导语
GE的Global Research团队,针对供应链与工厂流程打造「数字双胞胎」,借以持续监测所有装置设备正在发生的大小事,进而优化决策质量,带动库存管理效率及工厂吞吐量攀高。
在Gartner依惯例发布2017年十大技术趋势,其中最受瞩目的亮点,便是Digital Twin,有人把它翻译为「数字双胞胎」,其意指物件或系统的多元软件模型,借助传感器来理解标的物件或系统的真实处境,让使用者能精准快速地反应各种变动情况,从而改善物件或系统的的操作,或增添其附加价值。
Digital Twin随着计算机能力提升、传感器价格下降,精确度更准确,许多事件都可以在电脑上进行模拟。企业可以用Digital Twin来尝试改变某些初始条件带来的结果。
以制造业而论,若能善加运用Digital Twin,即等于巧妙建立一套智能代理人,可以主动修复与规划设备服务,规划制程、产线或整座工厂,从而及早预测设备的潜在故障因子、强化产品开发,终至提升营运效能。
由此看来,一旦企业能够妙用工业物联网(IIoT)与Digital Twin,一方面就可以有效汇集来自外围环境或设备的大量资料,二方面更可善用这些数据,在犹如真实世界化身的数码世界里执行模拟运算。
如此一来,企业毋需耗费高昂的成本代价购置大量装置或设备,即可透过Digital Twin这个虚拟分身,持续不断进行分析与测试,并随时针对异常状态进行修补与复原,藉此缩短各项创新研发专案的试误历程,且易于维系创新产品的质量与稳定性。
1Digital Twin象征CPS虚实融合技术
有专家甚至认为,深究Digital Twin的本质,即是一种虚实融合技术,与工业4.0所提及的CPS,可说完全契合;因此若说数码双胞胎就是CPS,基本上算是一种正确说法,但Digital Twin似乎比起CPS更为生动到位。
而这个概念无疑是从既有虚拟制造、数码原型(包含几何原型、功能原型、效能原型)等技术基础演化而来,若欲凸显前后差异,则是数码原型之建构目的,主要用于描述产品设计者针对此产品的理想定义,作为产品生产制造、功能与效能分析的指引。
但不可讳言,在真实世界里,产品在生产过程的加工、组装等程序上,难免稍有误差,而后续产品被使用、维修的状态,更充满不可预测性,因此要让真实产品与数码模型保持一致,无疑难上加难,这也使得所有在数码模型上执行的模拟分析,不见得具备有效性。
反观Digital Twin,则充分运用物理模型、传感器资料更新,辅以历史运行数据,并集成多种维度的模拟过程,在虚拟空间中完成映射,进而更能确实反应出实体物件的全生命周期历程。
比方说,一个厂房或产线在尚未建构完毕时,即可先行建立数码模型,举凡3D布局、设备排布、产线规划、人因工程模拟与作业研究等因素皆可纳入其中,继而透过虚拟空间,针对厂房或产线进行预先模拟,假使察觉动线不良、产能不佳或可能造成人员伤害等等不利因子,便可预先排除并修正。
同时把经过优化的参数,传递予实际建厂的工程团队,而日后即使该工厂或产线正式启用,在日常维运过程中,虚实世界两端也能彼此进行信息交换。
值得一提的,随著计算机运算能力增强、传感器价格下降、感测精准度攀高等正面因素加持,展望未来,许许多多事物皆可透过Digital Twin执行高精准度的模拟,使企业得以利用经济实惠且又安全的环境,模拟各种流程改变可能产生的影响,甚至进一步将虚拟实境(VR)、扩增实境(AR)、混合实境(MR)乃至Digital Twin等不同技术概念,巧妙融合在一起,帮助企业研发团队「身历其境」推动各种创新探索。
就在去年(2016),身处工业4.0概念发源地(德国)的西门子,便在其论坛活动中,针对Digital Twin做了绝佳演绎。该公司强调,透过Digital Twin可助企业纵向或横向集成价值链,从而为工业生态系的建构、乃至工业4.0的实现,打造一条从上到下完整的实践路径。
更让人啧啧称奇的,西门子也将VR技术运用得淋漓尽致,于英国柴郡的一座工厂内安装Virtalis虚拟实境软件与系统,借以实现组装制程的模拟与优化,并提升概念设计的效率、有效执行工厂规划,针对制程过程早期阶段可能出现的种种问题,一并加以解决。
不仅如此,西门子除透过这套Virtalis VR系统,帮助这座英国工厂减少差错外,更促进跨专业领域的大规模沟通,使得不论是生产工程师、测试工程师、生产管理者、生产作业员,甚至研发单位、机构部门、物流公司或外包商,都能在VR环境中共同作业,确保新产品研发专案的各个设计环节都趋于完善。
如果在虚拟世界中对产品进行前期的规划、部署、仿真和验证,那么未来也就不需要花费高成本来验证和调整,这将大大提升企业的生产效率,保证此后大规模生产的稳定性,并将整个企业的价值链有效叠加在一起,这就是西门子和客户真正关注的。
2Digital Twin加VR 挥洒弹性制造效益
总而言之,虚拟实境、Digital Twin等技术之于工业界的运用范围相当广阔,从虚拟厂区布置、虚拟原型、网路虚拟制造、虚拟装配,一直到虚拟工厂的建立等,皆拥有很高的利基优势。
Santa Cruz是一家美国自行车公司。像绝大多数产品一样,从最初在CAD环境下进行设计,到出厂进入消费者手中,厂家很少能够再获得产品的任何实际使用情况,这也是目前最常见的产品流程——没有反馈、改进的单向流程。
接下来看下这家自行车公司如何通过“Digital Twin”4步打通物理、数字世界,从中或许可以帮助大家感性了解智能互联对传统工厂产生的翻天覆地变化。
传统自行车测试、维修只能手动拆卸
扫描条码,实时传感数据即通过AR、Digital Twin技术叠加显示在屏幕上
专家解释,伴随工业生产技术进步,不少制造企业为了提升竞争力,纷纷把原本单一生产的机台模式,转变为多台机械連线的自动化生产模式,并结合计算机控制,满足少量多样的弹性化生产需求,组合为多数业者并不陌生的弹性制造系统(FMS)。
然而一套FMS个中涵盖多个自动化岛(Islands of Automation),由多台CNC加工机、搬运设备(例如无人搬运車、输送带、机械手臂)、仓储系统与监控计算机等单元共同组成,可想而知,意欲维运FMS,少不得需要投注大量金钱与人力资源,且可能衍生莫大风险。
为了兼收趋吉避凶、撙节成本等多重效益,近年来部份企业已结合FMS、VR与Digital Twin等不同系统与技术,构筑一套虚拟弹性制造系统,让使用者可透过互联网从远程操控系统,譬如藉由CAD/CAM软件将绘制好的工件图形转为NC码,接著把NC档案传送到服务器,进而汇入虚拟弹性制造系统,实现整个系统加工作业,达到虚拟制造目标。
专家一并提醒,尽管Digital Twin对于制造业而言,算是富含魅力的应用模式,但不宜将之窄化为只是一套「构型管理工具」、「制成品的3D尺寸模型」或是「制成品的模型定义(MBD)」。
它主要是透过内嵌的综合健康管理系统(IVHM),再集成传感器资料、历史维运资料,经由大数据挖掘出来的高值化信息,因而可持续预测装置、设备或系统的健康状态、剩余使命寿命,甚至是执行任务的成功机率,亦可预先洞察潜在的安全事件,显示这些装置、设备或系统的未知问题。
更有甚者,制造企业一经采用Digital Twin,也可能透过启动自愈机制或建议修改任务参数等方式,针对有疑虑的装置、设备或系统进行降级,以便将可能的损害降低到最轻微程度,等于把迈向工业4.0目标的路障,予以有效排除。
-
cps
+关注
关注
2文章
45浏览量
17489 -
vr
+关注
关注
34文章
9648浏览量
150894 -
数字双胞胎
+关注
关注
0文章
10浏览量
3001
原文标题:妙用Digital Twin虚实融合 驱动智能制造升级转型
文章出处:【微信号:IndustryIOT,微信公众号:工业互联网前线】欢迎添加关注!文章转载请注明出处。
发布评论请先 登录
相关推荐
徐州数字孪生工业互联网三维可视化技术,赋能新型工业化智能制造工厂
SME 如何利用工业虚拟实境快速探索和部署机器人解决方案
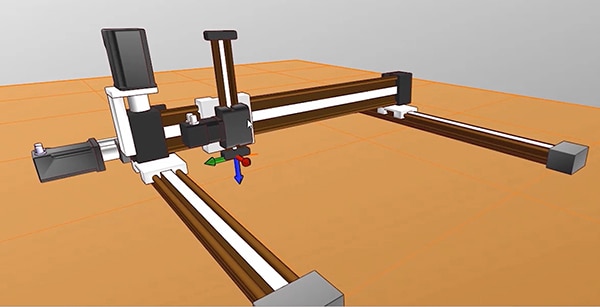
【RA-Eco-RA4E2-64PIN-V1.0开发板试用】读取RA4E2单片机的128位身份证号码
以智能制造为导向的数字孪生工厂构建方法与应用
使用适用于TPS536xx VR13多相解决方案的融合数字电源设计器
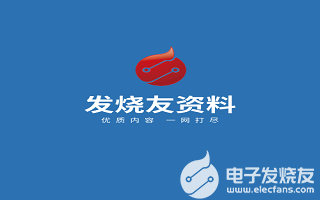
天津数字孪生工业互联网可视化技术,赋能新型工业化智能制造工厂
数字孪生在制造业的应用
指纹读取器上进行扫描什么意思
电动机制造5G智能工厂工业物联数字孪生平台,推进制造业数字化转型
飞机制造5G智能工厂数字孪生工业物联平台,推进制造业数字化转型
缝纫机5G智能制造工厂物联数字孪生平台,推进制造业数字化转型
生物识别验证在哪里开启
数字双应用场景,推动行业变革
应用 Simcenter 试验系统优化疲劳耐久试验流程
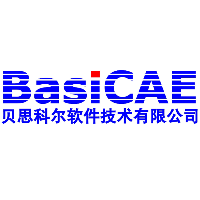
评论