一、引言
随着工业自动化的快速发展,可编程逻辑控制器(PLC)作为工业自动化领域的核心控制设备,已经深入到工业生产的方方面面。PLC以其高度的可编程性、稳定性、可靠性和灵活性,对工业控制产生了深远的影响。本文将从PLC的定义、特点出发,详细探讨PLC对工业控制的影响,并结合相关案例进行分析,以期为工业控制领域的发展提供参考。
二、PLC的定义与特点
定义
PLC是一种专门为工业环境设计的数字运算操作的电子系统,它采用可编程的存储器,用于在其内部存储执行逻辑运算、顺序控制、定时、计数和算术运算等操作的指令,并通过数字式或模拟式的输入/输出控制各种类型的机械设备或生产过程。
特点
(1)可编程性强:PLC具有强大的可编程性能力,可以按照用户需求自由定制具体的控制方案。同时,PLC还支持多种编程语言,如梯形图、指令列表、结构化文本等,大大提高了程序编写的灵活性。
(2)稳定性高、可靠:PLC采用了先进的电子技术,具有高度的稳定性,能够在各种恶劣的工业环境下稳定运行。其内部硬件采用高品质的元器件,具有较高的抗干扰能力,并且具备自动纠错和异常处理的功能。
(3)适应性强:PLC具有很强的适应性,可以应用于各种不同领域的自动化控制。它可根据不同的生产需求进行定制设计,同时还具备较高的扩展能力,可以根据不同的应用场景进行扩展,以实现更多的自动化控制任务。
(4)操作简单、便于维护:PLC采用图形化的编程界面,用户只需要进行简单的拖拽、连接等操作就可以完成程序的编写。同时,PLC还支持在线调试、实时监控等功能,使控制更加方便和智能。由于其结构简单,故障排查和维护工作都相对容易。
三、PLC对工业控制的影响
提高生产效率
PLC通过精确控制生产设备的运行,实现了生产过程的自动化和智能化。在生产过程中,PLC可以实时监测和控制各种工艺参数,如温度、压力、流量、速度等,确保生产过程的稳定性和高效性。例如,在石油化工行业中,PLC可以控制反应器的温度、压力和物料的流动速度,从而保证整个炼油过程稳定安全。这种自动化控制不仅提高了生产效率,还降低了生产成本。
提升产品质量
PLC通过精确控制生产设备的运行,确保了产品质量的稳定性和一致性。在生产过程中,PLC可以实时监测生产数据,如温度、压力、流量等参数,并根据预设条件进行自动调整。这种数据驱动的方法有助于改进生产过程、优化资源利用和实现智能决策。以食品生产行业为例,PLC可以控制整个生产过程,包括原料的投放、搅拌、加热、冷却等步骤,大大提高了产品的质量和口感。
增强生产安全性
PLC通过集成安全控制功能,确保了工业系统的安全运行。PLC可以监测和响应潜在的危险和风险,通过编写安全逻辑和安全检测程序,防止因操作失误、工艺参数异常等原因导致的风险。这种安全保障功能有助于保护工人的安全,并减少事故和损害的发生。在汽车制造过程中,PLC可以控制机器人的动作和自动化装配线的操作,并通过实时监测各个环节的运行状态,及时发现并处理异常情况,从而确保生产过程的安全性。
促进工业智能化发展
PLC作为工业自动化领域的核心控制设备,其应用推动了工业智能化的发展。随着工业4.0和物联网等技术的不断发展,PLC将与人工智能、机器学习等先进技术融合,实现更智能化的控制。同时,PLC还将借助高速通信网络,实现更高效的数据传输和处理。这种智能化的发展将使得工业控制系统更加灵活、高效和可靠,进一步推动工业生产的进步。
四、结论
综上所述,PLC对工业控制产生了深远的影响。它提高了生产效率、提升了产品质量、增强了生产安全性并促进了工业智能化的发展。随着技术的不断进步和工业自动化的深入发展,PLC将在工业控制领域发挥更加重要的作用。
-
plc
+关注
关注
5019文章
13400浏览量
465947 -
工业控制
+关注
关注
38文章
1472浏览量
86088 -
工业自动化
+关注
关注
17文章
2489浏览量
67444
发布评论请先 登录
相关推荐
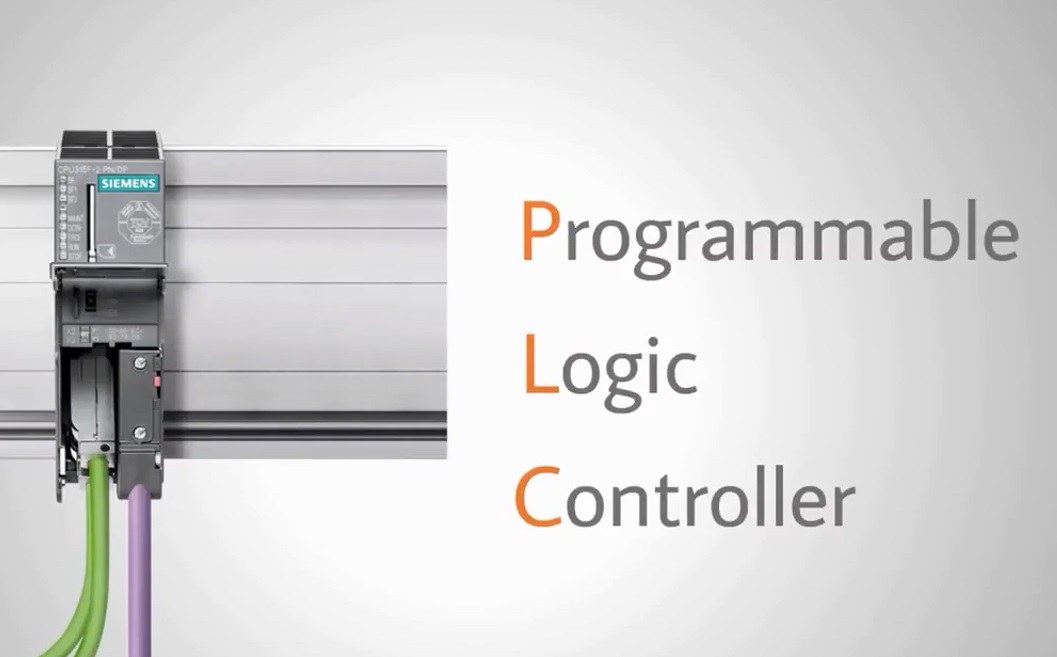
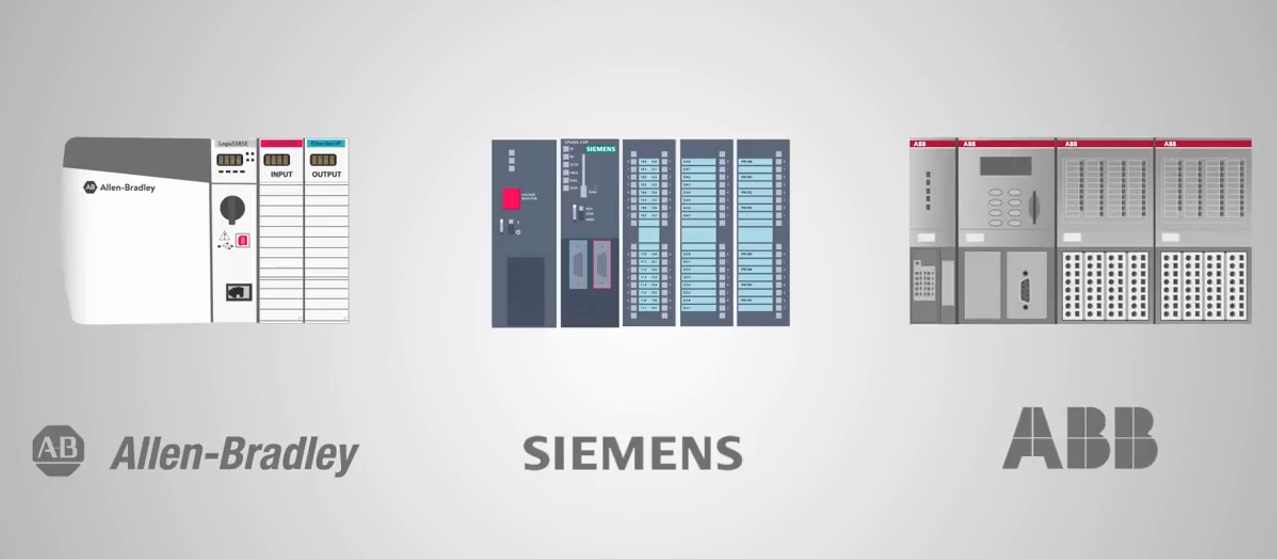
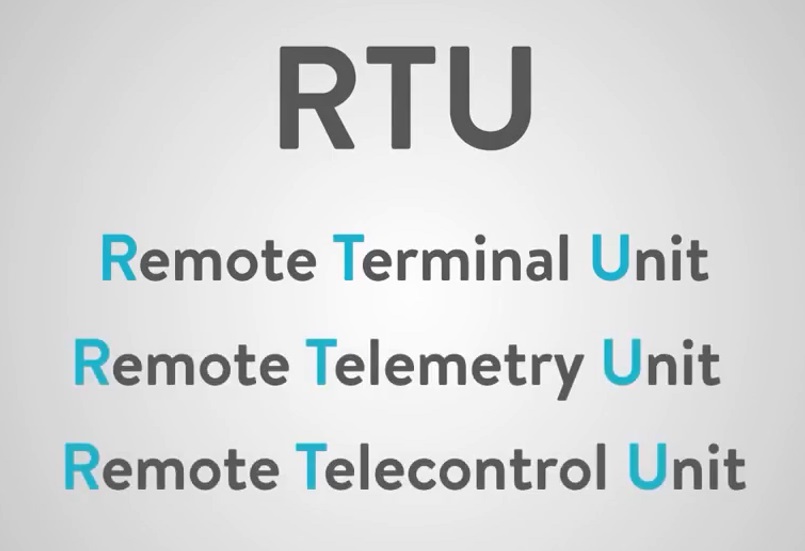
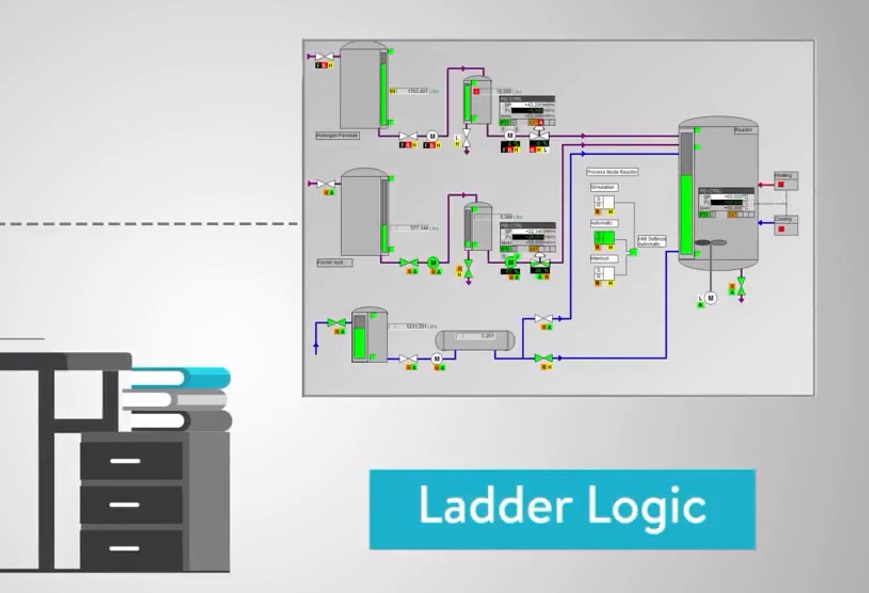
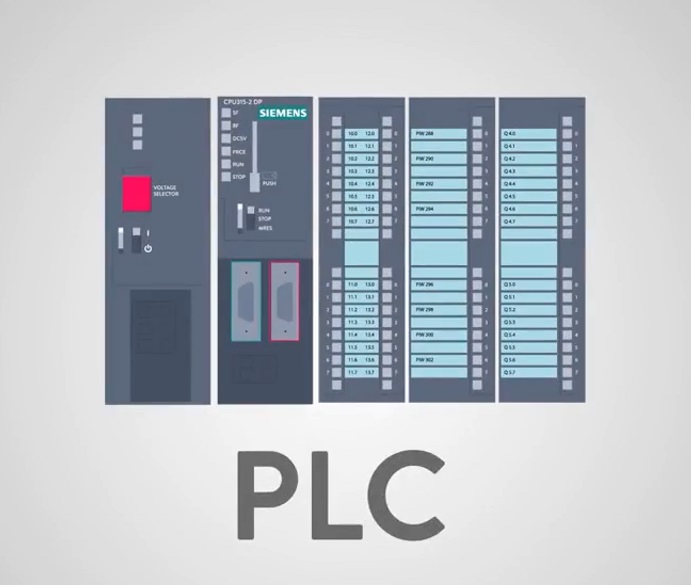
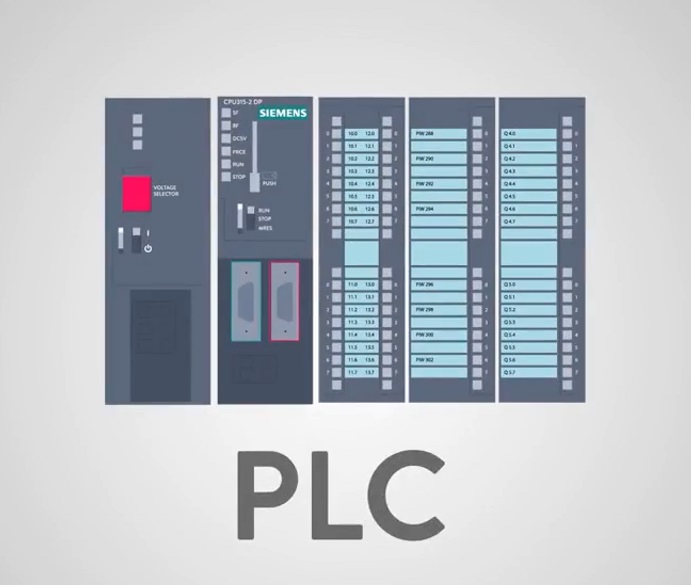
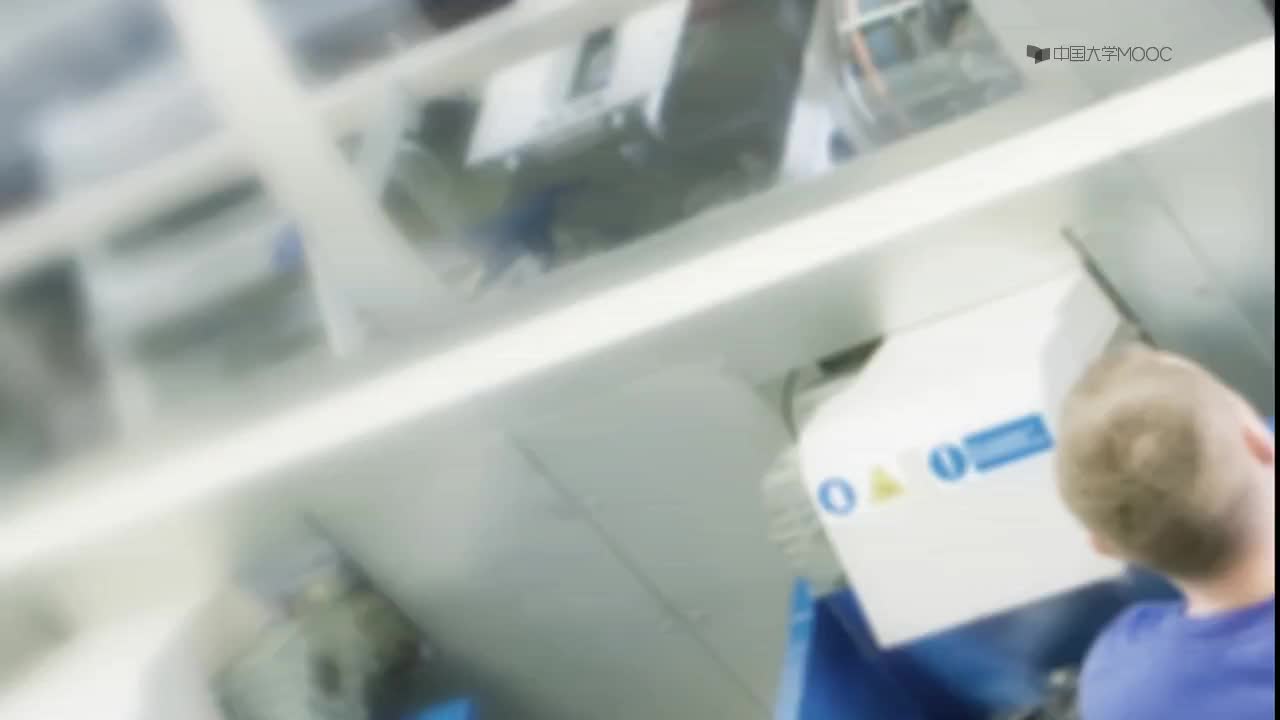
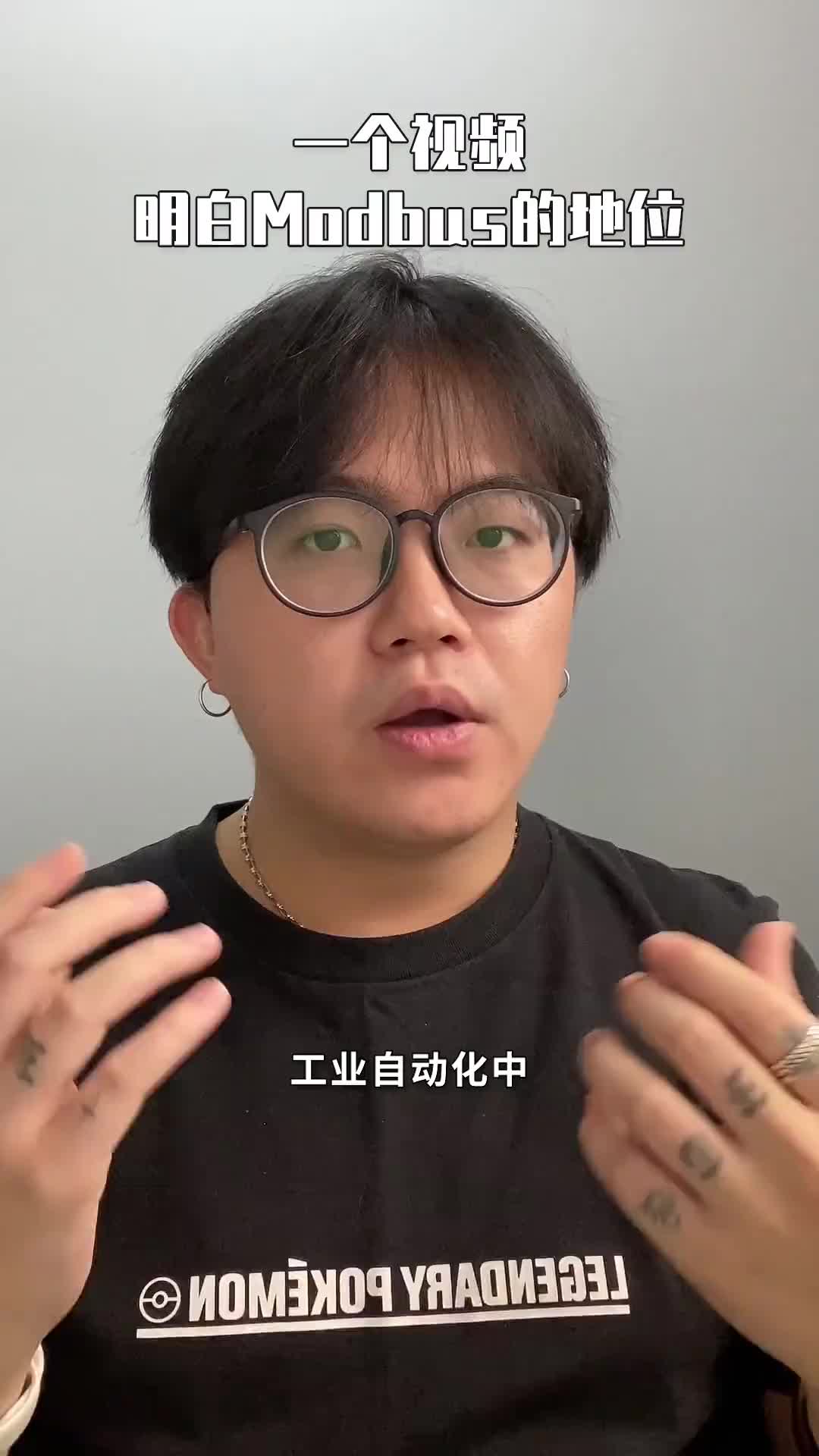
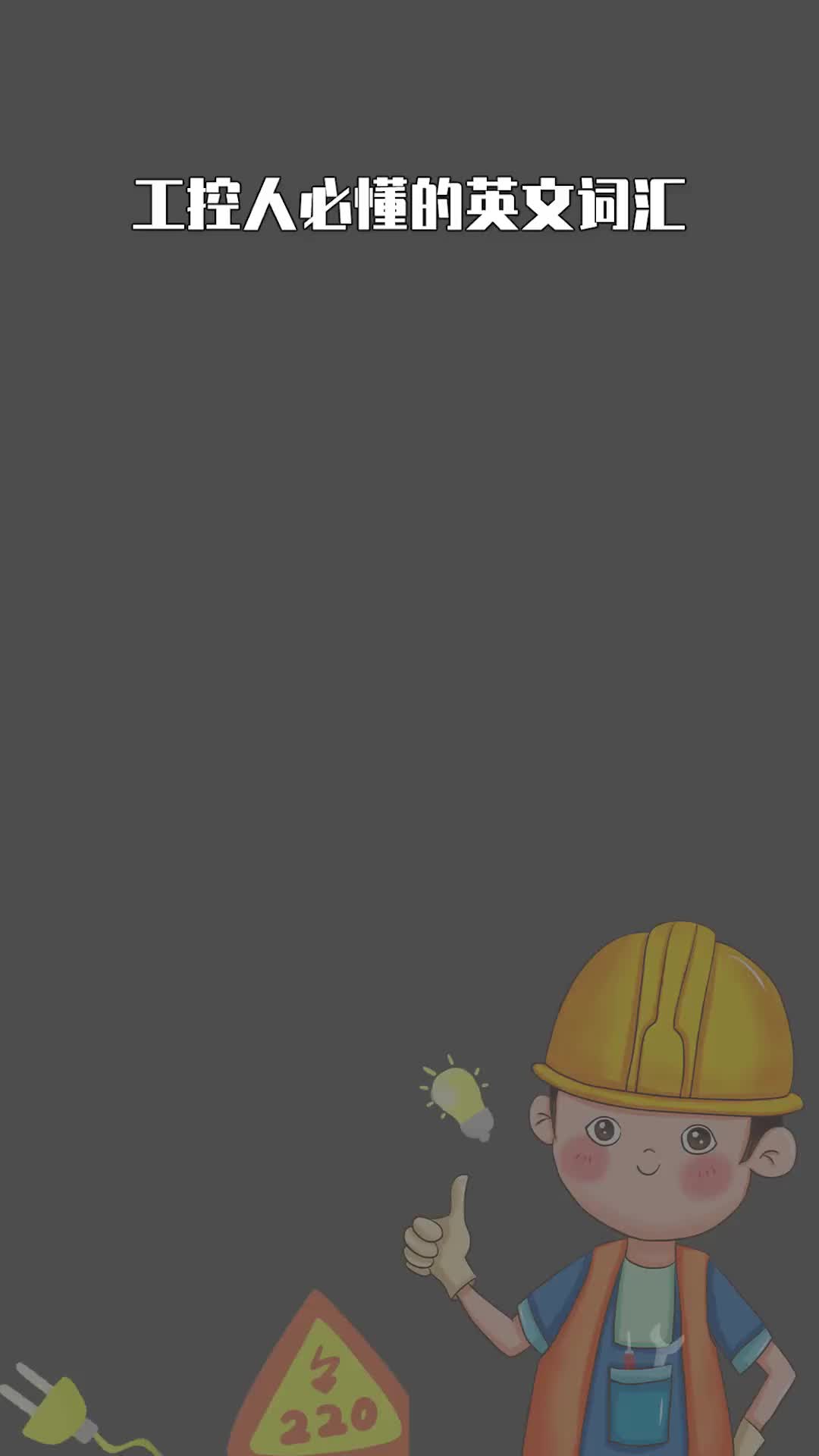
欧姆龙PLC工业控制的应用实例
从工业控制方案来分析PLC与工控机
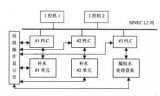
评论