随着国内制造业朝着自动化、智能化方向快速发展,产品质量检测也由过去的脱机、人工检测方式向在线自动检测转变,作为在线检测的重要工具,机床测头在制造业自动化生产过程中发挥着非常重要的作用。
1.自动化检测与防呆:机床测头可以自动检测工件的位置和尺寸,以实现快速工件定位和位置校正。这对于确保零件加工的首件正确性至关重要,避免了因为人工操作造成的误差,提高了加工精度和测量一致性;
2.刀具磨损监控与补偿:机床测头能够定期检测刀具尺寸和状态,实现自动刀具磨损补偿,确保加工尺寸的稳定性,这不仅提升了产品的加工质量,还延长了刀具寿命,降低了生产成本;
3.自动化分中与位置调整:传统的人工校准既耗时又易出错,机床测头支持快速自动校准,包括机床坐标系、旋转轴精度以及刀具长度和直径的校定,大大缩短了准备时间和提高了生产线的灵活性;
4.过程控制与质量保证:在加工过程中,测头能够实施在线质量检查,实时监测关键尺寸和几何特征,及时发现并纠正偏差,减少不良品产生,提高生产良率;
5.数据采集与分析:现代机床设备通常配备有数据通信能力,配合外部数据采集软件能将测量数据实时反馈给控制系统或MES(制造执行系统),实现生产过程的数字化管理。数据分析可以实时监控加工动态以及优化工艺流程,从而实现持续性改进;
6.降本增效:通过减少停机时间、消除人为错误、降低废品率,机床测头直接促进了生产效率的提升和运营成本的下降。下面通过一个实际案例来了解中图仪器机床测头在零部件自动化生产过程中的具体应用。客户背景
广东某公司,专业生产自动化设备零部件,现场使用855中型立式加工中心(FANUC 0I MF-PLUS数控系统),直线导轨式机器人加零点定位工装夹具,配置MES控制管理系统。
测量难点
1.加工前机器人自动上下料,毛坯长宽无法确认是否装夹正确;
2.毛坯余量大小不均,加工高度Z基准无法确认;
3.加工后产品尺寸无法确认是否合格,需要间隔时间送三坐标室检测,工作量大且测量等待时间长,加工异常无法及时有效发现;
4.测量数据无法反馈给MES系统,系统也无法对加工过程做有效管理控制,同时MES系统也无法根据反馈结果做出相应的指示动作;
5.产品加工检测数据无法实时采集归类以及数字化管理。
中图仪器机床测头在线检测方案
配置:中图仪器PO40红外触发测头(测针长度50mm,测球直径2mm)+发那科定制测量宏程序。
加工测量流程如下:
1.编程员利用Fanuc系统定制测量宏程序编写加工前防呆测量和更新坐标Z主程序;
2.编程员利用Fanuc系统定制测量宏程序编写加工后检测程序;
3.编程员把加工前测量程序/加工程序/加工后测量程序串联成新程序同时按照命名规则重新命名,并放入指定文件目录;
4.MES系统根据要加工的零件自动引导机器人上料同时分配对应测量加工程序;
5.设备自动启动后根据分配好程序预先调用红外测头按照一定安全位置盲测实际安装毛坯长度和宽度,同时把测量结果与理论值进行对比,判断毛坯大小位置安装正确与否。
6.盲测毛坯顶面高度位置,按照产品加工Z坐标自动更新零点;
7.调用加工刀具开始加工;
8.加工结束后使用扫屑装置清理干净产品测量位置;
9.调用测头检测预定测量尺寸位置,数据采集软件同步采集测量数据;
10.判断尺寸合格与否,同时反馈给MES系统做出相应动作(比如欠加工补偿后再精加工一次或者这过切加工报废则反馈信号给MES系统指导机器人卸料放置于报废区域);
11.加工测量结束,MES系统引导机器人卸料于指定位置;
12.数据采集软件把测量数据放入指定文件目录以便数字化管理和测量数据追溯查询。
应用效果
1.降低了产品因为装夹错误而导致的撞机(停机)的风险;
2.降低了因为毛坯余量不均导致的欠加工或者过加工风险,避免了产品加工不良和批量报废;
3.降低了人工介入的次数,提高了产品的生产效率和生产良率;
4.降低了操作人员的劳动强度;
5.测量数据可输出存储,提高了产品质量问题追踪溯源能力,为数字化管理提供有力的数据支持。
机床测头的应用大大提高了零部件生产的自动化水平和精度控制能力,缩短了生产周期,降低了成本,提升了产品质量,提高了产品市场竞争力。
-
检测
+关注
关注
5文章
4490浏览量
91496 -
自动化
+关注
关注
29文章
5585浏览量
79326 -
管理系统
+关注
关注
1文章
2509浏览量
35934
发布评论请先 登录
相关推荐
MBox20网关助力汽车零部件企业实现与效率飞跃
3D 视觉定位技术:汽车零部件制造的智能变革引擎
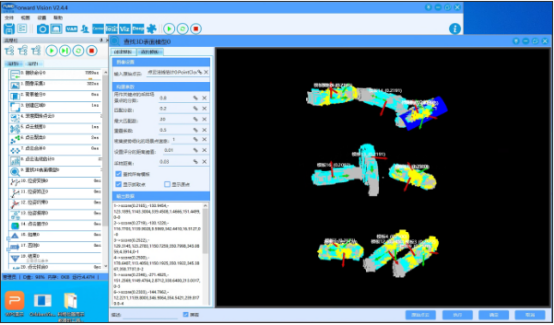
机床测头助力塑胶模具自动化生产
3D扫描仪为民航零部件制造精准护航!
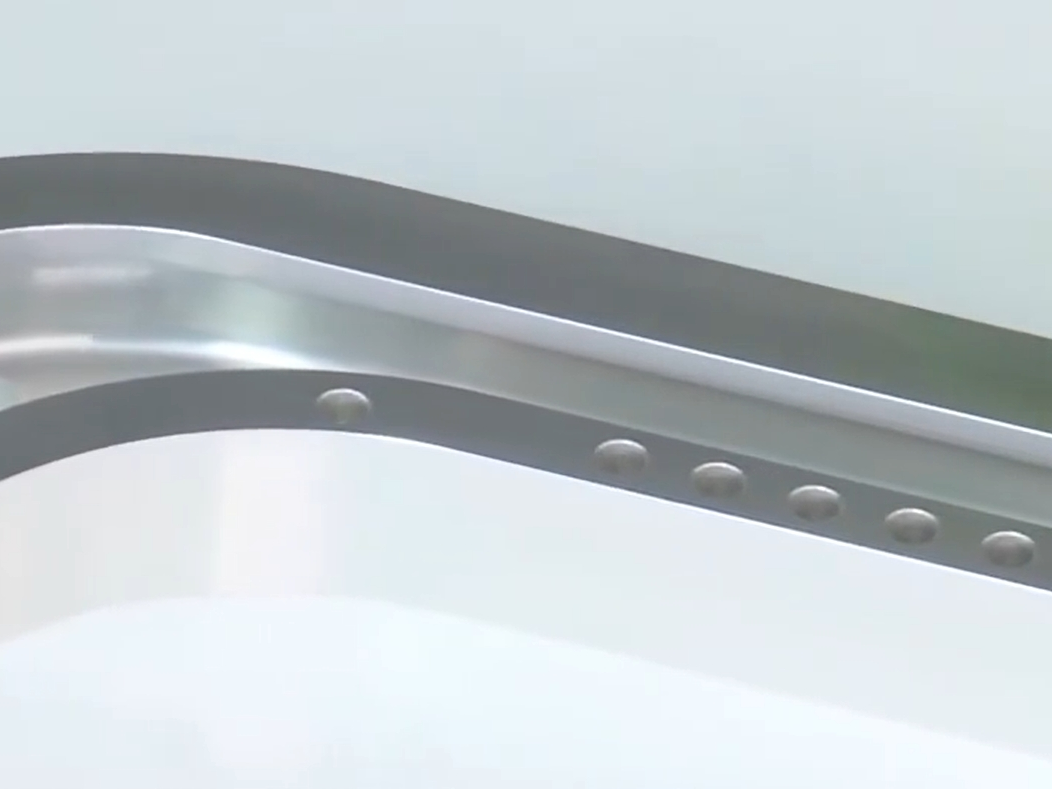
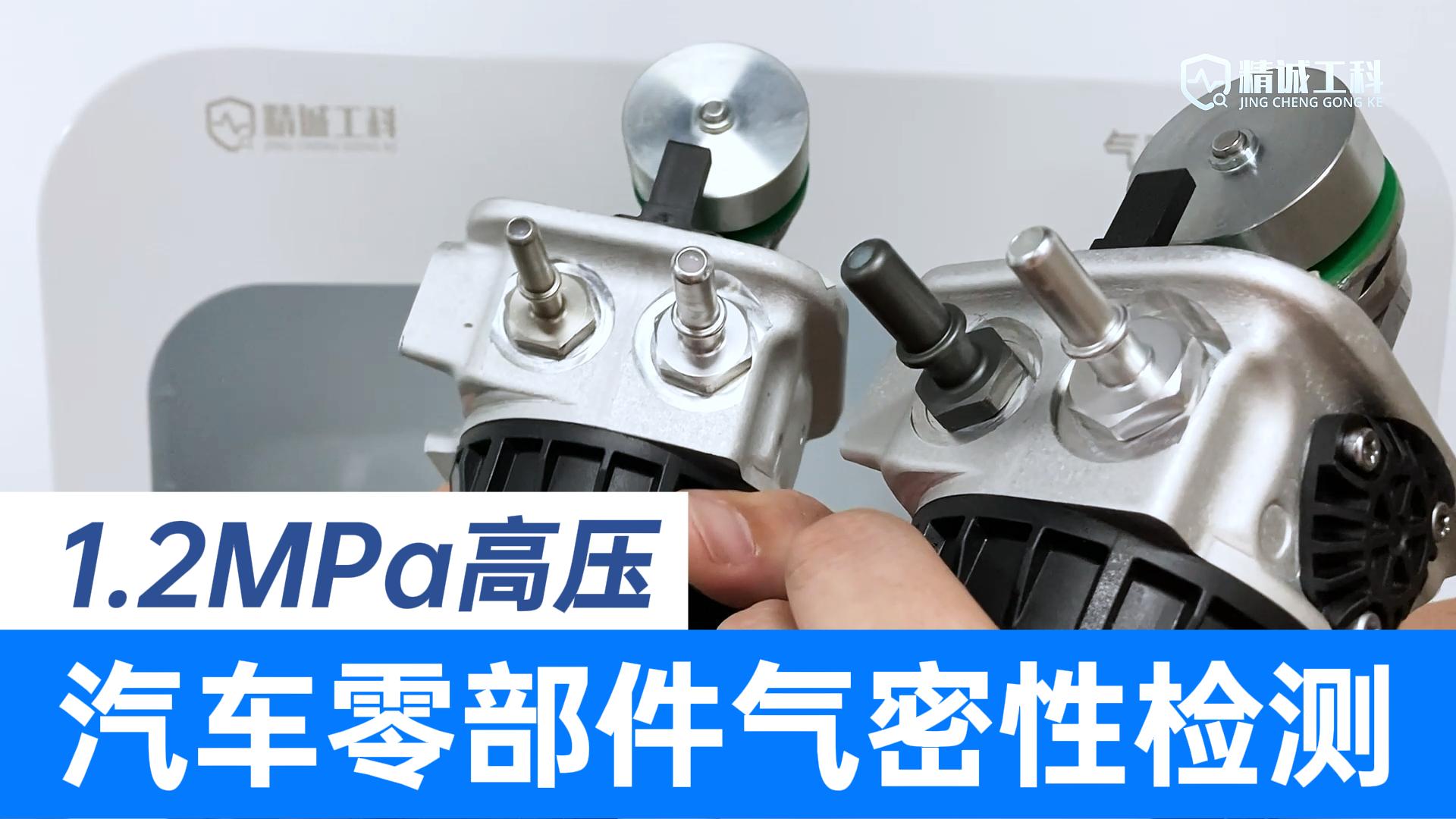
三坐标CMM三次元用于测量电子零部件
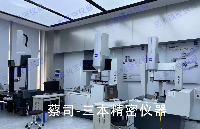
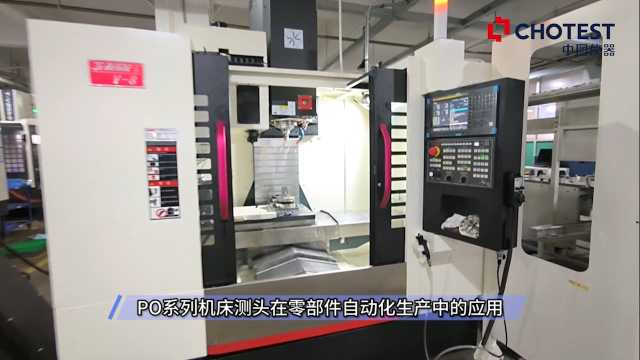
机床测头助力零部件自动化生产
汽车零部件MES系统功能
汽车零部件制造迎来智能化升级,3D视觉定位系统助力无人化生产线建设
汽车零部件需要做哪些环境试验?
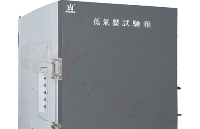
CASAIM与LG化学越南工厂达成全自动化智能测量技术合作,助力汽车锂电池相关零部件全自动化测量及质量管控
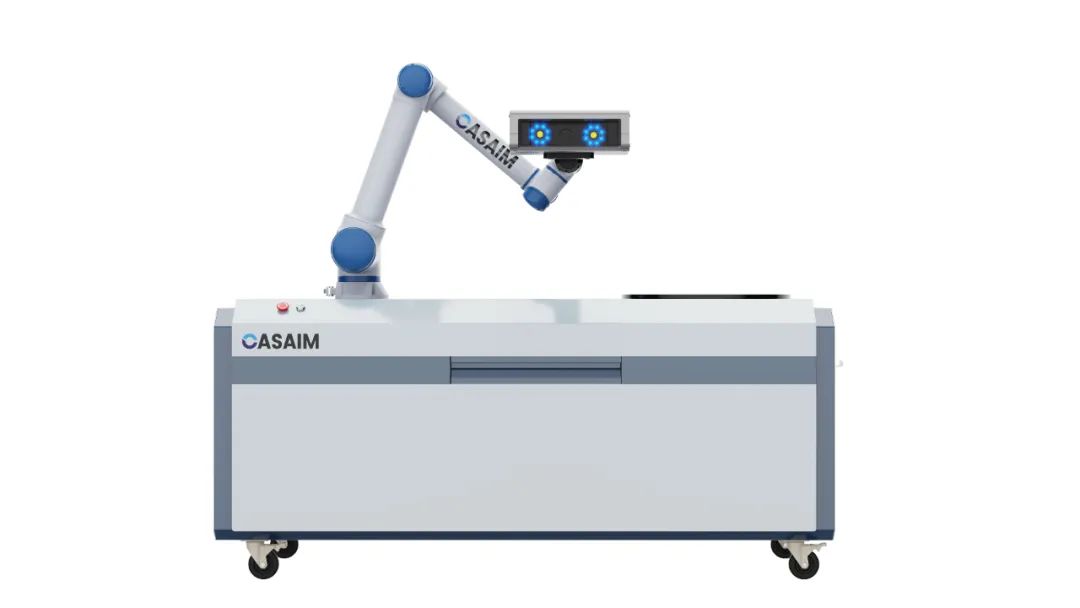
评论