在制造业中,冲压自动线规划是确保高效生产和卓越质量的关键环节。成功的规划需要综合考虑多个因素,以满足产品设计、生产能力和质量标准等方面的要求。本文将围绕冲压自动线规划的几个关键考虑因素提出阿童木的思考。
1.是否采用同步技术
同步技术在冲压自动化领域的广泛应用已经受到了广泛认可,对提升生产效率具有重要意义。
在传统的冲压自动化生产过程中,压机通常采用“单次”运行模式。下料手(下料机械手/机器人)需要等待压机完成整个冲压循环,滑块回到上死点并停止后才开始动作。上料手(上料机械手/机器人)则需等下料手完全退出压机工作区域后启动。压机滑块必须等到下料手完全退出工作区域后才开始下行,导致每个循环周期较长,直接影响整体生产效率。
同步技术采用“连续”运行模式,通过精确计算,使上下料手和压机滑块实现“同步”启动。下料手在滑块回程上行到一定角度(回到上死点前)后开始取件,上料手则在滑块下行到一定角度前完成送件。在确保整个过程不发生干涉的前提下,下料手有足够时间将工件送入下道工序。为保证相邻两台压机滑块运动中始终保持合理的相位差,从而使上下料手的工作周期相对延长。
特别是对于大批量大型覆盖件冲压生产而言,高速冲压自动线结合同步技术相比其他方式,如包括单滑块多工位在内的方式,具有更为显著的优势。
2.压机重点参数——滑块行程
在进行生产线规划时,考虑到众多压机参数,滑块行程是其中至关重要的因素之一,直接影响自动化实现的可行性和难易程度,因此在规划过程中需要给予重点关注。
滑块行程的选择紧密关联着所需生产的冲压件的拉延深度和端拾器的高度等因素。在规划阶段确定滑块行程时,必须确保上下料手在抓取工件水平运动的过程中,端拾器与上模最低点及下模最高点之间保持足够的安全空间。
考虑到大型覆盖件的拉延深度通常超过200mm,因此,大型高速冲压自动线的压机滑块行程一般需要在1000mm以上。这样的设计确保了生产线的适用性,为安全、高效的自动化冲压过程提供了坚实的基础。
3.模具及端拾器的结构形状
为了获得更理想的干涉曲线,除了需要专注于滑块行程、速度-加速度曲线等压机固有参数或特性,还应考虑模具和端拾器的结构形状。合理的模具和端拾器结构能有效弥补自动化方面的不足,提高冲压自动化生产的可行性。
此外,在模具设计中,还需要考虑以下几点:确保同一生产线上模具闭合高度相差不宜过大,最好保持一致;尽可能在下模安装制件到位传感器;统一模具安装槽的位置,以减少自动夹紧器的数量,从而降低成本;确保废料能够顺利排出工作台外,对于排料困难的位置可考虑加入冲顶装置;成型类模具应配备制件顶松装置,如弹顶销或顶出气缸,并尽量避免采用较大的斜楔机构,多采用旋转斜楔。这些考虑因素将有助于优化整个冲压生产过程。
4.对钢板料垛的要求
与手动生产线相比,自动化冲压生产对钢板毛坯料垛的规整程度提出了更为严格的要求。若料垛不够整齐,可能导致磁力分张效果不佳(容易出现双料现象),同时影响拆垛手的板料抓取位置的准确性等问题。因此,在投入自动生产线之前,为确保生产效率达到目标值,必须清晰明确对钢板料垛的要求。
此外,汽车冲压产线还配置有双料检测器。过去,通常会选择进口产品来满足这一需求,但现在阿童木成功研发出了可替代进口产品的解决方案。这不仅为用户提供了更多选择,同时还加入了更多本土化的功能,使其更加贴合特定需求,成为更为适宜的选项。
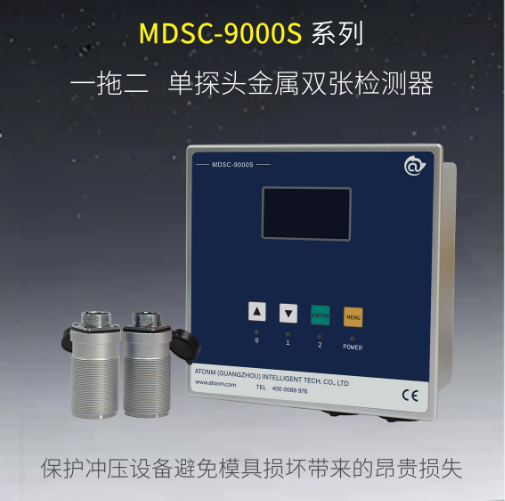
5.对冲压件工艺排布的要求
(1)确保同一模具的送料中心与生产线中心的对应关系尽量保持一致;
(2)在制件传输过程中,特别是在高速冲压线和多工位情况下,积极减少旋转,避免制件绕Z轴旋转,以确保稳定性;
(3)在同一生产过程中,务必使送料面的高度尽可能保持一致,这有助于有效减少节拍损失。
-
制造业
+关注
关注
9文章
2238浏览量
53603 -
自动线
+关注
关注
0文章
4浏览量
6533
发布评论请先 登录
相关推荐
冲压机数据采集与深控技术 “不需要点表的工业网关” 应用
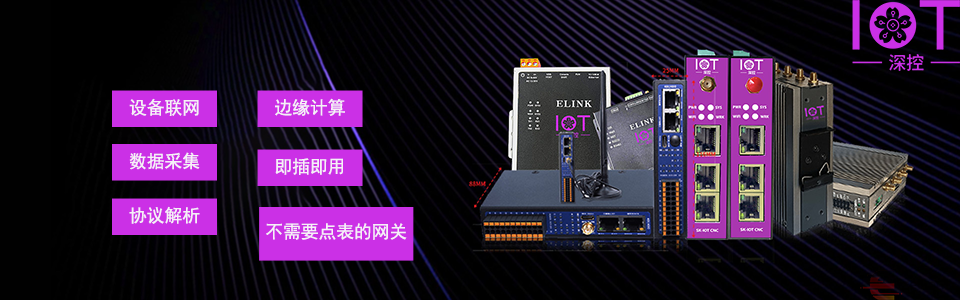
多台仓储AGV协作全局路径规划算法的研究
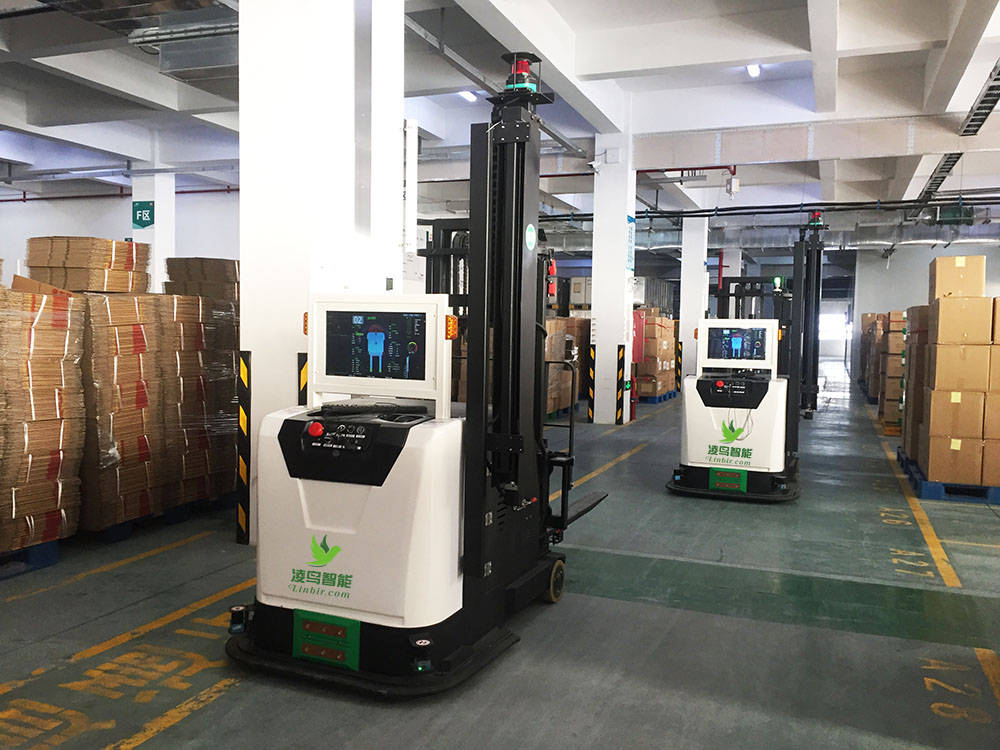
深控技术 “不需要点表的工业网关” 在冲压机上的应用
汽车零部件热冲压工艺的关键技术
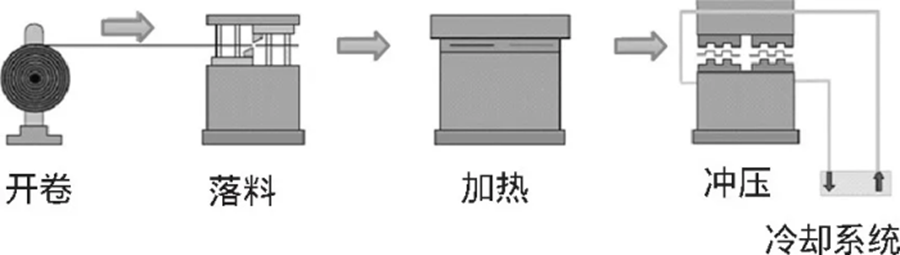
高速pcb布线规则有哪些
冲压模具如何实现视觉在线检测?
高效质量控制:阿童木双张检测传感器在五金冲压产线的成功案例
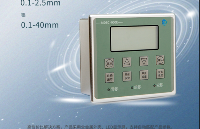
射频PCB走线规则简析
常见的五金冲压件外观缺陷问题
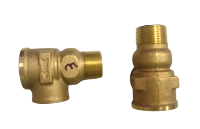
【选型指南】各大行业自动化生产线冲压叠料检测传感器
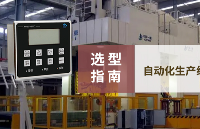
自动化设备行业连接器应该如何选择
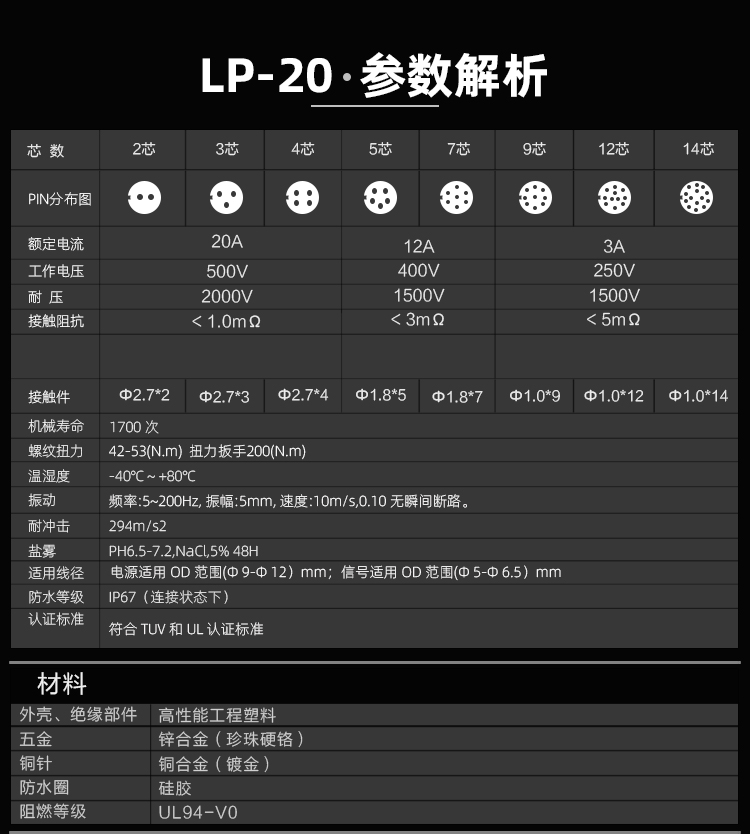
分析伺服冲压自动化线的生产工艺及装置
电动机绕组的接线规律
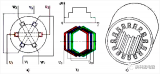
评论