一、抗蚀油墨篇
1.历史的回顾
用于电路板耐蚀刻掩膜的油墨大约在上世纪中期问 世,而以前的掩膜均为以重铬酸盐为感光剂再加入胶体而成,这期间经过了三个阶段:
(1)以虫胶为胶体的掩膜:这项技术最初是从前苏 联那里学来的。用乙醇溶解和显影,但因操作繁琐,价格较高易起火不安全被逐步淘汰。
(2)以骨胶为胶体的掩膜:这项技术是从印刷制版 和标牌、面板的制造那里移植过来,不耐贮存,因需高 温固膜, 而当时的基材不耐高温,经过反复研究试验后 又发明了物理固膜和化学固膜相结合的方法,只加温至 100~130就可以了,其骨胶(加少量蛋白片或不加)的组 成主要为蛋白质胶体而成。在温度稍高时不易保存,最初 有人提出加防腐剂,但加入后影响曝光性能。后来由聚乙烯醇胶体取代
(3)聚乙烯醇胶体掩膜:此胶体掩膜克服了以上 操作繁琐和贮存期短的弊病,配制好的胶液最长可用 30~40天,所以这种感光胶使用的生命力特强,延至干膜抗蚀剂的出现才慢慢消失。
2.最早的抗蚀油墨
早在上世纪七十年代,随着电视机、录音机、半导体、 收音机产量的飞快增加,用感光胶制造图形已经无法满足 生产的急需。唯一的出路——丝网印刷。当时用蚕丝丝网 制网版,但印料(抗蚀油墨)无处购买。此时行业内专家 们, 自己动手制出自干型抗蚀油墨和烘干型抗蚀油墨,克 服了当时的这一重大的技术难题,为印制板的生产加快了速度。
(1)自制抗蚀油墨
配方1:石油沥青、滑石粉、燥油、溶剂汽油等,自调粘度。
配方2:厚柒、滑石粉、色料、松香、松节油。
自制抗蚀油墨的问世,解决了当时的电路板的批量不 断上升的矛盾,但配制时均为代用设备和材料,虽然各村 有各村的高招,但一致性较差,有时会随着天气的变化油 墨也患“感冒”,最突出的毛病就是细度不够,所以越来越突出的影响着线条的光滑程度和精度。
(2)抗蚀油墨的商品化:
当油墨商们看到此商机后,根据使用工艺很快就制出 烘干型和自干型的抗蚀油墨,随着需求量的增加,在产量 增加的同时又推出碱溶性(碱性去墨)的抗蚀油墨,在环保上又迈进了一步,大大方便了用户。
(3) UV固化抗蚀油墨:随着电视机生产线引进的风潮和其配套的单面板生产线也不断引进,同时也引进了单面板印制图形的UV固化油墨,看准我国的市场,国外和一些地区的UV品牌陆续登 陆,而且价格不菲,不久国产的民族品牌问市,结束了进口 品牌一统天下的局面,而且价格下降使不少中小型企业受益。与此同时,和其配套的UV固化设备也相继面市。
3.图形电镀技术和油墨
八十年代初图形电镀技术(即平时所的反镀法,现在 仍在应用)传入我国。开始时全部用干膜抗蚀剂做抗电镀 的掩膜当时价格虽然很高,但电路板的售价更高,因此制造 商都能接受,随着电路板价格的下滑,根据产品情况有的制 造商们开始选择直接网印图形抗电镀油墨,以维持正常的利润。
4.抗电镀油墨
一般均为热固能够满足抗二次镀铜,镀铅锡的工艺条 件,细算起来价格只有干膜的二分之一或三分之一,但是工 厂需有优秀的制网版技术和网印技术,不足的是线条边缘 的光滑程度和陡直程度远远赶不上干膜,严格来说,只能 制出0.6mm以上的线条,对于一些密度细线的板子就无能为 力了。因此不少制造厂两项工艺同时应用,视不同的线粗和 密度而不定。此种油墨最早均为进口,现在国产和进口同时在市场上销售质量和价格差异较小。
5.光成像抗蚀抗电镀油墨早在上世纪的八十年代中期,南方的一个PCB厂开始引进一个日本品牌的光成像抗蚀抗电镀油墨(以下简称湿膜)。首先开创了用湿膜制造图形掩膜的先河(当时大都用干膜),随着时间的流逝大家对湿膜开始有了认识,几年后应用范围不断扩大。为此,该厂还举办了湿膜的应用学习班,使其逐步推广。
(1)湿膜的应用和推广:湿膜以它优良的分解率、良好的耐电镀性、耐蚀刻性(在一定条件下也耐碱性蚀刻)和良好的加工性,深受用户的青睐。尽管对于使用干膜和湿膜的争论还在继续,但湿膜应用范围之广、扩大速度之快已经成为公认的事实,尤其在 多层板的制造厂,对于内层的图形蚀刻早已经开始以湿膜代 替,并且很快地发展开来,这是因为:一是从价格上分析它 只有干膜的1/2或2/3,而且几乎是零的废物排放(而干膜则 需处理揭下的涤纶薄膜)。二是使用湿膜无需增添专用设 备(凡具备制造双面板的公司都具备使用湿膜的条件)。三 是因湿膜在一定条件下能耐碱性蚀刻,所以生产厂家只备 一台碱性蚀刻机,既能完成多层板内层的图形蚀刻又能完成以PbSn或Sn层为掩膜的外层图形蚀刻。
到目前为止,湿膜的应用在中小企业极为普遍,凡是 使用图形电镀工艺的中小企业,基本上都使用湿膜来制造图形。
(2)湿膜的发展
我国PCB发展的飞快速度,受到国外及有关地区PCB材 料供应商的注目,尤其是台湾及香港,PCB制造厂的内迁,使 PCB事业不断发展状大,也激活了湿膜的制造及应用。看准 我国的PCB市场,日本、南韩、德国、美国、法国、英国、意大 利、瑞士等国家的湿膜品牌,也纷纷登陆珠江三角洲和长 江三角洲,形成了进口品牌的湿膜在我国市场上竞争的局 面。结束了一两家国外湿膜品牌垄断的时代。在上述的进口 湿膜品牌中以日本最多,其他国家只有一、二个品牌。随着 台湾及香港PCB厂的内迁,相关配套材料也相继进入,其中湿膜是最多的一项,而品牌的增加就像分子裂变的形式湿膜的制造、经营、销售形成了很大的市场,湿膜制造厂虽不像雨后春笋,但也算得上是星罗棋布了。
审核编辑 黄宇
-
电路板
+关注
关注
140文章
4965浏览量
98085 -
PCB
+关注
关注
1文章
1813浏览量
13204
发布评论请先 登录
相关推荐
PCB焊接后焊接位置附近油墨起泡问题
一种可以提升动态血糖监测均匀性和精确度的导电油墨
油墨塞孔之大忌,这个要求不合理
PCB高可靠性化要求与发展——PCB高可靠性的影响因素(上)
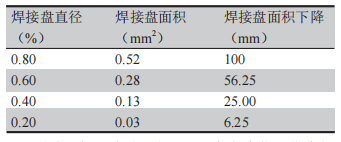
Haydale HDPlas™ 技术导电油墨在微量元素分析中的应用前景
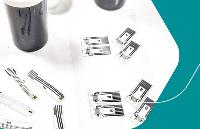
pcb板树脂塞孔和油墨塞孔的区别?
高导电石墨烯导电油墨
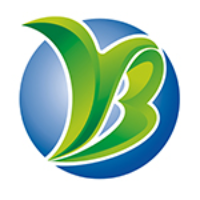
用于印刷电子柔性丝网印刷的高导电石墨烯油墨
用于印刷电子柔性丝网印刷的高导电石墨烯油墨
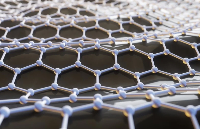
导电油墨:电子面膜制作的关键核心③
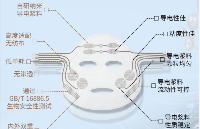
揭秘UVLED油墨固化机:低能耗、无污染,助力绿色印刷发展
PCB板的颜色应该怎么选?为什么绿色最常见?
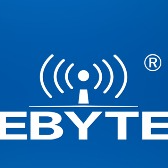
略谈PCB油墨应用及发展——(下)
略谈PCB油墨应用及发展——中
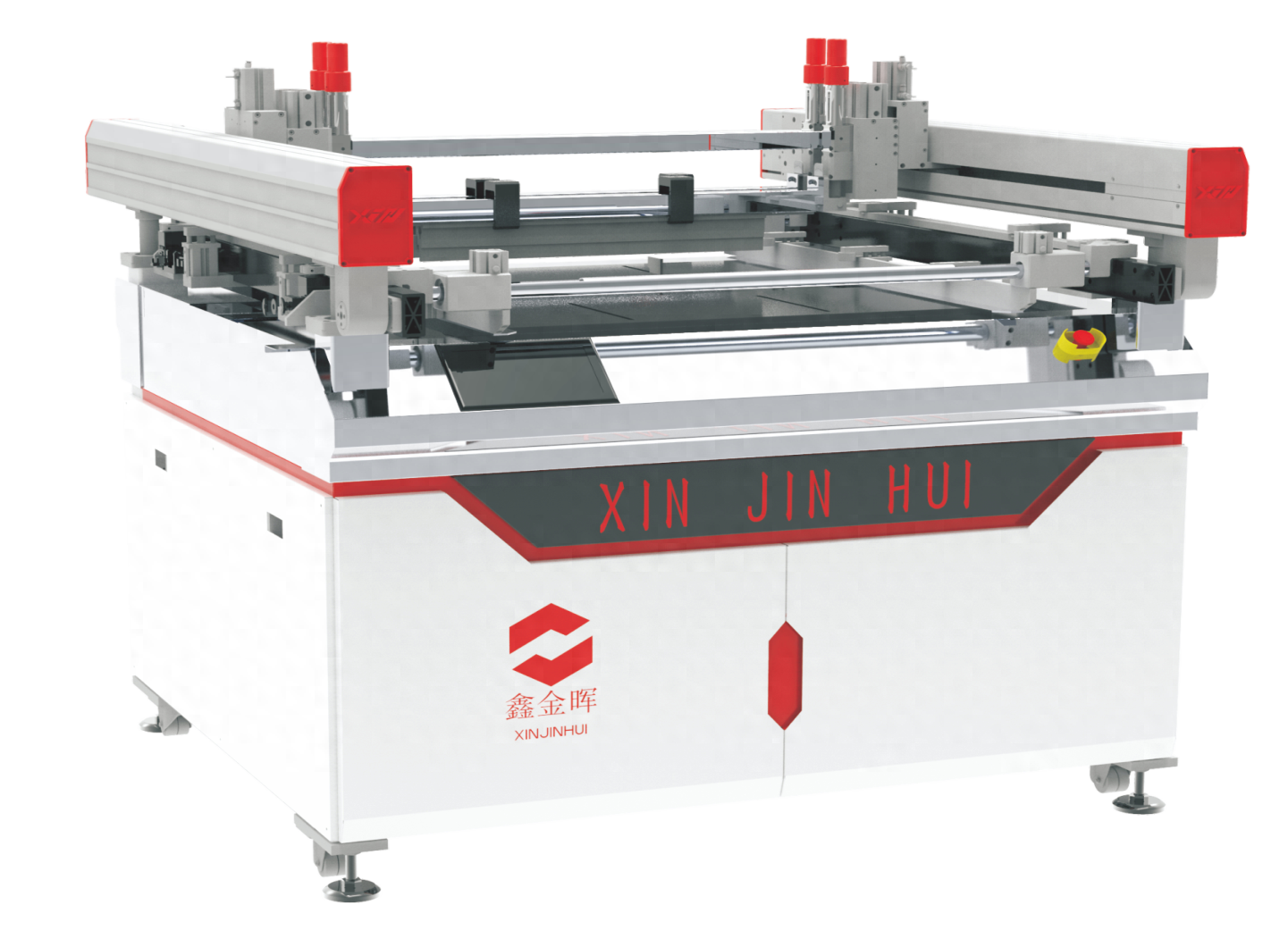
评论