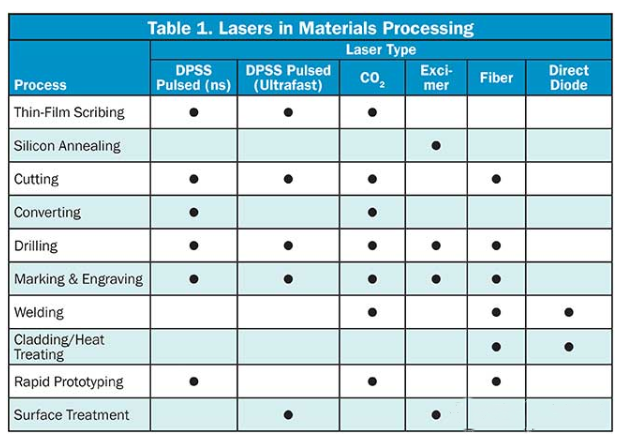
从在实验室条件下在有限数量的样品上成功演示一种新的激光工艺,到将该工艺扩大到大批量工业应用,这是一个重要的步骤。特别是,有必要确定工艺参数的变化如何影响终结果,以便确定可接受的工艺输入和操作范围。
激光材料加工实际上是一个的术语,适用于各种各样的应用。表1总结了这些用途的主要类别以及为其服务的激光器。一方面,在汽车、造船和电器生产等行业,使用千瓦光纤和二氧化碳激光器切割和焊接金属。在光谱学另一方面,紫外和超快激光器用于在微电子、显示器和太阳能电池制造的高精度工艺中钻出微米大小的孔和刻划薄膜。
工艺鉴定在所有这些领域都很重要,尽管主要关注点和主要考虑因素会随着应用范围的变化而变化。例如,在许多钣金切割应用中,环境没有得到很好的控制,并且进料中经常存在批次间的变化。在这种情况下,重要的是要开发一种能够在这些变化的情况下成功运行的流程,通常用于自动化、全天候使用,只需少的操作员干预。
相比之下,高精度工艺的制造环境通常受到严格控制。但是,保持更严格的机械公差的需要可能会更加重视精密夹具的开发。超快过程尤其可能需要更好地控制光学对准,以便保持驱动非线性效应所需的高峰值功率。
成本是关键
无论制造任务的具体情况如何,工艺评定程序的个输入是制造商对工艺必须实现的目标的声明。具体而言,这涉及到为所有工艺结果设置标称值和公差,例如激光钻孔的直径、深度和位置。
工艺鉴定的下一个关键输入是成本。对于大多数制造商来说,实际的衡量标准是每个零件的成本。必须从一开始就考虑这种投入,因为任何新的生产方法只有在比现有方法更便宜的情况下才能用于完成相同的任务;当它提供明显更大的运营灵活性时;或者当它允许生产商以提高自己对消费者的价格的方式增加产品的功能或价值时。
有几个因素会影响每个零件的成本。明显的是生产设备的资本成本及其拥有成本特征,如功耗、其他消耗品和维护成本。然而,还有许多其他因素。例如,生产率,即在给定时间段内生产的零件数量,通常是一个重要的考虑因素,尤其是当工艺生产瓶颈时。此外,机器的增量容量也可能是一个考虑因素。具体来说,从风险调解的角度来看,使用几个容量较低的机器会更好吗?尽管它们的成本效益较低?工艺产量、所需返工水平或某种形式的后处理(如零件清洁)的需求也直接影响成本。
另一个重要的成本问题是支持设备所需的人力。设备是否需要操作员?如果需要,操作员的技能水平如何?这台新机器能很容易地与其他生产设备集成吗?如有必要,它是否适用于自动零件装载和卸载?
机器的维护要求也可能影响人力预算,特别是如果制造商需要配备专业人员来执行系统的日常维护和调整。这是基于激光的设备的一个特别考虑因素,因为激光和光学调整可能超出了公司现有维护人员的专业知识范围。当然,无论是日常维护还是维修的停机时间,加上维修本身的成本,也会对成本产生重大影响。
过程变量
一旦确定了所有这些因素的目标,那么工艺鉴定就涉及到开发一种满足这些成本和质量限制的生产方法,并且可以大规模复制。从本质上讲,过程鉴定是一门统计学学科。在少量零件上证明给定的工艺是不够的,因为这将无法显示当工艺扩大到更大的数量时自然发生的潜在变化。因此,必须进行足够的测试,以产生足够大的样本量,从而可以确定批量生产中预期的零件间变化水平的准确统计数据。
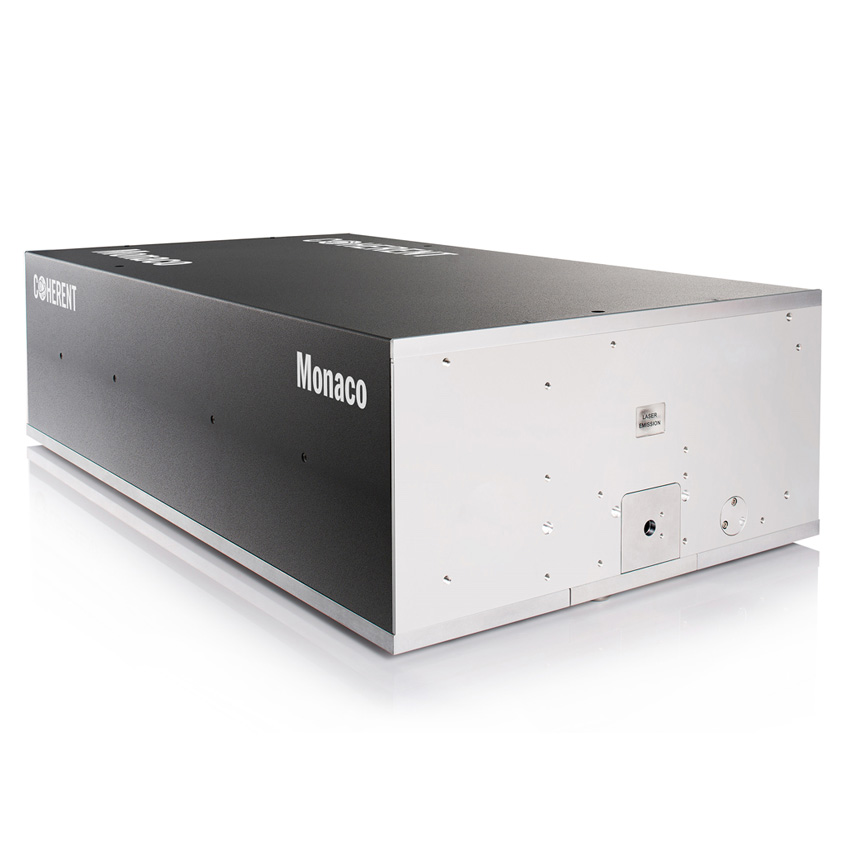
图2:工业超高速激光器,如Coherent股份有限公司Monaco(400-fs脉宽),在高精度材料加工中越来越受欢迎。与较长的脉冲宽度相比,它们的高峰值功率和短脉冲宽度可减少热影响区(HAZ),并降低烧蚀阈值,从而实现对各种金属、半导体和有机材料的高精度加工。由Coherent股份有限公司提供。
有几个因素导致了刚才提到的过程输出的变化。一些明显的因素包括材料、夹具、激光输出、光束输送、环境条件和其他工艺输入条件,如电源或冷却水供应。值得更详细地研究这些因素。
在现实世界的制造环境中,材料通常来自多个供应商,即使在单个供应商的产品中,也可能存在批次间或单位间的不一致。这些变体可以大致分为两类。首先是尺寸变化,如厚度,这显然会影响切割和钻孔等过程。
第二种类型的材料变化是固有的,或者是材料本身性质的差异,例如吸收或反射特性、折射率、热导率、内应力特性、化学成分等。这些变化可能直接影响激光与材料的相互作用,并改变工艺结果。
就激光输出而言,影响工艺结果的明显变量是激光功率或脉冲能量。此外,许多工艺对脉冲形状很敏感,尤其是在决定峰值功率的程度上。这对于超快激光器来说尤其关键,因为超快激光器通常通过非线性过程与材料相互作用,而非线性过程必然高度依赖于峰值功率。
周围环境条件的变化,特别是温度和湿度的变化,会以多种方式影响一个过程。例如,光学机械支架和光学器件本身都可能以改变光束指向或光束形状的方式对温度变化做出响应。这会更改焦点的几何图形或位置,当生成较小的特征时,这一点变得更加关键。同样,由于烧蚀速率是注量的函数,因此尺寸以及靶上的注量对于超快激光器来说尤其关键。
即使在没有任何环境波动的情况下,机械零件的性能也总是存在变化。例如,如果零件被装载到给定的机械夹具中1000次,那么每次零件实际所在的位置都会有分布。
现实中的过程鉴定
理论上,确定每个过程变量可接受极限的理想方法是单独改变每个参数,同时保持所有其他参数不变,然后观察这种变化对结果的影响。
然而,这种方法不切实际,而且通常是不可能的。这是因为在给定的过程中通常存在大量的变量,其中一些变量,例如激光脉冲形状,不能容易地确定地变化。
因此,现实世界中的过程鉴定通常从系统设计开始。具体而言,这涉及到选择系统组件,如激光器、光学支架和零件夹具,这些组件已经证明在相关操作条件下随时间推移是稳定的。换言之,选择高度稳定的激光源消除了测试激光功率变化或脉冲间稳定性影响的过程的需要。
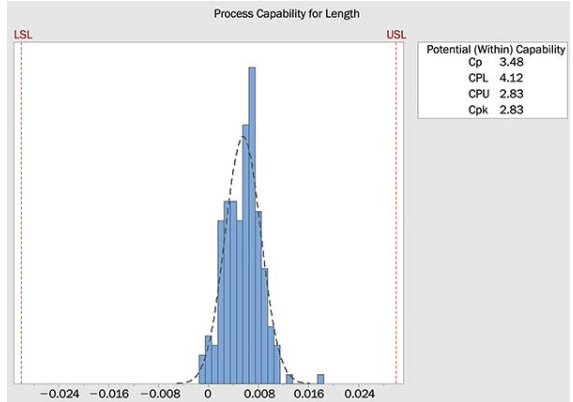
图3。为加工玻璃零件的长度采集的标准化统计数据。由Coherent股份有限公司提供。
此外,在某些情况下,没有必要测试给定变量的影响。相反,一些开销只是简单地添加到流程中,以便它能够正常工作,即使存在预期的变化。例如,可以在测试过程中确定,在理想条件下,激光切割过程可以在1m/s的进给速率下成功操作。但是,由于已知在生产中会有材料变化,因此将生产进给速率设置为0.8m/s以适应这种情况。
当然,这会对成本产生影响。以较慢的速度运行工艺会降低产量,但也可能降低废品率。因此,工艺鉴定的一个关键方面是确定哪些因素是关键的。具体来说,什么结果对成品零件的正确操作是必要的,哪些参数不那么关键。
后,必须使用测试过程生产足够数量的零件,以便对批量生产中预期的零件间变化水平进行统计有效的确定。
展示玻璃应用
回顾一个实际的过程鉴定示例可能有助于使这一切更加具体。在一个案例中,一家显示器制造商与一家激光器制造商签订了合同,以确定使用超快激光器切割小于1毫米的薄玻璃的工艺。
该生产商一直在机械切割玻璃,但这需要在切割后进行研磨和抛光,以提供所需的切割边缘质量。此外,机械切割不具备产生弯曲切割的能力,也不具备处理非平板玻璃的能力,这两者都成为该应用的要求。超快激光加工提供了克服所有这些缺点的潜力。为了使基于超快激光的工艺成为一种具有成本效益的替代技术,生产商确定了必要的生产率、公差和产量。
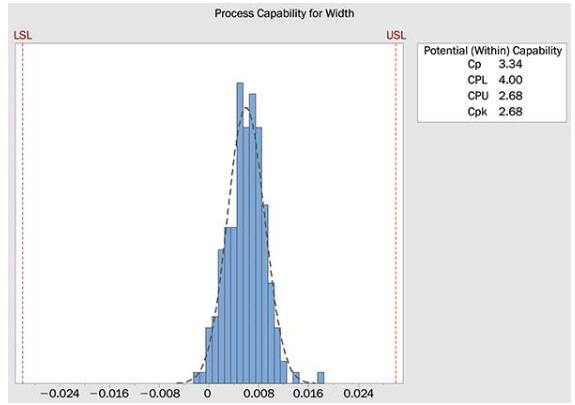
图4 获得的加工玻璃零件宽度的归一化统计数据。由Coherent股份有限公司提供。
很快就确定,为了满足处理时间要求,需要使用高速、电动XY平台进行零件定位的工作平台。然后,任务变成了确定平台移动的加速度值之间的折衷,该值小化了处理时间,同时仍然产生在用户的尺寸精度规范范围内的定位误差。然后,目标是找到具成本效益的控制器和阶段包,能够可靠地提供这种级别的性能。
使用不同阶段加速度值进行了一系列测试运行,以确定这些权衡。连续三天重复这些测试,每天重复几次,以证明随着时间的推移和环境操作条件的变化,该过程是稳定的。测试还利用了几个批次的零件来说明材料的批次差异。特别是,客户已经将玻璃内部应力的变化确定为影响终结果的问题。
加工后,使用光学显微镜测量零件尺寸。此外,还采用了光学表面轮廓仪来测量表面质量。由此,为切割件的长度和宽度尺寸以及加工边缘表面粗糙度的分布组装了结果的统计图(图3-5)。长度和宽度图是测量的特定尺寸的直方图,以及制造商提供的规格上限(USL)和规格下限(LSL)。此外,还显示了测量值分布的理想拟合线。
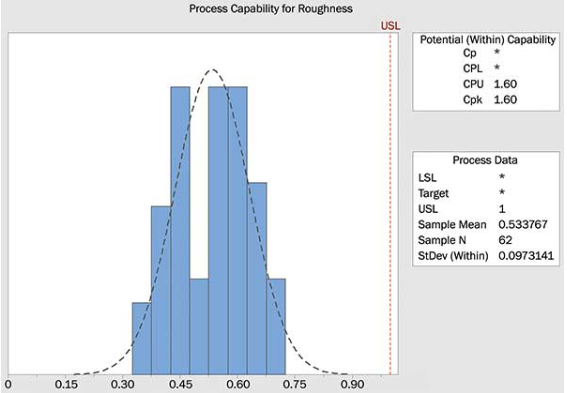
图5 已加工玻璃零件的边缘粗糙度的归一化统计数据。由Coherent股份有限公司提供。
根据这些数据,计算出工艺能力的统计量(Cpk)。Cpk是一个数字,它量化了一个过程相对于过程的自然变异性与规范限制的执行程度。Cpk的值越高,生产的任何给定零件超出规格限制的可能性就越小。例如,Cpk值1.33表示99.99%的工艺产率。
在本例中,通过在连续三天的三次运行中确定机械公差的Cpk值,对该过程进行了鉴定。这些图显示了组合数据的能力。更具体地说,它们绘制的是与标称值的偏差,而不是标注的实际值。Cpk值远大于2时,所配置的工艺被证明是高度可行的。此外,测量表面粗糙度,并计算出Cpk值为1.6。这再次表明,这一过程运行得非常好。
总之,工艺鉴定是从“概念验证”阶段进入生产现实的必要步骤。由于终用户并不总是很好地理解激光加工的细微差别,因此通常可以通过与具有进行工艺验证研究能力的激光供应商合作来好地实现这一点。
审核编辑 黄宇
-
激光器
+关注
关注
17文章
2551浏览量
60802 -
光谱
+关注
关注
4文章
848浏览量
35395
发布评论请先 登录
相关推荐
半导体激光器和光纤激光器的对比分析
半导体激光器的波长应该如何选择
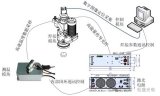
垂直腔面发射激光器(VCSEL)的应用
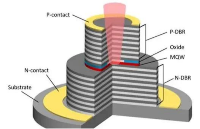
浅谈半导体激光器的应用领域
电子科普!什么是激光二极管(半导体激光器)
驱动激光器的窄脉冲是怎么产生的?
石墨烯在激光器中的应用
半导体激光器的工作原理和应用
选择手持激光焊接机激光器的 5 大秘诀!壹晨激光为你揭晓!
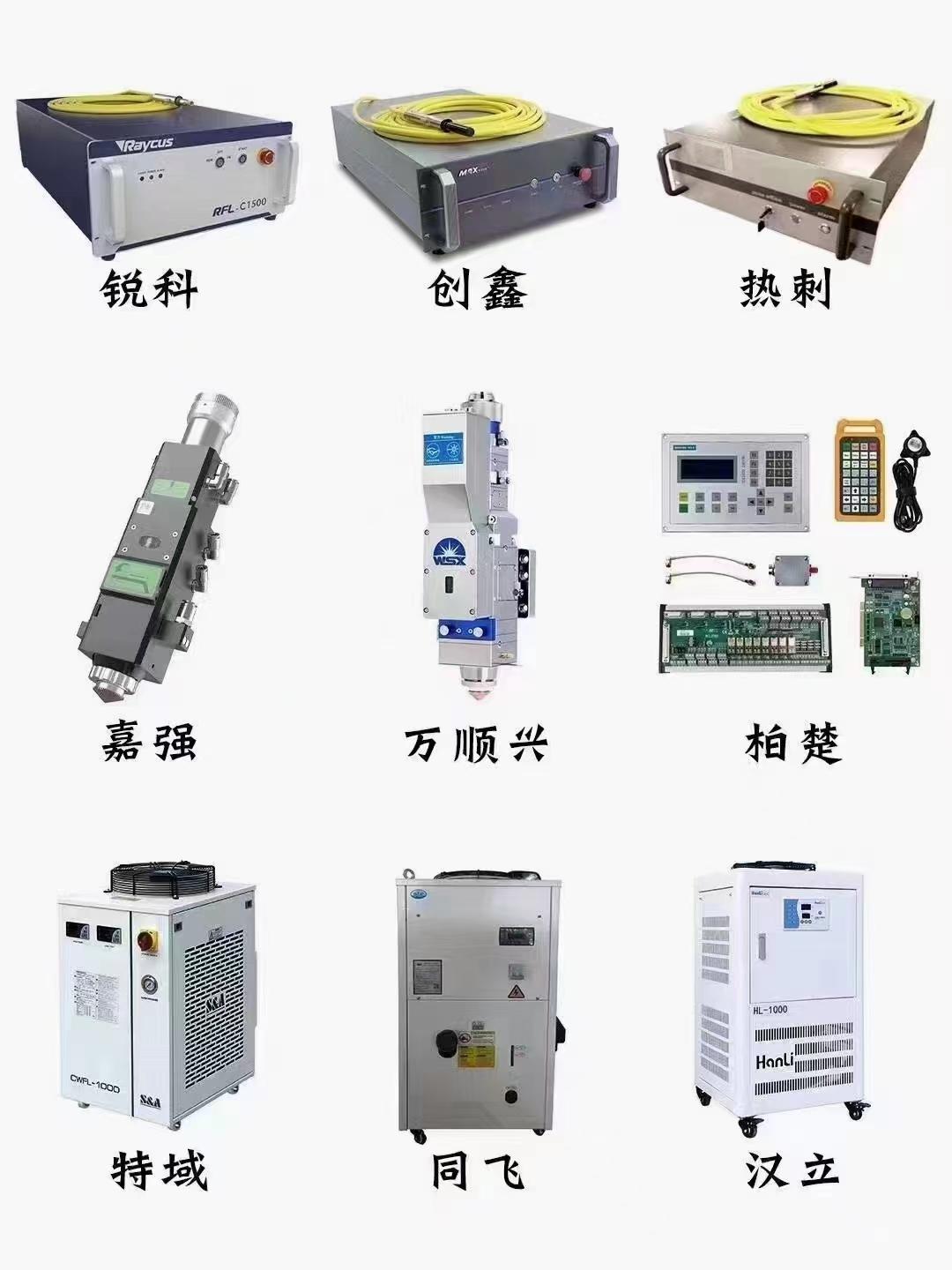
评论