自动化程度是决定生产效率与产品质量的重要因素,在国家大力发展工业4.0和动力电池趋向大规模智能制造背景下,自动化、智能化装备工艺程度,将直接决定动力电池/材料企业未来的竞争力。
2017年,提质降本成锂电行业发展主旋律。为了进一步提升产品竞争力,在提升技术的同时,自动化生产成为了各大企业的首选。
自动化程度是决定生产效率与产品质量的重要因素,在国家大力发展工业4.0和动力电池趋向大规模智能制造背景下,自动化、智能化装备工艺程度,将直接决定动力电池/材料企业未来的竞争力。
由于锂电池生产工序复杂,不同结构形式、不同材料的工艺,所需的自动化装备配置不尽相同,因此每家电池/材料企业的自动化生产线配置也大不一样。自动化产线的差异化也涌现出了一部分优秀的自动化制造解决方案。
在2017年高工锂电金球奖评选中,高工组委会梳理了参评年度自动化产线的15家电池/材料企业(仅部分),呈现出以下四大特色:
1、从设备来源来看,尽管部分自动化产线设备依然选择进口(以韩国设备为主),但有不少企业已经开始大量采用国产设备,这意味着国内智能制造进程提速。比如:中航锂电就与国内一流设备厂商联合研发,自主集成自动化动力电池生产线、自动化动力电池分选线、自动化动力电池模块组装线及自动化动力电池系统集成线。
2、从智能化角度来看,自动化和智能化从来都是不分家的,国内自动化产线都通过导入MES系统等方式,自动生产的同时,进行智能管理。比如:龙能科技就引入了MES系统,从细节处入手,保证影响动力电池性能的因素处于可控范围之内。
3、从经济效益来看,自动化产线在大幅度提升生产效率的同时,还在很大程度上降低了人工成本,从而提升了整体的经济效益。比如:比克电池自动化产线可使生产效率提高116.7%;捷威动力产线可实现生产人员减少70%以上。
4、从性能提升来看,自动化生产规避了人工操作带来了误差,产品的成品率、可靠性、和一致性都得到了很大的提升。比如:多氟多自动化产线整线直通率95%以上,同时电芯可配组率提升至98%以上。
以下为高工组委会梳理的15家电池/材料企业自动化产线。
电池企业自动化产线远东福斯特
远东福斯特采用进口全自动设备,打造了一条自动化、智能化的自动化产线,生产效率高、参与人工少、运营成本低。
高工锂电了解到,该智能制造产线采用自动极片生产、全自动卷绕、全自动电芯装配、清洗、自动化成、老化、分容和自动PACK生产线。与其他目前国内外电池生产装配方式相比,拥有产线自动化、智能化水平程度高、产品成品率高、可靠性和一致性好的优点。
具体来看,该产线的高端设备如自动加料系统(精度达到千分之一),采用先进的挤压涂布机进行涂布,厚度精度可达到±1.5μm(±1.5%),涂布速度达到25m/min,而国内常规涂布机的精度为±3μm(±3%),涂布速度为25m/min。
同时,进口的韩国DA全自动装配流水线,生产效率达到150PCS/min,日生产量超过18万PCS/天,生产出的18650电芯循环性能可达到1C放电2000次以上,大幅提高产品的一致性。
龙能科技
为在高速发展的动力电池市场抢占先机,龙能科技果断引进韩国著名设备制造装备,一期总投资15亿元,建成具备3.5亿安时动力电池年产能,自动化程度极高的尖端生产线,该生产线涵盖了锂离子动力电池生产的全工艺流程。
在先进设备为产品一致性提供强力保证的同时,龙能科技稳妥地引入MES系统,从细节处入手,保证影响动力电池性能的因素处于可控范围之内。
目前,出自该产线的动力电池单体能量密度可达250wh/kg,循环寿命4000周,最大充电倍率2-3C,放电倍率5C,持续放电倍率3C,已通过挤压、针刺、重物冲击等国标检测。根据龙能科技布局规划,其二期项目还将投资70亿元,规划高端锂电池产能6.5亿安时。
此外,龙能科技还在着手PACK无人工厂建设,预计该工厂2018年开工,2020年建成投产,产品主要为单体电池及电池组。一二期项目达产后,年产能预计可达10亿安时。
比克电池
比克电池搭建的锂离子电池生产综合自动化管理系统,可实现工厂内自动投料,自动涂布、碾压和切片、卷绕、装配等生产工序的数字化、可视化、自动化控制。
将一整套数字化管理系统运用锂离子动力电池自动化解决方案中,通过MES系统,实时掌握计划、调度、质量、工艺、生产线运行等信息情况,同时将实时数据同步到数据库,实现生产线的自动化控制,MES系统与ERP系统、WMS系统对接。
此外,比克电池自动化产线采用数字化建模仿真,全自动化设备,在仓储物流设备方面,采用堆垛机、AGV和RGV等智能装备,可使生产效率提高116.7%;同时,自动化生产设备、智能化的管理管理监控、自动化流水线,分级管理措施等,又可促使运营成本降低25%。
沃特玛
据悉,沃特玛自动化产线将预充、分容、分选、点焊、包膜、配档、锁模、组装、测试、包装各工序集成为一体,全面实现自动化生产。该生产线在保障电池一致性、稳定性等方面起到了关键作用,实现了为企业降本增效。
值得一提的是,沃特玛自动化产线,可实现机器人自动上料、在线自动分选、自动碰焊等功能,配备AGV小车,提升了电芯的一致性,缩短了交货期,降低企业运营成本;同时沃特玛自动化产线还具有自动化、智能化、数字化的特点,整个生产过程通过大数据管理,能有效追溯电芯生产状态及信息并做出有效处理。
多氟多
多氟多焦作新能源公司“新能源汽车动力电池智能化车间”自动化产线具有以下6大特点, (1)设备自动化程度96%以上;(2)单批次电芯制造时间缩短至7天以内;(3)电芯能量密度达到250Wh/kg以上;(4)整线直通率95%以上;(5)电芯可配组率提升至98%以上;(6)自动数据采集率92%以上 。
多氟多焦作新能源称,通过关键制造工艺的数值模拟,生产过程的可视化仿真和先进传感、控制、检测、装配、物流及智能化工艺装备与生产管理软件的高度集成及现场数据采集与分析系统、制造运行管理系统(MES)与产品全生命周期管理(PLM)、企业资源计划(ERP)、数据采集和监控系统(SCADA)高效协同与集成来实现新能源汽车动力电池智能制造的新模式。
中天储能
中天储能自动化产线通过在产品研发、制造、检测、运维环节导入数字化和智能化理念,并通过信息化与工业化的深度融合,实现不同型号产品的定制生产及柔性化生产,快速响应市场需求。
在生产制造方面,公司项目通过生产过程仿真系统、装备群的高度集成、在线实时监测系统建设、智能化生产管控平台的建立,有效保证生产效率的发挥和产品的质量稳定。此外,“高柔性”及“高自动化”的设计方案解决用户电池组装线(PACK生产线)订单批量小、规格多的生产管理问题。
在产品性能方面,单体电池产品容量、内阻一致性可达97%,电池组一次合格率大于95%,电池组使用寿命大于10年或20.0万公里,电池产品性能处于行业领先水平。
剑兴锂电
剑兴锂电二期智能化车间在锂电池生产的全部制造和装配工艺皆采用了先进的自动化生产系统、智能化检测系统和绿色环保系统,数字化车间实现互联互通网络保障体系以及基于企业云的ERP和MES等管理软件的协同与集成,制造过程的虚拟仿真、优化与实时监控,全过程多方位的可视化智能管控技术、以及大数据分析的智能优化生产决策支持系统等方面。
其创新点在于,以在建的新一代高性能动力锂离子电池生产项目为依托,致力于生产“高安全、长寿命、可快充、全天候”的新一代高性能动力锂离子电池产品,将最新的自动化、信息化、智能化技术与传统的锂电池生产行业深度融合,打造一个全新的高质高效、绿色环保的锂电池智能制造车间,形成具有行业标杆的智能制造新模式应用。
猛狮科技
福建猛狮新能源18650动力锂离子电池产线采用国际最先进的锂离子电池制备技术和工艺,以及当前世界上该产业最先进、自动化程度最高的电池生产线,进行锂电池智能化生产。目前该条生产线已达产,可年产8000万支锂电芯。
据悉,该三元18650圆柱型锂电池电芯生产线采用道式极片烘干、全自动卷绕、全自动电芯装配、清洗、全自动化成、老化检测设备和PACK生产线,与其他目前国内外电池生产装配方式相比,生产工艺更简单、生产柔性更好,可以同时生产不同材料、多种容量、规格的锂离子动力电池。大大提高了生产的自动化水平,产品成品率高、可靠性、一致性好。
中航锂电
中航锂电与国内一流设备厂商联合研发,自主集成自动化动力电池生产线、自动化动力电池分选线及自动化动力电池模块组装线及自动化动力电池系统集成线。采用涂布在线测厚闭环控制技术、辊压全液压控制技术、切片CCD检测技术、叠片X-RAY检测技术、化成能量回馈技术、电池自动分选技术、电池信息管理系统等先进控制技术,实现电池生产全过程的自动化控制,自动在线监控。建立每个锂电池生产全过程数据库,实现按数据对电池在线自动分组,对故障电池原始数据可追溯查询。
高工组委会了解到,中航锂电关键装备的各项技术指标已接近国际先进水平,整线装备国产化率超过90%。相比采购周期长、价格高的进口设备,国产设备更具优势,相同产能生产线成本仅为国外进口线30%左右。
捷威动力
捷威动力采用了国际最先进的锂离子电池制备工艺和技术,以及当前世界上该产业先进化、自动化、信息化、智能化程度最高的电池生产线。据捷威动力介绍,公司产线自动化程度已经达到国际先进水平,可实现动力电池的高速度、高效率、高质量、低成本的连续化生产,OEE水平可达85%,装配自动化产线合格率可达99.5%以上。
相比国内同等产线,该产线可实现生产人员减少70%以上,同时能够实现动力电池制造过程控制因子的自动记录和监控,实现动力电池的信息追溯,真正实现动力电池的智能制造。
亿纬锂能
亿纬锂能采用高度自动化与信息化生产方式,一线员工人数占比约50%,为客户提供一流的产品和服务。以圆柱动力电池生产为例,今年就建成130ppm的全自动化、全信息化动力圆柱21700电池生产线(兼容18650)。
此次,亿纬锂能报名参评的是中大型软包动力电池全自动化生产线。这条产线拥有半成品及成品的自动化品质检测系统,具有三大创造性优势:
一是采用流变学的设计方法,以使新材料及多种化学物质实现最优;二是采用大容量及全自动在线生产系统,以保障产品品质一致性;三是具有人机料法环全系统的MES追溯系统。
星恒电源
星恒电源打造的独有的生产制造体系,不是简单引入国外工艺、设备,而是“量体裁衣”,凭借多年装备研发经验,打造了一条低能耗、低损耗、高效率、高质量的“超级”产线。
在模切工序,将极片精度做到微米级。自创极耳铆接工艺,使内阻降低至毫欧级。同时,星恒研发自动组装机器人,将原来的10道工序在一台设备实现全自动化。独特的壳体设计配合专利激光焊接工艺,解决行业级焊接难题。四大生产环节严控湿度+独创的闭口工艺,彻底解决行业水分控制难题。
在该产线中,星恒还全面引进自动化设备,赶超国际制造先机水平,包括高速离散机、激光、红外检测设备、AGV自动搬运机器人等,为高品质、自动化制造保驾护航。
电池企业自动化产线格林美
据了解,格林美正极材料生产线引进高端机器人、自动装钵、自动输送系统、智能辊道窑、自动包装系统等一系列高端自动化设备,自动化设备占比100%,实现了物料计量、混合、烧结、粉碎分级、除铁、合批包装等工序全流程自动化运转。
在此基础上,实现产线设备联网,采用SCADA数据采集与监视控制系统,集成生产设备PLC系统信息,实现对产线生产设备运行的可视化、自动预警、自动控制功能。同时,该产线还引进条码管理系统,并与公司ERP系统集成,实现原辅材料、半成品、成品的智能仓储管理,实现产品录入、维护、入库、出库、信息查询、库存盘点等功能,从而加快生产周转,实现对生产操作的可追溯和批次管理。
重庆特瑞
重庆特瑞实施的磷酸铁锂正极材料自动化生产线项目,相比传统的生产线具备多种优势。该项目提出水相阴阳离子多元复合法合成磷酸铁锂的方法,加入了三元材料中间体作为主要的复合原料,从本质上提高了磷酸铁锂导电性。
重庆特瑞表示,采用该自动化产线生产出来的磷酸铁锂材料具备多种先进性,具体体现在:导电性能好;产品批次稳定性好;倍率性能优异。
丰元锂能
丰元锂能首次在磷酸铁锂行业采用数字化、智能化、自动化生产线,率先采用“配料→分散研磨→喷雾干燥→烧结合成→粉碎→包装”的全过程智能化、自动化生产。
该自动化产线可以对产品的生产过程进行追溯,有效防止了人工操作的不确定性,提高了产品性能和一致性。相比较传统生产线,使产线人员数量降低80%,从而大大降低人工成本和提高了产品的一致性。
-
自动化
+关注
关注
29文章
5597浏览量
79415 -
电池
+关注
关注
84文章
10627浏览量
130276
原文标题:【佳的自动化·高工透视】15家电池/材料企业“智造”PK 自动化产线呈现4大特色
文章出处:【微信号:gh_a6b91417f850,微信公众号:高工锂电技术与应用】欢迎添加关注!文章转载请注明出处。
发布评论请先 登录
相关推荐
自动化创建UI并解析数据
自动化创建UI并解析数据
制造业上自动化产线的RFID读写器与标签的选型应用方案——选型流程
自动化设备产线数据采集解决方案
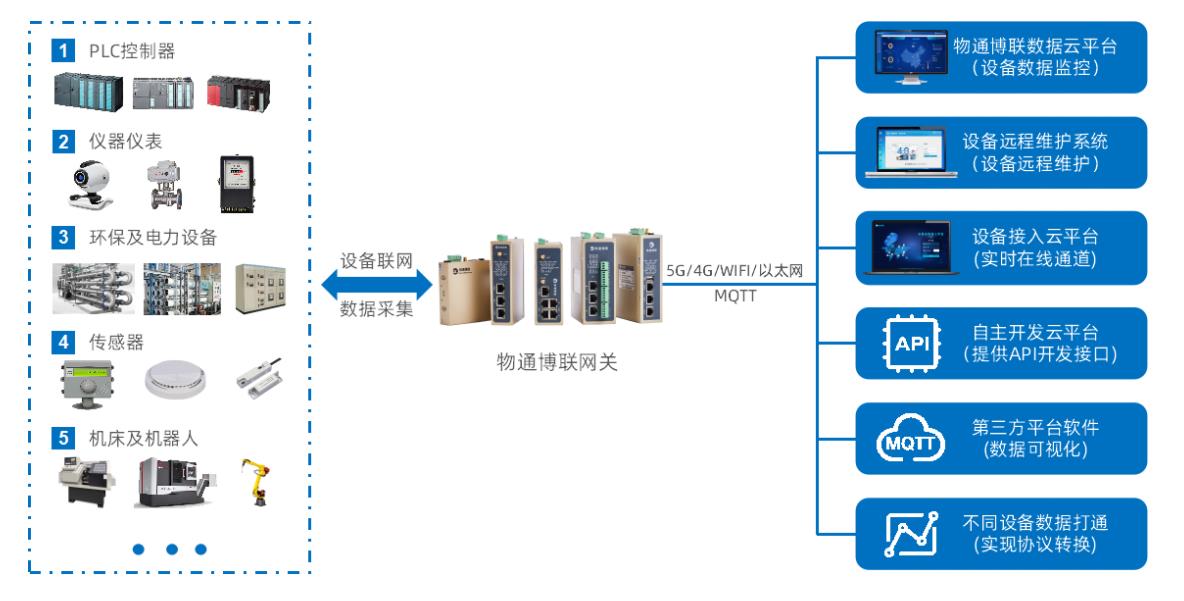
电子元器件工厂自动化产线数据采集解决方案
比斯特自动化:引领电池组PACK自动化生产线的创新与发展
电池自动生产线:智能化制造的未来趋势
机械自动化是自动化的一种吗
产线自动化改造,智能化空调压缩机中的工业RFID技术应用
比斯特自动化|电池组全自动生产线:推动电池制造行业的革新与效率提升
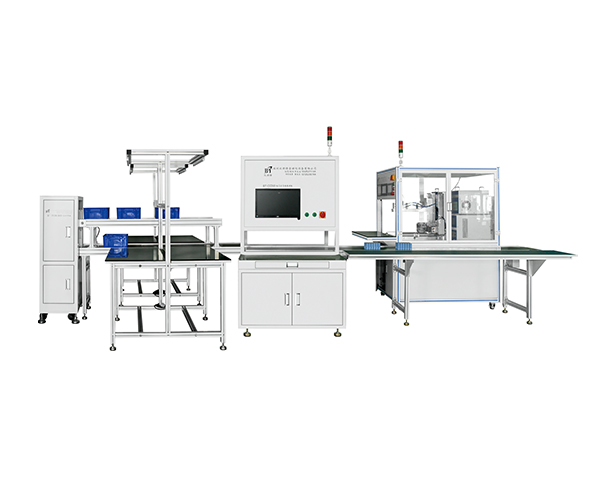
纳米软件分享:电源管理芯片自动化测试方案
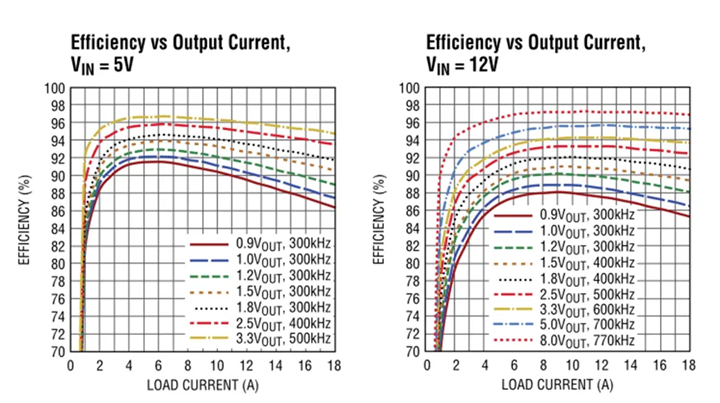
评论