摘 要:以含有腔体结构的LTCC叠层生瓷为研究对象,介绍了腔体在层压形变的评价和控制方法。分析了LTCC空腔在层压时产生变形的主要影响因素。阐述了在生瓷表面上增加金属掩模板来控制腔体形变的叠层结构设计。有限元分析结果表明不锈钢掩模可使腔体边缘应变降低至无掩模时应变的1/6,并通过工艺试验验证了金属掩模板的有效性。结果表明合理的层压结构设计和恰当的层压工艺可以制作出满足尺寸精度的空腔结构。
1背景介绍
低 温共 烧 陶瓷 (Low Temperature Co-fired Ceramics,LTCC)是一种集层间互连、无源元件集成的三维电路基板[1]。其结合了多层陶瓷元件技术和多层电路图形技术,将流延而成的生瓷冲孔并进行导体填孔,实现层间互连,经叠片和层压实现多层印刷线路图形的立体累加,利用低温共烧结制成三维空间高密度电路基板。近年来,随着多芯片组件的发展,LTCC基板在埋置电阻、电容和电感等无源元件的同时普遍具备腔体结构。腔体中可以封装芯片,提高组装密度的同时缩短层间互连线,降低微波不连续性影响,大大提高组件可靠性[2]。
在LTCC生瓷叠层之后、烧结之前,通常进行层压工艺处理,使叠片坯体不再发生相对位置的变动,各层生瓷结合为一体,坯体的初始致密度在层压过程中可以得到明显提升。按照叠片层压的时序,层压可以分为一次性叠片层压和累积法叠片层压。一次性叠片层压是在叠层过程中不加压力,叠片完成后一次加压压实各叠层膜片。而累积法则是在生瓷逐层叠放的过程中施加压力,叠片和层压同时完成。但最底层的生瓷累积受压多次,叠层的厚度方向结构变得不均匀。按照加压方式,层压可以分为单轴加压和等静压。使用单轴层压工艺,LTCC叠层坯体上下层有承压板的支撑,在腔体结构的部分,压力不能均等传递,腔体结构在受压过程中因收缩不一致易受损坏。而对于等静压工艺来说,理论上,整个坯体包括腔体结构受到的压力是一致的,腔体除了因瓷片收缩带来的变化外无其他变化。
由于腔体一般在单层生瓷上制备,经叠片和层压后,腔体形态容易发生形变。腔体在层压过程中的变形处理成为了LTCC的加工难题之一[3]。为确保腔体在叠片和层压过程中的变形量最小,需要采用特定的材料对腔体内部进行保护[4]。通常选用硅胶为填充材料,将硅胶制备成腔体的嵌件预置于腔体中。在层压时可以保护外力对腔体的冲击,使腔体很好地成型。针对复杂腔体结构(如双面腔体)的LTCC多层基板,可以兼顾一次成型和累积法成型两种方法,将复杂结构分割成多个简单结构,分别进行叠层层压,最后将层压好的多个坯体叠层,最后再进行层压合体[5]。本文针对带有空腔的LTCC层压工艺技术,利用白光干涉仪测量空腔在层压过后的形态变化,分析腔体结构对层压形态变化的影响规律。同时,提出一种层压形变控制工艺设计,可以有效降低腔体形态变化,提高腔体的边缘成型质量。
2试验设计及测试
2.1试验材料及结构设计
选择单层厚度为127滋m的Ferro A6生瓷为研究材料,利用激光对单层生瓷进行腔体加工,单层瓷片腔体结构设置如表1所示。腔体的形态主要考虑圆形和方形两种基本类型,其余复杂的腔体形状可以看作是这两种结构的组合。腔体的深度主要通过叠层的层数控制,对于同样形状、同样大小的腔体,分别叠层5、10和15层3种,代号为N5、N10和N15。
对位叠层完成后进行层压。如图1(a)所示,层压中包封从下到上的放置顺序为:金属背板、生瓷和约1 mm厚度软硅胶。随后采用真空包装袋进行真空包装。在80℃的水介质中预热10 min后在20.3 MPa(3 000 Psi)压力下保压10 min。腔体成型状态如图1(b)所示。
表1腔体结构参数设置
图1层压叠层结构示意图
2.2试验测试
理论上讲,LTCC生瓷在等静压过程中受外界介质施加压力是均匀的,坯体收缩一致,腔体可以完好成型,不存在边缘塌陷现象。但是实际过程中,由于包装密封材料在等静压过程中的变形,生瓷腔体边缘受额外的应力(F’),额外产生的应力作用在腔体边缘,容易导致腔体边缘的变形塌缩。为了评价腔体边缘的形态变化,采用白光干涉仪测量空腔在层压过后的变形状态。测量时将被测试件置于干涉显微镜下,由CCD接受白光干涉条纹。当垂直扫描系统驱动时,干涉显微镜垂直移动。工件不同高度表面上的零件条纹被记录,经计算机处理得到三维形貌图像。
3试验结果
3.1评价方法
图2(a)给出了带有半径2 mm圆形腔体的10层生瓷层压后的高度云图。由于腔体的对称性,沿着腔体圆心位置提取高度信息,可以得到如图2(c)的一维高度轮廓。为了评价腔体边缘形变,一方面可以通过形变范围表征,即腔体的塌缩宽度,对于半径为2 mm的圆形腔体其形变范围约为0.75 mm。另一方面可以通过距离理论腔体边缘一定距离(ΔL)的高度应变量(ΔH)进行说明。例如ΔL为0.15mm时,ΔH为142滋m,即说明在距离腔体边缘0.15 mm处高度方向塌缩了142滋m。对于方形腔体,可以采取类似的方法进行分析评价。图2(b)给出了带有边长4 mm方形腔体的10层生瓷层压后的高度云图。通过沿着垂直于腔体边缘的方向提取高度信息,可以得到如图2(d)的一维高度轮廓。腔体边缘形变同样可以通过形变范围及高度应变量进行表征。
图210层生瓷层压后的高度云图及中心截面轮廓图
3.2腔体大小的影响
在相同层压条件和腔体厚度(10层)条件下,图3 (a)给出了不同半径的圆形腔体的高度轮廓图。为了表征方便及对称性的考虑,腔体边缘位置及腔体底部被归一到零的位置。从图中可以看出,较小的腔体尺寸导致了较大的腔体边缘形变,形变范围增大。对于半径为0.5mm和4mm的腔体,腔体的形变范围从0.7mm增加到1.2 mm。ΔL为0.3 mm时,ΔH从45 μm增加到152 μm。
对于方形腔体,如图3(b)所示,腔体大小的影响规律与圆形腔体类似,随着腔体边长的增大,腔体边缘高度上的形变增大,范围也增大。当边长从1 mm增加到8mm时,腔体形变范围从0.65mm增加到1.2mm。ΔL为0.3 mm时,ΔH从50 μm增加到164 μm。
图310层生瓷层压的高度轮廓图
3.3腔体深度的影响
腔体的深度是通过叠层的数量决定的。在相同层压条件和腔体大小的条件下,图4(a)给出了半径为2mm的圆形腔体分别叠层5、10和15层的高度轮廓图。为了对比轮廓,在不影响分析结果的情况下,腔体边缘位置被归一到零的位置,顶层的生瓷高度统一归一到10层瓷片的高度。从图中可以看出,较多的叠层数量意味着较深的腔体尺寸,越深的腔体导致了越大的腔体边缘形变,形变范围增大。叠层数量为5、10和15时,腔体的形变范围分别为0.5 mm、0.8 mm和1.1 mm。ΔL为0.3 mm时,ΔH分别为24μm、57μm和100μm。
对于方形腔体,如图4(b)所示,叠层数量的影响规律与圆形腔体类似。ΔL为0.3 mm时,ΔH分别为25 μm、74 μm和115 μm。
图4不同叠层厚度的高度轮廓图
4试验分析
在LTCC生瓷层压过程中,生瓷除了在等静压力之外,由于包装密封材料在腔体上的变形,应力(F’)不可避免地在腔体边缘集中,导致腔体边缘的变形塌缩。变形塌缩的程度直接取决于F’的大小。F’越大,导致腔体边缘形变塌缩程度增大,形变影响范围增大,即在一定的ΔL处,ΔH也越大。F’的大小与包装材料的材质及包装材料在层压过程中的形变密切相关。在一定包装材料的条件下,F’的大小直接取决于包装材料的形变。通过对比图1(a)和(b),包装材料的形变直接与腔体结构相关,即与腔体半径或边长及深度有关。腔体深度越大,形变量越大,腔体半径或边长越大,与其对应的形变量越小。
通过以上分析和试验结果,圆形腔体和方形腔体的腔体边缘变形的规律基本上是相同的。如图4所示,对于半径为2 mm的圆形腔体和边长为4 mm的方形腔体,在相同的厚度下,腔体边缘形变是非常接近的。由于方形腔体相较圆形腔体的面积较大,与此对应的形变要稍小于圆形腔体。此外,对于圆形和方形腔体,腔体厚度及大小的影响规律也是基本相同的。下面就以圆形腔体为例,分析圆形腔体半径和腔体深度对腔体边缘形变的影响规律。
图5给出了ΔL固定为0.3 mm时,腔体深度和圆形腔体大小对形变(ΔH)的影响规律。如图5(a)所示,对于相同的腔体大小,ΔH与腔体深度基本呈线性关系。腔体越深,ΔH越大。此外,线性的斜率随着腔体半径的增大而减小。这就说明,深度对于较小的腔体影响较大,而对于较大的腔体,深度的影响作用较小。因此,随着腔体深度的增大,腔体尺寸的差异带来的形变差异也越来越大。如图5(b)所示,对于相同的腔体深度,ΔH与圆形腔体半径的倒数基本呈线性关系。腔体尺寸越大,ΔH越小。此外,直线拟合的斜率随着腔体深度的增大而减小。腔体较小时,腔体深度的影响较大,因此,随着腔体尺寸的增大,腔体尺寸的差异带来的形变差异也越来越小。
图5ΔL为0.3 mm时腔体深度和尺寸对形变的影响规律
5形变控制
5.1层压结构优化设计
为了提高腔体结构设计的灵活性,就必须解决LTCC腔体在层压过程中边缘形变的问题。即使对于较小的腔体和较大的腔体深度,也要保持良好的腔体边缘质量。较为常用的腔体保护技术为嵌件技术[4],通过在腔体中填充硅胶等嵌件,将带腔基板改善为平面结构,降低层压过程中实际的腔体深度,对腔体实施保护,减少了腔体形变。但是,由于制作尺寸匹配的嵌件耗时费力,嵌件填充和取出的过程中也容易破坏腔体边缘[5]。降低了腔体成型的成品率,增加了LTCC制造的成本。本文提出一种制备高精度腔体的层压结构设计,如图6(a)所示,在橡胶垫和瓷片之间夹上硬质的金属掩模板,掩模板上通腔的形状与陶瓷基板腔体形状对应。腔体等静压过程中,如图6(b)所示,弹性材料板会在外部压力作用下通过金属掩模板开口部分填充到腔体中,以保证腔体各个方向上所受压力更加均匀,而金属掩模板会支撑保护腔体结构,保持腔体结构不变形。
图6优化的层压结构示意图
5.2形变模拟对比
为了验证金属掩模板的作用,采用有限元分析方法对层压形变进行分析。有限元分析的材料、结构及应力参数如表2所示。金属掩模板材料选择具有代表性的结构钢。根据经验值估算得到LTCC材料参数,采用简化的局部模型进行仿真,分析腔体边缘处的生瓷在包封材料带来的额外应力(F’)作用下引起的形变,分别对有无金属掩模板的腔体边缘处生瓷的应变分布进行模拟,分析金属掩模板的作用。
表2有限元分析参数设置
图7给出了有无金属掩模的有限元分析应变云图。由图7(a)可见,LTCC应变集中在应力施加的区域,最大应变为0.123,发生应变即应力影响的区域长度约为0.85 mm。当存在金属掩模时,如图7(b)所示,LTCC应变依然集中在应力施加的区域,但是最大应变降低为0.021,仅为无金属掩模的最大应变的1/6。此外,应力影响区域的长度约为2.0 mm,基本上是无金属掩模的应力影响长度的2倍。说明金属掩模可以有效增大应力分布区域,降低应力作用效果,降低最大应变。
图7有限元分析应变云图对比
5.3试验结果对比
为了进一步验证含有金属掩模板的层压设计,在试验上对有无金属掩模的层压试样进行腔体边缘形变测量和对比。图8给出了半径为1 mm的10层生瓷圆形腔体有无金属掩模层压后的高度云图及相应的腔体中心截面轮廓图。从图中可以看出,在相同的腔体结构条件下,存在金属掩模的试样经层压后,腔体边缘较为陡直,腔体塌缩较少。应力导致的形变的影响范围从0.65 mm降低到0.15 mm。当ΔL固定为0.15 mm时,ΔH从135 μm降低到了30 μm,说明金属掩模板的存在可以有效降低腔体边缘形变,实现腔体的高质量制作。
图8半径为1 mm的10层生瓷圆形腔体有无金属掩模层压后的高度云图及相应腔体中心截面轮廓图
6结论
本文利用白光干涉仪测量LTCC空腔在采用软硅胶等静压层压过后的变形量。测试结果表明:空腔边框的形变与生瓷腔体的大小和厚度相关。同样的腔体大小,腔体深度越大,层压后腔体的变形越大;同样的腔体深度,较大的空腔对应着较小的层压形变。在此基础上提出了一种层压形变控制工艺设计,在LTCC生瓷和弹性材料垫片之间增加刚性金属材料掩模板;利用有限元软件对金属掩模板的作用进行分析。
以不锈钢掩模为例,分析结果表明不锈钢掩模可以有效控制形变,存在掩模的最大形变只有无掩模的1/6;并进行实际使用的测试,试验结果显示不锈钢掩模的存在可以有效降低腔体的变形量,提高腔体的边缘成型质量。提出的LTCC腔体层压工艺改进是一种普遍性方法,对加工成型具有一定的借鉴作用。
审核编辑:汤梓红
-
电路板
+关注
关注
140文章
4945浏览量
97666 -
叠层
+关注
关注
0文章
28浏览量
9843 -
LTCC
+关注
关注
28文章
127浏览量
48771 -
无源元件
+关注
关注
1文章
1279浏览量
16945
原文标题:LTCC生瓷层压中腔体的形变评价及控制
文章出处:【微信号:中科聚智,微信公众号:中科聚智】欢迎添加关注!文章转载请注明出处。
发布评论请先 登录
相关推荐
LTCC基板三大关键工艺问题的优化方案
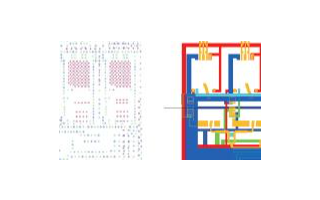
DFM提高LTCC设计效率的方法
层压板与LTCC板射频模块的比较
LTCC电子器件的模块化
LTCC技术有什么特点?
空间映射方法研究及其在LTCC设计中的应用
LTCC技术参数手册
LTCC Antenna LTCC 天线
LTCC,什么是LTCC,ltcc技术
如何用DFM方法提高LTCC设计效率
基于熵权的研究生培养质量多级模糊评价
如何设计SiP封装层压板和LTCC板的射频模块
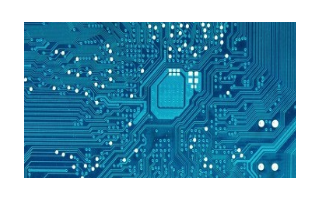
华林科纳在微系统应用中的LTCC技术报告
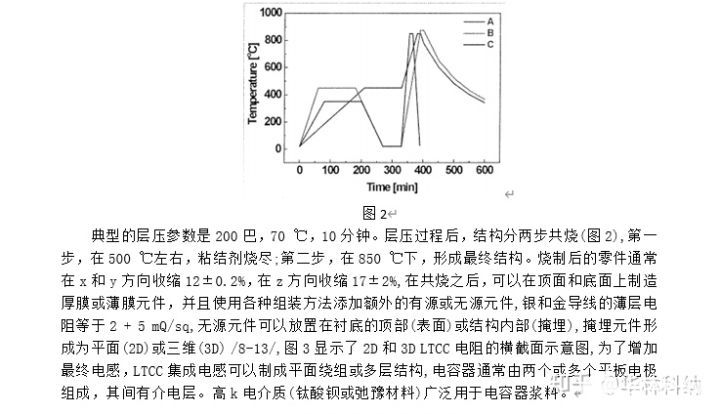
评论