盘点设备管理5 大 误 区
随着设备自动化、数字化水平的提高,工厂亟需提升设备管理能力。在智能制造的浪潮下,制造业也正在积极转型,自动化、数字化、智能化水平大大提高。但是,多数制造企业虽然花费巨资上马了非常先进的设备,但设备管理维护、人员知识结构仍停留在较低水平:数采基本靠笔,处理基本靠人,分析基本靠猜(经验)。可以说是买来了工业4.0的设备,却延续着工业2.0的管理。
从设备资产效益产出角度看,我国制造业的设备综合效率的提升空间巨大。据统计,我国大部分离散制造业的OEE在40%左右,距离发达国家至少还有30%-40%的提升空间。同时,很多企业对设备维护和保养的精细化管理不够重视,造成异常停机和备件浪费等隐性损失。在当前疫情冲击、全球化局势不确定性进一步增加的形势下,提升设备管理水平可以为企业的生存发展,提升竞争力带来宝贵的机会。
如何构建面向新型设备的管理能力,是当前我国制造业面临的一个问题和挑战。为此,我们总结了制造业企业存在的5大误区,并给出了对应的策略建议,希望可以帮助企业少走一些弯路。
大部分企业新建工厂或者新购买的设备,只重视硬件的验收交接,忽视了软件系统的运行、维护、服务标准,没有明确要求设备厂商提供数据采集接口和定义设备数据所有权。
根据相关数据统计,目前我国企业生产设备的数字化率平均为47%,关键工艺的数控化率51%,关键设备联网率41%。嵌入式软件、人机界面、数据监测模型、管理平台都是智能设备的重要组成部分,也都应当是设备管理的范畴。设备数据采集受制于工业现场协议众多、原厂不开放不支持、设备数据不确权等原因,设备数采仍然是生产现场数字化推进中最大的痛点之一。
●设备管理经历了四个发展历程●
从1.0的纠正性维护(CM),
2.0预防性维护(PM)、
3.0的可靠性维护(RCM)、
4.0的预测性维护(PHM),本质上是以设备健康管理(EHM:EquitmentHealthMangment)为中心,从“治已病”到“防未病”的进化过程。通过EHM,设备健康状态不再是简单地划分为正常、异常。
我们可以通过新技术、新工具,分析积累的基础数据,评估出设备的亚健康状态,提前维护,大大减少设备维护成本。配备带有振动传感器的智能点检仪,就像给医生配了“智能听诊器”一样,通过数秒的监测振动,结合内置的频谱分析模型,就可以准确、快速地判断出设备健康状态、故障征兆原因,对设备工程师故障诊断起到重要辅助作用。这样,设备管理人员的职责从原来的坏了再修,转向如何保障设备健康运行的专业维保维护工作,进入良性循环。
虽然TPM已经推行了多年,但许多管理者观念和行动上,还是认为设备出了问题,就是设备部的事情,导致生产部门对设备的故障不关心,对影响产量、质量的设备维护不重视。设备维护工程师也往往因为地位低、薪酬低,自嘲为看门狗和替罪羊:节假日,别人可以休息,他们却不能离开,因为这正是维修设备的好时机;凡是出了问题,无论是设备停机,生产停产,还是质量事故,都会与设备相关,设备人员几乎永远是背锅侠。
设备部成了优秀人才最不愿意去的地方这种恶性循环现象需要生产管理者身体力行,树立正确的设备管理理念,构建生产为主体的全员自主维保体系。只有生产部门管理者重视起来了,生产设备操作者才会改变对设备漠不关心的态度,才能有效进行设备保养。这个光靠设备部是玩不转的。
零故障是不可实现的,企业在遇到困难需要削减成本时,很多情况是拿设备维修费用开刀,甚至提出让维修预算每年递减百分之几的目标。从传统财务角度看,设备维修资金一般被定义为成本和费用。其实早在30年前,德国召开欧洲维修团体联盟国际会议时,就提出“维修——为了未来的投资“的主题。作为投资,就需要有清晰的投入产出。维修的投入是设备日常维护所投入的人工费、各类防护费、备件费,以及设备管理系统的投资。产出是什么呢?是避免由于设备维护不足、设备管理不善,带来的设备停机、精度或者质量缺陷带来的损失。如果对这些损失的价值误判,则容易扼杀设备维护技术和管理体系的改善性投入。
降低设备停机1小时的价值,仅仅是这1小时涉及到的员工的人工成本。设备停机一小时的损失,要从工厂视角端去衡量整体,这里面其实包括了产能损失的机会成本,即1小时的产品产值损失,才是这个工厂真正的损失。这样算下来,工厂许多可以改善停机、改善浪费、现场精益类的小改小革的项目,都可以进行开展,能激发起基层员工的创新积极性,也确实能给工厂带来实实在在的效益。
在实际操作中还存在一个问题,就是备件的更换,很大程度上掌握在维修工手上,存在着许多“人为掌握”更换的因素。维修人员大都靠经验判别备件损坏程度,对怀疑有故障的零部件,通常为了减少麻烦,即使还可以用也会更换成新的,导致产生过度维护的隐性浪费。这块隐形的损失,如果通过构建更精准的备件寿命管理,可以转变成“利润”。
设备维护工作由过去强调为生产服务,追求较高的设备完好率指标转变到以企业的经济效益为中心,要求设备管理工作重视维修费用的管理与控制,找到以最少的维修费用达到最高的设备可利用率的平衡点。企业高层管理者应当从“投资”的角度认识维修和设备管理,实现转变设备管理理念。
预测性维护的落地比预想中困难,是因为企图单纯依赖数据提取可解释的工业机理逻辑,难度远超想象。
●主要有两个原因●
1
许多企业的基础数据还缺乏积累
比如设备基本的巡点检、维护保养、故障分析记录,都还是散落在各种纸张、Excel中,设备缺乏数字化档案,基本维护保养数据、备件更换记录、故障和修理数据,包括设备的故障特征数据还没有结构化的积累,就不可能实现模型的训练和验证;
2
许多厂商企图单纯依赖数据分析路径而忽略了设备工程师现有专业知识和经验的融入
光靠数学和AI算法容易走入统计陷阱,只是得到了相关性,不容易得出可解释、可预测的因果性模型。所以我们建议工厂一是要重视设备数字化档案、基础维护、维修工单、故障树等这些基本数字化能力的建设。二是针对重点的高价值、停机高损失设备,将经验模型和数据模型结合建模,而且模型的输出,目的是起到辅助人员维护维修的作用,最后还是需要交给人来综合判断。
构建新型的设备管理能力,需要工厂管理者认识到设备是构建工厂核心竞争力的基础,积极变革设备管理和作业方式,向数字化、智能化发展。
免责声明
本文内容来源于互联网,仅供学习、交流。版权归原作者设备人所有,如有侵权联系必删。
审核编辑 黄宇
-
数字化
+关注
关注
8文章
8783浏览量
61932 -
设备管理
+关注
关注
0文章
116浏览量
9320
发布评论请先 登录
相关推荐
TPM:企业设备管理的卓越策略
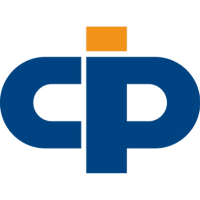
设备管理流程优化的优势
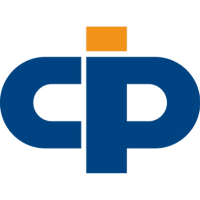
设备管理:医疗设备管理创新与优化之路
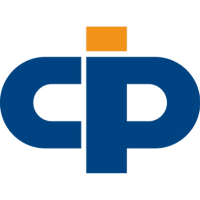
评论