SIS(安全仪表系统,Safety Instrumented System)和DCS(分布式控制系统,Distributed Control System)在工业生产过程中各自扮演着重要角色,它们之间存在明显的区别,主要体现在以下几个方面:
一、功能与应用领域
SIS系统:
主要功能:专门用于保护工业过程和设施的安全,通过监测潜在危险的过程状态,并采取措施使其保持在安全的操作范围内,或在必要时关闭危险的过程或设备。
应用领域:广泛应用于石油、天然气、化学、制药、发电、冶金等行业,用于保护工艺设备、储存设施和管道系统等,确保人员、资产和环境的安全。
DCS系统:
主要功能:用于过程连续测量、常规控制(连续、顺序、间歇等)、操作控制管理,保证生产装置平稳运行。
应用领域:特别适合需要复杂过程控制和实时数据监控的应用场景,如化工、石油、冶金、能源和水处理等行业。
二、系统特性
SIS系统:
安全性与可靠性:SIS系统在设计、制造和维护过程中都经过严格的测试和质量控制,具有高安全性和可靠性。它通常采用冗余设计,以提高系统的可靠性和可用性。
独立性:SIS系统通常与工艺控制系统(PCS)或其他控制系统保持独立,以避免互相干扰,并确保在紧急情况下能够独立采取行动。
静态性:在正常工况下,SIS系统始终监视装置的运行,系统输出不变,对生产过程不产生影响;在异常工况下,它将按照预先设计的策略进行逻辑运算,使生产装置安全停车。
DCS系统:
动态性:DCS系统是动态系统,始终对过程变量进行连续监测、运算和控制,对生产过程进行动态控制,确保产品质量和产量。
灵活性与扩展性:DCS系统可以根据需求扩展系统的功能和规模,支持多种类型的输入输出模块和通信协议。
实时监控与集成性:DCS系统能够实时采集、监测和控制过程数据,并将控制、监控、数据采集和报警等功能集成在一个统一的平台上。
三、系统组成
SIS系统:
主要由传感器、逻辑解算器和最终单元三部分组成。
传感器用于检测过程变量,逻辑解算器根据预设的逻辑进行运算处理,最终单元则执行控制动作,如关闭阀门、启动停机程序等。
DCS系统:
一般由人机界面操作站、通信总线及现场控制站组成。
人机界面操作站提供操作员与系统交互的界面,允许操作员监视过程状态、调整参数和查看报警信息。
现场控制站负责接收来自传感器的信号,并进行初步处理和控制。
四、维护与管理
SIS系统:
维修时间非常关键,因为SIS系统的离线运行可能导致生产装置失去安全保护屏障。
需要定期进行测试和维护,以确保其功能的可靠性和有效性。
DCS系统:
对维修时间的长短和要求不算苛刻,可进行手动/自动切换。
通过实时监控和故障诊断功能,可以及时发现并解决潜在问题。
综上所述,SIS和DCS在功能、特性、组成以及维护管理等方面都存在显著差异。在工业生产过程中,它们各自发挥着不可或缺的作用,共同保障生产装置的安全、稳定运行。
-
DCS
+关注
关注
20文章
616浏览量
50686 -
sis
+关注
关注
1文章
29浏览量
16618 -
分布式控制系统
+关注
关注
0文章
16浏览量
6341 -
安全仪表系统
+关注
关注
0文章
5浏览量
1010
发布评论请先 登录
相关推荐
DCS PLC区别;PLC常见的六大应用
DCS与PLC的区别和共性
DCS与PLC的区别要点
基于Fluke测试仪对BPCS及SIS的维护
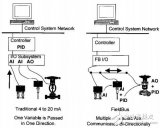
电气仪表的8个要点包括:SIS与ESD、DCS、PLC的区别仪表的“线制”等
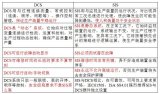
浅谈DCS与PLC之间的区别
使用最简单基础介绍DCS和PLC区别和应用
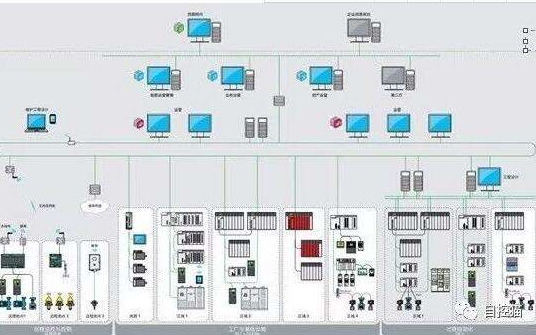
ESD和SIS之间有何区别 安全联锁系统组成元件的设计原则
浅谈DCS、SIS和 MIS定义和分工
DCS、PLC、SIS、GDS系统在氯碱和聚氯乙烯行业的应用
基于飞腾 CPU 的首个全国产 DCS/DEH+SIS 智慧电厂建成投运!
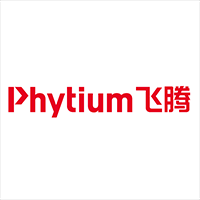
dcs和sis可以共用仪表吗
SIS联锁和DCS联锁有什么区别?
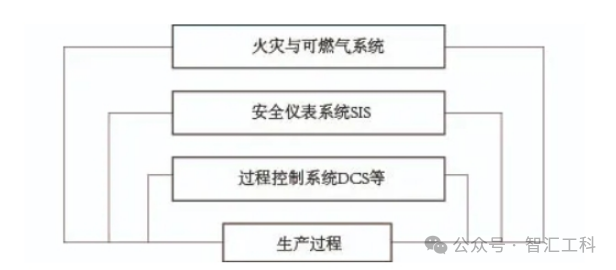
评论