在现代制造工业中,随着精密铸件的复杂性和精度要求不断提升,行业对先进的质量控制手段的需求也越来越强烈。激光三维扫描技术凭借其高精度、非接触和高效的数据采集能力,正成为业界实现质量提升和成本控制的重要手段。
01 项目背景
本案例中的客户专业从事传统汽车、新能源汽车、通信、光伏储能、逆变器、轨道交通、医疗航空及通用工业零部件铝合金压铸和精密加工。公司以技术引领生产,以“高品质”为定位,注重产品质量与研发,凭借着近二十年的行业经验和技术,在模具设计与制造、压铸工艺、半固态轻量化新工艺、精密数控加工技术等领域拥有多项专利和创新工艺。
项目中客户需要测量的是汽车变速箱壳体表面三维数据,并进行加工余量分析。变速箱壳体是支撑和固定变速箱内部齿轮、轴承和其他零部件的重要部件,在车辆的动力传动系统中起到了关键的保护作用。
变速箱内部有许多精密的齿轮、轴承和其他机械部件,壳体内外表面和安装孔位的几何公差会影响变速箱内部零部件装配准确性,导致装配偏差或部件磨损,因此需要严格把控变速箱壳体的加工精度。此外,变速箱壳体在车辆运行过程中承受较大的负载和应力,需要通过质量检测识别表面缺陷,保证其在实际工作中的使用寿命和可靠性能。
02 客户需求及痛点
客户要求完成以下测量:1.全尺寸检测:测量表面全尺寸三维数据,确保其符合设计规范;2.孔径检测:测量孔的直径,尤其是用于轴和轴承的孔,以确保其在公差范围内;3.加工余量检测:确保足够的加工余量,保证后续精加工质量。
变速箱壳体铸件几何形状特征较为复杂,包含较多曲面、深腔、圆角、倒角及不规则型面,这给测量工作带来了挑战,客户以往在测量室进行测量,存在较多不足之处:
1. 工件的深腔和死角结构较多,以往的测量手段只能获取部分关键点的数据,无法完整采集表面数据。
2. 测量室测量复杂繁琐,效率低下,且无法对检测结果进行直观全面的量化评估并生成余量分析报告,容易导致加工材料浪费,增加后续余量加工时间和成本。
03 解决方案及优势
为了应对以上挑战,客户最终使用了思看科技SIMSCAN 42掌上三维扫描仪,该设备对于狭窄空间及死角处扫描的优势十分显著,是测量深腔铸件的理想选择,大大提高了检测效率。
检测过程:
1. 扫描:利用扫描仪全方位、多角度扫描壳体表面,确保表面特征均能被捕捉到。
一边扫描,一边实时生成高精度点云数据,设备体积小巧,便于进入深腔内部扫描,其超短相机基线可以轻松获取狭缝及死角区域的三维数据,不遗漏细节之处,使得扫描数据更完整。
扫描过程非常高效,SIMSCAN 42以280万次测量/秒的点云采集速率,仅需5分钟即可完成扫描。
2. 三维建模:将点云数据进行简单的处理,如拟合、拼接,最终转化为实物的高精度三维模型。
设备精度高达0.020mm,对于腔体孔位、圆角及微小表面细节,均能精准还原。
3. 数据分析:借助专业软件将实物模型与原始数模进行对比,生成详细的色谱偏差图,便于直观地获取表面及关键部位尺寸偏差信息。
4. 余量检测:通过分析比对,确定加工余量,如果表面铸件出现较大偏差或余量不足,则可以辅助工作人员进一步优化或调整加工工艺,确保成品符合设计要求及质量标准。
5. 数字化存档:将所有的点云数据、分析报告进行数字化存档,作为制造过程各阶段状况的数字记录,以便后续质量追踪和管理。这些数据还可以作为产品质量的参考,为后续批次的生产及质量控制提供依据,确保产品的可追溯性。
04 项目小结
借助SIMSCAN对汽车发动机变速箱壳体深腔铸件进行了全尺寸及余量检测。针对死角多、结构复杂的腔体结构,SIMSCAN在整个检测过程中展现出了显著的性能优势,凭借非接触、小巧便携、高精度等特征,有效提升了检测效率和加工精度,极大程度简化了生产工艺流程,为客户提供更加全面、更有效率、更具性价比的检测方案,助力客户迈向高质量、智能化、数字化生产转型之路。
审核编辑 黄宇
-
变速箱
+关注
关注
4文章
171浏览量
18837 -
3D扫描
+关注
关注
2文章
103浏览量
21736
发布评论请先 登录
相关推荐
自带尺寸标注的3D预览为制造商组件提供更强劲的客户体验
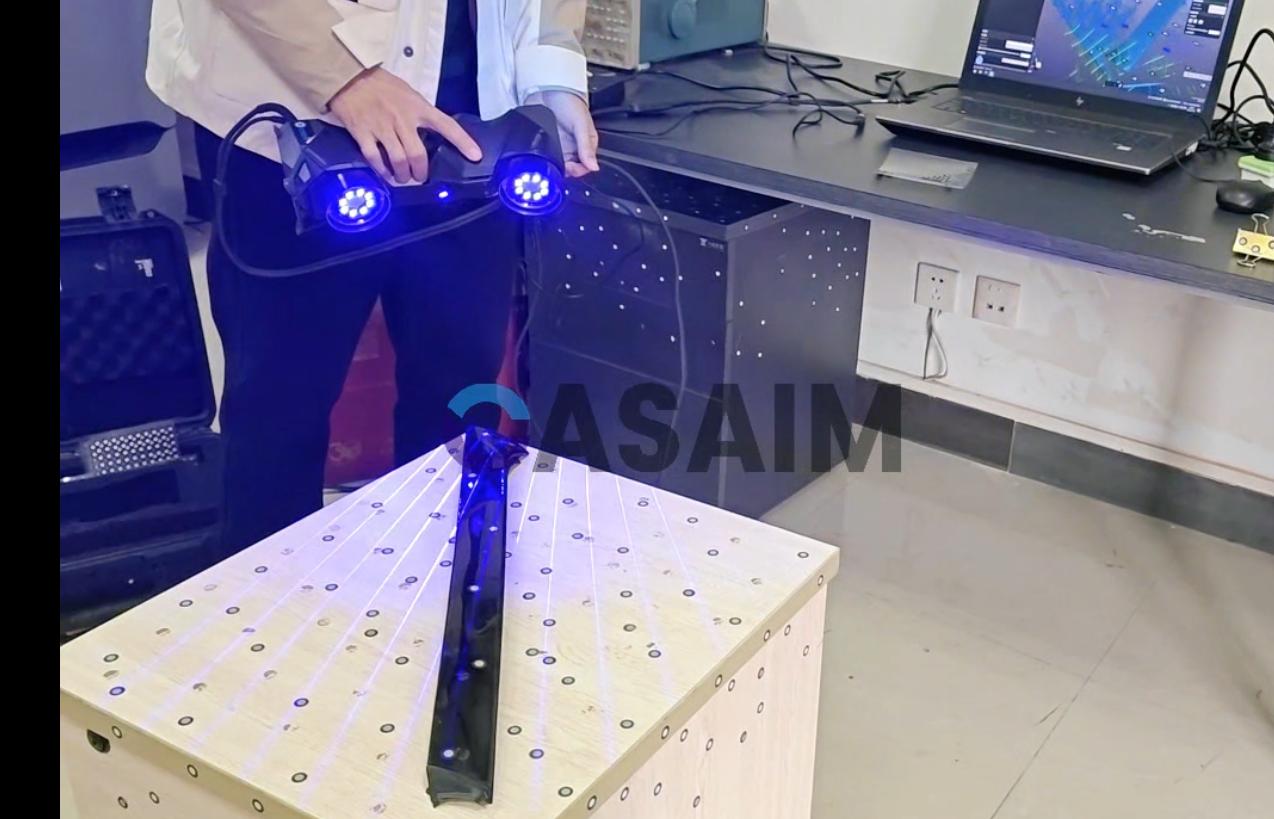
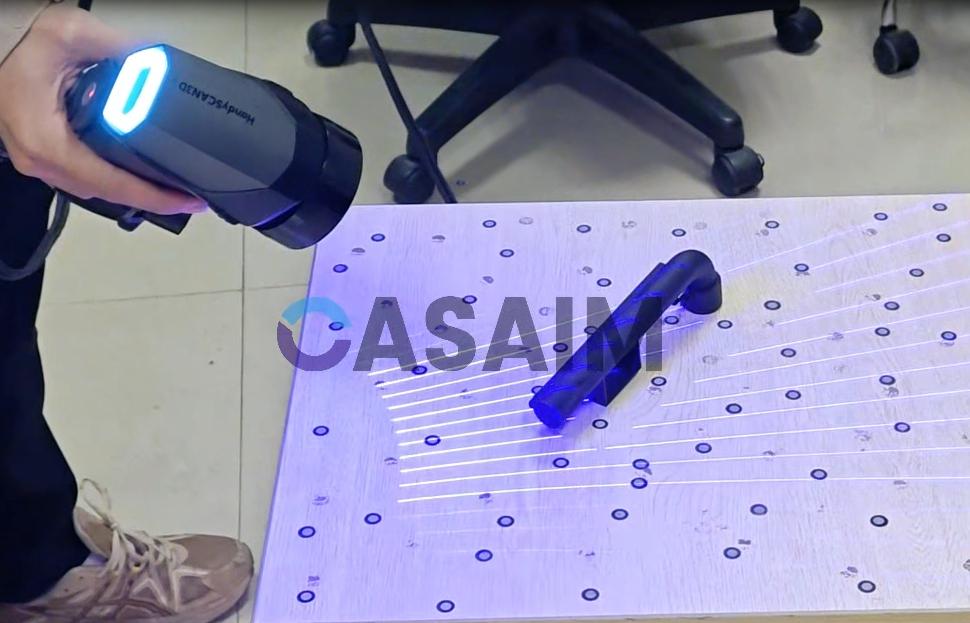
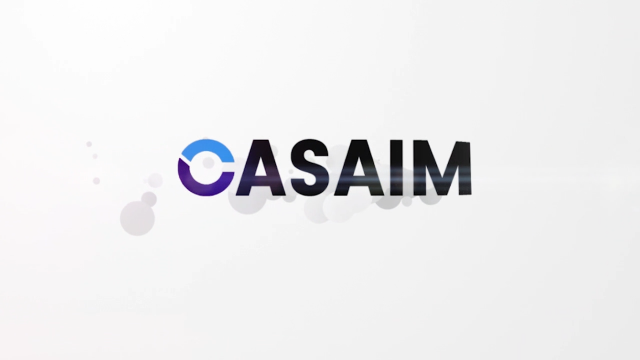
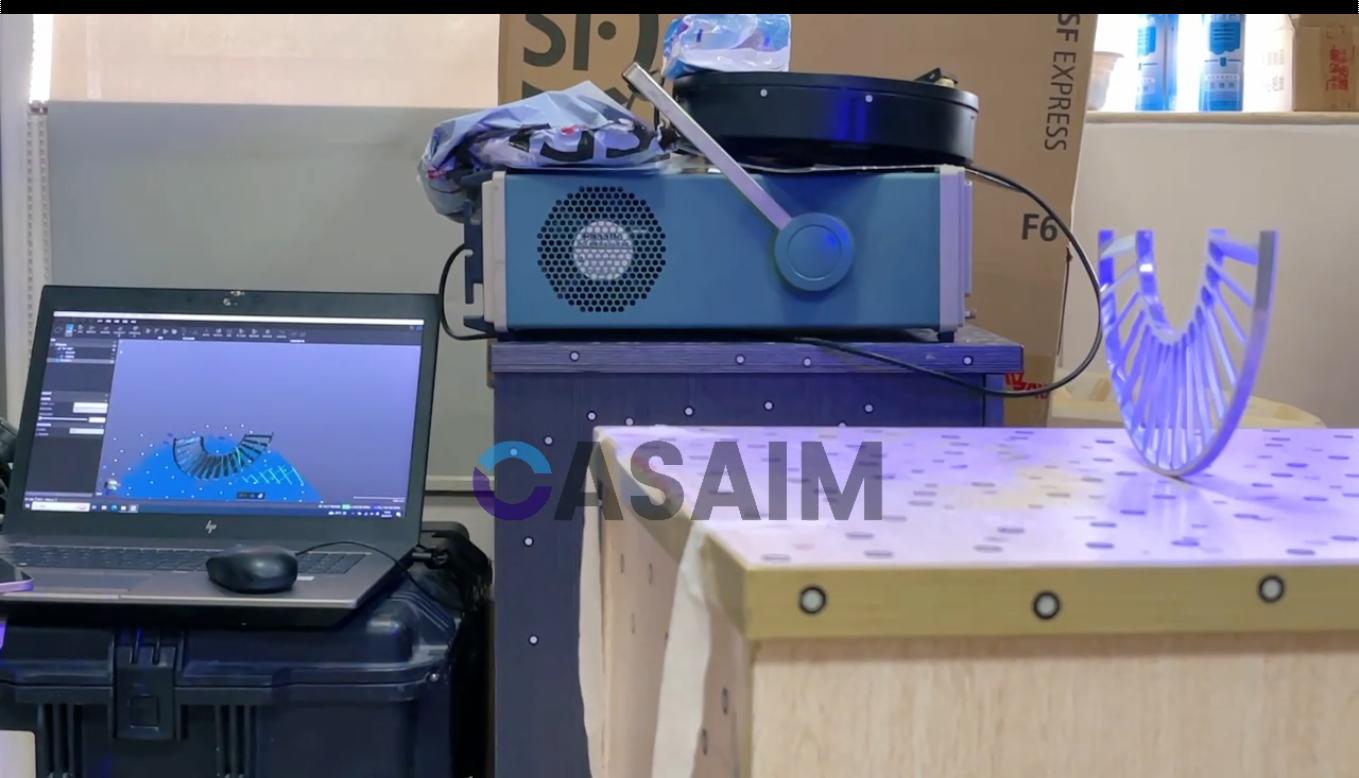
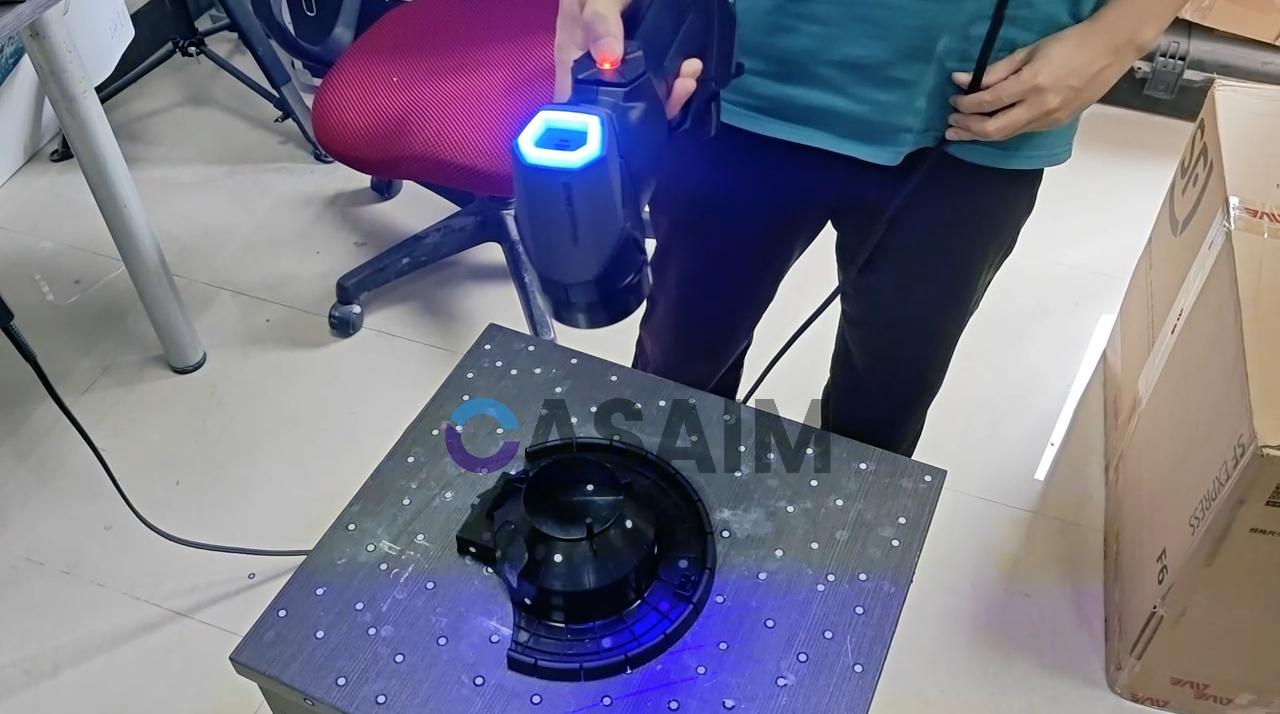
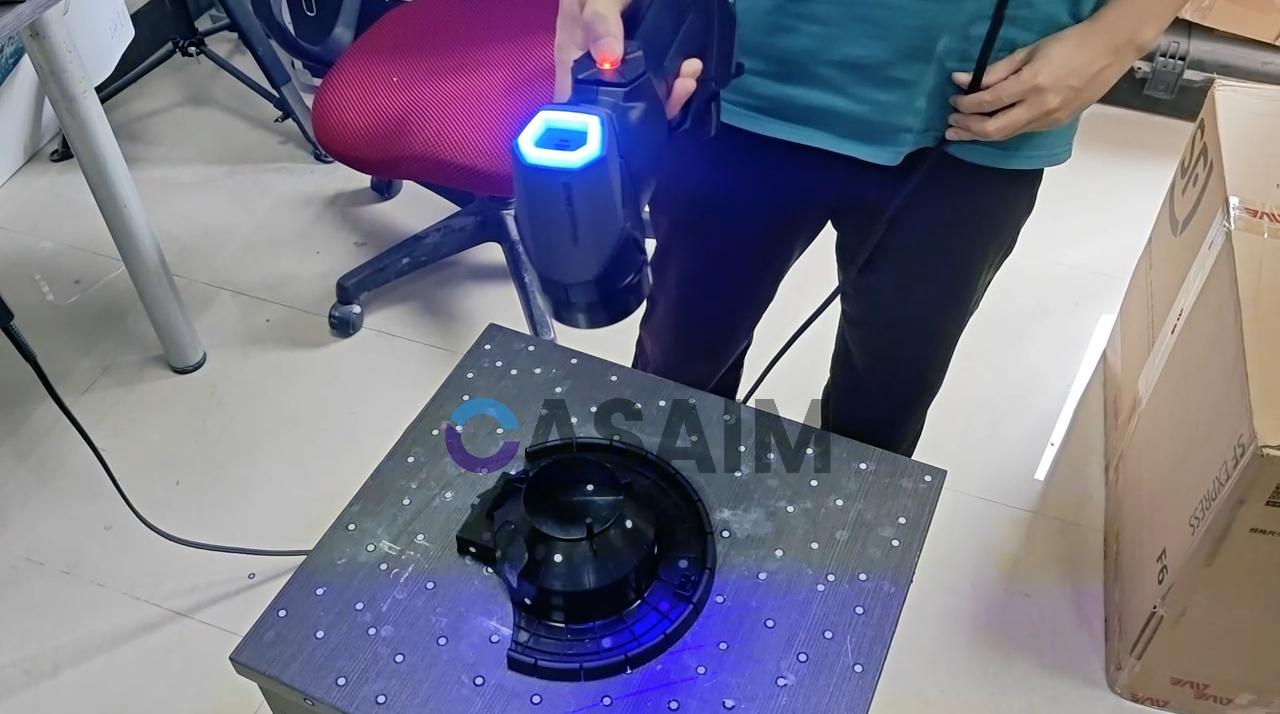
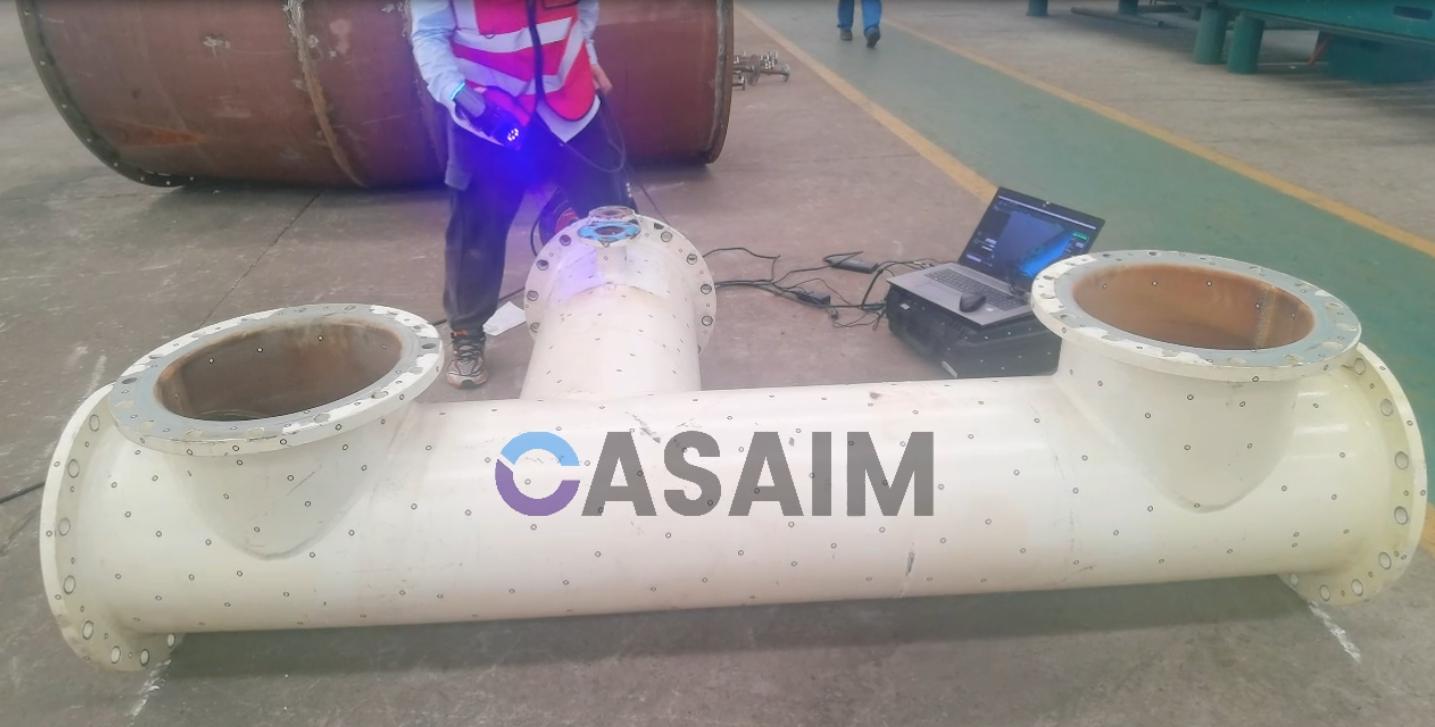

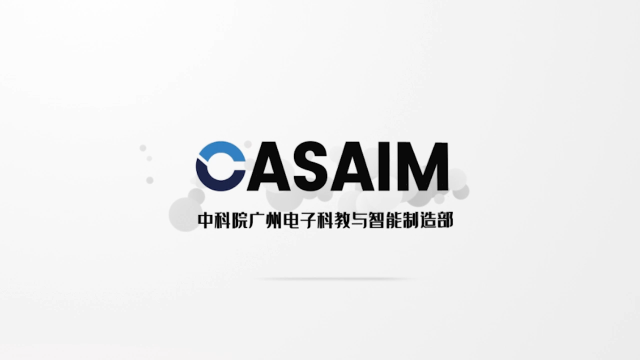
评论