3D视觉引导方案,下料器的摆放精度直接关系到产品的最终质量和生产效率。如何在繁忙的生产线上,确保下料器能够精准无误地将工件放置在指定位置,成为了摆在我们面前的一大挑战。今天,我们就来揭秘我们的3D视觉引导方案,如何在视野宽度1500mm、相机分辨率2000万的情况下,确保下料器摆放精度达到±2mm。
一、高精度的3D视觉系统
首先,我们的方案采用了高精度的3D视觉系统。这套系统通过高速相机和先进的图像处理算法,能够实时捕获生产线上的工件信息,并对其进行三维重建。在视野宽度1500mm的范围内,我们的系统能够清晰地识别出工件的每一个细节,为后续的摆放提供了精确的数据支持。
3D视觉
二、智能算法优化
然而,仅仅依靠高精度的视觉系统是不够的。为了确保下料的摆放精度达到±2mm,我们还需要对算法进行优化。我们的研发团队通过大量的实验和数据分析,对视觉识别、路径规划、机器人控制等各个环节进行了精细的调整和优化。
在视觉识别方面,我们采用了先进的特征提取和匹配算法,能够准确识别出工件的位置和姿态。在路径规划方面,我们考虑了多种因素,如机器人的运动轨迹、工件的形状和尺寸等,以确保机器人能够按照最优的路径进行摆放。在机器人控制方面,我们采用了高精度的伺服电机和控制器,确保机器人能够按照预设的路径和速度进行运动。
三、实时反馈与调整
此外,我们的系统还具备实时反馈与调整的能力。在机器人进行摆放的过程中,我们的系统会不断对工件的位置和姿态进行实时监测,并将监测结果反馈给控制系统。如果发现实际摆放位置与预设位置存在偏差,控制系统会立即对机器人进行微调,以确保最终的摆放精度达到±2mm。
通过我们的3D视觉引导方案,我们已经在多个铝合金板件加工企业成功实现了下料器摆放精度的提升。在实际应用中,我们的系统不仅提高了生产效率,还降低了不良品率,为企业带来了实实在在的经济效益。
综上所述,我们的3D视觉引导方案通过高精度的视觉系统、智能算法优化和实时反馈与调整等手段,成功实现了铝合金板件加工中下料器摆放精度的提升。在未来,我们将继续不断优化和完善我们的方案,为更多企业带来更高效、更精准的自动化加工解决方案。
审核编辑 黄宇
-
机器人
+关注
关注
212文章
28895浏览量
209573 -
3D视觉
+关注
关注
4文章
442浏览量
27730
发布评论请先 登录
相关推荐
解决方案 3D 视觉机器人赋能汽车制造新征程
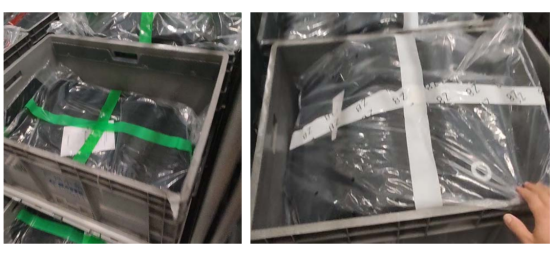
洛微科技3D视觉引导软包拆垛解决方案
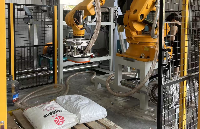
3D视觉引导的多SKU纸箱拆解
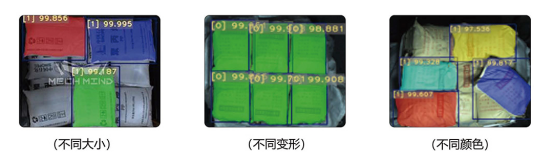
3D视觉引导技术,助力打造高效的物流管理体系
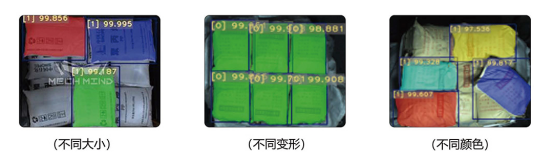
技术突破:铝合金板件正面保护与3D视觉引导的完美结合
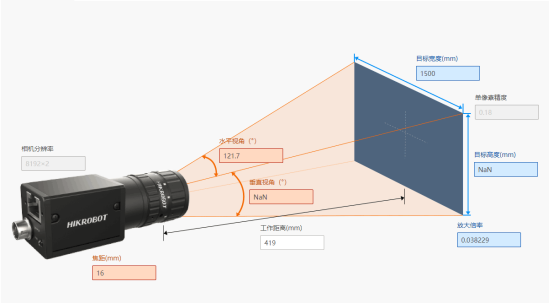
解决方案|3D视觉引导多SKU纸箱混拆
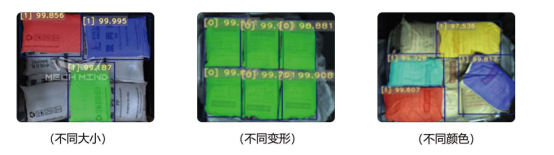
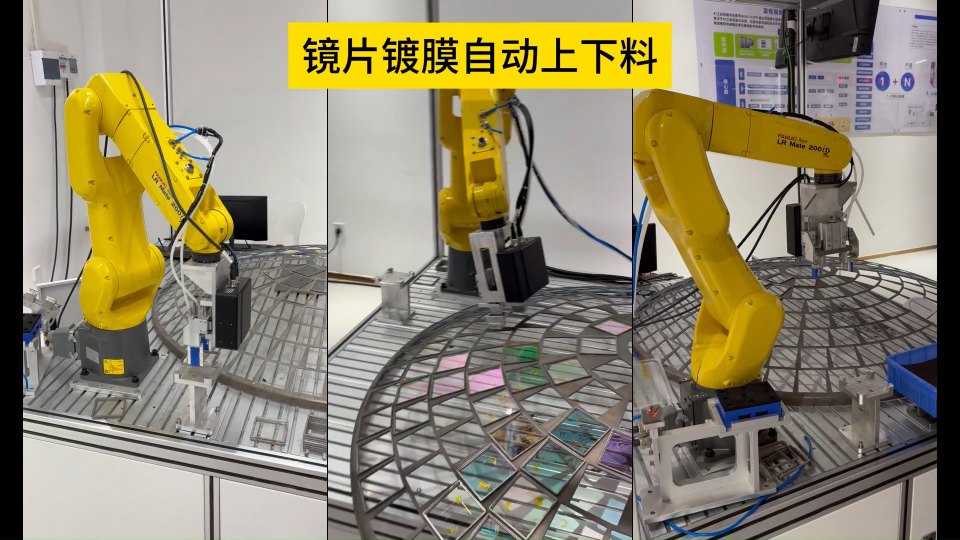
富唯智能案例|3D视觉引导机器人抓取鞋垫上下料
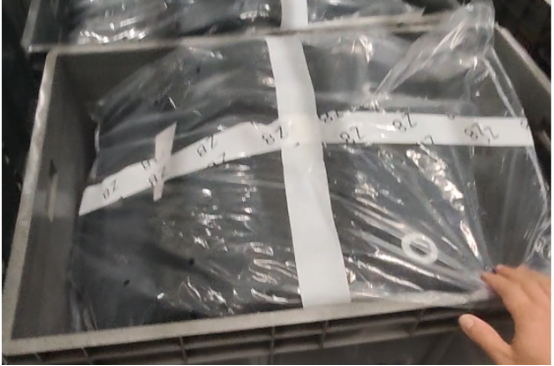
采用3D视觉引导技术实现缸套的自动化下料,从而提升生产效率、降低成本并提高产品质量
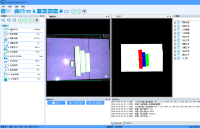
评论