换相的时机只取决于转子的位置,一种比较简单的方式是用光电编码盘充当位置传感器,这个东西在工业上用得比较多。
其次是用霍尔效应器件来充当位置传感器,其可以根据转子不同位置时的不同磁场方向分布情况,给出高电平或低电平的输出,一般在电机的不同位置上装三个霍尔传感器,就可测出转子的位置。这就是所谓的“有感无刷电机”。值得一提的是,车模和船模中的电调多是使用“有感”方式,因为其电机需要频繁启动、停止、反转,而且对整套动力系统的重量也不是十分讲究,故用有感无刷电机电调是比较合适的。无感的方式则是省去位置传感器,利用某时刻没通电的第三相的反电动势来估测转子的位置。这使整套系统分量更轻,结构更简单。其缺点在于启动比较麻烦,启动的时候可控性较差,要达到一定转速后才变得可控。
无感换相基本原理
那无感换相如何根据第三相的反电动势来估测转子的位置?如图3-1,在AB通电期间,线圈CC’的C边在图(a)中切割N极的磁力线并产生一个正向的感生电动势,在图(b)中确是切割S极的磁力线而产生一个反向的感生电动势了。C’边的情况也类似。这说明,在AB相通电期间,如果去测量线圈 CC’上的电压,会发现其间有一个从正到负的变化过程。于此类似,其余通电情况也可以用这个办法分析。
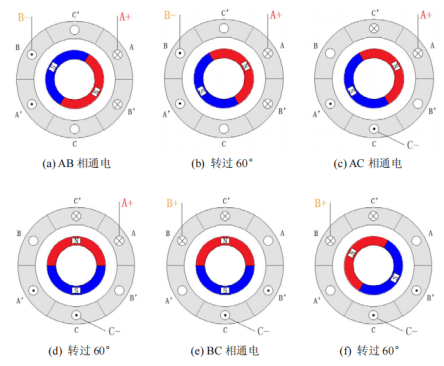
那无感换相如何根据第三相的反电动势来估测转子的位置?如图3-1,在AB通电期间,线圈CC’的C边在图(a)中切割N极的磁力线并产生一个正向的感生电动势,在图(b)中确是切割S极的磁力线而产生一个反向的感生电动势了。C’边的情况也类似。这说明,在AB相通电期间,如果去测量线圈 CC’上的电压,会发现其间有一个从正到负的变化过程。于此类似,其余通电情况也可以用这个办法分析。
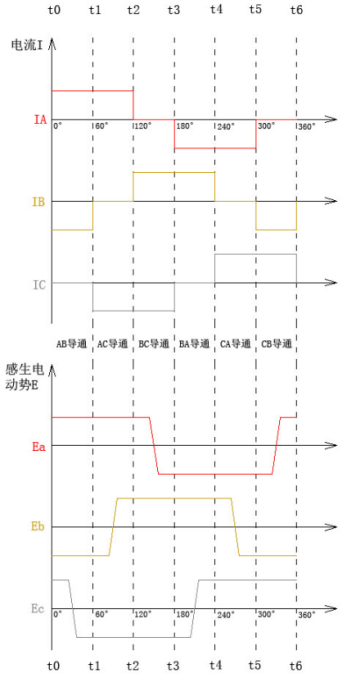
在AB相通电期间,CC’的感生电动势会整个换一个方向,也即所谓的“过零点”。在图3-2的t0时刻,为AB相通电刚开始时的情况,CC’产生的感生电动势的等效电路图如图3-3 (a)所示。而在t1时刻,为AB相通电快结束时的情况,CC’产生的感生电动势的等效电路图如图3-3(b)所示。
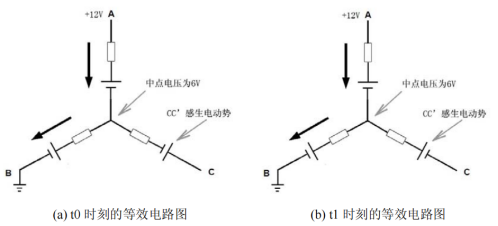
这里需要说明一下的是,在AB相通电期间,不只是线圈CC’上产生感生电动势,其实AA’和 BB’也在切割磁力线,也都会产生感生电动势,其电动势方向与外加的电源方向相反,所以叫“反向感生电动势”(BEMF)。线圈绕组AA’和BB’上产生的反电动势是很大的,两者相加几乎略小于电源电压(假设为12V)。线圈绕组本身的等效电阻很小(约0.1欧左右),如果反电动势不大的话,端电压加载在线圈绕组等效电阻上,会产生巨大的电流,线圈非烧掉不可。为方便理解,姑且假设在额定转速下AA’和BB’各产生5.7V的反电动势,那么它们串联起来就产生11.4V的反电动势,那么施加在等效电阻上的电压就为(12-11.4)=0.6V,最终通过绕组AB的电流就是0.6 /(2* 0.1)=3A。同理,由于各绕组的结构是相同的,切割磁力线的速度也是相同的,所以线圈CC’也应该会产生一个大小约为5.7V的感生电动势。由于中点电势值始终为6V,CC’的线圈产生的感生电动势只能在以中点6V电势为基准点的基础上叠加,仍旧假设在额定转速下CC’上会产生5.7V的感生电动势,那么在t0时刻,如果去测量C点的电压,其值应为6+5.7=11.7V;在t1时刻,C点的电压值应为6-5.7=0.3V。也就是说,在AB相通电期间,只要一直监测电机的C相引线的电压,一旦监测到低于中点电压,就说明转子已转过30°到达了t0和t1中间的位置,只要再等30°就可以换相了。如果电调的MCU足够快的话,可以采用连续AD采样的方式来测量C相电压,不过会浪费CPU资源,因为大部分采到的AD值都是没用的,我们只关心它什么时候低于中点电压。可以使用一个模拟比较器来监测过零信号。一旦C相输出电压低于中点电压,比较器马上可以感知并在输出端给出一个下降沿。同理,当电机处于AC相通电时,监测的是B相输出电压;当电机处于BC相通电时,监测的是A相输出电压。继续往前,当电机开始进入BA 相通电时,C相输出电压一开始会处于一个较低的状态,过零事件发生时,C相输出电压会超过中点电压,这时比较器会感知并输出一个上升沿。接下来的CA,CB相通电情况也类似,不再赘述。
延迟换相
根据前文所述知道在C相的过零点,转子只转过30°,还需要再转30°才可换相,那怎么知道转动余下的30°需要多少时间呢?一种比较简单的做法是近似认为转子转速在这 0°~60°的小范围区间内基本是恒定的:从AB相开始通电到检测出C相过零点的前半段时间,基本等于后半段的时间。所以只要使用定时器计数前半段的时间间隔T1,等过零事件出现后再等待相同的时间再换相即可。当然,更直接的方法是监测到过零点后不延迟30°,而是直接换相。这种方法当然也可行,但是会损失一点效率,且同等情况下转矩也会减小。
消磁现象
在实际换相过程中,例如AB相切换到AC相的过程中,由B相电流突然减小(不会突然消失,续流一段时间直到自身能量耗尽),其线圈的自身电感会在续流期间,成为一个电动势产生者,而且方向和原来相反,并叠加在中点之上。如图3-4,此时B端电位是高于中点电位。注意(a)图中B线圈的感生电动势是导体切割磁力线产生的,而(b)图中的续流电动势是B线圈自身的电感产生的(其大小要高于切割磁力线的感生电动势大小)。
当B线圈能量耗尽后,切割磁力线的行为再次成为主导B相感生电动势的主要因素,所以B端电位此时又会低于中点电位,这就是所谓的“消磁现象”。如图3-5即为换相时出现的消磁现象。
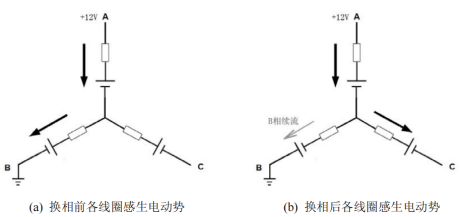
当B线圈能量耗尽后,切割磁力线的行为再次成为主导B相感生电动势的主要因素,所以B端电位此时又会低于中点电位,这就是所谓的“消磁现象”。如图3-5即为换相时出现的消磁现象。
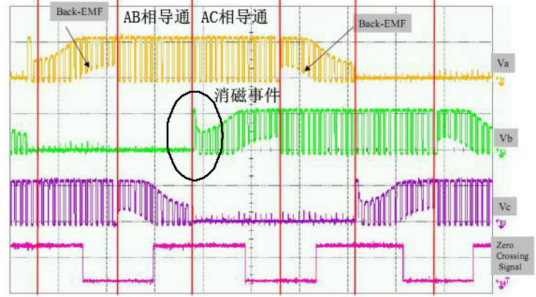
由于消磁事件的存在,B端会在AC相通电期间,产生两次上冲过零事件(也即模拟比较器会捕捉到两次过零信号),前一次是无效的,后一次才是有效的过零信号。软件上可通过以下策略滤除消磁现象的干扰,在比较器捕捉到过零信号后,检查当前距离上一次换相的时间是否大于延迟换相的时间,大于则为有效过零信号,小于则为消磁现象引发的过零。
六臂全桥MOS驱动电路
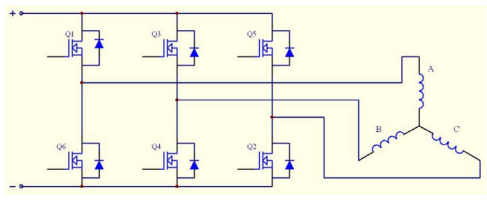
图3-6为六臂全桥MOS驱动电路简图。Q1到 Q6为功率场效应管,当需要AB相导通时,只需要打开Q1,Q4管,而使其他管保持截止。此时,电流的流经途径为:正极→Q1→线圈A→绕组B→Q4→负极。这样,六种相位导通模式:AB, AC, BC,BA,CA,CB分别对应的场效应管打开顺序为Q1Q4,Q2Q2, Q3Q2,Q3Q6,Q5Q6,Q5Q4。实际控制中,通常将上臂或者下臂常开,另一臂通入PWM信号进行控制。BLDC的调速就是用PWM信号的占空比进行调制。
反电动势过零检测电路
PHASE_A,PHASE_B,PHASE_C分别接电机的A,B,C线,经过一个分压网络后分别为NULL_A,NULL_B,NULL_C,MITTEL为估测的变形后的中点电压。只要在AB通电期间将NULL_C和MITTEL比较;AC通电期间将NULL_B和MITTLE比较;BC通电期间将NULL_A和MITTLE比较,就可以成功检测出各相的过零事件。由于这三个过零事件产生的时间不同,如果能在比较器的输入端不断地切换这三个端点电压,只要复用单个比较器就可以。
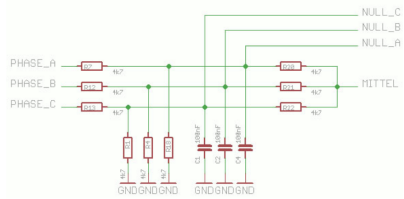
制动策略
通常利用电机自身进行快速制动有两种简单的办法,一种是能耗制动,一种是短接制动,能耗制动是把电机的动能消耗在外部制动电阻上,短接制动是把电机的动能消耗在电机的定子绕组上。显然能耗制动对于减少电机发热更加有利。
短接制动是指在刹车时能做到让电机的驱动MOS管上桥臂(或者下桥臂)全部导通而下桥臂(或者上桥臂)截止状态,电机的三相定子绕组全部被短接。处于发电状态的电机,相当于电源被短路。因为绕组的电阻比较小,所以能产生很大的短路电流,电机的动能被快速释放,从而使电机瞬时产生极大的制动力矩,能够达到快速刹车的效果。电机速度越高,短路电流越大,制动力也越大。
短接制动在广义上也是能耗制动,
只是一般的能耗制动用的外接的耗能电阻,在超大功率场合应用。中小功率都可以使用短接制动,使用Rs能耗制动。
考虑不能超过MOS管的承受能力,一般等待电机降低低速后再使用短接制动。实际设计时,考虑导通桥臂带有PWM控制,这样还可以对刹车力度进行适当调节。为了避免在电机高速时产生过大的短路电流,一般开始短接制动时PWM占空比不要超过30%。当电机速度降低为低速时,加大制动力矩,即使采用100%的占空比对于MOS管也是安全的。
其利天下驱动方案
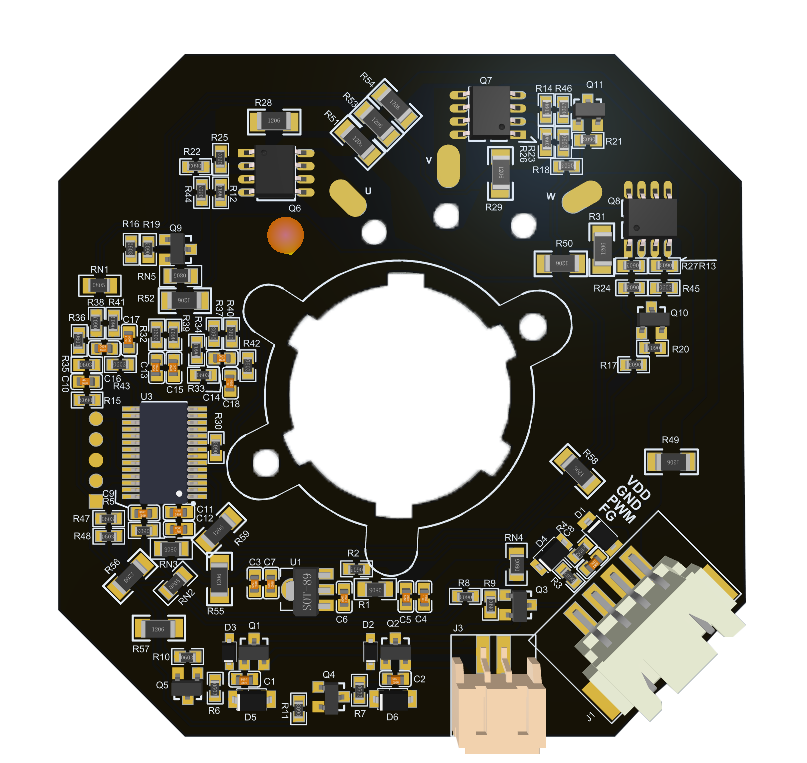
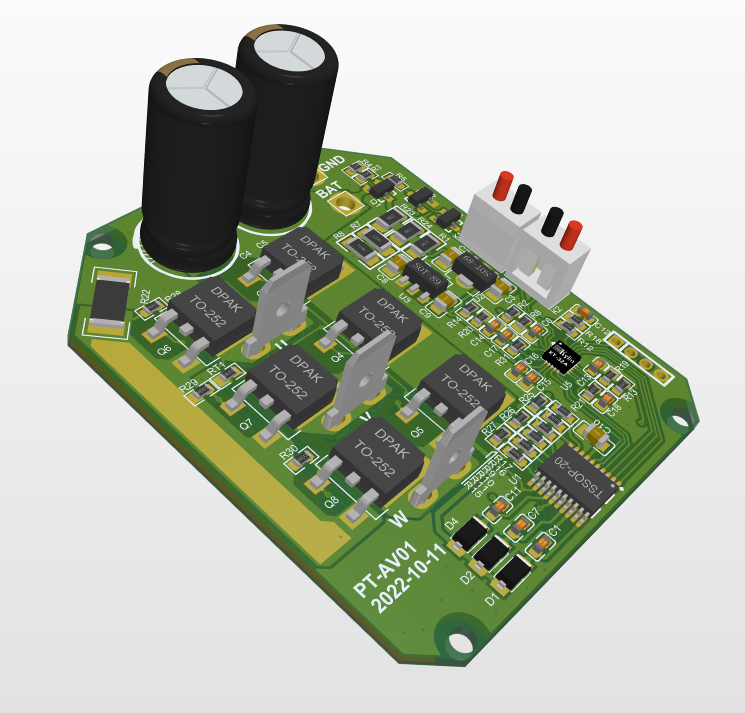
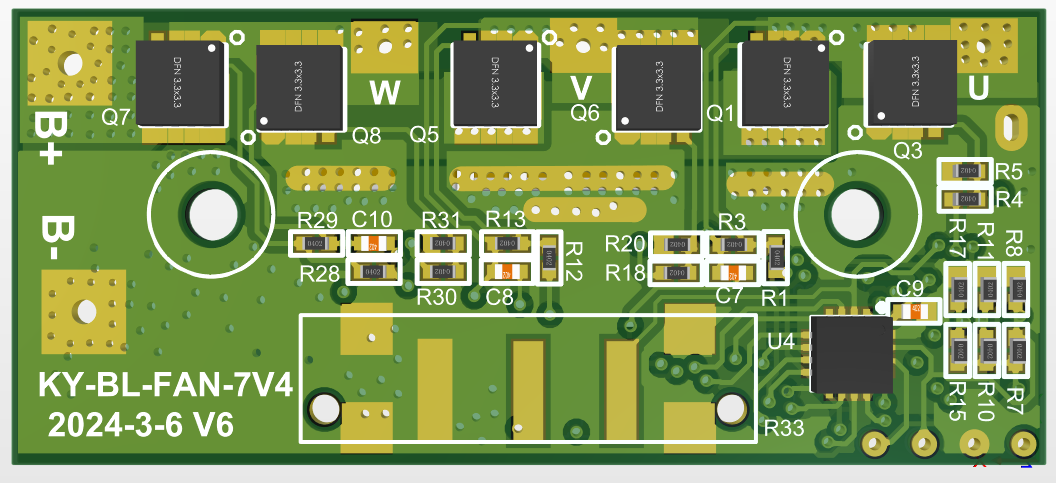
-
无刷电机
+关注
关注
58文章
854浏览量
46214 -
BLDC电机控制
+关注
关注
2文章
22浏览量
14656 -
无刷电机驱动
+关注
关注
0文章
24浏览量
2596 -
无刷电机控制
+关注
关注
0文章
8浏览量
2175
发布评论请先 登录
相关推荐
六步换相法pwm控制bldc电机,电机超过额定电压控制的原因?
如何实现直流无刷电机中的换相
采用六步换相法驱动无刷直流电机,最高速度只有电机额定速度的一半
基于FOC无刷电机的按摩器方案以及PCBA介绍【其利天下技术开发有限公司】
无刷电机无感六步方波驱动原理及过零现象产生分析
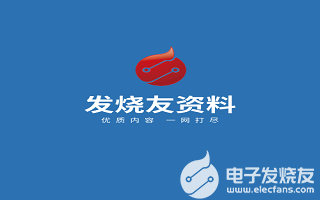
评论