共读好书
姚秀华 刘笛
摘要:
伴随着现代微电子技术的高速发展,对温度较敏感的电子元器件在设计中被普遍采用,为了满足这种电子元器件的封装要求,平行缝焊技术应运而生。平行缝焊是一种温升小、气密性高的高可靠性封装方式,普遍用于对水汽含量和气密性要求较高的集成电路封装中。影响平行缝焊质量的有诸多因素,如盖板和管壳之间的匹配、工艺参数的设置、电极表面的状态等。我们通过在SSEC(Solid State Equipment Company)M-2300型平行缝焊机上进行实验,总结出电极的状态对于平行缝焊的成品率有着直接的影响。
1 引言
平行缝焊是一种温升小、气密性高的高可靠性封盖方式,普遍用于对水汽含量和气密性要求标准较高的陶瓷封装和金属管壳封装中。影响平行缝焊质量的因素有很多,如夹具的设计、盖板质量、盖板与基座的匹配、电极状况以及平行封焊各工艺参数的匹配等。本文主要分析电极状况对器件封装可靠性的影响。
2 平行缝焊工作原理
平行缝焊的基本原理如图 1 所示。它是一种电阻焊,用两个圆柱形的滚轮电极与金属盖板接触形成闭合回路,焊接的功率以电流的形式从其中一个电极分为两股电流,一股流过盖板,另一股流过管壳,回到另一电极。整个回路的高阻点在电极与盖板接触处,电流在接触处产生大量热量,使其呈熔融状态,凝固后即成一连串焊点。因焊接采用脉冲电流,故焊点能相互交叠,就形成了气密填充焊缝 [1] 。
平行缝焊的能量主要由以下几个工艺参数决定:功率P、脉冲PW、周期PRT、速度S 以及缝焊长度 L。各参数间的关系如公式(1)所示:
平行缝焊的总能量
E=(P ×PW × L) / (PRT × S ) (1)
在实际工作中PW、L 、PRT、S为预先设置,在缝焊过程中不改变,所以可将(PW ×L)/(PRT × S)用系数A 代替,因此公式(1)可写为E = A × P。
在缝焊过程中,电极与盖板边缘接触,在电极与盖板接触处产生接触电阻R,根据P=I 2 R 和E = A× P,联立可得E=I 2 RA。由此可见缝焊的总能量与缝焊过程中的接触电阻值成正比,而在实际缝焊过程中电极表面的平整程度、洁净程度和电极位置的变化都会对接触电阻产生影响,进而改变平行缝焊过程的总能量,对平行缝焊的可靠性产生影响。
3 电极对平行缝焊可靠性的影响
3.1 电极的角度
在实际缝焊过程中,主要使用两种角度的电极,分别是 4°电极和 10°电极。电极的角度主要是指电极的斜切面与水平面之间的夹角θ,如图 2所示。
分别用4°电极和10°电极对DIP-8陶瓷管壳进行封盖试验,为了观察电极度数对封盖可靠性的影响,将封盖参数调整到使之接近DIP-8陶瓷管壳封盖总能量的极限值,以方便观察和分析,封盖参数设置如表 1 所示。
在进行缝焊的过程中,平行缝焊机通过电极以脉冲放电的方式进行缝焊,电极与盖板接触,在盖板边缘处产生连续的焊点,焊点间相互叠压,形成一个闭合的焊接链,用4°电极与10°电极以表1中的缝焊程序分别对10 只样品进行封盖,对封盖后的样品外观进行观察,发现 4°电极缝焊的焊缝明显宽于10°电极焊缝,因此可知电极的度数决定了在缝焊过程中电极与盖板之间接触面的大小。
观察样品管壳的侧壁,发现用10°电极进行封盖的产品中有6 只在缝焊环与陶瓷接口处出现裂缝,而用 4°电极缝焊的 10 只管壳无该现象出现。样品侧壁出现裂纹是由于缝焊环和陶瓷管座热膨胀系数不同造成的。在4°电极与10°电极缝焊的过程中,根据公式(1)可知两种电极所释放的总能量一致,但只有10°电极封盖时出现开裂现象是因为 10°电极与盖板的接触面偏小造成了热量局部加载到缝焊环处,而用 4°电极缝焊时电极与盖板的接触面积相对更大,使缝焊过程中产生的热量更加均匀地加载在缝焊环处,所以使用 10°电极比使用 4°电极封盖更容易出现样品侧壁开裂的现象。
因此在进行陶瓷管壳封盖时,应尽量选取 4°电极,这样更容易释放缝焊过程中加载在壳体上的热应力,有助于提高封装的可靠性。
3.2 电极表面平整程度
对大批量的产品进行连续封盖和在封盖过程中出现的打火现象都会造成电极表面的不平整,不平整的电极表面对封盖的成品率有着直接的影响,这是因为在缝焊过程中,电极表面的坑洼处与盖板接触的瞬间,接触电阻 R 发生了改变,根据缝焊总能量E=I 2 RA 可知,接触电阻R 的改变影响了缝焊的总能量值,而能量的变化不仅会影响良好焊点的形成,而且还会造成打火现象,使产品的漏气率大大增加。
3.3 电极表面洁净程度
在缝焊的过程中电极表面的洁净程度也是影响封装成品率的主要因素,封盖过程本身的瞬间高温和封装环境的不洁净都会造成电极表面的不洁净。在缝焊过程中,电流在电极与盖板接触处产生高温,瞬间的高温使盖板镀层部分熔化粘附到电极表面,形成粘附层,如果不及时处理,会对漏气率产生影响,下面我们用一组数据来说明该问题,见表 2。
电极表面的粘附层伴随着连续封盖次数的增多,其厚度变大,造成了电极与盖板之间接触电阻的改变,盖板表面的焊缝变得越来越粗糙,形成了不良焊点,不仅在缝焊过程中容易发生打火现象,而且封盖漏气率也随着连续缝焊数的增多急剧增多,容易形成可靠性隐患。
另外,如果封盖环境不洁净,那么在封盖过程中,封盖环境内的微小颗粒可能会落到盖板和电极接触处,使接触电阻发生改变,导致打火现象的发生,致使样品漏气。
因此在缝焊过程中要时刻注意电极表面的洁净程度,在连续缝焊时,要定期对电极表面进行检查,发现表面玷污要及时进行打磨处理。
3.4 电极的位置
在平行缝焊过程中左、右电极的位置应尽量对称,这样既可以保证接触电阻的一致性,又可保证焊缝宽度的一致性。平行缝焊过程中还要注意延迟距离的大小。如果打火现象发生在电极与盖板开始接触的瞬间,则是由于延迟距离设置太短。延迟距离一般可设为1.04mm左右。如果打火现象发生在电极与盖板分离的瞬间,则是由于封焊的距离设置太长。封焊的距离应为所封器件的封装长度与 2 倍延迟距离的和。如果打火现象发生在封焊过程中,则应调节电极高度的大小。
4 总结
通过一系列的试验,我们可以得出电极度数的改变,电极表面的平整程度、洁净程度以及电极的位置变化对于缝焊最终的可靠性都有着直接的影响。因此在缝焊过程中,定期对电极状态进行检查对于提高样品成品率是十分必要的。
审核编辑 黄宇
-
电极
+关注
关注
5文章
813浏览量
27210 -
焊接
+关注
关注
38文章
3114浏览量
59701
发布评论请先 登录
相关推荐
焊接方法对焊接质量的影响
VWD-J型振弦式表面测缝计计算公式
焊盘与焊盘的距离规则怎么设置
pcb焊盘区域凸起可以焊吗
PCBA锡膏加工虚焊和假焊的危害有哪些?
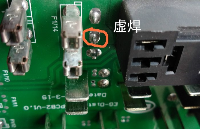
影响平行板电容器电容的因素
手焊、回流焊和波峰焊三种焊接方法,怎样操作才能保证SIM卡座的质量
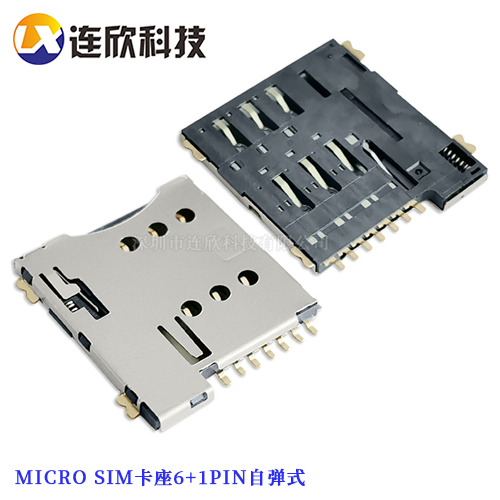
浅谈医院能源管理电能质量在线监测系统的应用
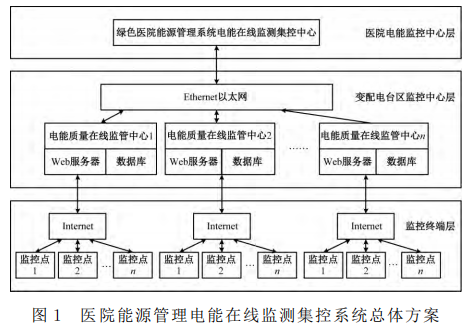
浅谈二极管的电极与符号
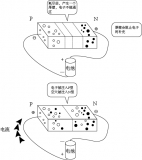
PLC编织袋切缝机如何实现数据采集和远程监控
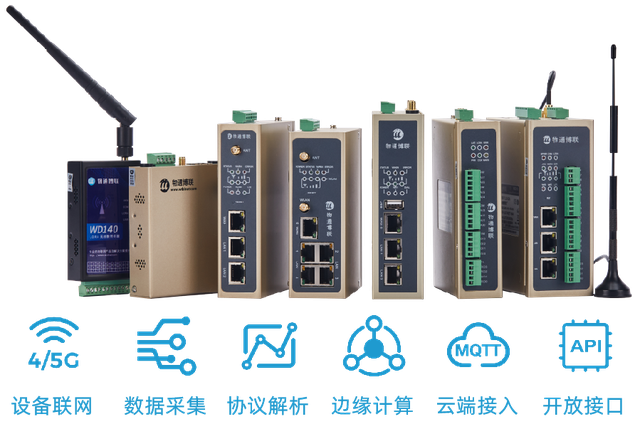
PCB焊盘脱落的原因及解决方法?
管壳类产品缝焊过程质量问题分析及解决方法
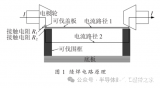
评论