共读好书
周岩 刘劲松 王松伟 彭庶瑶 彭晓飞
(沈阳理工大学 中国科学院金属研究所师昌绪先进材料创新中心江西蓝微电子科技有限公司)
摘要:
目前,键合铜丝因其价格低廉、具有优良的材料性能等特点正逐渐替代键合金丝广泛应用于电子封装领域。本文对当前市场上应用的金丝、铜丝、银丝及铝丝性能特点进行了分析对比,探讨了以键合铜丝替代传统键合丝材料的优势;简要介绍了铜丝材制备和键合过程的研究进展,并对键合铜丝的封装失效形式进行了简要分析;综述了微合金化对键合铜丝服役性能的影响规律及机理;最后从市场需求及理论研究方面分析了键合铜丝市场的发展趋势。
键合丝是集成电路封装的基本材料之一。常用的键合丝材料包括金丝、银丝、铜丝及铝丝。 一直以来,键合金丝因其出色的力学性能和加工性能占据着电子封装市场。 然而,随着电子产品向高密度化、高速度化和小型化发展,芯片引脚数越来越多,布线间距越来越小,封装厚度越来越薄,封装体在基板上所占的面积越来越小,这就要求键合丝材料朝着低介电常数、高导热、低成本的方向发展 [1] 。 近几年,键合铜丝以其低廉的成本及较好的综合性能已经开始占领电子封装行业的中低端市场,主要用于二极管、三极管、集成电路、大规模集成电路等各种半导体器件中作为内引线 [2] 。 在无引脚封装、小间距焊盘等高端产品领域, 键合铜丝也表现出良好的使用潜力。因此,国内外越来越多的科研人员投入到键合铜丝的研究中。本文根据相关专利及文献,对键合铜丝的性能特点、服役情况及其微合金化改性研究进展等方面进行了综述。
1 键合铜丝的性能特点
键合丝作为芯片与框架之间的引线,是半导体封装的核心材料,起着实现芯片与外界电流、信号交互的重要作用。键合丝具有繁多的产品门类、复杂多变的应用场景以及较高的质量要求,使得其生产制造有一定的技术壁垒和工艺难度。
1.1 键合丝性能要求
键合丝的材质和线径不仅决定着键合过程的形弧情况,而且对后续封装厚度及器件的服役时间都有着十分重要的影响。因此,对于丝材的抗氧化性、导电、导热性、可焊接性、可靠性都有着十分严格的要求。此外,还需考虑键合丝线径的一致性及其放线性能是否顺畅、丝材表面的光洁度以及丝线在温度变化时的稳定性等。理想的键合丝材料应具备以下特点:能够保证芯片与引线框架之间形成良好的键合;键合过程所需较小的键合温度、键合力;化学性质相对稳定,尽量减少金属间化合物的生成;可塑性好等。
传统的键合丝材料有 Au 、 Ag 、 Al 、 Cu 。 4 种常见键合丝材的物理性质如表 1 所示。 Al 丝在键合过程中,可与芯片铝膜电极形成 Al-Al 系统,因此不存在金属间化合物对焊接性能造成影响,但其拉伸强度及耐热性差,易导致塌丝问题且在键合过程中成球性差,不易焊接等缺点使其应用空间大大受限。 Ag丝有着优异的导电导热性能,并且在键合过程中不需要保护气体,可 Ag 具有极高的电敏感性,在高密度键合的过程中易出现塌丝以及 Ag + 迁移现象,此外 Ag 的延展性差,高温下易氧化,不易加工成符合规格的键合丝。 Au 丝具有极佳的机械性能、良好的焊接接合性能、稳定的化学性能以及耐腐蚀性,但 Au丝在键合过程中易形成紫斑 (AuAl 2 ) 和白斑 (Au 2 Al),导致界面处形成柯肯德尔空洞以及裂纹,从而影响焊接强度。值得注意的是, Au 丝的价格成本大约是Cu 丝的 70 倍左右,而 Cu 丝具有比 Au 丝更优异的导电和导热性能,抗拉强度也更优于 Au 丝和 Al丝, Cu 丝也具有相当好的焊接性能。采用 Cu 作为引线框架材料时,也不会形成金属间化合物,因而Cu 丝也是目前替代传统键合丝材料的最佳选择 [3-5] 。
1.2 键合铜丝性能优势
除了以更加低廉的价格优势大幅降低了器件的制造成本,吸引更多厂商及研究人员的关注外,键合铜丝本身也具有非常优良的材料性能,使其近年来能够在电子封装等领域具有非常高的市场占有率。键合铜丝的性能优势主要表现在以下几个方面:
(1) 较高的伸长率和破断力键合铜丝优良的力学性能, 主要体现在其具有较高的伸长率和破断力,二者对引线键合的质量起着十分重要的作用。高破断力代表铜丝能够抵抗更高的应力,而较高的延伸率能使铜丝在键合过程中具有更好的成弧形,避免塌丝现象,进而提高器件的可靠性 [6] 。 此外,在满足相同焊接强度的情况下, 可采用直径更细的铜丝代替金丝,使引线键合的间距更小,进而满足对集成度要求更高的器件的生产。
(2) 较高的导电导热率曹军 [7] 研究表明,铜键合丝具有良好的导电、导热性能,用铜线替代金线和铝线可缩小焊接间距,提高芯片频率和可靠性。铜的电导率大约是金的 1.33 倍, 在承受相同的电流时,铜丝采用更细的丝线便可达到要求。对于芯片来说,散热能力是非常重要的指标。 铜的导热率也比金高出 20% 左右,减小焊丝直径更有利于铜丝散热。 而且铜丝具有比金丝更高的热膨胀系数,其焊点应力自然也较低,降低了后期焊点颈部断裂的可能性,提高了器件的可靠性。此外,直径更加细小的丝线可以在微间距封装中提高功率调节器件的电流容量和性能,还能降低由于寄生电容引起的信号串扰,提高传输速度。因此,铜键合丝更适合用于高端、引线数量更大、焊接尺寸更小的元器件封装 [8] 。
(3) 较慢的金属间化合物生长速度在键合过程中, 影响焊接成型以及焊接可靠性的一个关键因素是焊丝与金属化层之间的金属间化合物 (inter-metallic compound, IMC) 的增长速率,一定含量的金属间化合物可以增加键合时的结合强度,但 IMC 生长速度较快时,易形成肯德尔空洞以及裂纹,严重影响器件的可靠性。键合时,焊丝与金属化层的扩散速率越低,使得接触电阻越低,金属间化合物的增长速度就越低,产生的热量就少,从而提升键合强度,并最终提高焊接可靠性 [9] 。
铜丝与金丝焊点相比,铜丝焊点中的金属间化合物生长速度显著减小。使得产热减少,更进一步提高了器件的可靠性。瑞典 Ainouz 等 [10] 研究了铜线作为互连材料在半导体封装中的性能。研究表明,铜在键合过程的匹配性及可靠性要更优于金丝和铝丝。
2 键合铜丝的研究现状
2.1 铜丝制备过程的研究进展
传统键合丝在生产过程中需要经过拉铸、拉拔以及退火等工艺,通过拉铸将金属熔成棒材,再经过多道次的拉拔将其拉成丝状,拉拔后进行退火,以消除键合丝的内应力,避免丝材发生扭转、弯曲等情况, 也可进一步对丝材的机械性能进行调整,最后根据产品要求,进行绕线以及产品检验。 目前,在拉制键合铜丝时,对铜丝的断线率、表面质量都有着十分严格的要求。 在键合铜丝的制备过程中经多道次的拉拔易发生断线情况,致使单盘产品无法满足要求,造成浪费。拉拔后铜丝的表面质量若不达标, 会使铜丝在后续的键合过程中成球性差,导致焊接强度严重降低。
由于铜键合丝的线径较细,在拉拔过程中对坯料中的杂质含量比较敏感,坯料内部的杂质微粒及缺陷会造成丝线组织性能的不均匀,严重时便发生断裂。胡立杰 [11] 提出,为防止在拉拔细丝过程中晶界出现断裂从而影响铜材的传导性能,可采用真空熔炼氩气保护热型连铸设备制备的单晶杆铜,因其具有致密的定向凝固组织,解决了气孔、横向晶界等缺陷,此外其结晶方向和拉拔方向相同,可以承受更大的塑性变形。曹军等 [12] 针对单晶杆铜拉制键合铜丝的成分及断口形貌进行了分析, 发现拉拔时,控制力不均会引起线材的局部应力变化,从而造成断线。在拉制过程中保持控制力稳定、避免对丝材表面造成损伤,并在成品拉丝前进行去应力退火能够大大降低断线率。
2.2 铜丝键合过程的研究进展
目前,绝大多数铜丝的键合方式均采用引线键合。引线键合技术的关键就是通过金属丝借助热、压力、超声波使芯片上的引线与底座外引线连接起来,进而实现芯片与基板间信息交互,键合后效果图如图 1 所示。 由于引线键合具有低成本、可靠性高、产量高、适用多种封装形式等优点而占据了目前封装管脚行业约 90% 的市场份额 [13] 。
按照键合条件及工艺的不同,引线键合技术又可分为热压键合、超声键合和热超声键合 [14] , 3 种键合方式性能对比如表 2 所示。 热压键合是利用微电弧使引线端头在高温下发生形变, 一般使其熔成球状,再通过调控时间及压力来完成键合过程 [15] 。 其键合强度较高且工艺简单, 即便键合失败也能在同一位置再次键合。超声键合利用超声能量在常温下使键合丝发生塑性变形, 并破坏引线与焊件之间的氧化薄膜,进而完成键合,使用时的超声频率通常不超过 60kHz 。 超声键合技术主要适用于铝丝的键合,因键合过程不会形成化合物影响焊接强度且对被焊件表面洁净度要求不高而被推崇。 热压超声键合即将热压键合与超声键合两种技术结合起来, 在超声键合机中通过加热器辅助加热,进而实现引线的高质量焊接 [16] 。 其键合温度及压力均不高,利于提高器件的可靠性,是目前较为理想也是应用最为广泛的键合技术。
引线键合按键合工具种类不同,分为球键合及楔键合两种基本形式 [17] 。 两种键合方式都需先在芯片表面形成第一焊点,然后形弧,最后在基板上形成第二焊点 [18] 。 不同的是球键合是指将引线一端熔成球状然后使其焊接在芯片电极上的一种焊接方式,键合点无方向性。而楔键合则是借助热、压和超声能量直接将引线焊在基板上,并且楔键合的两个键合点具有严格的方向性, 球键合与楔键合的键合点如图 2 所示。 与楔键合相比,球键合具有操作便捷、焊接速度快、焊点牢固且无方向性等特点,也因此被用来实现高速自动化焊接。
针对铜丝通常采用热压超声工艺进行球键合。但在烧球过程中,常发现球表面不够光滑, 成球性差。这是由于铜线在高温下熔成球状时, 发生了氧化,进而影响铜球质量。 赵健经研究发现,在键合过程中通入用 95%( 体积分数 ) 的氮气和 5%( 体积分数 )的氢气混合气体可有效解决此类问题 [20] 。 少量氢气的加入还能将纯铜线在储存过程中表面生成的氧化薄膜也还原成铜。 余斋等 [21] 将前沿的微动学理论加以改进,并融入到探索热压超声球引线键合的机理中,提出了二类键合图,键合时通过反馈系统实时监控各项参数的变化情况,并加以调整和改进,从而保证实现更高效、可靠的键合。
3 键合铜丝的失效形式及原因
尽管键合铜丝凭借着良好的综合性能,市场占有率逐年提升,但因其硬度较大、易氧化等特性造成的封装失效仍是当前阶段急需解决的问题。在实际电子封装过程中,铜丝球键合点的失效模式大致分为粘接失效、界面失效及球内断裂三种 [22] 。在不同的温度条件下,随着保温时间的延长,由于焊盘上铝和铜残余量的不同,使铜球内部结构以及 IMC 的成分含量发生变化,进而导致键合丝失效。而在实际生产和使用过程中, 键合丝的失效形式更为复杂,在众多不确定的环境因素下,键合铜丝的失效原因更应引起研究人员的注意,以便早日制定出更加科学合理的防护措施。
3.1 封装缺陷
封装缺陷是指在后续封装的过程中可能会出现的缺陷,包括外键合点颈部裂纹、键合丝短路等。 ATi公司采用芯片阵列球栅阵列 (chip array ball grid ar-ray, CABGA) 封装形式生产的处理器,在使用一段时间后发生失效,机械开封后发现塑封与引线框架之间并没有产生明显的分层,但其键合点颈部产生了局部裂纹甚至贯穿性裂纹,如图 3 所示。 裂纹的产生可能与键合工艺有关,此类失效有可能在测试阶段就排查到, 之后需对同批次产品依次进行测试,避免在后续应用过程中发生大规模失效。
键合丝短路可能是键合丝与接地引脚之间发生短路,或者相邻键合丝由于间距过小、走向安排不合理、线弧高度设置错误等问题造成的短路。Atheros公司采用 CABGA 进行封装的手机处理器,由于线弧高度设置错误, 造成封装引脚之间短路,如图 4 所示。 此外,由于键合丝强度过低,封装后形成塌丝并与其他导体相互接触也易造成短路现象。键合丝塌丝可能触及电容端头, 也可能触及芯片边缘造成失效 [23] 。 但无论何种原因造成的短路现象,都需及时优化键合参数,防止器件长期应用时,产生漏电、退化并突发失效。
3.2 键合点出现键合弹坑
弹坑是由于焊球在压到芯片焊区表面时,接触力、 键合力和键合功率设置匹配不当导致焊区的硅层受到损伤。键合铜丝硬度越大,越容易导致弹坑的出现。国产 SOT23-6 封装的脉冲宽度调制控制芯片在焊接完成后发现功能失效,通过化学开封,发现弹坑呈现环状,说明损伤较为严重,如图 5 所示,通过扫描电镜会非常清晰地观察到硅缺失的痕迹,也说明键合过程中的键合力较大 [24] 。 通常情况下,弹坑损伤较小,呈月牙形。在键合过程中,对于不同类型的芯片需进行适当的工艺调整,若调整不当,则会导致键合过程中焊盘局部界面挤压现象严重,发生批次性的键合弹坑现象。 这会大大降低键合强度及介质绝缘性,表现为漏电异常,漏电会随着后续通电使用时间的增长不断加大,进而导致反向击穿电压过低,甚至击穿短路,对器件使用性能造成严重影响 [25] 。键合点的弹坑损伤失效也具有潜伏性,在应用时遇到外加电应力或者温度应力会加速失效。
3.3 键合点发生化学腐蚀
TI 公司生产的超薄缩小型封装微处理器在使用几个月后失效,激光开封后可见氯腐蚀铜丝,键合点化学腐蚀 SEM 图像及腐蚀形貌图如图 6 所示 [24] 。由于封装过程中,塑封材料中可能会检测到少量的氯元素,尽管氯离子不能直接与铜离子发生化学反应,但铜的表面可以形成 Cu 2 O ,发生电化学的腐蚀作用,并且能够和氯离子形成络合离子产生进一步反应 [26-27] ,从而降低器件的可靠性。
在铜铝键合的过程中,铜铝键合的 IMC 主要成分为 CuAl 2 、 CuAl 和 Cu 9 Al 4 [28] 。 铜丝键合点腐蚀主要是由于 Cu 9 Al 4 和 CuAl 2 受到 Cl - 侵蚀导致 [29] ,最终导致键合强度下降,可能的一系列反应为:
为了能够预防此类失效形式的发生,应加强对于塑封材料中卤素含量的控制并提升塑封材料的抗湿性能。也可通过在其表面涂覆三防漆进行防护,除此之外,提升键合铜丝的抗氧化性也可进一步避免氧化物与卤素离子之间发生化学反应,进而产生腐蚀。
3.4 键合点发生电偶腐蚀
电偶腐蚀也被称为原电池腐蚀,是一个十分漫长的过程,需要一定的时间积累,具有潜伏性,会导致键合强度降低最终出现断裂,键合点位置过热会形成塑封料的炭化现象。 铜铝键合界面失效表现为键合点没有形成弹坑, 没有明显的过电应力和化学污染,键合点呈现过热失效。最终引起铝层氧化,键合强度降低。
4 键合铜丝微合金化改性研究进展
尽管铜丝键合时具有优良的力、热、电学性能,但键合铜丝的发展也有着巨大的挑战。由于铜丝键合过程中面临易氧化等问题, 可以向铜丝中添加一些微量元素,延长其保存时间的同时,对于键合丝的其他性能也能得到一定程度的提高。 若要得到性能更加优良的键合铜丝,便要控制铜丝的硬度,铜丝硬度过高,容易造成基板断裂、虚焊等问题 [30] 。 可通过提高铜丝纯度使其自身硬度降低, 从而减少键合过程铜对芯片的损害,但铜丝纯度过高,又会使得自身强度下降,成型难以控制,形弧高度也不均匀;此外也会使铜丝再结晶温度降低,破断力、伸长率也会随着使用时间的延长而下降 [31] 。 因而合理控制铜丝中添加的微量元素种类及其含量对键合过程有着至关重要的影响。本文通过整理现有研究结果,得到各微量元素的分类及其作用机制如下:
碱金属元素:碱金属元素可作为除杂元素加入铜丝中,有利于杂质元素形成氧化物、硫化物、硒化物进而去除 O 、 S 、 Se 等元素 [32] ;也可作为合金元素,利于提高焊球颈部的断裂强度,降低细丝的断裂几率。专利文献 CN104278169A 中, 向纯铜中加入了 0.008%~1.000%( 质量分数 ) 的 Li , 0.3%~0.5%( 质量分数 ) 的Ce ,使得铜丝的耐腐蚀性得到显著增强,同时使得焊接热影响区长度较一般键合铜丝降低了 22% [33] , Li的加入也使得焊球颈部的强度得到提升,使得断裂几率大大降低。
碱土金属元素:碱土金属元素为元素周期表第二主族元素。其中 Be 、 Mg 均可作为脱氧剂,但由于 Be的价格昂贵,因而并不常使用。 Ca 几乎不固溶于铜,可与杂质形成高熔点化合物,能调节键合丝力学性能和高温塑性。专利文献 CN104593635A 中,通过向铜丝中加入 0.000 5%~0.020 0%( 质量分数 ) 的 Mg 、0.0005%~0.0100%( 质量分数 ) 的 Sr ,提高球焊过程的稳定性以及铜丝的抗高温氧化性 [34] 。 专利 CN109390309A 中,向纯铜中加入 0.1%~3.0%( 质量分数 ) 的Ag 以及 0.02%~0.05%( 质量分数 ) 的 Ca 和 0.026%~0.050%( 质量分数 ) 的 Be ,发现 Ca 能有效提升铜合金的焊线作业性,增强线材与芯片及基板的粘附性能,有助于提升线材的抗硫化能力和抗老化能力,而Be 能提高铜合金线材的再结晶温度,提升线材在高温环境下的耐疲劳性,有效降低颈部断裂的几率。使得生产出的铜合金线具有优异的作业性和可靠性,且成本较低 [35] 。
过渡元素:微量的 Fe 可以细化晶粒,提高铜丝的塑性加工性能;微量的 Zn 可以抑制铜的氧化; Zr 可以提高铜丝的再结晶温度,经常和其他元素混合添加;而 Ti 可以增强铜线的键合稳定性。专利 62-130249中在 4 N 纯铜中加入 5~200 μg/g 的 Ti , 大大提高了铜线的键合效率 [36] 。 专利 CN106992164A 中发表了一种微电子封装用铜合金单晶键合丝,该 Cu 丝中各成分的重量百分比如下, Ag 为 0.01%~0.02%( 质量分数 ) 、 Sc 为 0.01%~0.02%( 质量分数 ) 、 Fe 为0.001%~0.015%( 质量分数 ) 、 Ti 为 0.001%~0.02%( 质量分数 ) ,余量为 Cu [37] 。 研究发现, Sc 能影响铜合金的组织和性能,在保持合金塑性的同时,能够大幅提高合金强度,具有净化和改善组织的作用,而 Ti的加入会产生很强的变质作用和抑制再结晶能力,也可与 Cu 形成固溶体,不会生成 IMC 相,提高器件的可靠性。专利 CN111004982A 中向铜钯合金中加入了一定质量分数的 Ti 、 Co 元素,通过研磨、压制形成中间体后,进行淬火,反复捶打后得到铜钯合金复合材料,解决了其在使用过程中易发生断裂的问题,提高了用户对产品的使用体验 [38] 。
稀土元素:稀土元素具有很高的电负性以及较大的原子半径,微量的稀土元素能够细化晶粒 [39] ,提高铜丝抗氧化性和可焊性。添加适量稀土元素也有利于降低铜丝硬度, 在添加量为 0.000 2%~0.002 0%( 质量分数 ) 时,更有利于提高铜丝的可焊性,使器件更可靠。专利 CN105463237A 中以铜为基底材料,将0.1%~5%( 质量分数 ) 的 Ag 作为主合金,合金中加入含量≤0.001 5%( 质量分数 ) 的稀土元素,使得丝材在具有高强度、良好导电、导热性能的同时,降低了自身硬度,并提高了抗氧化性 [40] 。专利 CN1100718526A 中以铜为基底材料,加入 0.005 1%~0.100 0%( 质量分数 ) 的稀土元素及 0.000 1%~0.080 0%( 质量分数 ) 的 Pd ,所述 稀 土 元 素 为 La 、 Ce 、 Pr 、 Nd 、 Pm 、 Sm 、 Eu 、 Gd 、 Td 、Dy 、 Ho 、 Y 中的一种或多种的组合 [41] 。 由于钯元素的添加,使得铜丝的抗氧化性得到增强,硬度降低。 适量的稀土元素与铜中的微量杂质铅等形成高熔点化合物,呈细小弥散的质点在晶粒内部均匀分布,细化晶粒的同时,进一步改善了铜的力学加工性能,从而满足窄间距、低长弧、高强度的键合要求。综上,对添加微量元素种类及其作用进行整理,如表 3 所示。
通过采用微合金化改性的手段,键合铜丝的硬度及抗氧化性也得到了改善,具体案例如下:为了降低铜丝的硬度,专利 CN104752385B 公开了一种 IC 封装用超软键合铜合金丝的制备方法,在纯度为 4N以上的铜丝中加入 0.000 01%~0.000 2%( 质量分数 )的 W , 0.000 1%~0.001 0%( 质量分数 ) 的 S , 0.000 4%~0.020 0%( 质量分数 ) 的 P 以及 0.000 8%~0.020 0%( 质量分数 ) 的 Ag ,多次拉丝后再退火处理,最终得到的键合铜丝硬度低至 67 HV ,使得铜丝硬度大幅降低,解决了由于铜丝硬度过大易对芯片及基板造成损坏的问题,大大提高了器件的可靠性 [42] 。 专利CN105161476B 中采用纯度为 4 N 以上且主体氧含量≤0.000 5%( 质量分数 ) 的 Cu , 晶粒平均直径为1.6~1.8 μm ,通过真空熔炼和定向连续拉拔工艺获得线材后再拉成丝状,其间进行两次退火处理,最终得到硬度极低、球焊时变形球圆度高的适用于细间距封装的键合铜丝 [43] 。
为解决铜丝易氧化的问题,除了在铜丝表层镀覆金属,向铜中添加微量元素同样可以提高丝材抗氧化性。专利 CN109402445B 中向纯铜中加入 0.000 6%~0.0015%( 质量分数 ) 的 Al , 0.000 9%~0.001 5%( 质量分数 ) 的 Si, 0.000 3%~0.000 8%( 质量分数 ) 的 P ,预制合金后,拉铸,在氮气保护下连续退火,使得铜的再结晶温度、力学性能得到增强的同时,其抗氧化能力也大幅提升 [44] 。
在微电子封装领域,由于现代封装对于长距离、窄间距的键合要求,专利 CN107904434B 以高纯铜、锡及微量金属元素为原材料,采用定向凝固连铸技术制成棒材后,在氢气气氛下退火处理,通过多道次的拉拔最终得到直径为 0.010~0.018 mm 的超细丝 [45] 。 制备出的铜丝不仅有良好的导电、导热性,强度也大大提高,加工态伸长率 ≥2.0% ,且在拉拔过程中不易断线,单根细丝最大长度超三万米,解决了超细超长铜丝的技术生产难题,有利于产业化的实施和应用。
近年来,国内涌现出了多家键合丝生产厂商,并通过多年的投入及研发,打破了国外企业在中国市场的垄断地位, 未来国内的键合铜丝市场也将呈现更加多样化的产品,竞争也会愈发激烈。
5 展望与总结
统计数据表明, 2021 年我国键合丝需求量已经达到 238.9 亿米, 而其中键合铜丝的市场占有量已远超过键合金丝。随着近年来金价的持续上涨,铜丝也一定会成为键合丝市场的主流引线键合材料,铜丝键合工艺技术也将成为重点研究方向 [46] 。 为有效克服当前键合铜丝存在的易氧化、热稳定性差、力学匹配性差等问题, 通过向铜丝中添加多种微量元素来改善键合铜丝的性能已经成为主要趋势,由于可添加元素种类繁多,各元素的作用较为复杂,按照传统方法通过大量实验找出较优的方案无疑需要花费大量的时间和资源。未来可利用机器学习模型对合金成分进行优化设计, 以更低的资源消耗寻求更加合适的元素成分及含量,得到性能更加优良的铜丝,提高器件使用的可靠性,满足高端领域的材料需求 [47] 。
审核编辑 黄宇
-
芯片
+关注
关注
459文章
51715浏览量
430885 -
键合
+关注
关注
0文章
72浏览量
7994
发布评论请先 登录
相关推荐
芯片封装中铜丝键合技术
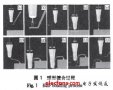
键合线等效电阻的IGBT模块老化失效研究
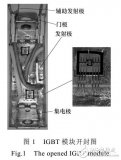
键合铜丝有什么特点!
铜丝键合塑封器件的几种不同失效模式和失效机理分析
陶瓷基板上自动键合各参数对键合形貌的影响研究
引线键合在温度循环下的键合强度衰减研究
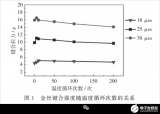
评论