QT能源科技有限公司成立于2022年11月30日,投资557718万元,购置位于台州市黄岩区澄江街道工业地块,占地面积164087.4m2,通过新建工业厂房及其他配套设施,并购置电极、装配、检测、PACK等设备,实施清陶10GWh固态锂电池项目。
项目投料方式:
本项目主材吨包装经过吊装设备将主材吊到投料口,采用负压方式吸入到计量罐内,辅材投料采用真空吸料方式加入搅拌机内,投料过程中加料首先关闭料仓出料阀门,开启真空泵使料仓和输送管道内形成真空;再接上真空吸枪,物料被吸入输送管道,并进入料仓中;真空泵与料仓之间设置有过滤器,对气体和粉料进行分离;当料仓内添加到一定量的物料后,真空泵停止。生产时主材通过重力落料方式投入搅拌机内。溶剂采用隔膜泵从NMP储罐中经过密封管道输送到计量罐内,生产时采用流量计输送到搅拌机内。本项目投料过程均先投加液状原料,再投加粉状原料,有利于减少粉尘的产生量。
材料混配方式:
本项目主材吨包装经过吊装设备将主材吊到投料口,采用负压方式吸入到计量罐内,辅材投料采用真空吸料方式加入搅拌机内,投料过程中加料首先关闭料仓出料阀门,开启真空泵使料仓和输送管道内形成真空;再接上真空吸枪,物料被吸入输送管道,并进入料仓中;真空泵与料仓之间设置有过滤器,对气体和粉料进行分离;当料仓内添加到一定量的物料后,真空泵停止。生产时主材通过重力落料方式投入搅拌机内。溶剂采用隔膜泵从NMP储罐中经过密封管道输送到计量罐内,生产时采用流量计输送到搅拌机内。本项目投料过程均先投加液状原料,再投加粉状原料,有利于减少粉尘的产生量。
项目BOM表:
核心原材料:
正极
镍钴锰酸锂:年消耗22652吨;
单壁纳米碳管:年消耗1849吨;
多壁碳纳米管(CNT):年消耗2319吨;
导电碳黑(SP):年消耗265吨;
N-甲基吡咯烷酮(NMP):年消耗7109吨;
三氧化二铝:年消耗543吨;
负极
石墨:年消耗13171吨;
羧甲基纤维素(CMC)钠、粒度50μm:年消耗207吨;
丁苯胶乳胶(SBR):年消耗689吨;
固态电解质
双三氟甲基磺酰亚胺锂(LiTFSI):年消耗106吨;
锂镧锆氧粉体(LLZTO):年消耗178吨;
二甲基乙酰胺(DMAC):年消耗4384吨;
N-甲基吡咯烷酮(NMP):年消耗130吨;
浸润电解液
电池电解液(EC、DEC、DMC、EMC、PP、PC均≤60.0%,LiPF610.0~20.0%):
年消耗545.6吨;
碳酸二甲酯(DMC):年消耗472吨;
基材
正极铝箔:年消耗2112吨;
负极铜箔:年消耗3639吨;
聚酰亚胺高温胶带:年消耗595182平方米;
PET叠片终止胶带:年消耗178555平方米;
PP隔膜:年消耗11810万平方米;
无纺布:年消耗71500万平方米;
密封
双组份(环氧/聚酯)导热结构胶:
A组份:填料40~70%、氢氧化铝10~30%、胺类物质<15%、聚硫醇<15%、有机硅聚合物<3%
B组份:填料50~90%、氢氧化铝10~30%、聚酯共聚物10~20%、环氧树脂1~10%、蓝色染料<3%、有机硅聚合物<3%
年消耗共380吨;
密封铝钉:年消耗2500万个;
密封胶钉:年消耗2500万个;
过程PP密封钉:年消耗2500万个;
隔热垫固态:年消耗1342万个;
串联汇流排:年消耗1241万个。
锂离子电池整体生产工艺示意图:
主要工艺说明
极片:
项目负极极片生产工艺与正极极片生产工艺一致,仅原料不同。正/负极主辅材采用投料系统经过密封管道自动输送搅拌机内,采用双行星制浆机在一定转速、-0.080MPa真空条件下将主辅材进行搅拌分散,再经过过滤、除铁、除泡后制成分散均匀、稳定的浆料。制浆配料过程中有粉尘产生。
自动投料:
主材吨包装经过吊装设备将主材吊到投料口,采用负压方式吸入到计量罐内,辅材投料采用真空吸料方式加入搅拌机内,投料过程中加料首先关闭料仓出料阀门,开启真空泵使料仓和输送管道内形成真空;再接上真空吸枪,物料被吸入输送管道,并进入料仓中;真空泵与料仓之间设置有过滤器,对气体和粉料进行分离;当料仓内添加到一定量的物料后,真空泵停止。
生产时主材通过重力落料方式投入搅拌机内;整个过程中粉尘经过管道负压收集经布袋除尘和高效过滤器处理净化后返回车间。溶剂采用隔膜泵从NMP存储罐中经过密封管道输送到计量罐内,生产时采用流量计输送到搅拌机内。本项目投料过程均先投加液状原料,再投加粉状原料,有利于减少粉尘的产生量。
正极粉体原料(镍钴锰酸锂、导电炭黑和PVDF)、负极粉体原料(石墨、CMC)在密闭的正极(负极)配料房内进行投料,所用设备是自动上料机系统,粉体原料均为吨袋或纸袋,因此该过程不会产生粉尘。将吨袋或纸袋装的镍钴锰酸锂(固)、导电炭黑(固)、PVDF(固)的出料口与混合器进料口通过软管相接,采用重力投料的方式。
加料投料时,首先关闭料仓出料阀门,拆去吨袋或纸袋外层包装,将内包装是铝塑膜吨袋或者纸袋直接投入设备中,再由设备内部进行开袋,依靠物料自身重力将物料投入计量罐中,由计量罐将每种物料投送至发送罐,再集中由发送罐投入搅拌机进行混料;至此,一个投料过程完成。
匀浆:
正极匀浆:将单壁纳米碳管、NMP、CNT采用隔膜泵+流量计通过密封管道输送乳化机内,搅拌0.5~1h左右,使其充分溶解,至呈糖状液体,制成NMP胶液。
主材经过自动计量精确计算重量,采用重力落料经过管道输送到搅拌机内,胶液通过隔膜泵+流量计,经过密封管道输送到搅拌机内(真空度-0.08Mpa),材料输送到搅拌机后设定公转、自转、真空度等参数经过4~8H搅拌制成正极浆料,浆料制成后,通过管道自动输送出到储存罐,经初过滤最低要求过150目)、除铁(用磁铁吸除浆料中的铁杂质)、消泡和浆料粘度检测后输送入涂布机。
正极搅拌机使用NMP溶液(浓度是99%的NMP溶液,混合1%的浆料)进行常温搅拌清洗,15天清洗一次,约20次/年,12.5T/次,产生清洗废液。滤网上的少量滤渣需定期拆下,用无尘布擦拭干净;另外,遇停产或设备维修,需要用棉布将合浆壁上挂料擦净,产生废擦拭棉布。
负极匀浆:
①纯水储存在匀浆车间的1500L储罐中。首先,按所需纯水用量通过人机对话控制系统控制,通过管道自动输送系统将储罐中的纯水加入搅拌机中。
②投加纯水、SBR后,密闭合浆罐,然后缓慢打开合浆罐上的真空阀,缓慢抽真空;到达真空度-0.080MPa以下后,关闭合浆罐上的真空阀,停止抽真空;再通过管道向搅拌机中输入CMC,每次三分之一,分三次加入,每十分钟加入一次;最后开启搅拌机在常温下开始打胶,打胶时间为5h,制成2%的胶液,静置并保持真空密闭状态。为保证浆料质量,减少搅拌过程产生气泡,搅拌机设置真空泵,待形成湿料后开始抽取真空。
③浆料制成后,通过管道自动输送出到储存罐,经初过滤最低要求过150目)、除铁(用磁铁吸除浆料中的铁杂质)、消泡和浆料粘度检测后输送入涂布机。
滤网上的少量滤渣需定期拆下,用无尘布擦拭干净;另外,遇停产或设备维修,需要用棉布将合浆壁上挂料擦净,产生废擦拭棉布、废负极浆料。负极搅拌机使用纯水进行常温搅拌清洗,15天清洗一次,约20次/年,17.6T/次;搅拌机零部件300次/年,0.1T/次。负极清洗过程会产生清洗废水。
涂布:
涂布采用双层两面高速连续挤压涂布机,涂布烘箱采用蒸汽加热,浆料经密封管道从制浆输送到涂布中转罐,经过过滤、除铁由螺杆泵输送到涂布头中,经模头挤压均匀涂覆在正/负极箔材上(正极基材为铝箔,负极基材为铜箔,放卷后直接使用,无前处理工序),涂布温度在120℃左右,涂布速度为60m/min,涂布厚度为0.2mm。
涂布后的湿极片送入涂布机自带的干燥烘箱进行干燥,去除浆料中的溶剂或水分,其中正极为NMP废气,负极为水分,干燥温度约90~140℃。本项目干燥烘箱采用蒸汽加热,NMP由热风循环系统带走进入NMP冷凝回收系统处理。干燥后的极片经张力调整、自动纠偏、面密度检测合格后收卷,供下一步工序进行加工。
涂布机为全密封设备,涂布基片进出口为微负压,同时在涂布机烘箱上安装配套的NMP回收系统,涂布及干燥过程中挥发的NMP全部进入NMP回收系统,回收后的NMP委托供货单位回收处理。
涂布机产生的NMP废气通过排风机将其从设备内抽出后,进入热回收器,通过真空泵压入冷凝器[制冷剂为R-134a(四氟乙烷),为目前国际公认的替代R12的主要制冷工质之一,是环保型制冷剂,通过一级冷却段、二级冷却段两级冷却水的热量交换后,将冷凝为液态的NMP导入至回收液体罐中,委托供货单位回收处理,剩余废气(<30mg/m2)经排气筒排入大气。主要是利用同一物质在不同温度下具有不同的饱和蒸汽分压,且温度越低,饱和蒸汽分压越低。将废气温度逐级降低后,使废气中NMP达到过饱和状态而结露析出,从而实现NMP与空气组分的分离。每天生产完后,涂布机与极片接触位置需要用棉布擦拭干净,产生废擦拭棉布。
聚偏氟乙烯(PVDF)的分解温度为>316℃,项目的烘干温度为105℃,远低于其分解温度,故PVDF不会发生分解而产生氟化氢气体。
辊压:
正极辊压采用单辊辊压机,负极采用双辊辊压机,涂布后极卷经过展平、纠偏、进入对辊装置,在0.5~0.7Mpa压力条件下将极片涂层压实,压实后极片厚度满足工艺要求,经过展平、测厚后收卷。
分切:
采用辊压分切一体机将极卷按照规定尺寸进行分切,极卷由人工采用上料小车安装在放卷轴上,极卷通过纠偏、张力控制、主牵引、进入分切刀内,极卷分切后经过除尘、除铁、纠偏收卷。分切后进行极片尺寸检测,不合格产品作为废极片处理,合格极片进入下道工序。
制备(自动投料、匀浆):
固态电解质由企业自行制备,电解质制浆采用自动上料系统上料,固态电解质以DMAC(二甲基乙酰胺)为主要溶剂(重量比例超过30%)将其他戊类(LLZTO锂镧锆钽氧氧化物固态电解质)、LiTFSI混合制成浆料。其制备过程同正极(负极)浆料的制备过程一致。滤网上的少量滤渣需定期拆下,用无尘布擦拭干净;另外,遇停产或设备维修,需要用棉布将合浆壁上挂料擦净,产生废擦拭棉布。搅拌机、管道使用NMP溶液(浓度是99%的NMP溶液,混合1%的浆料)进行常温搅拌清洗,15天清洗一次,5.4T/次,清洗过程会产生清洗废液。
涂布:
半固态电解质成型采用转移式连续涂布,烘箱采用蒸汽加热,将制备好的电解质浆料通过隔膜泵和密封输送管道输送到涂布机模头中,通过调整刮刀间隙保证涂层均匀性。涂覆后极片传送到烘箱内经过90~120℃高温烘烤,快速挥发电解质中溶剂。经过牵引、纠偏、辊压、面密度检测合格后收卷。
涂布机产生的DMAC废气通过排风机将其从设备内抽出后,进入热回收器,通过真空泵压入冷凝器[制冷剂为R-134a(四氟乙烷),为目前国际公认的替代R12的主要制冷工质之一,是环保型制冷剂]中,通过一级冷却段、二级冷却段两级冷却水的热量交换后,将冷凝为液态的液体溶剂导入至回收液体罐中,委托供货单位回收处理,剩余废气(<30mg/m2)经排气筒排入大气。主要是利用同一物质在不同温度下具有不同的饱和蒸汽分压,且温度越低,饱和蒸汽分压越低。将废气温度逐级降低后,使废气中DMAC达到过饱和状态而结露析出,从而实现DMAC与空气组分的分离。
电解质干燥过程中挥发的DMAC全部进入NMP回收系统,回收后的回收液委托供货单位回收处理。每天生产完后,涂布机与极片接触位置需要用棉布擦拭干净,产生废擦拭棉布。
电芯模切
采用高速五金模切生产,人工将极卷安装到设备的放卷气胀轴上,设备自动放卷,纠偏机构对放卷过程进行自动纠偏,并通过张力控制系统控制放卷张力,进入模切之前会进行二次纠偏(过程纠偏),放卷储片,冲切工位利用五金模将极耳冲切成型、R角成型、CCD瑕疵检测,然后通过拉料机构拉到裁切位裁切成片后,通过输送皮带运送至尺寸检测,经过刷粉检测后(两面),不良品自动被分类剔除到NG料盒中,合格品被收集到成品料盒。
电芯叠片
将整卷隔膜放入叠片机中,按照正极片—隔膜—负极片相互间隔的方式,在叠片机中进行Z字形叠片。完成后贴固定胶、二维码胶。
设备采用弹夹式极片料盒上料,正负极极片料盒通过人工退入到叠片机的取料位。离子导体膜放卷为主动放卷,有张力控制机构。离子导体膜通过放卷带路引入叠片台,叠片台带动离子导体膜前后往复移动。负极片先叠,负极机械手吸盘先将负极片从负极料盒中取出,经CCD预定位后叠放在叠片台;叠片台移动到正极叠片位,同时正极机械手吸盘将正极片从正极料盒中取出,经CCD预定位后叠放在叠片台上;然后叠片台返回负极,叠负极片。正负极如此交替叠片;设备可实现双工位同时叠片。
单个电芯叠片完成后,机械手夹取电芯下料,依次完成离子导体膜切断,尾卷、自动平贴二维码、侧面贴胶、称重后自动下料至输送线托盘中。
电芯装配
装配采用全自动装配线生产,线体包括:绝缘检测、热压成型、X-RAY对齐度检测、绝缘/厚度检测、预焊、极耳裁切、极耳终焊、焊印贴胶、包Mylar膜、入壳、顶盖焊接、氦检、绝缘检测工序。
绝缘检测:利用绝缘测试仪对电池施加高压直流电,检测电池绝缘性能。
热压成型:利用热烘箱将电池加热到预定温度,电池在高温、高压条件下离子导体膜与极片粘合定型。
综合检测:利用绝缘测试仪检测电池绝缘值,利用高度测量仪器检测极组厚度。
预焊:通过超声波焊接机发出的高频振动波传递到两个需焊接的金属表面,在加压的情况下,使两个金属表面相互摩擦而形成分子层之间的熔合。
极耳裁切:裁切过程对极耳压紧,利用五金刀具将多余极耳裁切掉。
极耳终焊:分别在正、负极焊机上将极耳焊接在电芯叠片体上。正、负极耳均外购,正极耳是由热熔胶带和铝带组成的铝极耳,负极耳是由热熔胶带和铜带组成的铜极耳。此工序采用极耳焊接机,不使用任何助剂,直接使金属相连,因此不产生焊接废气。
焊接工艺介绍如下:锂电池极耳焊接机是利用高频振动波传递到两个需焊接的金属表面,在加压的情况下,使两个金属表面相互摩擦而形成分子层之间的熔合,其优点在于快速、节能、熔合强度高、导电性好、无火花、接近冷态加工,不需任何助焊剂、气体、焊料,环保安全,无焊烟产生,无需安装排焊烟装置。
焊印贴胶带:在焊点位置贴上保护胶带并用测试机进行检测。
包Mylar膜:机械手夹取电芯上料、定位,人工进行底托片上料、绝缘片上料,机械手抓取绝缘片与底托片热熔,对极组绝缘片热熔、侧部热熔,机械手对极组及绝缘片贴固定胶、尾部贴固定胶,采用绝缘测试仪对大面进行绝缘检测。
入壳:设备通过铝壳定位机构定位铝壳,入壳机械手夹取电芯,通过四周的入壳导向装置,将电芯压入到铝壳中,完成入壳。通过合盖机构对入壳后的电池进行合盖,通过检测仪器对合盖后间隙检测,通过激光焊接对合盖后的电池进行预点焊,确定良品和不良品,并将不良品挑选出来。
顶盖焊接:机械手抓取电芯扫码后定位,上保护盖组件、采用激光焊接对顶盖进行焊接,焊接后对焊接外观进行检测提出不良品。激光焊接是以激光束作为能量源,利用聚焦装置使激光聚集成高功率密度的光束照射在工件表面进行加热,在金属材料的热传导作用下材料内部溶化形成特定的溶池。
氦检:通过机械手实现锂电池的上料后,对被检工件抽真空和充注氦气,应用真空箱法进行氦质谱气密性检测,通过该装置判断出被检工件中的合格与不合格,最后将被检工件内的氦气排出。
绝缘检测:利用绝缘测试仪对电池施加高压直流电,检测电池绝缘性能。
电芯烘烤
采用全自动电芯烘烤线生产,将装配后电池抓取放在烘烤夹具内,采用机械人将夹具送入烘箱内,在80~95℃、-0.08MPa条件下烘干一段时间(烘干过程充氮气保护,防止其氧化)去除电芯在制作过程中吸入的微量水分。使用卡尔费休水份检测仪对电池进行水分检测。
界面处理
半固态电池中,正极/固态电解质和负极/固态电解质界面接触电阻相比于液态电池略大,为了更优的电性能,需要注入微量的电池电解液,降低内阻,提升倍率性能。浸润时由真空泵将腔内真空度抽至-60~-90kpa,采用定量伺服泵将电池电解液注入电池内。
电解液固化
电池密封放置在40~45℃高温房内静置10~24H,电解液发生固化反应。
化成/静置
目的为对电芯进行充放电处理,确保正负极表面活性物质充分激活。
工序在锂电池化成机中进行,激活器全密闭,电芯已被封口,将电芯的极耳与激活器的导线相连接,激活器对电芯进行充放电,将电极材料激活,使正、负电极片上聚合物与电解质相互渗透,确保正负极片表面活性。
NCM三元材料中过渡金属离子的平均价态为+3价,Co以+3价存在,Ni以+2价及+3价存在,Mn则以+4价及+3价存在,其中+2价的Ni和+4价的Mn数量相等。
电池充放电过程可用下式表示:LiCoxMnyNi1-x-yO2Li1-zCoxMnyNi1-x-yO2+zLi++ze对电芯进行充电激活电极材料,设备采用负压排气工艺,在湿度露点-30~-40℃,温度45±3℃的环境下进行,可使化成产生的气体及时排除,有效的缓解电池化成过程的鼓胀问题,保证了界面稳定一致。
化成时先采用0.01~0.05~C小电流充电达到一定电压后,静置几分钟再用0.1~0.5C进行充电在达到一定电压后化成完成。
一次注液完成后随即对电池进行负压化成处理,化成工序在密闭化成柜内。
电池在首次充电中,完成电化学反应的产气过程,化成柜直连真空泵抽气以便除去化成工序产生的废气,确保电池密封后不至于再产生更多的气体从而影响电池安全性能和外观尺寸。
电解液中含有六氟磷酸锂(LiPF6),该物质若暴露空气中及高温条件下会分解产生PF5(白色烟雾)。PF5在常温常压下为具有刺激臭的无色有毒腐蚀性气体。热稳定性好,空气中不燃烧。只要有少量水分就水解生成氟化氢和氟氧化磷(POF3),而POF3最终转变成磷酸,即PF。遇水水解生成氟化氢和磷酸。因此,它在空气中强烈地发烟。但在干燥环境下,即使在250℃环境下也不与氢、氧、磷、硫等物质反应。
注液时辅以氮气干燥系统,注液工序采取全封闭形式,采用双层真空不锈钢筒密封储存电解液,通过自动接头到自动注液机进行注液操作,保证注液过程从电解液容器开口到电池注液封口均在封闭状态下进行操作,且车间设置有转轮除湿系统严格控制注液过程的湿度,经采取以上措施后,注液工序六氟磷酸锂分解放出的氟化物气体量很小,可忽略不计。让在化成内压及压力条件下外溢的少量电解液回流至卷芯体,稳定卷芯性能。
激光封口
项目采用激光焊接工艺,电池定位、密封钉自动上料并夹紧定位、激光清洗,激光密封钉预焊定位,封口片圆周焊接等工作,焊接的同时对附近的极柱可实现有效保护。封口后采用氦气作为示踪气体,将已充氦气电池放入真空箱中,然后通过氦检漏仪能高精度迅速准确的判断工件的泄漏情况。在线检焊接过程检测系统,实时监测熔深、焊缝外观、工作距离、焊缝宽度及表面形貌、焊缝位置跟踪来检查焊接效果。
分容
先用0.3~1C倍率将电池充满,再采用0.3~1C对电池进行放电,计算放电容量,分容记录充放电曲线、电池电压、电流、容量、开路电压等特征数据,对应条形码形成电池各种检测数据,并将数据上传储存到数据库。并对电池容量进行挑选,NG电池自动排出。
OK电池输送到静置房在常温25±5℃静置12~24H,再进行分容后首次电压测试,再输送到25±5℃静置7~15天后进行电压测试,计算搁置期内压降情况,将不合格电池挑选出来,合格电池转入下一工序。
自放电检测
检测电池初始电压,将电池放置在恒温房内一段时间后,复测电池电压;计算电压差值得出K值。将不合格电池挑选出来,合格电池转入下一工序。
包膜
清理电池表面、检测电池尺寸后在电池表面贴上一层保护薄膜和条形码,以防划伤。起到保护铝壳作用。
分选
先对电池表面进行清理、检测电池尺寸后在电池表面贴上蓝膜、顶贴片起到保护铝壳和绝缘作用。按照电池的电压、内阻、K值、容量,根据工艺要求进行等级筛选合格产品入库。
电池组电芯预加工
将分选后的电芯按照事先设计好的电压、容量等要求在特定的范围内进行电芯配对。叠装将配组、充电后的若干电芯串并联在一起,并用绝缘胶带包好,并放置在模块盒内,形成一个标准模块。
涂导热胶
在准备好的铝合金上、下壳体内部涂上外购配好的导热胶,导热胶是以有机硅胶为主体,添加填充料、导热材料等高分子材料,混炼而成的硅胶,具有较好的导热、电绝缘性能。激光焊接通过激光焊接机,将配件焊接在模块盒顶盖上。
装配/入箱
焊接好的标准模块进入半自动组装线,进行入箱、串联连接、信号线连接等。外壳焊接通过激光焊接机对电芯顶盖与铝壳壳口进行焊接。
焊接
通过激光焊接机对电芯顶盖与铝壳壳口进行焊接。
测试
成组系统进入测试工序,进行高温老化及充放电测试。
电池检验
每批次生产抽取部分产品进行检验,检验后进行人工拆解(电池进行绝缘检测,并进行放电或绝缘处理,经检测后的锂离子电池使用螺丝刀、扳手等工具进行人工外部拆—48—解,拆开外壳,并对电芯进行进一步拆解(该过程恒温并保持干燥,因企业生产固态锂电池,电芯中添加少量电池电解液,故该过程仅产生少量挥发性有机物)。
固态电池的原理
固态电池工作原理:
●充电过程(锂离子从负极移动到正极):
1.锂离子的脱嵌:
在充电时,负极材料(如锂金属或锂合金)释放锂离子。这些锂离子原本嵌入在负极材料的晶格结构中。
锂离子在电场的作用下,通过固态电解质向正极迁移。固态电解质允许锂离子通过,但阻止电子通过,确保电子只能通过外部电路流动。
2.电子的流动:
电子从负极通过外部电路流向正极,产生电流。这个电子流动与锂离子在电解质中的迁移相配合,以保持电荷守恒。
3.锂离子的嵌入:
锂离子穿过固态电解质,到达正极材料(如锂钴氧化物LiCoO2或其他高容量正极材料)。
在正极材料的晶格结构中,锂离子找到空位并嵌入其中。这个过程伴随着能量的储存。
●放电过程(锂离子从正极移动到负极):
1.锂离子的脱嵌:
当电池连接到负载并开始放电时,正极材料中的锂离子开始脱嵌。
锂离子在电场的作用下,通过固态电解质向负极迁移。
2.电子的流动:
电子从正极通过外部电路流向负载,为设备供电。同时,电子也从负载流回负极,完成电路。
3.锂离子的嵌入:
锂离子穿过固态电解质,到达负极材料,并嵌入其中。这个过程释放了储存在电池中的能量。
固态电解质的主要功能是提供一个通道,允许锂离子在正负极之间移动,同时阻止电子通过,确保电子只能通过外部电路。
固态电池的分类
根据液态电解质占电芯材料混合物的质量分数分类,电池可细分为液态(25%)、半固态(5%~10%)、准固态(0%~5%)和全固态(0%)四大类,其中半固态、准固态和全固态3种统称为固态电池。
半固态电池
相比液态电池,半固态电池减少液态电解质的用量,增加氧化物和聚合物的复合电解质,其中氧化物主要以隔膜涂覆和正负极包覆形式添加,聚合物以框架网络形式填充,此外负极从石墨体系升级到预锂化的硅基负极、锂金属负极,正极从高镍升级到了高镍+高电压、富锂锰基等正极,隔膜仍保留并涂覆固态电解质涂层,锂盐从LiPF6升级为LiTFSI,能量密度可达350Wh/kg以上。半固态电池虽然减少了液态电解质的用量,但仍存在易燃的风险。
全固态电池
相比液态电池,全固态电池取消原有液态电解质,选用氧化物、硫化物、聚合物等作为固态电解质,以薄膜的形式分割正负极,从而替代隔膜的作用,其中氧化物目前进展较快,硫化物未来潜力最大,聚合物性能上限较低,负极从石墨体系升级到预锂化的硅基负极、锂金属负极,正极从高镍升级到了超高镍、镍锰酸锂、富锂锰基等正极,能量密度可达500Wh/kg。
根据固态电解质的材质和特性,固态电池可以被分为几个主要类别,包括硫化物、氧化物和聚合物固态电池。
硫化物固态电池
硫化物固态电池使用的是无机硫化物材料作为电解质,这类材料通常具有较高的锂离子电导率,接近或超过传统液态电解质的水平。
硫化物固态电解质因其高的离子电导率而备受关注,例如Li10GeP2S12(LGPS)电解质的电导率可以达到1.2×10^-2S/cm。然而,硫化物电解质对水汽敏感,容易与水反应生成有毒的H2S气体,且与空气中的氧气、水蒸气发生不可逆的化学反应,导致离子电导率降低和结构破坏。
因此,硫化物固态电解质的开发难度较大,对生产环境要求严苛。
氧化物固态电池
氧化物固态电池使用的是氧化物材料作为电解质,这类材料的离子导电率一般较低,但具有良好的机械性能和化学稳定性。
氧化物电解质的代表是石榴石型结构的Li7La3Zr2O12(LLZO),其离子导电率较高,常温下可达10^-4S/cm。氧化物电解质的致密形貌使其具有更高的机械强度,在空气中稳定性好,耐受高电压。但是,由于其机械强度高,氧化物电解质的形变能力和柔软性能差,电解质片易脆裂,固固界面接触损耗大,限制了其应用。
聚合物固态电池
聚合物固态电池由聚合物基体和锂盐构成,室温下离子电导率较低,但在加热至60℃以上时,离子电导率得到显著提升。
聚合物电解质具有质量轻、弹性好、机械加工性能优良的特点,且其工艺与现有锂电池接近,易于大规模量产。然而,聚合物电解质室温下离子导电率低,且存在锂枝晶穿透造成短路的风险,热稳定性有限。
结合型固态电池
除了上述三种主要类型的固态电池外,还有结合型固态电池,如复合固态电解质,它是由硫化物/氧化物和聚合物电解质复合得到的电解质。这种复合电解质综合了无机和有机固态电解质的优点,兼具高锂离子导电率和电化学稳定性。
此外,还有氯化物固态电解质,它同时具备硫化物的高离子电导率、可变形性以及氧化物对高电压正极材料的稳定性,但在大规模商业化方面尚不具备可行性。
产业链上游:电解质
全固态锂电池使用固态电解质代替传统的有机液体电解质,有望从根本上解决电池安全问题,并且是电动汽车和大规模储能的理想化学电源。当然,用于全固态电池的所有电解质都有其优缺点。当前,世界各地的全固态电池公司都在进行各种电解质系统的技术研发。其中,西方公司偏爱氧化物和聚合物系统,日本和韩国公司正在努力解决硫化物系统。2020年1月中科院成功开发出多体系硫化物固体电解质和高性能固态电池,在固态电池的进程中迈出重要一步。
聚合物固态电解质
聚合物固态电解质(SPE),由聚合物基体(如聚酯、聚酶和聚胺等)和锂盐(如LiClO4、LiAsF4、LiPF6、LiBF4等)构成,因其质量较轻、黏弹性好、机械加工性能优良等特点而受到了广泛的关注。
发展至今,常见的SPE包括聚环氧乙烷(PEO)、聚丙烯腈(PAN)、聚偏氟乙烯(PVDF)、聚甲基丙烯酸甲酯(PMMA)、聚环氧丙烷(PPO)、聚偏氯乙烯(PVDC)以及单离子聚合物电解质等其它体系。
目前,主流的SPE基体仍为最早被提出的PEO及其衍生物,主要得益于PEO对金属锂稳定并且可以更好地解离锂盐。
然而,由于固态聚合物电解质中离子传输主要发生在无定形区,而室温条件下未经改性的PEO的结晶度高,导致离子电导率较低,严重影响大电流充放电能力。
研究者通过降低结晶度的方法提高PEO链段的运动能力,从而提高体系的电导率,其中最为简单有效的方法是对聚合物基体进行无机粒子杂化处理。
目前研究较多的无机填料包括MgO、Al2O3、SiO2等金属氧化物纳米颗粒以及沸石、蒙脱土等,这些无机粒子的加入扰乱了基体中聚合物链段的有序性,降低了其结晶度,聚合物、锂盐以及无机粒子之间产生的相互作用增加了锂离子传输通道,提高电导率和离子迁移数。无机填料还可以起到吸附复合电解质中的痕量杂质(如水分)、提高力学性能的作用。
为了进一步提高性能,研究者开发出一些新型的填料,其中由不饱和配位点的过渡金属离子和有机连接链(一般为刚性)进行自组装,形成的金属有机框架(MOF)因其多孔性和高稳定性而受到关注。
氧化物固态电解质
按照物质结构可以将氧化物固态电解质分为晶态和玻璃态(非晶态)两类,其中晶态电解质包括钙钛矿型、NASICON型、LISICON型以及石榴石型等,玻璃态氧化物电解质的研究热点是用在薄膜电池中的LiPON型电解质。
氧化物晶态固体电解质
氧化物晶态固体电解质化学稳定性高,可以在大气环境下稳定存在,有利于全固态电池的规模化生产,目前的研究热点在于提高室温离子电导率及其与电极的相容性两方面。目前改善电导率的方法主要是元素替换和异价元素掺杂。另外,与电极的相容性也是制约其应用的重要问题。
LiPON型电解质
1992年,美国橡树岭国家实验室(ORNL)在高纯氮气气氛中采用射频磁控溅射装置溅射高纯Li3P04靶制备得到锂磷氧氮(LiPON)电解质薄膜。
该材料具有优秀的综合性能,室温离子导电率为2.3x10-6S/cm,电化学窗口为5.5V(vs.Li/Li+),热稳定性较好,并且与LiCoO2、LiMn2O4等正极以及金属锂、锂合金等负极相容性良好。LiPON薄膜离子电导率的大小取决于薄膜材料中非晶态结构和N的含量,N含量的增加可以提高离子电导率。
固态电池的难点:界面工程
金属锂负极-固态电解质界面存在的问题,并把他们统一划分为静态及动态。静态问题中的化学不稳定或物理接触差都会导致界面阻抗大及固态电池性能衰退.界面修饰是一种普适性较强的解决策略,可通过反应型浸润有效地解决上述问题.在阻隔金属锂与固态电解质直接接触的前提下,均匀地传导锂离子,因此还能在一定程度上解决动态问题。大多数动态问题是金属锂不均匀沉积/剥离反应造成的.静态问题导致的界面不均匀性会衍生出动态问题.对于枝晶生长问题:枝晶可能会穿透聚合物电解质造成电池失效,提高聚合物电解质的模量可以在枝晶尖端产生抑制生长的应力;在无机固态电解质中,金属锂沉积在裂纹内部具有动力学优势.机械应力将积累在裂纹尖端,导致裂纹进一步扩展,甚至电解质完全破裂.此外,电解质的电子导电性可能会导致金属锂直接沉积在其内部,引起电池短路.因此,减少无机固态电解质的缺陷及降低电子电导率能够解决枝晶生长问题;金属锂内部污染物会驱使枝晶形成,因此对其纯化也是抑制枝晶生长的有效策略.另一个动态问题是孔洞形成:尽管在电池制备过程可以构建紧密接触的界面,一旦界面处的剥离速度大于补充速度,孔洞就会形成,减小后续沉积时的有效接触面积,造成局部电流密度提升、枝晶生长等一系列问题.因此,CCS应该在后续研究中受到更多的关注.施加外部压力能够有效地提高CCS.然而,这种做法在实际应用中受限.弹性界面/集流体、三维结构设计是解决动态问题的有效策略。
近年来,固态电解质的离子电导率可以达到甚至超过液态电解质,固态电池的ASR也通过不断优化达到与基于液态电解质的电池相近水平,然而在满足实际使用的前提下,固态电池的性能还相对逊色,逐渐凸显出了动态问题对于实现高性能固态电池的重要性.三维结构是解决动态问题的有效策略,然而结合电化学稳定性问题还延伸出了如下问题值得关注:一般认为Ⅲ型界面对金属锂稳定.然而,该界面在移动的金属锂作用下可能发生剥落,导致副反应发生造成容量损失.且电阻性的Ⅲ型界面层可能会使金属锂完全失去电子传导通路,形成“死锂”.最近的研究工作揭示了金属锂沉积的新机理,并系统地给出了基于蠕变机制的固态金属锂电池设计规则.用于液态电解质的三维多孔集流体可以按照前述设计规则改造,应用于基于蠕变机制的固态金属锂电池.而如何实现大规模高效的基于蠕变机制的三维结构制备仍具挑战.
实现高性能的全固态金属锂电池必须要在解决静态问题的基础上解决动态问题,界面工程可以在不改变金属锂负极及固态电解质性质的前提下显著提高固态电池的性能,是重要的研究方向.然而,单一的解决策略很难完全解决界面问题或是存在实际应用方面的困难.因此,未来的研究应当从固态电解质(材料的选择及成型工艺等)、金属锂电极、电极-电解质界面及电池结构等多方面综合考虑.总之,在走全固态电池的路上,任重而道远!
全固态电池产业化尚需时日,半固态电池寸积跬步,兼具固态、液态电解质的优势。当下仍面临电导率(倍率性能)、界面(循环寿命)和成本问题,发展方向上来看,(半)固态电池核心仍是电解质,对于核心问题有较好解决的均有放量潜质,推荐关注固态电解质及锂盐、高性能正负极等。
半固态电池有望实现高能量密度+高安全性。能量密度:目前主流三元液态电池一定安全性下已接近能量密度上限,当前半固态电池能量密度已达到360wh/kg,后续将继续突破。安全性:半固态电池电解液质量分数仅为5%-10%,固态电解质的不易燃、零挥发,显著提升了电池的热稳定性。
当下仍面临电导率(倍率性能)、界面(循环寿命)和成本问题,发展方向上来看,(半)固态电池核心仍是电解质,现阶段多是聚合物+氧化物等,基于主流固态电解质性能出发,后续为了综合性能大概率延续复合体系的路径,同时添加新型锂盐等,为了提升能量密度大概率要使用高性能正负极比如超高镍、富锂锰基、锂金属负极等,同时辅以外部加压、电解质厚度平衡等工艺优化才可实现较好的性能。但就(半)固态产品而言性能是前提,成本是能否放量的基础,或先在成本容忍度高的领域应用,在新能源汽车领域应用大概率要平衡一部分性能和成本,空间上看,预计2030年固态电池渗透率6%,需求合计约300GWh,未来几年将迎来较快放量。
半固态电池是过渡路线
不过固态电池仍存在离子电导率低导致性能变差、成本高昂等问题,因此距离规模量产还有5-10年。固态电池电解液与电极之间是固-固界面,难以形成像固-液界面那样紧密充分的接触,因而不利于锂离子在正负极间的传输,影响了电池性能,而通过在固态电池内部添加部分电解液可以改善界面接触电阻,因此固态电池未来的技术发展采用逐步转化策略,即电解液含量逐步下降,最终采用固态电解质。按照电解质固液比例的不同,固态电池可分为半固态、准固态和全固态三种,固态电解质比例依次上升。半固态电池基于高安全性、与现有产线的高兼容性以及良好的经济性,成为当下液态电池向全固态电池过渡的最优选择,预计2025年前可以实现规模量产。
目前国内绝大多数厂商的量产规划都是基于半固态电池,以北京卫蓝、赣锋锂业、清陶能源为代表的企固态电池均有望在2023年实现装车。搭载北京卫蓝半固态电池的蔚来ET7预计于2023年上半年交付;搭载赣锋锂电半固态电池的东风E70示范运营车已于1月下旬完成交付,并且同样搭载赣锋锂电半固态电池的纯电动SUV赛力斯SERES-5计划于2023年上市;搭载国轩高科的高合汽车HiPhix将于2023年第一季度开始交付;搭载孚能科技半固态电池的岚图追光轿车,首批新车已量产下线;清陶能源的半固态电池将搭载上汽和哪吒的相关车型。
其实半固态电池对于能量密度提升并没有太大帮助,其短期的驱动因素主要还是安全性的提升,尤其在对于外部撞击、外部加热、内部短路等问题的风险测试中,固态电池的表现远优于液态电池。另外半固态电池在生产制造上与传统的软包电池产线兼容度很高,主要在原有工序的基础上增加原位固态化工艺即可实现快速的切换,所以半固态在短期内具备快速起量的条件,这也是半固态电池能够在今年装配到这么多车型上的主要原因。
-
燃料电池
+关注
关注
26文章
961浏览量
95204 -
材料
+关注
关注
3文章
1229浏览量
27304 -
固态电池
+关注
关注
10文章
699浏览量
27813
发布评论请先 登录
相关推荐
忆联亮相英特尔新质生产力技术生态大会
英特尔新质生产力技术生态大会顺利举行
聚焦培育新质生产力,小笨智能深耕服务机器人赛道
华为云尚海峰:以数智技术为核心,加速培育和形成新质生产力
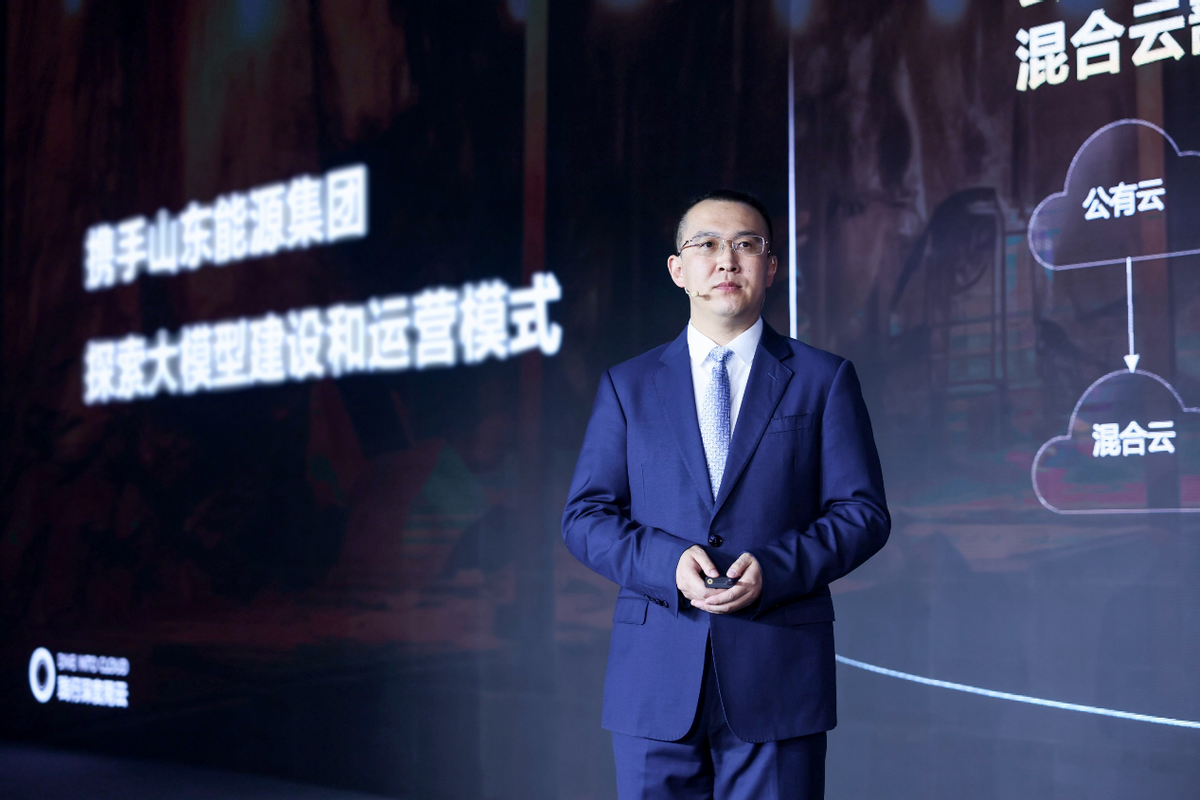
厚植创新沃土 IC PARK用“芯”赋能新质生产力!
亮点·滚烫 | 新质生产力与空间互联网:从“你”和“我”,变成“我们”
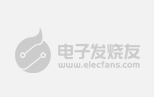
评论