摘要
全固态电池的研发是为了“防止被颠覆”,其产业化需以市占率突破1%为标志。
自推进以来,全固态电池的必要性和产业化始终是备受争议的存在。
全固态电池的研发是为了“防止被颠覆”,其产业化需以市占率突破1%为标志。在近期举办的全固态电池创新发展高峰论坛上,中国科学院院士、清华大学教授欧阳明高发表了上述观点。
论坛上主流观点认为,全固态电池产业化较可能在2030年取得突破。由于固态电池可同时满足高安全性、高能量密度、高功率、高温度适应性等,且材料选择的范围更高,具备“颠覆”液态电池的潜力。
不过,目前国内发展全固态电池产业面临的挑战是巨大的,具有跨学科的特性、技术门槛极高,包括材料界面、工艺、产业链、设备等,需要业界进行协同创新。
为什么需要全固态电池及产业化?
中国科学院院士、清华大学教授欧阳明高指出,固态电池相对于液态电池是颠覆性技术,行业应提高重视程度、积极研发,以防范风险。
首先,动力电池行业虽然已进入产能过剩的阶段, 电池成本不断下降,但并没有完全满足终端电动汽车客户的需求,如怎么在全寿命周期内不析锂、不影响寿命、不发生安全事故,低温续航,如何解决硅负极膨胀率高的问题、以提高负极中硅的含量、最终提高体积能量密度(磷酸铁锂电池)等。
其次,在新一轮技术创新周期中,行业已卷向“提质降本增效”,需要通过材料换代来实现。例如,行业内对于比能量的追求,并不单纯是提升比能量,而是在期待“比能量提升的同时,成本不需要提升太多”的颠覆。因此,行业需要居安思危,电池需要平衡的性能体系,全固态电池具备技术“颠覆”的潜力。
东风汽车集团有限公司研发总院副院长史建鹏同样认为,包括安全性、里程焦虑、能量密度在内的液态锂电池三大痛点,受到现有材料体系已接近能量密度上限因素的限制,本质上没有得到解决。
此背景下,产业希望构建新一代动力电池。其中,由于采用了固态电解质(不易燃、耐高温、化学活性低),固态电池能大幅提升电池安全性;又因为固态电池可兼容高比能正负极,将打开能量密度天花板,故有望成为动力电池下一轮技术竞赛的关键。
南方科技大学教授许晓雄认为,高安全、高性能、低成本是锂二次电池产业发展的必然趋势,高性能要求则囊括了高能量密度、高功率(可快充)、长寿命等,全固态电池有望实现以上高性能要求。
弗迪电池首席技术官孙华军则提出,全固态电池产业化能带来哪些价值,需要对标2030年液态电池会是什么状态来思考,液态电池也在持续改进;而且要从系统层级来思考,囊括如重量能量密度、体积能量密度、成本维度等。
2. 全固态电池的量产标志是什么?
从全球全固态电池产业化路线图来看,产业化时间聚焦在2027-2030年。
欧阳明高进一步指出,较为合适的产业化定义是全固态电池市占率达到1%。参照2023年2000万左右的电动汽车销量预期来看,即全固态电池装车量超过20万辆。
而一汽研究院院长王德平认为,全固态电池在2027或2030年的产业化,可能只是达到一定程度的小规模、小批量的示范性装车。对固态电解质等关键问题的突破,有望加速产业化的进程。
孙华军认同上述观点并表示,新电池技术的应用遵循一定规律,如锂电池先应用在电子消费产品上,经过长时间积累后才过渡到动力电池产品。按此推算,固态电池也应该先在其他领域应用,再逐渐扩展至电动汽车。
另据孙华军披露,比亚迪10年来持续进行着固态电池的研发,主要走硫化物路线,目前已可实现保留10%电解质的相关产品。
3. 全球固态电池产业布局呈现出何种差异性?
欧阳明高总结,从全球固态电池产业布局来看,中国企业最多,然后是日本、韩国,实力强劲。美国主要是一些创业企业,与欧洲合作广泛。
日本在电池与整车性能匹配结合方面较有优势,已经搭建起官-产-学联盟。如丰田、本田、日产,同时进行全固态电池研发和整车生产,其中丰田的研发进度最为深入。
韩国三大电池厂在全固态电池方面已取得实质性进展,尤其是三星,国内部分团队的任务之一,便是复现三星的全固态电池。
美国以创业企业为主导,缺少车企、电池厂的力量,一方面靠资本市场支撑,一方面则靠欧洲车厂的合作,如Solid Power和宝马合作等。
中国的固态电池技术路线相对多元化,以固液混合为主,以氧化物路线为主导。目前,国内半固态电池池正在试装车,但是良品率、电池成本、充电倍率、循环寿命这些问题还需要解决。
全固态电池技术方面,国内外专利布局存在较大差距。丰田有超过1300项相关专利,截至2023年10月,国内公司有关全固态电池的专利未超过100项。
4. 固态电池整体上面临什么挑战?
据史建鹏总结,目前固态电池存在四大挑战。
首先,固态电池所需,不只是在现有三元正极材料体系上去做增量或补充,而是更为复杂的高性能正极材料。短期内,正极材料沿用高镍三元体系,安全性差且易发生热失控,长期应向超高镍、富锂锰基、高压尖晶石等材料迭代。关于高电压下三元正极易产气导致电池鼓包的问题,解决策略是通过单晶化、氧化物包覆、金属掺杂等手段进一步提升电压。
第二,固-固接触的问题,既导致锂离子传输电导率低,也影响电池能量密度,可通过引入电解质膜改性等策略来解决。而现有设备难以支撑制备20μm以下电解质膜,叠加上材料复杂,成本高居不下。 三是相应负极材料的开发。硅负极在充放电过程中体积膨胀大,粉化和分层现象严重,有待解决。而在锂金属负极的开发过程中,锂枝晶生长、活性锂不断消耗,导致可逆性差;另受到工艺设备的影响,超薄锂金属负极的制备还存在困难。
第四,固态电池的制造工艺还需优化,部分生产设备需要定制。其中,正负极和电解质膜的生产设备为主要需要改造或全新研发的设备,尤其是中前段设备。叠片设备也需要做相应升级,与传统液态电池生产设备的共用率约为70%。总的来看,目前搭建一条1GWh液态电池产线的成本约为1.5亿,而固态电池产线搭建成本是其2倍。
具体到硫化物电解质全固态锂电池上,许晓雄指出,该类电池的优势是能量密度有望超过350Wh/kg、快充性能优、循环寿命长、工作温区宽等,但同时也面临着稳定性低、成本高、制造技术三大方面的挑战。
其中,当硫化锂价格低至50万元/吨时,该类电池成本才有可能与液态相当。制造环节的挑战则集中在干法制备工艺和装备的突破上。
审核编辑:刘清
-
电解质
+关注
关注
6文章
821浏览量
20208 -
全固态电池
+关注
关注
0文章
59浏览量
4883
原文标题:全固态与量产的距离:市占率破1%
文章出处:【微信号:weixin-gg-lb,微信公众号:高工锂电】欢迎添加关注!文章转载请注明出处。
发布评论请先 登录
相关推荐
固态电池时间表已定!比亚迪、丰田计划2027年全固态电池上车
王东海最新Nature Materials:全固态锂硫电池新突破
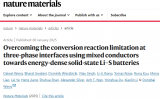
评论