添加热界面材料(Thermal interface material,简称TIM)作为目前最具有优势的散热方式,由于其制备工艺简单,对设备无腐蚀无损害,不增加额外能耗等优点成为现今阶段攻克电子器件散热问题最引人注目的方法。研究新型热界面材料也成为现今散热研究的主流方向。
电子封装中的热传导情况
热界面材料的基本概念及作用机制
电子产品封装中的一个重要方面是确保电子设备使用过程中产生的热量能够有效的排除。而对于日渐小型化微型化的便携式电子产品,散热问题成为影响整个产品质量的关键问题。而热界面材料指的是涂敷在散热电子元件与发热电子元件中间,降低两个电子元件之间接触热阻所使用的材料总称。
热界面材料充分地填充了固体表面缺陷之间的界面间隙,有效地排除了空气,使得产热元器件与散热器件之间的接触更加密切,大大降低了界面接触热阻,建立起了高效的热传递通道,从而使得散热器件的工作效率得到了最大化的提升。
TIM的主要作用是填补间隙,这就要求TIM必须是柔软且可润湿的材料。电子封装中的TIM本身应该拥有较好的散热能力,向其中添加高导热的填料是改善TIM热性能的主要方法。
热界面材料作用机制示意图
热界面材料的分类
现在已用于工业生产的热界面材料主要分为以下几种:导热垫片、导热膏、导热凝胶、导热相变材料。
导热垫片
是一种传统的热界面材料,由高分子聚合物材料为基体,加入拥有较高热导率的填料和助剂通过加热固化制备得到的一种片状材料。与其他的热界面材料不同,导热垫片在固化之后才开始对电子设备的封装。其填充在芯片和散热元件的缝隙以排除产热原件和散热原件中的空气进而提高整体的导热效率。
由于导热垫片较为柔软并且贴合性较好,除了导热还有密封、减震、绝缘的作用,导热垫片的制备工艺技术非常简单并且产品制备流程较为成熟,目前在热界面材料市场上占有非常大的份额。
但是,导热垫片在使用的过程中,压力和温度是两个相互制约的因素,随着设备运转一段时间后的温度升高,导热垫片会发生软化、蠕变、应力松弛现象,其机械强度也会随之下降,最终导致电子封装结构中的压力降低,影响电子设备的性能。
导热膏
又称导热硅脂,一般由高导热的固体作为填料,流动性优良兼有一定粘度的液体作为基体通过混合脱泡而成。目前最常用的导热填料为无机填料,主要有金属颗粒(铜、银、锌等)、氧化物类(氧化铝、氧化锌、二氧化硅等)、氮化物类(氮化硼、氮化铝等)以及碳材料(碳纳米管、石墨烯等),这些导热填料都有比较优越的导热性能。而最常用的基体是硅油,主要为二甲基硅油,乙烯基硅油、氨基硅油、苯基甲基硅油等,他们均具有良好的润滑性以及与填料之间较好的相容性。
与其他热界面材料相比,导热硅脂通常能提供更好的热性能和更短的制造周期,它的热导率大概在在3~5 W m-1K-1之间。导热硅脂的粘度比较小,这可以使其轻易地填满界面空隙,在使用过程中,它的粘结层厚度(BLT)也非常小,因此相应的热阻会随之减小,其热阻可以低至0.1 K cm2W-1。
然而,导热硅脂也存在许多明显的缺点。在使用寿命期间容易受到各种失效机制的影响,比如硅脂渗油或者因干燥而失效,这直接造成了热阻的增加;另外,当电子设备通电或断电时,会导致芯片组和散热器件之间的相对运动,这往往会将导热硅脂挤出接口间隙,造成硅脂溢出污染电路板,引起短路等风险。
导热凝胶
其作用机制是将还未固化的液态聚合物通过用手动或自动的方式填入电子设备的界面之中,然后再在一定条件下固化成热固性聚合物材料,从而实现最大程度地贴合两相界面,减少空隙。
一般的导热凝胶是由高导热的填料与高分子基体中组合而成。根据导热填料是否导电将导热凝胶分为两类:绝缘导热凝胶以及导电导热凝胶。而制备导热凝胶所使用的高分子基体主要有有机硅、聚氨酯、环氧以及其他类的导热凝胶。导热凝胶易加工成型、工艺简便且可实现全自动封装,目前已经广泛应用于微型电子器件领域,并且逐渐成为了热界面材料的研究热点。
导热凝胶的缺点是使用中需要固化步骤,其热导率也比导热硅脂低;另外,由于导热凝胶的粘结性能比较弱,在使用过程中可能导致其出现分层现象,这会影响到电子设备长期有效的散热。
导热相变材料(PCM)
能够随着温度的变化由固态变成液态,通过其中产生的相变焓使热量得以排除。导热相变材料由于其低成本,特有的储热性能以及灵活精准的控温功能而受到了热管理方面的极大关注。
现今各种散热器的设计广泛使用到了PCM材料,尤其是较大规模的电子器件。通过使用PCM填充的散热器,电子器件的散热性能得到较大的改善。石蜡是最常见的导热相变材料,拥有较高的潜热用来固相转变为液相,这使得其具有非常优秀的储热能力,可以作为热界面材料应用的一种有发展前景的材料。
导热相变材料本身拥有非常好的热能转化能力但导热能力却有所缺乏,所以在实际应用中,通常在石蜡中加入高导热的填料制备复合导热相变材料以填补其短板,使其能够实现高效的热传导,通常采用的填料有氧化铝、氮化硼以及氮化锌等。
热界面材料用导热填料研究进展
陶瓷
陶瓷同时具有高热导率和优异的电绝缘性,特别适用于要求电绝缘领域。在已报道过的陶瓷材料填料中,氮化硼(BN)具有非常高的热导率,正成为热管理应用中最有吸引力的研究对象。
碳材料
碳材料,如石墨烯、金刚石、碳纳米管已经被证明具有高的导热系数,因此采用碳材料作为导热填料有望大幅提高聚合物的导热系数,制备出高性能热界面材料,受到了国内外学者的广泛而深入的研究。
但是,碳材料作为导热填料最大的问题是:由于其一维和二维材料的特性,当添加至聚合物中时,造成粘度急剧增加,使得其添加量有限,在实际应用过程中受到限制。
杂化填料
将两种不同种类、不同尺寸的导热填料进行复配,制备杂化填料,可以比一种导热填料更能提高聚合物的导热系数。例如,鉴于石墨烯与氮化硼具有良好的声子匹配性,可将石墨烯与氮化硼进行复配,制备石墨烯/氮化硼杂化填料。
热界面材料的市场应用
随着电子技术的快速发展,热界面材料的应用愈加广泛,需求量越来越高。根据BBC Research的报告,全球热界面材料市场规模已超过9亿美元,年增长率达7.4%。伴随5G技术的应用,电子产品和通信模块轻薄化和性能提升的速度加快,将带来热界面材料需求的新一轮快速增长。
热界面材料应用市场占比是随着各终端领域的变化而发展的,以通信网络(5G)、汽车电子(新能源汽车)、人工智能、LED等为代表的领域未来发展潜力巨大,相应的会带动热界面材料市场的发展壮大。
一是在通信行业规模化应用,5G时代将带来巨大的增量需求。由于通信设备功率不断加大,发热量也在快速上升。导热材料能有效提高设备可靠性,因此在通讯领域有着广泛的应用。近年来,在电信运营商投资的带动下,通信设备行业目前仍旧保持了较快的发展速度。5G时代下,基站投资额和基站数量将快速增长,对程控交换机和移动通讯基站设备的需求将快速增加。
二是支撑5G时代下的物联网应用,除了手机和电脑,5G终端还扩展到了汽车、家用电器、智能穿戴、工业设备等,终端设备的丰富也将直接拉动对导热材料和器件的需求,利好导热材料行业。
热界面材料的产业现状
自20世纪90年代以来,以美国为代表的发达国家大学和科研机构(如麻省理工学院、佐治亚理工学院等)、美国军方(DAPA项目)和骨干企业(Intel,IBM等)都投入巨大力量持续进行热界面材料的科学探索和技术研发。这带来了美国和日本的企业,如Laird(莱尔德)、Chomerics(固美丽)、Bergquist(贝格斯,汉高收购)、Fujipoly(富士高分子工业株式会社)、SEKISUI(积水化学工业株式会社)、DowCorning(道康宁-陶氏)、ShinEtsu(信越化学工业株式会社)和Honeywell(霍尼韦尔)等占据了全球热界面材料90%以上的高端市场。
我国高端热界面材料基本依赖从日本、韩国、欧美等发达国家进口,国产化电子材料占比非常低,大大阻碍了我国的电子信息产业发展和限制终端企业的创新活力。2018年开始,中美贸易摩擦升级导致的“中兴芯片制裁”事件和“华为制裁”事件,充分说明:发展国产化热界面材料对于避免芯片核心技术和集成电路产业受制于人具有重要的现实意义。
面对激烈的竞争,我国在国家层面也充分重视。国家科技部从2008年部署、2009年开始启动02重大专项(极大规模集成电路成套工艺与装备),2014年启动集成电路大基金,经过近十年的支持,我国集成电路产业取得了长足的发展,封测产业跻身全球前三。但作为物质基础的高端电子封装材料,仍然基本依赖进口。
热界面材料在电子等行业应用广泛,国家也出台了相关扶持政策促进国内热界面材料产业的发展。例如,2016年国家科技部启动“战略性先进电子材料”专项,布局了“高功率密度电子器件热管理材料与应用”,其中研究方向之一为“用于高功率密度热管理的高性能热界面材料”。
在热界面材料这一细分市场中,美国和欧洲公司在国际及国内中高端市场上处在垄断地位。现代电子产业发展于国外,因此相关的基础材料商出现的也比中国早。由于我国本土企业早期缺乏核心技术,主要高端导热材料生产基材还是需要国外生产制作商提供,产品性能指标以及研发积累与欧美企业仍存在一定差距。
对比国外知名的热界面材料生产厂商,如日本信越、美国道康宁、德国汉高、美国固美丽等,我国热界面材料生产厂商的性能较差,无法满足高端芯片的封装要求。其主要问题是,我国热界面材料生产的原材料(如有机硅、氧化铝、铝和氮化铝)纯度不够,热界面材料复合工艺水平有待提高。
-
元器件
+关注
关注
112文章
4746浏览量
92753 -
Tim
+关注
关注
0文章
81浏览量
17941 -
电子材料
+关注
关注
0文章
63浏览量
10782
原文标题:最具优势的散热方式——热界面材料的分类、市场应用及产业现状
文章出处:【微信号:gh_e972c3f5bf0d,微信公众号:艾邦加工展】欢迎添加关注!文章转载请注明出处。
发布评论请先 登录
相关推荐
导热界面材料对降低接触热阻的影响分析
中国锂离子电池原材料市场调查分析报告2008-2009版
电路设计散热材料的选择
LED界面散热材料的分类与散热解决方案分享
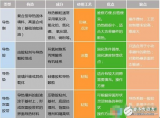
芯片发热为什么要应用导热界面材料散热?
杜邦首次展示最新研发的BETATECH聚氨酯热界面材料
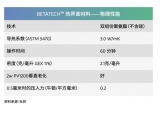
IDTechEx在这份新报告中深入研究了热界面材料的形式和组成
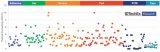
评论