BC电池工艺全梳理——可与多种技术(TOPCon,HJT)结合(TBC,HBC)
1、BC不是一种全新的电池技术。BackContact,金属电极均以叉指状排列在电池背面,为正面创造更多的吸光面积,提高电池片的整体光电转换效率。
2、BC不是一种孤立的电池技术。TBC=TOPCon(隧穿氧化硅/掺杂多晶硅)+BC(全背面接触);HBC=HJT(非/微晶硅)+BC(全背面接触),TBC/HBC的竞争实质上是TOPCon和HJT的进一步差异化竞争。
3、BC技术壁垒高,并非拥有TOPCon/HJT储备即可随时转产BC电池。①BC电池的生产工序较长,尤以背电极制作较为繁琐,需要经历2~3道激光开槽工艺,对设备稳定性/工艺成熟水平要求较高,而激光开槽过程中造成的漏电问题是制约电池片生产良率的重要瓶颈;②由于背电极相互交叉,在焊带设计/焊接工艺和封装工艺也需要做相应调整。焊带方面,扁平化、变薄变宽趋势;胶膜方面,主流方案EPE+POE,胶膜厚度可随焊带超薄而下降;串焊机方面,焊接精度要求大幅提高,需要BC专用串焊机。
4、BC技术高度适配电镀铜。当前金属化方案中,电镀铜、银浆各具优势,长期看,对于工艺复杂,人力、设备、材料成本高昂的BC电池而言,电镀铜在成本、工艺匹配上表现出巨大潜力。
结构
BC基础结构:
从上至下:SiNx/SiO2-n+Si(掺磷)-Si基底-p+(硼扩)/n++(磷扩)Si-SiO2/SiNx-金属电极(叉指)
n+Si(掺磷):利用场钝化效应降低表面少子浓度,从而降低表面复合速率,同时还可以降低串联电阻,提升电子传输能力。
p+Si(硼扩):发射极能够与N型硅基底形成p-n结,有效分流载流子。
n++Si(磷扩):与n型硅形成高低结,增强载流子的分离能力,是IBC电池的核心技术。
SiO2/SiNx:背面,抑制IBC太阳电池的载流子复合;正面,减反层提高发电效率。
图:IBC电池结构
来源:《叉指背接触硅太阳能电池》,国金证券研究所
图:叉指电极
来源:DSNewEnergy官网
HBC结构(HJT/BC):
从上至下:减反层-本征非晶硅-Si基底-本征非晶硅-n/p型非晶硅-TCO-金属电极
图:HBC电池结构
来源:摩尔光伏
TBC结构(TOPCon/BC):
从上至下:减反层-钝化层-AlOx-n+Si(掺磷)-Si基底-隧穿氧化层-p+/n++掺杂多晶硅-钝化层-减反层-金属电极
图:TBC电池结构
来源:光伏测试网
工艺
表:各BC技术工艺流程
来源:全球光伏
HPBC电池工艺流程
两种P-IBC电池结构
工艺流程①:刻蚀掩膜
工艺流程②:全激光
难点:N/P区图形化
目的:在电池背面建立独立的电子/空穴传输通道
工艺:激光开槽。激光1、激光2做图形化,激光3用于金属化前的SiNx开孔。
要求:激光能量均匀
图:隆基HPBC全激光流程图
来源:全球光伏
表:各BC技术效率、投资额
来源:东方日升
双面率问题:BC电池由于电极都在背面,牺牲了一定的双面率,但正面遮光面积增加3-4%带来的效率增益足以抵消背面效率降低带来的影响。从应用场景角度看,BC电池的单面特性及其适用于屋顶光伏,发电量可比TOPCon高2-3%(河南/河北光照条件下,来源:隆基中期业绩交流会)。BC电池的双面率仍有提升空间,当前BC电池主攻单面市场,在双面性能表现出明显优势之前,暂不会参与双面市场竞争。
封装
IBC电极均在背面,无法用一根焊带直线互联。IBC组件的焊接工艺需要特殊的互联焊带进行连接。
互联工艺的难点是绝缘问题:1、电池片本身做绝缘处理,但这种方法成本较高;2、利用绝缘胶膜在背接触电池片焊接前进行绝缘处理,但会影响组件生产效率。
目前行业内提出的2个方案:
1、导电胶+柔性电路背板。
基于全新的金属箔电路设计,每片电池片通过柔性的导电胶和金属箔电路互联从而自动形成完整的回路。
组件封装结构:钢化玻璃-EVA-电池片-绝缘层-导电背板-EVA-背板。
来源:日托光伏,国金证券研究所
来源:索比咨询
2、涂锡铜带焊接和普通背板。
a、使用特殊形状焊带(根据背面结构定制化设计),材料成本低,实现较简单。
b、IBC电池串焊连接时,通常将完整的一整根焊带裁切截断后,连接相邻两个电池片的正极和负极。因而,传统的焊带用于IBC电池串焊时,存在多次的拖拽、拉伸和截断操作,降低生产效率和产品良率。
b、焊接原理发生了变化,从双面焊接变成单面焊接,单面焊接时,硅片易受热弯曲,增加工艺难度。需要全新BC电池专用串焊机。
隆基焊带方案:将具有导电段和绝缘段间隔交替分布的焊带用于IBC电池片的串焊中,同一条焊带的导电段同时焊接相邻两个IBC电池片中,一个电池片的正极区域、另一个电池片的负极区域。
焊带形状:圆形、矩形、三角形。
图:隆基焊带专利示意图
来源:隆基专利CN219610448U
胶膜:原则上EVA、POE、EPE都可用。IBC组件正面无金属栅线,外观要求更高;背面线路焊接,耐腐蚀性要求高。Maxeon的IBC组件采用的是纯POE胶膜的封装路线。
*封装IBC电池时,无需考虑焊带对电池正面胶膜厚度的影响,POE胶膜虽然价格昂贵,但工艺上允许可以适度降低正面胶膜克重,利于组件降本。
金属化
BC电池的重大区别在于:背面制备出呈叉指状间隔排列的P区和N区,以及在其上面分别形成金属化接触和栅线。
因此金属化的要求:
1、减反层开孔面积小。背面金属接触比例越小,复合电流就越小,开路电压提高。
2、N和P的接触孔区需要与各自的扩散区对准,否则会造成电池漏电失效。
图:SiNx开孔
来源:《叉指背接触硅太阳能电池》
银浆在BC电池中的局限:
1、BC电池栅线均在背面,对光照遮挡要求低,且考虑到电极面积越大更利于电流输出,一般栅线较高。这种情况下,银浆耗量大、成本高,且目前没有降本路线。
2、BC电池背面n区/p区面积大小不同且间隔排列,不同区域对应栅线宽度也不同,使用丝网印刷银浆的方案,在网版设计上要做出重大调整。
3、BC电池电极均在同一面,意味着电子/空穴分离后将向同一方向运动、输出,相比其他结构电池,同一方向运动难免存在更严重复合问题,也就对金属端的导电能力提出了更高要求。银浆并非纯银材料,大量的有机物、添加剂等使其导电能力不如纯铜。
4、银铝浆存在高度差,增加焊接难度。
铜电镀更为适配:
1、BC电池背面叉指状的P区和N区在制作过程需要多次的掩膜和光刻技术,且之间的gap区域需非常精准,与铜电镀精细的掩膜光刻工艺适配,可以同时降低金属化环节的设备投资成本。
2、光刻工艺下,铜栅线线宽灵活可调且更加精细,易找到电流输出与接触面积的最佳平衡点。
3、铜价格低廉,铜栅线材料成本低。
4、纯铜栅线相比银浆导电性更好。
图:IBC电池铜电镀工艺
来源:《Directcontactplating-InlineplatingsolutionforZEBRAIBCbylocalcontacting》
HPBC电池技术
受制于光伏电池的快速发展,行业中迫切需求高效率、高发电性能的产品以实现光伏电站的投资收益预期,实现光伏发电的经济性,最终实现30·60碳达峰碳中和的目标。
为此隆基研发部门经过近2年的研究,开发了全新的HPBC电池技术,该电池技术结合了行业中两种先进的电池技术TOPCon和IBC技术,首先电池通过氧化硅和重掺杂的多晶硅层实现了电池表面高质量的钝化和电流传输,减少了光照产生的载流子的复合,提升了组件的效率和电压,另外通过结合IBC的电池工艺,将电池所有负责收集传输载流子的金属栅线全部移到组件背面,用于接收光线的电池正面完全没有栅线遮挡,使得入射到电池的光线被充分吸收,提升了电池的光线利用率,从而使得HPBC电池的光电转换效率得到大幅的提升,达25%。
图1HPBC电池结构图
图2HPBC电池与PERC电池外观对比
HPBC组件
隆基基于分布式和地面电站不用的应用场景,推出了基于主流M10(182mm)硅片(2022年上半年M10组件出货占比达55%左右)的两个版型的HPBC组件:54型和72型,其中54型和72型单面组件应用于分布式市场,72型单、双面组件面向集中式光伏电站。并且两个版型的组件尺寸均采用行业中M10标准化的组件尺寸,72型组件尺寸为2278*1134mm,54型组件尺寸为1722*1134mm,组件尺寸的标准化实现组件设备和供应物料标准化,以及在电站端支架等配套设备的标准化,有利于降低非标准化带来的成本上升。
图3HPBC组件设计、版型及应用场景
表1为隆基HPBC组件在2022年底产出的组件功率、效率等信息,可以看到,72型单面组件年底量产功率可实现575W,组件效率达22.3%,相比目前M10PERC组件当前主流功率550W有25W的功率提升,组件效率提升1%的绝对值。
对于光伏组件发电性能会随着组件工作温度的升高下降的现象,也可以通过选用隆基HPBC组件得到有效改善。得益于HPBC电池的高转换效率和高的开路电压,隆基新品HPBC组件具备更优的功率温度系数-0.29%/℃,相比PERC的-0.34%/℃有大幅提升,以组件工作温度为65℃为例,隆基HPBC组件较PERC的发电增益达2%。
图4HPBC组件功率路线图
并且由于HPBC电池栅线均在背面,组件内电池片间连接均通过背面实现,避免了常规PERC组件中电池正/背面栅线互联的现象,基于全背面的高可靠互联技术,隆基HPBC组件的功率质保全面升级,其首年衰减仅1.5%,线性衰减仅0.4%/年,相比PERC组件首年2%、线性0.45%有大幅提升,仅功率质保的提升,HPBC组件相比PERC组件在25年全生命周期的发电量增益可达2%以上。
图5HPBC组件功率路线图
基于未来HPBC电池效率的持续提升,未来隆基HPBC组件功率将会以每年5W稳步提升,到2024年下半年72型单面、双面组件功率分别可达585W和580W。
图6HPBC组件功率路线图
目前隆基HPBC组件已通过各项IEC认证及加严测试,在TC600(温度循环测试)、DH2000(湿热2000小时)、PID及在综合测试序列中隆基HPBC组件均呈现了极低的功率衰减。
图7HPBC组件功可靠性测试
HPBC组件价值
基于上述HPBC组件的上述特性,HPBC组件的应用可以降低客户系统投资成本、运维成本,降低光伏发电LCOE成本,提升客户的收益率:
①得益与HPBC组件的高效率,可以带来电站系统成本的降低,以PERC550W和HPBC575W组件电站建设成本对比为例,隆基HPBC组件可以带来4.7分/W的光伏场区成本降低,其中主要的成本下降包括组件支架、基础、线缆、土地、安装等。
IBC电池无非就是把PN结放到了背面,不能脱离开半导体的基本的物理规律,所以TopCon IBC的理论效率,跟现在的TopCon的理论效率是一致的。异质结IBC的效率跟现在的异质结也是一致的。28.7,28.8这样的一个范畴。
IBC电池是1977年美国斯坦福大学的几个教授他们发明的,然后进行产业化;2014年日本的Sharp 公司提出PN结全部换成HJT,形成了 HBC这样的突破,2016年日本的Kaneka在这个基础上的话,做出了一个26.33的大面积的这样的一个效率,后来日本人在Kaneka的基础上的话,又花了一年的时间,获得26.7的这样的效率。
无论是常规的IBC还是到异质结的IBC,效率的话得到了一个大幅度的提升,由原来的25.2得到了26.7的效率,但是的话就是万变不离其宗。异质结IBC它也是第一个对工艺的要求极高,这个的话也是一个半导体级别的,而且是不会低的。第二个的话就是图形化技术是最大的障碍,做下来的话,至少有3道到4道图形化的技术,图形化的技术的话要用到光刻的技术,光刻的技术的话也可以用到其各种各样的曝光。第三个的话就是电池的良率比较低,无论是tbc还是HBC,特别依赖于湿法。另外一个就是表面的色差是比较明显的,所以说电池的良率会比较低。第四个的话设备投资昂贵,异质结电池本身就贵,你在异质结基础上叠加了IBC不就更贵了吗?或者是TopCon电池的生产线都比perc要贵,你在这个上面叠加了IBC,它也不更贵吗?所以设备投资是昂贵的。
还有一个辅材的昂贵,因为它用到了图形化,用到了图形化的膜,包括干膜湿膜,还要用到了各种各样的添加剂,所以说的话它的辅材比较昂贵。
所以说N型IBC和HBC电池的大规模的产业化,成本是最大的因素,成本因素只有上市的辅材设备投资良率等等所造成的,它是一个综合性的这样概念。
XBC电池反馈
1、BC(backcontact)意值背接触电池,将正面的金属栅线放到电池背面减少阳光遮挡而提高转换效率。BC电池在70年代就提出,其优势是转化效率高,短路电流大、填充因子高,并且比较美观,但缺点是制造流程太复杂、成本比较高。
2、BC类电池包括IBC、TBC、HBC、HPBC等,经典的IBC电池已经有上量的公司,美国SunPower是先行者,有长期的技术和较全面的专利储备,其Maxeon品牌产能已有几个GW,由于美国关税保护,其在美国市占率比较高,近几年排产期一直长达1-2年。
3、BC与TOPCon与HJT不是排他性的,BC大家庭的另外几个分支,如TOPCon与IBC结合的TBC路线,HJT与IBC结合的HBC,目前TBC与HBC基本都是N型产品;隆基HPBC是P型产品。TBC、HBC的转化效率要高于IBC,业内反馈,头部的TOPCon公司,已在储备TBC产品,中试的182-72片TBC组件功率可能达600-610多W。
4、BC电池很可能是未来方向之一,由于效率高、美观但成本高,如果未来成本下降,在屋顶市场是很好的方案。除了隆基2021开始产业化的HPBC产品,据了解,中国公司针对屋顶方案的TBC产品,一年后可能就会批量走向海外市场。
5、BC电池制成流程很复杂,成本高,未来还需要解决系列问题,包括制备流程长,成本与一致性问题,需要减少表面复合,硅片勺子寿命要求更高等。关于导电浆料问题,之前行业交流反馈,电镀距离应用还比较远,部分现行方案的银耗比PERC要高几倍。
XBC各大公司去做主要是实现差异化的竞争。但是从目前的这样的一个实际情况来看,分布式高端市场海外市场还是有些优势,但是国内的整体优势的话并不突出的。第二个是XBC的销售规模有限,单凭某一家公司很难实现跨规模的放量生产,这个里面包括成本良率和效率。就是发现光伏技术有这么一个特点,如果这个技术只有一家去做,太危险了。
现在图形化的技术,图形化的设备,图形化的材料的话,相对来说成本比较高。如果光凭几家公司上几个GW或者是几十个GW现在都不是一回事儿。第三个从性价比和规模的角度来说,从科学的数据来看,未来还是TopCon和异质结的天下。如果XBC的效率的档次和TopCon的效率档次拉不开的话,这个XBC的空间是有限的。
如果异质结能做到25.3%,你XBC要做到多少呢?你得往26.3%以上或者26%以上,不往上这个数据上做的话,它的成本是非常高的。这种电池主要是为了实现差异化的机制,因为你现在可选择的东西非常少,要么就钙钛矿,知道钙钛矿就是忽悠,骗子,从我们的角度。资本界怎么看不管,这个就把它排除在外了。剩下的perc是过时了的。现在只有TopCon和异质结,剩下一个XBC还有钙钛矿叠层。但是钙钛矿叠层还属于基础研究,成本更高,所以说现在能拿得出手的也就是这三个。
审核编辑:汤梓红
-
芯片
+关注
关注
456文章
51157浏览量
426682 -
电池技术
+关注
关注
12文章
907浏览量
49415 -
工艺
+关注
关注
4文章
602浏览量
28871 -
电池
+关注
关注
84文章
10673浏览量
131060
原文标题:技术前沿:XBC电池的进与退
文章出处:【微信号:AIOT大数据,微信公众号:AIOT大数据】欢迎添加关注!文章转载请注明出处。
发布评论请先 登录
相关推荐
笔记本是否应该拔除电池使用?新的电池是否要全放全充?
【Thunderboard Sense试用体验】之(三)梳理供电问题
2020年燃料电池行业研究及产业链梳理相关资料分享
BC电池是什么意思 bc电池和topcon的区别
bc电池和topcon的区别在哪
高效太阳能电池:HPBC、TBC与HBC,三种不同BC电池结构对比
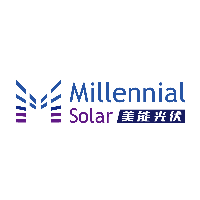
评论