晶圆分选良率因素
制造后,晶圆被送到晶圆分选测试仪。在测试期间,每个芯片都会进行电气测试,以检查设备规范和功能。每个电路可能执行数百个单独的电气测试。虽然这些测试测量设备的电气性能,但它们间接测量制造工艺的精度和清洁度。由于自然过程变化和未检测到的缺陷,晶圆可能通过了所有的工艺内检查,但仍然有不工作的芯片。
由于晶圆分选是一个全面的测试,许多因素影响良率。它们是:
1. 晶圆直径
2. 裸片尺寸(面积)
3. 加工步骤数量
4. 电路密度
5. 缺陷密度
6. 晶体缺陷密度
7. 工艺周期时间
晶圆直径和边缘裸片
半导体行业在引入硅时采用了圆形晶圆。第一批晶圆直径不到1英寸。从那时起,晶圆直径一直在稳步增加,150毫米(6英寸)在1980年代末成为VLSI制造线的标配,200毫米晶圆在1990年代用于生产。到2012年,300毫米晶圆全面生产,450毫米直径晶圆正在引入,预计到2018年全面生产。
向更大直径晶圆的转变是由生产效率、裸片尺寸的增加以及对晶圆分选良率的影响驱动的。当考虑到处理更大直径晶圆的成本增加是递增的,而晶圆上的可用完整芯片数量可以大幅增加时,生产效率就很容易理解,如下图所示。
增加晶圆直径对晶圆分选良率也有积极影响。下图显示了两个相同直径但不同裸片尺寸的晶圆。请注意,较小直径的晶圆有很大一部分表面被部分裸片覆盖——这些裸片无法正常工作。更大的晶圆,如果所有其他因素都相等,由于拥有更多数量和更高比例的完整裸片,将具有更高的晶圆分选良率。
晶圆直径和裸片尺寸
更大直径晶圆的另一个驱动力是裸片尺寸的增加趋势。如图所示,如果不增加晶圆直径而增加裸片尺寸,也会导致晶圆表面有更小比例的完整裸片。为了在裸片尺寸增加的同时保持合理的晶圆分选良率,需要增加晶圆直径。下图列出了不同尺寸晶圆上可容纳的各种尺寸芯片的数量。底线是,更大直径的晶圆更具成本效益。
晶圆直径和晶体缺陷
在之前的章节中,引入了晶圆晶体错位的概念。晶体错位是晶圆上的点缺陷,来自晶体结构的局部不连续性。错位贯穿整个晶体结构,并且像污染和工艺缺陷密度一样,影响晶圆分选良率。
错位也是在制造过程中产生的。它们在晶圆边缘的芯片和划痕处生成(或成核)。这些芯片和划痕来自处理技术不当和自动处理设备。磨损区域会导致晶体错位。不幸的是,在随后的热处理过程中,如氧化和扩散,错位线会传播到晶圆中心(见下图)。错位线进入晶圆内部的长度是晶圆热历史的函数。因此,接受更多工艺步骤和/或更多加热步骤的晶圆将有更多的错位线,影响更多的芯片。解决这个问题的一个明显方法是更大直径的晶圆,这在晶圆中心留下了更多未受影响的裸片。
-
芯片
+关注
关注
454文章
50689浏览量
423014 -
半导体
+关注
关注
334文章
27253浏览量
217924 -
晶圆
+关注
关注
52文章
4884浏览量
127918
原文标题:半导体工艺之生产力和工艺良率(四)
文章出处:【微信号:FindRF,微信公众号:FindRF】欢迎添加关注!文章转载请注明出处。
发布评论请先 登录
相关推荐
先进的清洗技术如何助力先进节点实现最佳晶圆良率
AI为晶圆代工产业将带来什么的未来?
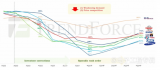
晶圆制造和封装之影响良率的主要工艺和材料因素(一)
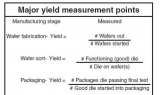
半导体工艺之生产力和工艺良率
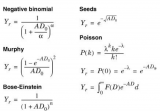
评论