1.引言
碳化硅(SiC)材料被认为已经彻底改变了电力电子行业。其宽带隙、高温稳定性和高导热性等特性将为SiC基功率器件带来一系列优势。近年来,随着新能源汽车企业将SiC基MOSFET模块应用于高端汽车,SiC衬底材料的应用前景再次受到广泛关注。SiC单晶采用物理气相传输(PVT)方法制备,6英寸产品投入市场,厚度约为10–30mm。相比之下,经过几十年的发展,现代电子信息产业的基石材料单晶硅(Si)已达到12英寸的尺寸。同时,其熔体的制备方法更容易制备出厚度更大的晶锭,最高可达1米以上,大大降低了单位面积的衬底成本。因此,目前的制备方法和晶体尺寸的限制导致SiC衬底的市场价格很高,严重限制了下游行业[5]的进一步应用。
因此,许多研究者对SiC晶体生长进行研究和开发工作。溶液法制备SiC晶体有着广阔的前景,但也面临着实际问题。例如,由于SiC的高熔点,添加助熔剂会导致夹杂物和位错,碳成分的连续供应仍未解决。对于PVT方法,增加晶体的厚度和尺寸是降低制备成本的关键,这也是研究人员的主要方向。然而,与溶液法不同的是,气相材料制备面临着许多困难,如无法直接观察、原料状态的巨大变化、加工过程中热场条件的恶化以及调节困难。因此,不容易同时增加厚度和保持高质量,并且在短时间内提升空间的潜力有限。SiC晶体生长具有扩径的自然习惯,因此在过去30年中,从最初的晶粒到厘米大小的单晶,晶体尺寸的扩大一直是其工业化的主要方向。与此同时,近年来,研究人员和工业界正在从5厘米、7.5厘米、10厘米和15厘米发展到20厘米。然而,晶体直径的扩大并不是通过几次迭代生长的简单扩展。
为了获得大尺寸SiC晶体生长的热场条件和控制方法,利用模拟工具对晶体生长的温度场进行了建模。在初始热场条件下,获得了适合于籽晶生长的温度。尽管如此,籽晶的径向温差仍达到93K。首先,通过引入新的籽晶腔设计,观察到径向温差约为10K和轴向温度梯度为12K/cm的热场条件。然后,分析了几个关键因素对籽晶界面温度和温度梯度分布的影响,包括感应线圈的频率和功率、原材料和线圈的高度以及线圈的直径,从中获得了更好的参数范围。基于优化的热场条件,进行了热场验证,成功制备了厚度为9.6mm的均匀多晶沉积。实验表明,优化方案的凸度比没有籽晶的原始方案小3.4mm,厚度分布的标准偏差从5.4降低到2.6。实验还验证了在本文的晶体生长实验条件下,单晶和多晶的生长速率是可比较的。这项工作为优化大尺寸晶体生长的热场提供了重要的参考,无论是在调节SiC籽晶沉积条件还是热场的设计理念方面。
2.建模与实验
感应电源提供晶体生长所需的能量具有效率高的优点。交流电形成交变磁场,在坩埚的侧壁中形成感应电流,该感应电流被用作热源以提供生长8英寸晶体所需的温度条件。先前的研究表明,接近平坦和微凸的温度分布和均匀的温度梯度对高质量晶体至关重要,尤其是当晶体尺寸扩展到6英寸及以上时。鉴于上述要求,重点研究了热场的温度分布,提取了设备和热场的主要结构和材料,其剖面如图1所示。不同的材料用不同的颜色标记。由于使用石英管代替水冷管作为炉壁,支撑热场的底部,因此大部分热量直接传递到环境中。相比之下,忽略了炉壁和支撑结构(图1a)。热场位于感应线圈的中心。在默认位置,线圈在热场中的中间位置比原材料表面低95mm。热区由绝热层、石墨坩埚和从外到内的内部结构、SiC籽晶、籽晶支撑体、气生长室和SiC原料从上到下组成(图1b)。气体压力设定为1000Pa。在顶部绝缘层的中心预留一个直径为6mm的测温孔。温度计(耐久性 1RH)由Fluke Process Instruments制造,其重复性为±0.3%满量程,系统精度为±0.5%Tmeas。模型的主要结构参数如表1所示,包括主要结构的直径和高度。
图1 热场结构和方案。(a) 整个计算领域;(b) 物理场;(c) 不同方案下的热场细节。
表1 主要结构参数。
为了解决籽晶边缘和中心之间巨大温差的问题,设计了各种热场结构来比较和研究它们对籽晶温度分布的影响(图1c)。在初始方案A中,籽晶的上部是坩埚上盖或籽晶保持器作为阻隔层,而籽晶的侧面是支撑结构。方案B将籽晶腔的设计融入到结构中,因此在籽晶顶部有一个厚度为7mm的气生长室,直径范围从100mm到240mm。方案C将气生长室直接延伸到整个籽晶上方。除了顶部的气生长室外,方案D还在籽晶支架和坩埚内壁之间提供了一个小生长室,位于籽晶与顶部气生长室连接的一侧。在四种设计下,其他结构保持不变。
表2 主要材料的物理参数。
表2显示了主要材料的物理参数,包括石墨、毡、坩埚石墨、SiC材料和气体。为了简化计算,将模型中的气体设置为氩气。需要指出的是,导电SiC单晶的实际制备需要将5–20%的氮气与氩气混合,以提供材料所需的载流子。其中,材料的传热系数随温度呈非线性变化。在计算过程中,通过调整绝缘层的热导率,模拟和实验所需的功率是合适的。在建立模型时,电磁热的稳态计算是基于线圈的输入功率。宏观层面上的电磁分析问题在于在一定边界条件下求解麦克斯韦方程组。移动的电流形成一个交变磁场,产生感应电流和热量。电磁加热节点表示电磁损耗Qe(W/m3),作为模型传递部分的热源。它由以下公式给出:
Qrh是电阻损耗,Qml是磁损耗。在数千度的温度下,辐射传热是一个不可忽略的过程。我们引入了面对面辐射,并选择了半立方体方法。材料表面的发射率来自于材料本身物理参数的定义。
在网格生成过程中,将手动设置和优化网格。一般来说,六面体网格具有精度高、效率高的优点,而四面体网格更适合处理复杂结构。考虑到热场域的不同形状,采用了各种策略来确保更好的网格质量和计算速度。表3显示了网格的设置细节,图2显示了设置后的网格图。测温窗口、籽晶、坩埚侧壁和原料均采用六边形结构网格,其网格单元大小被设置为远小于其几何尺寸。根据评估,网格元素的质量平均达到0.9966。生成的网格的总质量高于0.9,表明网格设置很高。
图2:生成的网格。(a) 热场;(b) 籽晶;(c) 生长室。
表3 控制生成的网格的参数和质量。
由于研究主要集中在晶体生长界面的温度分布上,功率和温度的数据一致性是判断模拟数据与实际数据拟合程度的关键。一方面,隔热层直接影响热传递。另一方面,隔热材料批次的一致性不是很好。即使是细节的匹配和使用,也会导致实际物理参数偏离标称值。因此,主要通过调整隔热层的传热系数来进行与实验的拟合。基于初始热场方案,经过多次调整,在相同的感应功率下,模拟温度测量点的温度与测量值之间的差值在10K以内,接近所用温度计的精度。可以认为热场模拟符合要求。边界条件的详细信息如表4所示。默认情况下,感应线圈功率为13千瓦,频率为14千赫,稍后将根据研究条件进行调整。
表4 边界条件。
3.结果和讨论
3.1籽晶界面温度的优化
3.1.1坩埚内部温度分布
不同方案下坩埚的内部温度分布如图3所示。坩埚内部的温度分布特征相似,因为高低温区位于坩埚的下部和上部。高温区的温度达到2700 K,而低温区的温度不超过2450 K。原料的内部温度大多在2650 K和2750 K之间。由于SiC原料上方的空腔的传热效率很低,原料表面的温度在2600 K左右,与接近2400K的籽晶的温度形成约200K的温度差。经过计算,坩埚生长室内的温度梯度达到10–20 K/cm,籽晶温度在2400–2500 K左右,与公开报道接近。这表明,在基本的热场设计方案下获得的籽晶处的温度和梯度可以满足SiC单晶的生长要求。然而,由于顶部绝缘材料变化的影响,不同方案下籽晶处的温度分布差异很大。在方案A和方案B下,顶部温度测量孔的存在使籽晶温度显著降低。
图3 坩埚中的温度分布。(A) 方案A;(B) 方案B;(C) 方案C;(D) 方案D。
径向温度梯度分布更好地说明了温度分布特征,更明显,如图4所示。方案A具有籽晶的最大径向温度梯度。籽晶的半径有20多条等温线,边缘温度梯度达到20K/cm。因此,籽晶的中心和边缘之间的温差很大,并且这种方案不适合均匀的单晶生长。与方案A相比,方案B具有较少的等温线和较小的径向温度梯度,表明顶部籽晶腔起到了积极作用。方案C和方案D下的径向温度梯度呈现出完全不同的特征。籽晶甚至整个生长室中的数值都低于2–4 K/cm。同时,支撑体与籽晶、支撑体与坩埚、坩埚侧壁和支撑体之间的界面处的温度梯度较大。与方案C相比,方案D在籽晶边缘保持较小的径向温度梯度,并且具有更好的径向温度斜率分布。
图4 腔生长室中的径向温度梯度。(A) 方案A;(B) 方案B;(C) 方案C;(D) 方案D。
3.1.2碳化硅籽晶中的温度分布
籽晶、籽晶支架和籽晶界面的温度分布清楚地表明了四种方案之间的差异,如图5所示。相邻的等温线是以每10K的温度差设置的。由于籽晶腔的存在,方案C和D的等温线被极大地压缩到籽晶支架的顶部,具有更好的隔热效果并阻碍了热损失,而籽晶支架中只出现一条等温线(图5a)。方案D的籽晶保持器内部的等温线比方案C的更靠近边缘,这意味着边缘温度降低,这受到籽晶保持器侧面的籽晶腔的影响。图5b显示了不同方案下籽晶的温度分布。四种方案下的籽晶表面平均温度分别为2415K、2425K、2493K和2488K,籽晶表面温差分别为93K、82K、16K和11K。与原方案相比,改进方案的径向温差减小了88%。与上述分析一致,籽晶腔的存在通过改变籽晶背面和侧面的传热,直接影响籽晶表面的温度分布,极大地提高了径向温度一致性。
图5: (a) 籽晶的温度分布(a)方案a;(B) 方案B;(C) 方案C;(D) 方案D;(b) 不同方案的籽晶表面温度。
3.2感应线圈特性的影响
3.2.1加热频率
由于趋肤效应,在感应加热的条件下,热量总是在加热体表面附近几mm的深度产生,然后传递到热场的内部。如图6所示,坩埚内的磁通模式分布主要集中在坩埚的侧壁,尤其是顶部和底部。随着加热频率的增加,坩埚表面的磁通量逐渐减少,平均值从6kHz时的0.0135T变化到16kHz时的0.009T。图6b显示了沿坩埚侧壁的磁通量曲线,其中0mm的高度对应于坩埚侧壁底部。由于线圈中心更靠近坩埚底部,坩埚底部的磁通量明显大于其他区域的磁通量,最大参数比最小参数高出约30%。磁通量的变化率决定了感应电流的大小,这将显著影响温度分布。
图6 :(a) 坩埚的磁通密度(MFD);(b) 沿着坩埚外壁的MFD。
趋肤效应中的穿透深度δ与f−1/2成正比,改变加热频率相当于直接改变加热器的有效厚度,从而间接影响传热过程。在不同频率下,燃烧生长室内的温度分布如图7所示。随着频率的增加,由于穿透深度的减小,反应生长室内的温度逐渐下降。当频率增加2kHz时,相应腔生长室中的温度降低约40K,但腔生长室中的温差总是达到150K以上。从等温线可以发现,在不同频率下,腔生长室中的等温线分布非常相似。籽晶附近的等温线显示出向下的、几乎平坦的和略微凸起的形状。同时,支架中间部分附近的区域显示出向下的、略微凸起的形状,尤其是当它远离籽晶时。这表明当晶体变厚时,晶体倾向于形成M形的不利形状。有必要进一步分析和比较晶体厚度变化的影响。
图7:生长室内温度分布。
籽晶表面的温度和温度梯度分布曲线有助于更好地分析生长条件,如图8所示。籽晶界面的温度随着每2kHz大约50k的频率的增加而降低。无论频率如何,籽晶边缘的温度都略高,比中心部分的温度高约10 K(图8a)。在大多数区域,籽晶表面周围的温度梯度高于−8 K/cm。较大的值在中心表征,但在边缘表征较小的值,这与所需的轻微凸起的晶体生长界面形态一致。随着频率的增加,温度梯度减小,籽晶晶体中部的梯度比边缘的梯度减小得更多(图8a)。这表明,通过增加频率可以提高籽晶表面温度梯度的均匀性,但同时可以降低籽晶表面的温度。
图8:不同频率下的温度和温度梯度。(a) 籽晶表面温度;(b) 籽晶周围的温度梯度。
3.2.2加热功率
在实际实验中,每0.1kW的温度变化约为5K,表明了模型的可靠性。在生长室中,等温线的密度随着功率的增加而增加。生长室内温差从12kW时的约140K增加到14kW时的160K。因此,生长室内温差每1kW增加约10K,表明温度梯度也会上升。另一个现象是等温线的形状。当功率较低时,曲线更平滑,表明在这种情况下籽晶表面的径向一致性良好。结论与上述频率分析一致。在相同条件下,增加加热功率或穿透深度有利于提高坩埚内部的温度,从而降低径向温度一致性。
图9 :生长室内的温度分布。
增加功率对籽晶界面温度和温度梯度的影响如图10所示。随着功率的升高,籽晶界面的温度分别升高约60K、40K和12K。结果表明,提高籽晶界面温度的作用逐渐减弱。这意味着整个热场在不同功率下形成了新的传热平衡状态。当高温区由于传热效应的增强而达到更高的温度时,籽晶处的温度受到顶部温度测量窗口的冷点的影响,其增加不如生长室中的整体移动那么明显。温度梯度的变化与上述分析一致。随着功率的升高,温度梯度大大增加,籽晶的中心部分甚至比边缘增加得更多,这增加了径向沉积条件的差异。这表明,高功率有利于在不改变热场结构的情况下获得大的温度梯度,但以牺牲沉积均匀性为代价,因此需要仔细考虑。
图10:不同功率下的温度和温度梯度。(a) 籽晶表面温度;(b) 籽晶周围的温度梯度。
3.3.线圈与原料的相对位置
3.3.1.感应线圈的直径
根据感应加热的原理,感应线圈的特性和加热体的位置直接决定了感应磁通的分布特性。线圈的半径用“Rcoil”表示。线圈直径的默认值标记为−80 mm,−100 mm表示线圈的直径比默认值小40 mm。不同线圈直径的生长室内温度分布如图11所示。随着线圈直径的增加,生长室内温度逐渐降低,但等温线的形状和密度没有显著变化。这是因为线圈直径的变化直接影响线圈与感应加热体之间的距离,从而改变感应区域中的磁感应线密度。然而,与超过400mm的线圈直径相比,40mm范围的直径变化几乎没有影响。因此,可以近似地认为加热效率改变,并且相对高温区域和相对低温区域的位置没有改变。由于线圈直径的变化比线圈和加热器的变化小得多,因此对温度的影响非常有限。需要指出的是,该距离的调整将涉及不同的加热效率和设备尺寸的限制,这一点需要考虑。
图11:坩埚中的等温分布。
线圈直径对籽晶沉积条件的影响如图12所示。在实验条件下,籽晶界面的温度随着线圈直径每增加40mm而降低约11K,并且降低范围增加。随着线圈远离热场,温度梯度略有下降。尽管如此,总振幅在1K以内。这表明,当线圈和加热器之间的相对距离在合理范围内时,对温度梯度的影响可以忽略。尽管如此,它仍将直接影响籽晶界面的温度。为了提高加热效率和节省电能,建议在线圈和坩埚之间留一个较小的空间。然而,在实践中,盘管需要嵌入循环水进行冷却,并且有两种根据相对于炉壳的位置区分的设备结构:外部盘管类型和内置盘管类型。前者设备中的线圈往往通过石英结构与热场分离,热场与石英管之间以及石英管与热场之间都有一定的距离。线圈可以更靠近前一设备的热场,但应避免因距离太近而导致的短路问题。同时,热绝缘层也会受到感应加热的交变磁场的影响,产生感应电流,感应电流比坩埚更靠近线圈。根据计算,它比坩埚加热体低大约两个数量级,这也需要考虑在内。
图12:不同线圈直径下的温度和温度梯度。(a) 籽晶表面温度;(b) 籽晶c周围的温度梯度。
3.3.2感应线圈的位置
线圈的高度直接影响高温区的位置,并显著影响温度和温度梯度分布。线圈高度在模拟中用“H线圈”表示。默认情况下,线圈高度标记为0 mm,−30 mm表示线圈从默认位置向下移动30 mm。不同线圈位置的室内温度分布如图13所示,相邻等温线之间的温差为10K。随着线圈位置的增加,室内温度逐渐升高,等温线分布变得稀疏。腔室中的温差从大约200K减小到110K,这意味着腔室中的温度差每下降30mm就减小30K,从而减小了腔室中的压力梯度。等温线的形状在不同的位置略有不同。当Hcoil=−30 mm时,籽晶附近的等温线分布略微凸起,而当参数为60 mm时,等温线变得更光滑,这将对温度梯度的一致性产生不利影响。
图13:恒温室内的分布。
如图14所示,线圈的位置越高,温度区域越靠近籽晶表面。线圈位置每增加30mm,温度分别升高约40K、38K和36K。这意味着,随着线圈位置的增加,提高籽晶表面温度的效果降低(图14a)。温度梯度分布发生显著变化,籽晶晶体中部的温度梯度值每上升30mm下降约2.7 K/cm。90 mm的高度变化从−30 mm到60 mm,使籽晶晶体中部的温度梯度降低了近一半。同时,籽晶边缘的数值也发生了显著变化,但径向温度梯度的范围明显减小。这表明,在实验设定的参数范围内,增加线圈的位置有利于获得更高的晶体表面温度和更均匀的径向温度梯度,但以牺牲轴向温度梯度为代价。总之,当通过线圈或热场的相对高度来调节生长条件时,有必要平衡温度梯度和温度的一致性,这可以与加热功率和频率相协调,以获得最佳结果。
图14:不同线圈高度的温度和温度梯度。(a) 籽晶表面温度;(b) 籽晶周围的温度梯度。
3.3.3 SiC原料表面的位置
作为坩埚中的主要固体材料,原料、气体区域和籽晶都在生长室中。原料的高度直接改变了籽晶与原料之间的距离,这将对温度分布产生一定的影响。原材料表面的位置表示为“Hpowd”。默认情况下,原材料的高度标记为0 mm,−20 mm表示原材料表面比默认位置低20 mm。在不同高度的原材料下,燃烧室内的温度分布如图15所示。随着原料表面的位置上升,腔室的空间被压缩。生长室底部的温度,即原料表面的温度也会降低。这是因为在辐射传热占主导地位的条件下,原料具有多孔粉末结构,其高度直接影响该区域的热阻,从而影响传热过程。同时,由于原料水平面和籽晶之间距离的变化,由于距离对辐射的主要影响,籽晶表面的温度上升。
图15:生长室内的等温线分布。
随着原料表面位置的增加,籽晶的表面温度同时逐渐升高,并且范围的增加变得更大(图16a)。从−20 mm到40 mm,原料表面每增加20 mm,籽晶中心的表面温度分别增加约1 K、1.2 K和1.4 K。可以看出,增加幅度并不明显,表明原料对坩埚壁传热的影响类似于减少原料与籽晶之间的传热距离或增加辐射传热。然而,籽晶表面的轴向温度梯度分布变化更明显(图16b)。随着原料表面的增加,温度梯度分别增加了1.2K/cm、2K/cm和3K/cm。当原料表面达到40mm的高度时,籽晶中心和半径为80mm的位置之间的值差达到6.5K/cm。这表明,在实验设定的参数范围内,增加原料表面的高度或缩短原料与籽晶之间的距离,有利于提高籽晶的表面温度和温度梯度,从而提高晶体生长速率,但不利于建立径向均匀的温度梯度。
图16:不同原料高度下的温度和温度梯度。(a) 籽晶表面温度;(b) 籽晶周围的温度梯度。
先前的文献指出,无籽晶下的多晶体沉积速率与单晶相当,表明单晶和多晶总是具有相似的轮廓。多晶沉积生长实际上是多点成核后晶粒生长的过程。与籽晶生长单晶相比,其生长过程不受台阶流模式和单晶取向的严格限制。为了验证模拟结果,使用石墨板代替籽晶进行晶体生长实验。实际晶体及其厚度的结果如图17所示。三组实验包括在原始方案下石墨板作为籽晶,在优化条件下石墨板用作籽晶,以及在优化条件(比较方案)下与小晶体结合的石墨板作为籽晶。晶体生长过程分别进行120小时、120小时和60小时。在原始方案中,晶体更凸,中心的晶粒尺寸与圆周附近的晶粒尺寸不同。在此条件下,最大晶体厚度为23 mm(生长速率为192µm/h),最小厚度为10 mm(生长速度为83µm/h)。其凸度为13 mm。在优化方案下,最大晶体厚度为16mm,最小厚度为9.6mm,凸度为6.4mm。在对比方案下,晶体表面相对平坦,与优化方案相似,并且结合的小晶体芯片具有相对均匀的沉积。比较方案中的多晶晶粒较小,因为小晶粒的融合随着晶体生长的进行而发生。在原始方案下,晶体的最大径向生长速率是最小生长速率的2.3倍,而在优化方案下,该值为1.7。后者的生长速率分布在100–130µm/h左右,其生长速率均匀性大大提高。在优化方案下,由于引入籽晶腔作为晶体生长的驱动力后,轴向温度梯度减小,因此晶体生长速率的平均值较慢。对于与小晶片结合的石墨板,同一圆周上的单晶区域和多晶区域的厚度是闭合的。扣除0.8mm的晶片厚度后,单晶的生长速率约为周围多晶生长速率的90%。通过优化条件,成功地制备了直径为200mm、厚度约为10mm、轮廓几乎平坦且略微凸起的多晶体。因此,优化方案可以在沉积均匀性方面提供更好的晶体生长条件。
图17:(a) 200mm多晶;(b) 晶体厚度和生长速率。
同时,实验验证了在无籽晶体的条件下,可以使用石墨板等替代材料进行多晶体生长,作为单晶生长的探索方法。
4.结论
基于仿真软件的电磁加热、传热和表面辐射模块,首次建立了感应加热PVT设备中8英寸SiC晶体生长的热场模型。经过与实验的拟合和调整,模拟与实验之间的温差接近10K,表明了模拟结果的可靠性。针对大尺寸晶体生长中温度条件径向均匀性差的问题,首次提出了籽晶腔来改善局部温度分布。研究表明,新设计的籽晶表面温差从93K降低到11K,降低了约88%,成功地获得了适合晶体生长的温度条件。
同时,还对感应线圈的特性和几个关键结构的位置进行了研究和分析。首先,较高的频率和较低的功率有利于提高籽晶表面温度梯度的均匀性,但会降低表面温度。其次,较小的线圈直径有利于提高籽晶的表面温度和加热效率,而对温度梯度的影响很小。第三,增加线圈的相对高度有利于提高温度梯度的均匀性,但会降低温度梯度值。第四,原料表面和籽晶之间的距离越近,有利于提高温度和温度梯度。尽管如此,它还是加剧了径向条件的不均匀性。
最后,进行了三个实验来验证仿真结果。在优化的条件下,成功制备了厚度为9.6mm、平均生长速度为110µm/h的均匀沉积的8英寸多晶,晶体的凸度比原始方案降低了50%,验证了优化方案可以为大单晶的生长提供条件。此外,研究结果表明,在相同条件下,多晶与单晶具有相似的生长速率,支持了热场条件的可行性,多晶沉积也可以验证PVT方法的可行性。
审核编辑:汤梓红
-
半导体
+关注
关注
334文章
27246浏览量
217914 -
功率器件
+关注
关注
41文章
1757浏览量
90403 -
SiC
+关注
关注
29文章
2796浏览量
62582 -
晶体生长
+关注
关注
0文章
2浏览量
65
原文标题:8英寸SiC晶体生长热场的设计与优化
文章出处:【微信号:芯长征科技,微信公众号:芯长征科技】欢迎添加关注!文章转载请注明出处。
发布评论请先 登录
相关推荐
【转帖】一文读懂晶体生长和晶圆制备
8英寸!第四代半导体再突破,我国氧化镓研究取得系列进展,产业化再进一步
NaCLO3晶体生长控温实验分析设计
晶体生长参数的检测与优化
基于LabVIEW晶体生长检测系统的圆弧拟合技术
GT Advanced推全新MonoCast晶体生长系统
晶盛机电:12英寸加工设备的研发和产业化正在加速推进
晶盛机电公司成功生产出行业领先的8英寸碳化硅晶体
科友半导体突破8英寸SiC量产关键技术
天岳先进、天科合达正加快8英寸SiC产能建设,满足客户需求
芯片制造工艺:晶体生长、成形
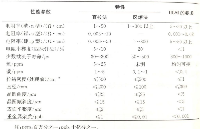
评论