物联网技术正在重塑整个制造业,在自动化基础上融合新一代信息化技术,实现生产线的数字化转型。
从工厂的层面来看,万物互联浪潮发展简化了设备维护的流程;从客户服务方面来说,物联网帮助企业实现了更全面的服务。
工业物联网将为制造创造巨大的收入,制造商开始在自己的产品里嵌入一些传感器来收集相关信息,包括监控产品材料、性能和在使用过程的实时信息,用来帮助企业调整产品计划和优化产品性能。
从飞机到汽车发动机和医疗设备,例如将在开发产品时将传感器内置在零部件里,从而提升产品性能,让产品变得更安全,可以获得更长久的使用等。
制造商能在问题出现前实现预测性维护,从根本上减少停机时间和维护成本。物联网的使用提高了客户的智商,新一轮以智能制造为核心的生产模式正在快速逼近。据相关机构预测,到2020年全球物联网支出将达到700亿美元。
实时诊断提升产品质量
一件产品从设计到生产再到用户使用,其整个生命过程都处于监控和数据采集的过程。通过嵌入式传感器和控制器可以帮助客户发现产品潜在的问题,然后反馈给设计和生产部门,使得产品在设计、材料选型和生产过程合理避过一些误区。同时,厂商可以通过信息收集了解客户使用的具体情况。
通常设备厂商不知道他们设备在现场运行会发生什么事,直到用户打电话来反馈才知道。有些厂商每隔一段时间做一次客户调查,才能了解产品使用的真实情况。除非在产品内部安装监控传感器,否则制造商和销售不会意识到设备哪里出问题,只能等客户投诉。
许多厂商有同样的问题,对于安装在客户现场的产品运行情况知之甚少。而在物联网时代,有关设备的温度、风扇运行时间和能源消耗的信息都可以通过网络报告给制造商,厂商可能考虑商业应用中实时诊断。
利用传感器远程监测
基于设备数据的接收和分析,制造商可以帮助客户避免故障和提高机器效率。这些公司也可以收集技术数据,从而调整产品和部件的设计,使其性能更好,更耐用。
首先是在设计中避免问题,其次是在生产后采取纠正措施,如修理、维护或更换。
制造商可以在几乎所有的制造工序中进行数据采集,这些数据有助于优化生产计划安排,指引企业如何利用资源设施,让企业更好地利用闲置设备和机器。在产品中内置传感器,可以帮助公司实现产品离开工厂后的数据采集,通过记录设备数据,比较设备在不同的环境下的表现,通过这些过程可以挖掘出运营效率低下的问题,从而避免了致命性失败。
通过分析或利用数据,制造商可以进行更合适的预防性维修和保修计划,而不是等到设备出错时才去处理。传感器的数据可以帮助厂商提前得到预警,确定哪些是必须维护的,从而根据设备的性能配置合理的参数以获得最佳性能。
远程状态监测(RCM)是一个基本的服务,也是影响客户服务质量的一个重要因素。在售后服务支持中,实时访问产品状态信息的能力是非常有用的,特别是因为它能更有效的从根本原因分析上解决产品的问题。远程状态监测的下一步显然成为预测性维护,使用传感器如热成像、声波和超声波振动分析,在问题发生之前检测出来。物联网为企业改善客户服务和推动销售量提供了一个很好的方式。
当然,工业物联网带来机遇同时也有巨大的挑战,安全和隐私是行业关注的重要问题之一。不安全的连接设备,可能为攻击都提供了一个后门,不但危害了消费者,也使得工业物联网提供商蒙受损失。
从被动维修到主动维护
基于物联网大数据的预测性维护正在逐渐流行,据分析有1/4的制造商已经通过预测性维护软件来跟踪产品的性能。厂家对物联网的使用越来越感兴趣,经营预测维护市场规模估计将从2015年5.8亿美元增长到2020年的18.8亿美元。
制造商正在整理数据从资产在价值链获得见解和分析资产利用率、故障预测与提升资产寿命。例如,当资产功能的特定组件或部分最佳资产通过机器数据技术和远程监控应用向中央系统发送所需的信息。
建立一个以客户为导向的服务生态系统,需要厂商为其安装基础维护数据采集产品。实时采集的基础信息价值大大提高,它们产生了新的客户、提高了售后服务和盈利能力。安装基础远程监控也创造了提供远程服务的可能性。
最重要的是,它会产生一个新的收入来源,同时提高客户满意度,使制造商能够抵消在经济低迷时收入下降的现象。信息化解决了资产管理团队因检测不足而导致突然停机或故障的问题,通过物联网将实物资产、人和流程无缝连接起来。许多制造企业都采用物联网对生产进行监控,从而降低成本,提高安全性,制造更强大的产品和提高整体设备效率。
在物联网时代,工厂可以实现更大的可视化生产车间,提高生产效率,增强盈利能力。预测性维护可以优化正常运行时间和计划停机时间,客户的订单能及时满足。此外,作为预测性维修计划,需要包括使用一个中央数据库标识备件、资产状况和客户订单,跟踪成本和确保适当的财务管理。
选择合适的分析模型
物联网正在成为一个强大的变革力量,它是制造企业设备维护和增强客户体验不可或缺的技术。而物联网趋势将提高复合分析模型的使用,制造商也可以选择传统的分析模型来实现这些目标。
传统的分析模型区分可修复和不可修复的部分,预测设备失效的周期。这些模型利用历史失效时间数据确定零件未来的失败时间。在这种情况下,制造商从传感器获得数据详细信息,这些模型证明特别有用。与复合模型不同的是导致零件失效也是确定因素,此功能可超出传统分析模型的一般特征。
对于制造商来说,接下来的问题是哪种模式更适合他们的特定需求。对此,需要考虑几个问题。
首先,数据的可用性是一个重要的因素,当数据导致零件失效和信息部分失败事件是可用的,选择复合模型更适合。另一方面,当只要求数据检索,传统的模型往往是更合适的。
其他因素影响分析的选择是部分可修或不可修到故障预测及零件的生命周期阶段完全不同。用正确的模式,制造商可以把他们的预测性维修工作的升到新水平。随着越来越多的玩家意识到这一点,我们将在行业中看到更聪明、更高效的制造企业。
-
传感器
+关注
关注
2551文章
51084浏览量
753439 -
物联网
+关注
关注
2909文章
44625浏览量
373235 -
数据采集
+关注
关注
38文章
6090浏览量
113642 -
RCM
+关注
关注
0文章
7浏览量
10036
原文标题:IT与OT融合,物联网重塑整个制造业
文章出处:【微信号:cqwu023,微信公众号:重庆物联网】欢迎添加关注!文章转载请注明出处。
发布评论请先 登录
相关推荐
制造业中物联网优势 重塑工业的强大引擎
一文探索制造业中物联网优势
计算机通信设备制造业、仪器仪表制造业等先进制造业发展向好
什么是物联网技术?
衡器制造业物联网数据采集解决方案
缝纫机5G智能制造工厂物联数字孪生平台,推进制造业数字化转型
工业物联网在制造业中的八大主要用途!
欧时制造业产品及解决方案助力中国制造业企业工业数字化转型
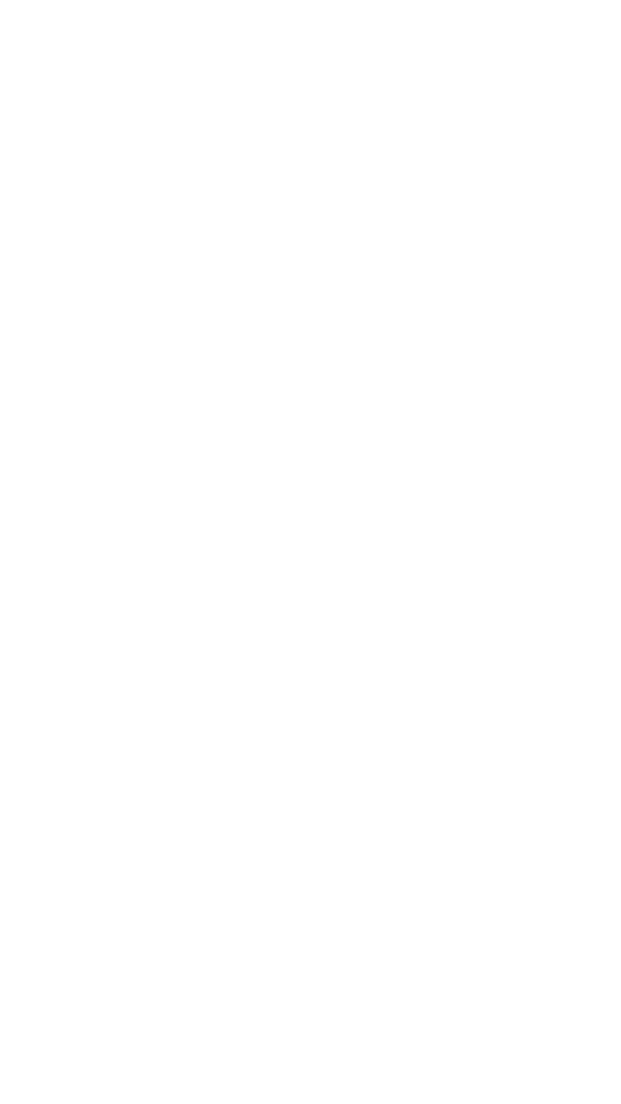
评论