摘 要:为改善低温环境下锂离子动力电池性能,本文提出一种基于单束热管的动力电池热管理低温预热模组结构。在对单体电池进行产热模型试验验证的基础上,采用数值计算的方法,研究热管蒸发段预热方式、加热液体的入口温度和环境温度对模组内电池的升温特性影响。
关键词:动力电池; 热管理; 低温预热
随着电动汽车技术的不断发展,电动汽车正在不断实现行驶距离更长、充电时间更短和安全性更高等要求。其中,锂离子电池以其能量密度高、无记忆功能、寿命长等优点被广泛用于电动汽车的动力源,但其性能表现出对温度的高敏感性。如果单体电池温度过高( 超过 40 ℃ 时) ,会引起电池组局部失效以及容量减退,导致电池组性能下降。如果电池组在低温环境下( 低于-10 ℃ 时) ,锂电池的放电性能会急剧降低。如果模组内单体电池的温差大于 5 ℃,也会导致电池放电性能的一致性变差。因此,开发一套有效的电池热管理系统( 简称 BTMS) , 实现锂离子电池在高温下的高效冷却和低温下的快速预热,并保证模组内电池温度的高度均匀性,对电动汽车的使用性能和安全性至关重要。
近年来,因热管具有很高的传热系数和温度均匀性等优点,在 BTMS 上得到了广泛应用研究,使用的热管形式包括管状热管、扁平热管、平板热管、脉冲热管等。文献提出了一种平板热管型 BTMS,最大温差相比于未采用平板热管的模组降低了 60%。上述热管式热管理结构多采用多束热管设计,这不仅增加了模组的重量,同时也提高了 BTMS 的成本。目前关于低温环境下热管式 BTMS 预热特性的研究较少。
本文针对方形锂离子动力电池,提出了一种结合单束热管与空气或液体传热相结合的轻量化复合 BTMS,建立其三维物理模型和数学模型,开展低温环境下电池模组的加热特性研究,以期为方形动力电池的轻量化 BTMS 设计提供参考。
1、BTMS 模组的物理模型
在传统的液冷BTMS 中,微通道大多布置在冷板上,导致冷板厚度为 1~ 2 mm。在本文提出的液冷结构中,冷却管放置在板的外围,使得导热板的厚度仅为 0. 2 mm,大大减轻了冷却结构的重量。并且,相比于传统的单一冷却方式,本文提出了将导热板、热管和空气或液体传热相结合的冷却方式,从而实现轻量化复合的 BTMS。
电动汽车电池组通常由多个电池模块组成,建立一个完整的电池系统和热管理系统比构建单个电池模块难度更大。为研究散热系统的散热性能,可将电池组系统替换为单个电池模块,且为便于本研究的仿真,对电池模块进行了简化 。
本文提出的具有单束热管、传热液体通道和导热薄板的电池模组结构如图 1( a) 所示,主要由 1 根束热管、6 块方形电池、1 块导热板和换热流体组成。因为研究 6 块电池既能很好地反映出单束热管与空气或液体传热相结合对 BTMS 模组产生的冷却性能,又能简化成百上千块电池给试验模拟造成的复杂情况,达到了简化数值计算的目的。其中热管的蒸发段插入到换热流体中,其他部分作为冷凝段被导热板的 3 个断面缠绕,为了能够使电池均匀散热,将 6 块电池分别布置在导热板的两侧,每侧布置 3 块方形电池 ( 如图 1( b) 所示) 。
在低温环境下,换热流体模块中通入高温流体,对热管蒸发段中液态工质加热并使其汽化,流向热管冷凝段凝结成液体并释放热量,再通过导热板传递给每一块动力电池; 凝结成液体的工质在毛细力作用下回流至热管蒸发段。重复上述过程,以此使得换热流体的热量被源源不断高效均匀地传递到每一块动力电池。
2、数值计算方法
2. 1 电池产热与传热的数学模型
1) 由于电池内部的换热较为复杂,认为为电池内部热通量是均匀产生的,因此假设内部热源产生的热量分布均匀。基于上述理论,方形电池的瞬态产热公式如下:
式中: φ 为电池发热量; I 为电池电流; E0 为电池开路 电压; E 为电池电压; T 为电池绝对温度;为温度系数。
2) 根据牛顿冷却定律,电池外表面的散热量可以用式( 2) 表示:2) 根据牛顿冷却定律,电池外表面的散热量可以用式( 2) 表示:
式中: qα 为对流散热量; hα 为对流换热系数; Ac 为换热面积;Tw 为电池外壁绝对温度; Tα 为外部环境流体绝对温度。
2. 2 计算条件
在本研究中,该 BTMS 中所用材料的热物性参数见表 1。传热流体的入口速度统一为 0. 5 m /s,流体进口温度在 15~25 ℃范围内变化。导热板材料采用铝,并在其与电池之间涂敷上一层导热系数为 2 W/( m·K) 、厚度为 2 mm 的导热硅胶,以消除导热板与电池之间由于表面粗糙度而引起的接触热阻的影响。所有仿真计算均通过瞬态计算完成,瞬态计算的时间步长为 1 s,一个时间步长内的最大迭代次数为 20 次。
2. 3 网格数目无关性研究
网格的质量直接影响着仿真计算的精度和模拟结果,因此网格的划分对后续的仿真计算至关重要。网格数目无关性就是验证计算结果对于网格密度变化的敏感程度,当网格数量增加到一定程度后,如果计算结果的变化在允许范围内,便可认为此时网格数量的变化对结果的影响可以忽略不计,即此时称为网格数目的无关性。
本文采用 Hypermesh 对 BTMS 模组的物理模型进行网格划分,主要包括电池、热管、导热板和流体域这 4 部分的网格,并且在划分这 4 部分网格时都采用了同一尺寸的网格单元。为了简化计算,通过采用不同尺寸的网格单元,生成了 6 个具有不同网格总数的模型,每一种网格数目对应着整个 BTMS 模组 4 个部 分( 电池、热管、导热板和流体域) 的网格总数。
在相同的边界条件下完成计算后,通过电池模组的最高温度( Tmax ) 来反映网格数量对计算精度的影响。从图 2 中可以看出,网格数量增长时,电池的温度逐渐升高,而当网格数大于 1. 53×106 时,最高温度几乎保持不变,且三者的最高温度值的相对误差小于 0. 2%,因此,选择网格数量不小于 1. 53×106 的网格模型进行数值计算。
2. 4 电池产热模型的试验验证
为了验证 2. 1 节中所述的简化后的电池产热模型以及数值模拟的可靠性,建立了与数值模拟条件相同的单体电池的放电试验系统。试验装置示意图如 图 3 所示。单体电池采用 20100140 型磷酸铁锂电池,使用 Neware CT-4008 T 电池测试站控制电池的 放电和充电。数值模拟设定的环境温度和试验设定的温度都为 25 ℃,电池模拟器模拟电池 2 C 放电。JK-8U 温度巡检仪用于记录温度数据。试验值为 5 个热电偶所测温度值的平均值,热电偶的位置如图 3 所示。测试结束后,试验数据与瞬态模拟数据的误差如图 4 所示。结果表明,瞬态模拟数据和试验数据基本一致,两者的误差在 2%以内,证明了电池产热模型的合理性。
3、BTMS 模组在低温环境下加热性能分析
本章节主要在前面所述的计算条件下进行仿真研究,包括电池的产热方程、冷却方式、计算的边界条件以及试验的可靠性,从而对 BTMS 模组在低温环境下的加热性能进行分析。
3. 1 热管蒸发段不同预热方式
1) 4 种热管蒸发段的预热方式。为了探索高效的热管蒸发段的预热方式,设计了 4 种换热方式,分别是空气( 简称 HPA) 、空气耦合翅片( 简称 HPAF) 、 液体( 简称 HPL) 和液体耦合翅片( 简称 HPLF) ,如图 5 所示。HPA 预热模式在热管的蒸发段使用风扇提供强制空气对流; HPAF 预热模式在热管蒸发段焊接了一些翅片,采用风扇驱动空气实现对热管蒸发段的强制对流加热,通过热管和导热板将该热量传递给电池; 对于 HPL 预热模式,热管的蒸发段采用传热液体进行加热; HPLF 预热模式则是将翅片焊接在热管蒸发段。
翅片的结构如图 6 所示。单个翅片尺寸为 24 mm×10 mm×0. 5 mm,中间开孔直径为 6 mm; 翅片间距取 4 mm。共设置 15 块翅片。
在加热流体入口速度为 0. 5 m /s、入口温度为 25 ℃、环境温度为-10 ℃ 且预热时间为 1 h 的情况下,电池模组的最低温度( Tmin ) 和最大温差( ΔTmax ) 在不同的预热方式下随时间的变化情况如图 7 所示。
2) 不同加热方式下电池最低温度变化情况。由图 7( a) 可以看出,在预热过程中,HPA 和 HPAF 两种预热方式的 Tmin呈线性增长趋势,HPL 和 HPLF 两种预热方式的 Tmin呈近似对数增长趋势,且后两种预热方式下的 Tmin显著大于前两者。这主要是因为热管蒸发段采用液体进行预热的对流传热系数远高于空气。在预热结束时,HPA 和 HPAF 的 Tmin分别为-8. 6 ℃和-4. 6 ℃,HPL 和 HPLF 的 Tmin分别为 15. 2 ℃ 和 15. 8 ℃。HPA 和 HPAF 的 Tmin差异为 4 ℃,而 HPL 和 HPLF 的差异仅为 0. 6 ℃。这些结果表明,无论有无翅片,热管蒸发段采用空气预热的电池模组最低温度值都达不到 10 ℃。因此,液体预热模式具有优异的传热性能,可以更好地满足 BTMS 的快速加热要求。
3) 不同加热方式下电池最大温差变化情况。图 7( b) 展示了 4 种预热方式下 ΔTmax的变化情况。从 图中可以看出,由于液体工质的对流换热系数要比空气的大得多,导致 HPA 和 HPAF 的 ΔTmax值在预热初期的上升速度较小,而 HPL 和 HPLF 的 ΔTmax在预热初期迅速上升,在 300 s 时到达峰值后逐渐减小。在预热结束时,4 种预热方式的电池模组最大温差值分别为 0. 5 ℃、1. 8 ℃、5. 1 ℃ 和 5. 2 ℃。结果表明,采用液体预热的 ΔTmax接近 5 ℃,且大于空气预热。
综上,与空气预热相比,热管结合液体预热的 BTMS 具有更好的预热性能,并且在提高电池最低温度上,翅片的使用对液体预热模式的电池模组温度均匀性的改善效果不明显。因此,为提升 BTMS 的预热速度,并降低其加工复杂性,后续选择 HPL 预热方式作为进一步研究的对象。
3. 2 预热流体入口温度的影响
图 8 展示了在加热流体入口速度为 0. 5 m /s、环境温度为-10 ℃且预热时间为 1 h 的情况下,预热过程中不同传热流体入口温度下电池模组的最低温度和最大温差的变化情况。
1) 电池模组最低温度变化情况。如图 8( a) 所 示,不同加热液体入口温度下的 Tmin均呈现出随着时间增长的趋势,但其增加的幅度逐渐降低。随着加热液体入口温度的增加,Tmin上升的速率呈现增加趋势,这与文献中研究的电池温度变化趋势一致。预热 1 h 后,加热液体入口温度 15 ℃、20 ℃、25 ℃ 所对应的Tmin分别可以达到 8. 0 ℃、11. 6 ℃和 15. 2 ℃,即加热液体的入口温度越高,Tmin越高。当加热液体的入口温度为 20 ℃ 和 25 ℃ 时,电池加热到 10 ℃ 的时间分别为 2640 s 和 1840 s,这个时间在减少,而加热液体的入口温度为 15 ℃时,预热 1 h 结束后 Tmin都达不到 10 ℃。
2) 电池模组最大温差变化情况。如图 8( b) 所 示,不同加热液体入口温度的 ΔTmax的变化趋势相同,呈现出先急剧上升,然后快速下降,最后平缓下降的趋势。这主要是因为加热液体的温度与电池初始温度之间的温差较大,刚开始预热时与导热板直接接触的电池部位温度急剧上升,但由于电池本身的各向异性导热性能,电池外部侧面的温度上升很慢,即电池本身内部的温差急剧增大,导致整个模组的最大温差急剧增大。随着预热过程的进行,更多的热量传递到远离导热板的电池外部侧面,导致 ΔTmax 快速降低。当加热液体的入口温度为15 ℃和 20 ℃时,电池模组最大温差降低到 5 ℃ 所需的时间分别为 2230 s 和 2890 s,当加热液体的入口温度为 25 ℃ 时,预热 1 h 结束时 ΔTmax仍大于 5 ℃,预热结束时加热液体入口温度 15 ℃、20 ℃和 25 ℃对应的 ΔTmax分别为 3. 7 ℃、 4. 2 ℃和 5. 1 ℃。结果表明,加热液体入口温度越高,ΔTmax越大,ΔTmax 降低到 5 ℃ 需要的预热时间越长。
3) 电池模组的温度云图。不同热流体入口温度下预热 3 600 s 时电池模组的温度如图 9 所示。由于电池模组加热量全部来源于热管和导热板的热量传递,靠近热流体附近区域的电池部位温度较高。同时,随着热流体入口温度的升高,电池模组的最大温差呈现上升趋势。
因此,提高加热液体的温度,可以更快地对该复合热管型电池热管理模组进行预热,但满足温度均匀性要求所需的时间也越长,且加热系统的能耗越高。所以需要综合考虑复合热管型电池热管理模组的加热速率和最大温差,不宜选择过高的热流体入口温度。
3. 3 环境温度的影响
图 10 展示了在不同的加热液体入口温度下电池模组预热 1 h 时 Tmin和 ΔTmax随环境温度( -10 ℃、-5 ℃和 0 ℃ ) 的变化情况。
1) 电池模组最低温度变化情况。从图 10( a) 中可以看出,当加热液体入口温度为 20 ℃时,环境温度 -10 ℃、-5 ℃和 0 ℃对应的Tmin分别为 11. 6 ℃、13. 1℃和 14. 4 ℃,环境温度从-10 ℃ 升高到 0 ℃ 时,Tmin 增大了 24. 1%。表 2 为各种工况下电池加热到 10 ℃ 所需的时间,从表中可以看出,当环境温度为 0 ℃、加热液体入口温度分别为 15 ℃、20 ℃ 和 25 ℃ 时,加热 1 h 的 Tmin 都超过了 10 ℃,所需要的时间分别为 2 640 s、1 470 s 和 1 092 s; 当加热液体入口温度为 20 ℃,环境温度为 0 ℃ 时 Tmin升高到 10 ℃ 所需时间比环境温度为-10 ℃时 Tmin升高到 10 ℃ 所需时间减少了 1 170 s。
2) 电池模组最大温差变化情况。从图 10( b) 中可以看出,当加热液体的入口温度为 20 ℃时,环境温度-10 ℃、-5 ℃和 0 ℃的 ΔTmax分别为 4. 4 ℃、3. 6 ℃ 和 2. 9 ℃。环境温度从-10 ℃升高到 0 ℃时,加热液体入口温度 15 ℃、20 ℃和 25 ℃ 下的 ΔTmax分别降低了 41%、34. 1%和 27. 5%。这表明环境温度的降低对控制该复合热管型电池热管理模组的最大温差带来了挑战,需要降低加热流体的入口温度以迎合热管理的温度目标,但这会延长加热时间,需要在实际操作中予以综合考虑。
4、结 论
针对方形锂离子动力电池,提出了一种结合单束热管与空气或液体传热相结合的新型轻量化复合 BTMS,对低温环境下该 BTMS 的预热性能进行数值计算与评估分析,结论如下:
1) 设计并研究了4 种不同热管蒸发段的预热方式对该 BTMS 预热性能的影响。单纯的空气强制对流并不能实现预热效果,即使在热管的冷凝段加上翅片; 液体预热比空气预热的预热能力更好,能够迅速实现电池模组升温的目的,但在加热过程中电池模组的最大温差往往会超出 BTMS 的温度控制目标,需要对其加热策略进行优化。
2) 在低温环境下,提高加热液体的入口温度可以显著提高预热速率,缩短预热时间,但加热液体入口温度的升高并不利于提升电池温度均匀性,应权衡热管理的预热速率要求和最大温差容忍度,选择合适的加热液体入口温度。
3) 低温环境温度的降低对电池热管理温度目标的实现带来了挑战,特别是模组的最大温差,需要降低加热液体的入口温度,但同时也会大幅延长整个电池系统达到预热目标温度所需的时间,需要根据环境温度的变化优化选择合适的加热液体的入口温度。
来源:安徽安凯客车股份有限公司 新能源研究所,合肥工业大学 机械工程学院
作者:焦云鹏,孙 然,帅深龙,唐志国
-
动力电池
+关注
关注
113文章
4531浏览量
77607 -
热管理
+关注
关注
11文章
441浏览量
21761 -
电池
+关注
关注
84文章
10560浏览量
129467
发布评论请先 登录
相关推荐
如何看汽车电池热管理系统
什么是电池热管理 电池预加热技术的应用
保障电池运行安全,如何进行电池热管理系统设计?
微型热管理和电源管理怎么解决散热设计的难题?
电动机热管理分析
燃料电池重卡热管理研究
电动汽车热管理系统和性能
热管空气预热器的特点及作用
TESLA电动汽车热管理系统研究
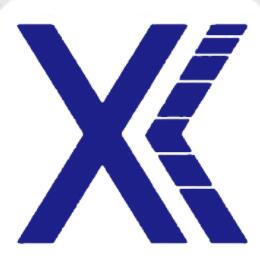
评论