一、引言
银及其合金在电子、电力、航空航天等众多领域具有广泛应用。为了提高银材料的物理和机械性能,常采用烧结工艺进行材料制备。烧结工艺根据施加压力的不同,可分为无压烧结和有压烧结两种。本文旨在详细探讨无压烧结银与有压烧结银工艺流程的区别,并分析各自的特点和适用场景。
二、无压烧结银工艺流程
无压烧结,即在烧结过程中不施加外部压力,通过粉末颗粒间的自有力和热运动实现致密化。无压烧结银的工艺流程主要包括以下几个步骤:
粉末制备:采用雾化、还原、电解等方法制备银粉末。粉末的粒度、形貌和纯度对烧结体的性能有重要影响。
粉末混合:将银粉末与添加剂(如烧结助剂、增韧相等)按一定比例混合均匀。混合过程需避免粉末的氧化和污染。
成型:将混合后的粉末填充到模具中,通过冷压、等静压等方式进行预成型。预成型坯体的密度和均匀性对烧结体的最终性能有直接影响。
烧结:将预成型坯体置于烧结炉中,在无压或微压环境下进行加热。烧结温度、时间和气氛需根据银粉末的特性和产品要求进行精确控制。在烧结过程中,粉末颗粒间发生扩散、熔合等物理化学变化,形成具有一定强度和致密度的烧结体。
后处理:烧结后的银制品可能需要进行热处理、机械加工、表面处理等后处理工艺,以进一步提高其性能或满足特定应用需求。
三、有压烧结银工艺流程
有压烧结,即在烧结过程中施加外部压力,以促进粉末颗粒的致密化和形状保持。有压烧结银的工艺流程与无压烧结相似,但在烧结环节存在显著差异。以下是有压烧结银的关键步骤:
粉末制备和混合:与无压烧结相同,有压烧结银也需要进行粉末制备和混合。粉末的特性和混合均匀性对烧结体的性能同样至关重要。
成型:有压烧结银的成型过程通常与烧结过程相结合,即在加热的同时施加压力。这种热压成型的方法有助于提高坯体的密度和均匀性。
热压烧结:将混合后的粉末置于热压模具中,在加热的同时施加单向或双向压力。热压烧结的温度、压力和时间需根据银粉末的特性和产品要求进行精确控制。在热压烧结过程中,粉末颗粒在压力和热力的共同作用下发生塑性变形、扩散和熔合等致密化机制,形成高密度和良好机械性能的烧结体。
后处理:热压烧结后的银制品可能需要进行与无压烧结相似的后处理工艺,如热处理、机械加工和表面处理等。
四、无压烧结与有压烧结的区别分析
致密化机制:无压烧结主要依靠粉末颗粒间的自有力和热运动实现致密化,而有压烧结则通过外部施加的压力和热力共同作用促进致密化。因此,有压烧结通常能够获得更高密度的烧结体。
烧结温度和时间:由于有压烧结在加压的同时进行加热,粉末颗粒间的接触和扩散过程得到加强,因此可以在较低的温度和较短的时间内实现致密化。相比之下,无压烧结通常需要更高的温度和更长的时间。
产品性能:由于有压烧结能够获得更高密度的烧结体,并且烧结过程中颗粒间的结合更加紧密,因此有压烧结银制品通常具有更优异的机械性能和电性能。然而,无压烧结在制备复杂形状和大型构件时具有更高的灵活性。
设备成本:有压烧结设备通常比无压烧结设备更复杂、更昂贵,因为需要额外的加压系统和模具。此外,有压烧结过程中的压力控制也对设备提出了更高的要求。
五、结论与展望
无压烧结银和有压烧结银作为两种重要的粉末冶金工艺,在银材料制备领域具有广泛应用。无压烧结具有工艺流程简单、成本低廉、适用于制备复杂形状和大型构件等优点;而有压烧结则能够获得更高密度和更优异性能的烧结体。在实际应用中,应根据产品要求、生产成本和设备条件等因素综合考虑选择合适的烧结工艺。
随着科技的进步和粉末冶金技术的发展,未来无压烧结和有压烧结银工艺将不断改进和优化。例如,通过粉末制备技术的创新,可以获得更细、更均匀、更高纯度的银粉末;通过烧结工艺参数的精确控制和智能化管理,可以实现更高效、更节能、更环保的生产过程;通过新材料的设计和复合化技术的应用,可以开发出具有更高性能、更广泛应用领域的银基复合材料。这些发展将为银材料的制备和应用提供更广阔的空间和机遇。
-
设备
+关注
关注
2文章
4540浏览量
70840 -
烧结
+关注
关注
0文章
16浏览量
7039 -
烧结工艺
+关注
关注
0文章
5浏览量
1007
发布评论请先 登录
相关推荐
AlwayStone AS9375是一款使用了银烧结技术的无压纳米银
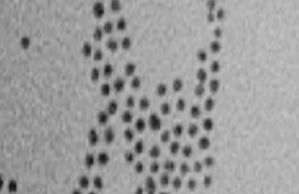
评论