在电力电子领域,面临的挑战是如何在更小的设备中实现更高的功率传输并降低成本。这些目标往往相互矛盾,导致必须做出妥协。更高的电流会导致器件内部的热应力增加,从而缩短其使用寿命。
为了解决这个问题,可以考虑使用损耗更低的解决方案,比如用SiC-MOSFET替代IGBT。不过,这样的解决方案会更昂贵。另一种方法是改善冷却效果,但绝缘基材在热传导上存在物理限制,而解决办法就是放弃绝缘要求。
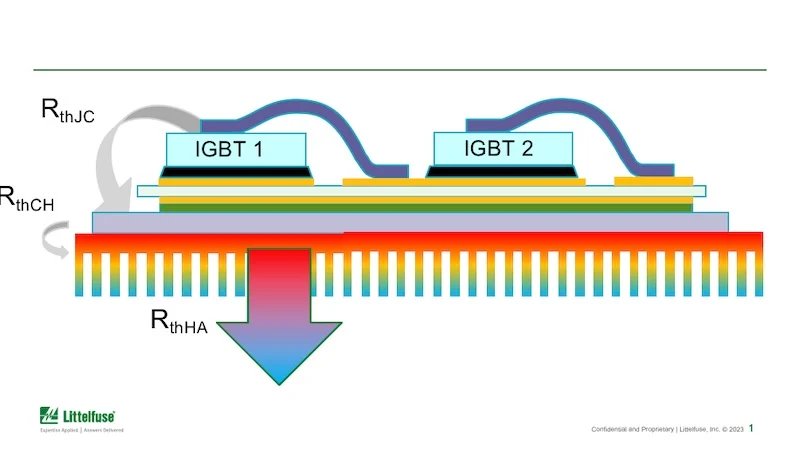
半导体模块的比较
最常见的半导体模块采用直接铜结合基材(DCB)和绝缘陶瓷层。这种设置可以承载多个芯片,通过对上层铜层的结构设计,可以处理不同的电位。图1示意性地描绘了这种方法。
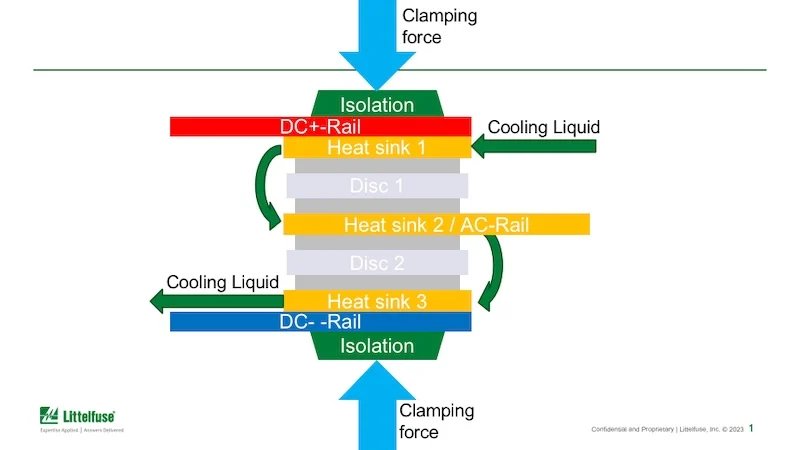
相比之下,高功率碟形器件通常与电活性冷却板结合,如图2所示。在图1所示的设置中,陶瓷层提供了主导的热阻。高性能陶瓷如氮化铝(AlN)具有高达180 W/(mK)的导热性。然而,为了达到所需的绝缘效果,所需的厚度导致了较大的热阻。图2中的设置改善了热性能,因为在功率半导体与散热器之间不涉及电绝缘。因此,必须使用电绝缘的冷却液,如去离子水/防冻液混合物,并且其绝缘特性必须进行监测和维护。
消除热阻
为了消除DCB的主导热阻,采用了一种方法,将IGBT芯片直接焊接到一个适合的液体冷却板上,该冷却板尺寸为40 x 80 mm²。这样,冷却板就成为了IGBT集电极的电连接。DCB基材则用于在发射极和控制端子侧安装功率端子。为了克服连接线带来的限制,基于不同装配技术构建了一个测试样件。
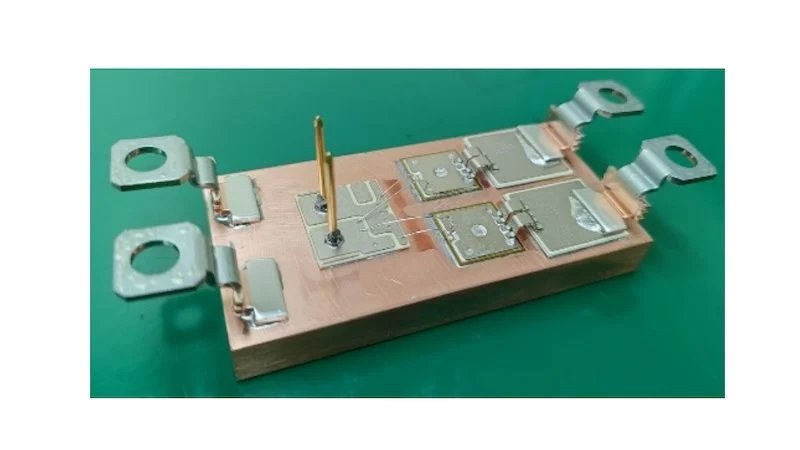
在这里,使用了一种具有可焊接前面金属化的不同芯片。连接线被用焊接到IGBT前面的连接夹替代。由于夹子无法直接焊接在芯片上,因此首先将接口垫焊接到IGBT上。图3展示了得到的测试样件。
进行了基于红外相机的测量,结果显示每个芯片可承载200 A的电流,如图4所示。
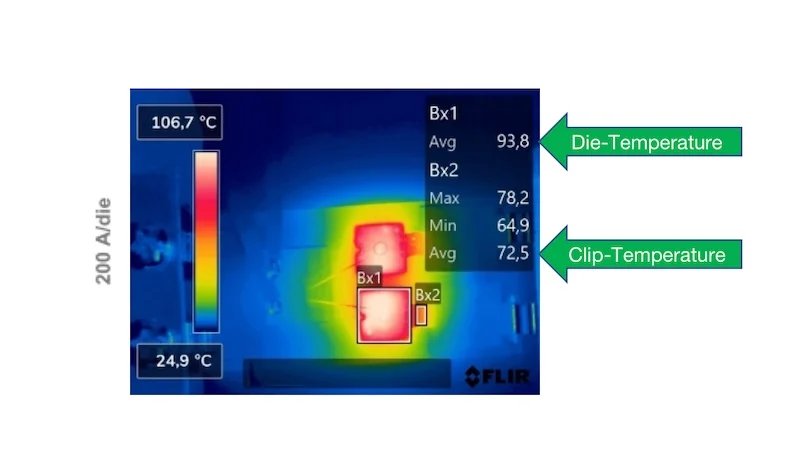
通过使用连接线所施加的任何限制已被消除。在超过连接线能够承受的电流密度下,夹子的温度保持在100°C以下。
本研究使用了一种额定电流为150A的标准芯片。今天的工业边界条件包括最大入口温度为65°C,最大芯片温度为175°C。测量结果显示该设置能够从芯片散发出最多380W/cm²的功率损耗密度。值得注意的是,额定150A的芯片在处理200 A时仍然在其热限制范围内。对于目标热条件和65°C的入口温度,最大结温Tvj=175°C在250 A时达到。
电气测试
尽管研究重点关注热性能,但基本的电气行为也进行了测试。双脉冲测试的结果总结在图5中。
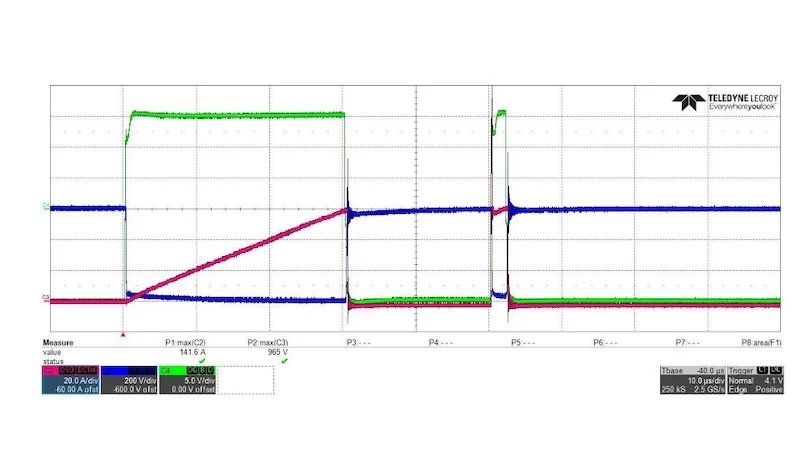
测试显示开关干净,但由于测试设置的性质,没有进一步调查的细节。虽然所研究设备的布局未针对开关进行优化,也未期待完美的开关行为,但结果仍然足够好,可以转化为潜在的系列开发。
循环负载测试
卓越的热性能是延长电力电子元件使用寿命的关键因素。在第二种设计中,几个设备按照IEC 60749定义进行了功率循环测试(PCsec)。
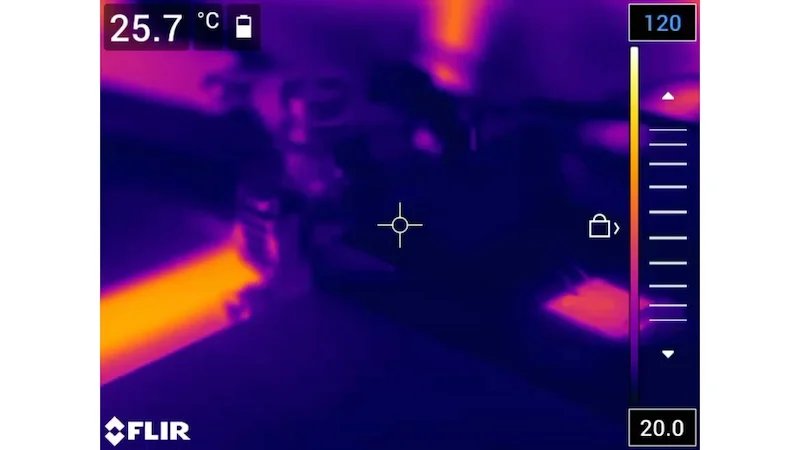
预期的是,垫片和夹子组合的寿命会高于使用连接线的系统,因为连接线的失效机制如连接剥离和连接脚裂纹被消除。然而,由于垫片焊接在芯片的前面,这一接口的剥离最终是不可避免的。测试在12°C的入口温度下进行。在一个4秒的周期内,负载电流为250 A,观察到芯片温度的波动为90 K。图6显示了卓越的热性能和冷却板内部的低热扩散。
需要注意的是,此测试中的IGBT额定芯片电流仅为150 A。因此,尽管在给定的芯片温度热限制内,芯片的工作电流远超现实应用中的参数。
此测试的寿命终止标准是在前向电压上升5%。这个值在大约145,000个循环后到达。而在这些条件下,传统的焊接技术约达到80,000个循环。考虑到芯片金属化、焊料合金和焊接工艺的进一步改进,达到至少两倍于焊接连接设备的功率循环能力似乎是合理的。
潜在应用及其带来的好处
所选结构及其实现的功率密度表明,这种设计旨在用于高功率应用。已经具备液体冷却并要求高功率传输的应用,特别可以受益于绝缘功率半导体配置。
这种方法针对风力发电的可再生能源生成或通过感应加热进行金属焊接。由于散热器与IGBT的集电极形成连接,这种方案非常适合构建具有高电流承载能力的单开关,如图8所示。
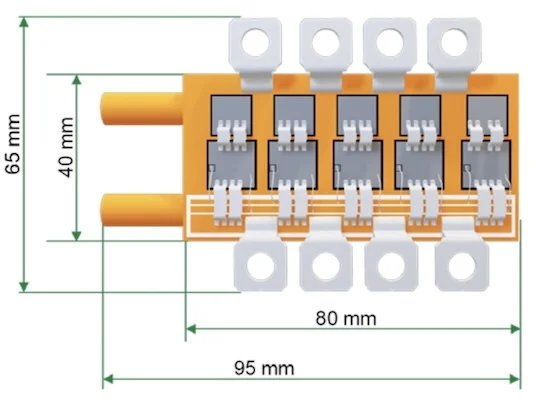
该版本配备250 A芯片组,类似于一个额定1200 A的单开关,体积为123.5 cm³。
由两个这样的器件构成的半桥大约占用250 cm³的空间。相比之下,当前使用的高功率模块最多需要700 cm³。
集成液体冷却的另一个好处是,所需的外壳不再承受电力半导体常见的高温。这为使用低档塑料,甚至是易于回收的材料打开了道路,这将在未来几年成为重要课题。
就资源使用而言,由图8中的设备构建的半桥质量低于0.7 kg,低于当前设计的一半。
通过用铝替代铜散热器,牺牲部分性能可实现成本和重量的减少。
高效的冷却也是充分发挥具有非常高去饱和极限IGBT能力的关键。前向电压、开关性能和短路鲁棒性构成了IGBT技术优化的限制三角形。低开关损耗的芯片往往具有更高的前向电压,反之亦然,只要短路能力不受影响。图9反映了优化为低前向电压的IGBT的前向电压。
这个额定电压为1200 V、额定电流为200 A的芯片在该工作点上产生240 W的损耗。尽管该芯片可以轻松承受高达450 A的电流,但损耗会增至720 W,或者在这种情况下为360 W/cm²。
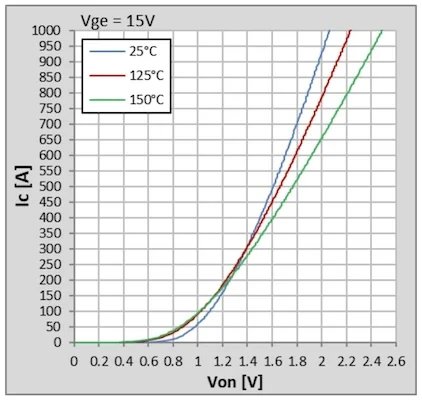
在使用陶瓷绝缘材料的组件中,这种功率损耗密度会导致芯片温度过高,即使安装了高性能陶瓷也不例外。
通过直接液体冷却的方法,已实现高达380 W/cm²的功率密度,使芯片在该工作点下能够正常工作而不超过其热限制。
因此,图8中的设备能够承载超过2 kA的电流,可能接近所用端子的可容忍电流密度极限。
推动电力半导体功率密度的极限
由于绝缘要求,当前电力半导体的功率密度提升存在物理限制。为了突破这些限制,必须识别出更有效地从电力半导体中提取热量的新方法。一种方法是结合适合的芯片和互连技术的直接液体冷却。这种从传统绝缘组件转向非绝缘组件的转变,为提升功率密度提供了十倍的可能性。
这不仅限于IGBT技术,也可以同样转移到宽禁带半导体上。
-
SiC
+关注
关注
29文章
2819浏览量
62660 -
功率半导体
+关注
关注
22文章
1157浏览量
42987 -
半导体器件
+关注
关注
12文章
752浏览量
32053
发布评论请先 登录
相关推荐
功率半导体器件的定义及分类
什么是基于SiC和GaN的功率半导体器件?
功率半导体器件的直接均流技术的解析
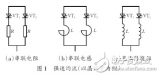
浅谈功率半导体器件与普通半导体器件的区别
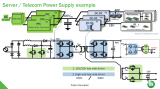
评论