.4slm) 下,膜厚均匀性表现为两端低中间高,整体均匀性大于2.5%;不同转速对掺杂浓度的影响与膜厚 不同,表现为两端高中间低,整体均匀性大于 5.5%, 具体如图7(c)所示。分析其原因,在托盘旋转后晶圆表面温度和沉积速率不断变化,而在低转速时晶圆表面 各部分温差大、沉积速率差异大,造成了整体均匀性不足。因此,优化旋转速度,使Ar2 流量大于0.5 slm, 这样晶圆表面温度分布和沉积速率将更均匀。由图7 可以看出,优化后的膜厚近似在一条直线上均匀分布, 膜厚均匀性小于 1%;优化后的掺杂浓度呈w 字形分布,均匀性小于3%。随着旋转速度的增加,膜厚和掺杂浓度更均匀,但旋转速度过大时晶圆容易被甩出托 盘,根据仿真计算结果得出,晶圆被甩出前托盘的转速对气流场的扰动依然较小。
(a) 线速度0.087 m/s
(b) 线速度0.260 m/s
(c) 线速度2.60 m/s
图6 托盘旋转速度对气流场的影响
Fig. 6 Effect of tray rotation speed on the airflow field
2 设备性能
2.1 腔室压力分析
碳化硅外延生长需要稳定的腔室压力,压力波动 带来的气流场扰动将影响气流分布的均匀性。当腔室 压力过大时,气体流速较低,生长源在进气端消耗过 快、到达尾气端的较少,影响外延生长均匀性;当降 低腔室压力时,气体流速增大,使得生长源滞留晶圆 表面的概率降低,从而降低了生长源的利用效率[7]。同时,气体高速流动会使腔室内的高温区向尾气端移动, 从而影响腔室温度场环境。因此,通过腔室压力来调 控生长源耗尽趋势,进而调试外延生长的均匀性是碳 化硅外延技术的关键。低压外延生长的实现要求设备 控压能力强、压力波动小,NAURA Mars 系列水平热壁碳化硅外延设备能够满足 60~150 mbar (1 mbar=0.1 kPa) 低压腔室工艺条件, 压力波动可被控制在±0.5 mbar内。
2.2 外延生长温度分析
腔室温度高低及其波动情况对碳化硅外延生长影响较大,典型的外延生长温度为1 550 ~ 1 680 ℃[12]。温度过低容易产生硅滴缺陷[7],而高温下虽然H 刻蚀能力增强,但生长速度降低,掺杂浓度增大,这些因素容易导致工艺窗口波动。目前,水平热壁碳化硅外延设备其腔室温度在1 500~1 700 ℃可调,温度波动可控制在± 0.5 ℃内,腔室升温速率大于80 ℃/min。研究确定的水平热壁设备升温曲线如图8所示,开始作业后,在设定的升温速率 70 ℃/min 下,机台可从待机温度900 ℃平滑升温至目标温度1 600 ℃,升温过程中温度波动较小,控温阶段温度波动小于± 0.4 ℃,验证了设备优异的升温控温能力。
图8 升温曲线
Fig. 8 Temperature-rising curve
3 工艺控制结果
3.1 膜厚
膜厚均匀性是表征外延层质量的关键参数,10 μm 的膜厚能满足千伏级器件要求,而万伏级器件则需要100 μm 的外延层厚度[8]。外延厚膜的慢速生长需要更长的时间,因此更易增加掉落物缺陷,而高速外延技术是一大突破。目前,水平热壁腔室外延生长速度能够达到60 μm/h 以上,在高速外延生长速度下,600 s 左右便可完成10 μm 膜厚的生长,表明了设备外延量产的高效率。如图9 所示,本文研究的水平热壁外延设备在快速外延条件下能够获得均匀的碳化硅外延层,不同外延层厚度均匀性低于1.2%。连续30 炉次10 μm 碳化硅外延膜均匀性分布情况如图10 所示,工艺控制结果稳定,各炉次膜厚均匀性均小于0.9%,验证了机台稳定均匀的温度场和气流场环境,以及较好的控温和控压能力。
3.2 掺杂浓度
SiC 外延技术中,N 型掺杂通过氮 (N) 原子并入晶格取代碳 (C) 原子位实现掺杂,P 型掺杂通过铝(Al) 原子并入晶格取代硅 (Si) 原子位实现掺杂,其 掺杂源分别为氮气(N2) 和三甲基铝(TMA)。掺杂浓度分布与腔室温度分布的均匀性息息相关,因此掺杂可调试范围及均匀性体现出设备性能。目前,前端外延生长以N 型掺杂为主,N 型掺杂浓度应在1e+14~1e+ 18 间可调,掺杂浓度均匀性应低于5%。本文研究的水平热壁设备由低掺杂到高掺杂浓度分布如图11 所示, 均匀性低于3%。在掺杂浓度目标值8.5e+15 下,对连续30 炉次的掺杂浓度均匀性进行统计,结果如图12 所示,各炉次掺杂均匀性基本稳定在3% 以内,表明了水平热壁外延设备性能较稳定。
图9 SiC 外延层膜厚分布
Fig. 9 Thickness distribution of SiC epitaxial layer
图10 连续外延工艺膜厚均匀性分布
Fig . 10 Distribution of thickness uniformity of continuous epitaxial processes
图11 SiC 外延层掺杂浓度分布
Fig. 11 Doping concentration of SiC epitaxial layer
图12 连续外延工艺掺杂浓度均匀性分布
Fig. 12 Distribution of doping concentration uniformity of continuous epitaxial processes
3.3 粗糙度
碳化硅外延采用台阶流生长模式,4H-SiC 外延层表面具有明显的台阶结构,两层SiC 原子间的间距约为0.25 nm, SiC 外延层粗糙度较小, 原子力显微镜(AFM) 可以测试SiC 表面形貌和表面粗糙度值(包括表面平均粗糙度Ra 和方均根粗糙度Rq)。SiC 表面缺陷-台阶聚并会增加外延层粗糙度,行业内SiC 外延层Ra 值一般低于0.3 nm。本文研究的水平热壁设备通过AFM 测得外延生长的SiC 表面形貌图如图13 所示,扫描范围为10 μm×10 μm,表面无台阶聚并缺陷,说明在外延生长过程中能稳定地进行台阶流生长,其Ra 小于0.15 nm。
3.4 缺陷
外延缺陷主要来源于衬底复制的缺陷和外延引入的缺陷,掉落物是外延过程中主要缺陷来源,存在于外延层中或外延层表面,能引起三角形缺陷等相关缺陷[5]。图14 为本文所研究的外延设备进行连续30 炉次外延片致命缺陷数据统计,各晶圆缺陷密度基本稳定在0.2 ea/cm2以内。
图13 SiC 外延层AFM 表面形貌图
Fig. 13 AFM images of SiC epitaxial layer
图14 连续外延工艺缺陷密度分布
Fig. 14 Distribution of defect density of continuous epitaxial processes
4 结论和展望
通过对水平热壁反应室温度场和气流场技术的研究,获得了生长高质量外延薄膜的腔室结构设计,反应室内托盘表面温差降低至8 K 以内,进气结构无涡流产生。在设定的工艺条件下,外延生长速度能够达到60 μm/h 以上,外延膜厚均匀性小于1.2%,掺杂浓度均匀性小于3%,缺陷密度小于0.2 ea/cm2,外延层表面方均根粗糙度小于0.15 nm,连续炉次的外延工艺控制结果稳定。本研究证明了采用水平热壁技术路线开发的国产外延设备能够在高生长速率下获得较优异的外延工艺控制结果, 对 SiC 外延研究和产业化有重要的意义。
碳化硅行业致力于不断降本增效,提升功率器件 中碳化硅器件的市场规模。未来将开发单腔多片式碳 化硅外延设备及8 英寸 (20.32 cm) 碳化硅外延设备, 这是目前碳化硅外延设备的重要发展趋势,基于此不 仅可以增加量产效率,而且能降低外延成本,支撑行业发展。
来源:半导体信息
审核编辑:汤梓红
-
半导体
+关注
关注
334文章
27305浏览量
218153 -
半导体材料
+关注
关注
11文章
532浏览量
29560 -
SiC
+关注
关注
29文章
2808浏览量
62610 -
碳化硅
+关注
关注
25文章
2749浏览量
49021
原文标题:碳化硅外延设备技术研究
文章出处:【微信号:芯长征科技,微信公众号:芯长征科技】欢迎添加关注!文章转载请注明出处。
发布评论请先 登录
相关推荐
研究碳化硅衬底和外延的实验报告
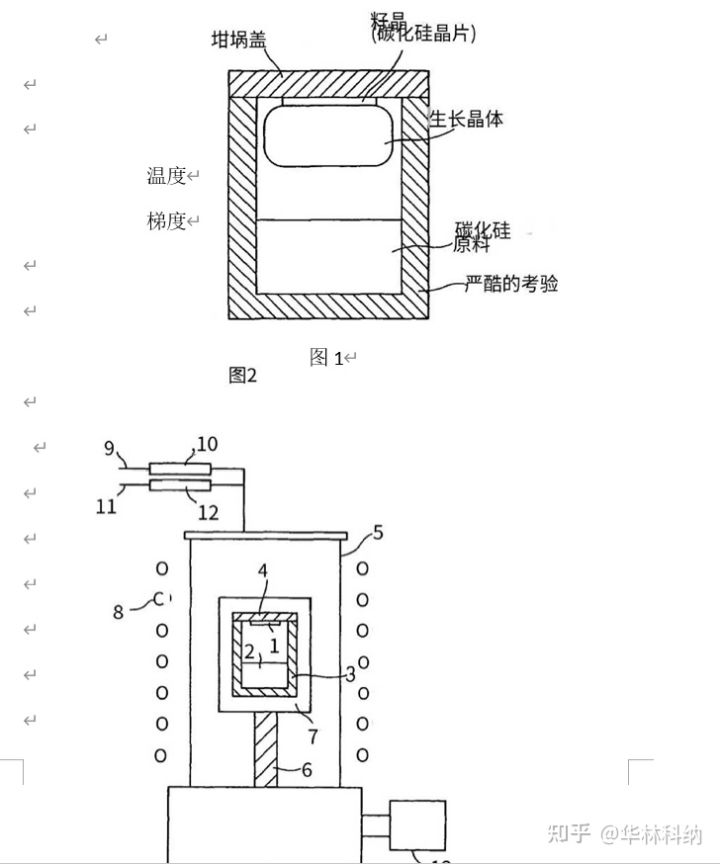
评论