将来应用的燃料电池生产技术很可能不是现在使用的技术,这是国内燃料电池的机遇,同时也是挑战。
拥有足以媲美锂电行业的高热度,却遭遇核心原材料及关键零部件极其匮乏的现实,中国燃料电池正处于“冰火两重天”的尴尬局面。
2017年资本大量涌入燃料电池领域,国内车企(以客车为主)纷纷宣布燃料电池客车示范性运行的时间节点。不仅如此,国家对燃料电池还保持了高昂补贴,并出台了燃料电池发展规划,其中2020年实现5000辆燃料电池汽车的示范性运行,2025年争取实现10万辆。
但事实上,经过调研显示,真正拿得出手的产品,大概也就上汽和宇通分别在乘用车/客车领域取得的阶段性成果。造成这一困局的原因,一方面可归咎于国内燃料电池产业化起步较晚;另一方面则是国内燃料电池核心原材料及关键零部件产业链的缺失。
产品技术空心化
事实上,国内高水平燃料电池电堆主要还是引进加拿大巴拉德的产品和技术,本土电堆企业实力普遍薄弱,目前只有上海神力(已被亿华通收购)和大连新源动力两家公司具备完整的燃料电池电堆的设计和制造能力。
在核心原材料的产业化生产方面,国内更是堪称一片空白。全氟磺酸质子交换膜(PEM)仅仅只有山东东岳集团联合上海交大完成了中试,但其样品不论是在质子电导率还是在成品一致性以及寿命等关键指标上,跟美国杜邦的Nafion膜相比都有较大的差距。
此外,Pt/C电催化剂、炭纸、双极板这些核心原材料以及低能耗紧凑型空压机、高效增湿器等关键部件在国内都极为匮乏。
值得一提的是,尽管国内燃料电池产业化呈现出“理想丰满、现实骨感”的状态,但并非完全没有机会。
中国工程院衣宝廉院士表示,目前全球范围内都没有建立一条真正具备大规模生产能力的燃料电池产线,包括2017年本田和通用宣布投资5000万拟建的燃料电池产线,依然不具备规模化,因为当前的燃料电池生产工艺本身就不满足大规模生产的要求,即便是丰田的燃料电池发动机生产效率也不过3台/天。
看似困境实则机遇?
衣宝廉的言下之意,将来应用的燃料电池生产技术很可能不是现在使用的技术,这是国内燃料电池的机遇,同时也是挑战。
以燃料电池的核心材料膜电极为例。为了使膜电极具备燃料电池汽车行驶条件,全球范围内的研究人员都做了长足的探索。
其中美国3M公司花费了17年对膜电极催化层进行了改性研究,其核心思路是降低维度。即由三维体相材料转变为零维的纳米颗粒,并通过通过调控其尺寸、形貌、组份以及径向分布形成铂基核壳结构材料。
3M公司研制的PtPd/C核壳催化剂,在性能、寿命以及铂用量上都达到了车用条件,但其有一个致命的缺陷,即亲水。要知道铂表面是非常亲水的,生成一点水都会吸附在铂表面,使氧气在其中扩散,造成巨大困扰,这一难题时至今日也没有获得突破。
与3M公司不同,丰田使用的是常规催化层,但通过3D流场技术,在性能上达到了相同的效果。通常的燃料电池流场是一个沟道,气体沿着沟道流动。在化工领域有一项技术,叫挡板技术,即在气体流道前加一块挡板,气体就会形成一个漩涡。丰田正是把挡板技术应用在了燃料电池上,所谓3D流场,就是气体像电机里的传递不仅仅靠扩散,还有对流的成分在里面,从而将膜电极做到3-4A。
而国内燃料电池企业新源动力在膜电极上也有自己的特色,比如应用于双极板的复合板专利。当前国际上的双极板主要分为金属和石墨两类,其中石墨板主要应用于大巴和物流车,其比能量仅为金属板的三分之一,乘用车基本都使用金属板,但金属板的表面改性是一大难点。新源动力的复合板专利采用金属和碳复合,其中碳用来引导气体流场,也能将膜电极做到3A。
从3M、丰田、新源动力对燃料电池膜电极的探索中不难看出,当前国际上燃料电池产业化的技术路线还没有一个确切答案,其中丰田的路线最具参考价值,毕竟量产版燃料电池汽车Mirai是摆在眼前的事实,但即便是Mirai也没有形成大规模应用,这意味着其燃料电池技术还有待进一步改进升级。
相对来说,国内燃料电池产业比较落后,却也具备了自主创新的能力。换个角度看,站在巨人的肩膀上,虽谈不上坐享其成,但至少可以少走弯路。
-
燃料电池
+关注
关注
26文章
962浏览量
95264
原文标题:【索尔科技•FCEV专栏】产品技术空心化 中国发展燃料电池从何谈起?
文章出处:【微信号:weixin-gg-lb,微信公众号:高工锂电】欢迎添加关注!文章转载请注明出处。
发布评论请先 登录
相关推荐
燃料电池测试负载如何进行负载测试?
燃料电池技术的环保优势
燃料电池与氢气的关系 燃料电池与电动汽车的比较
燃料电池的主要材料 燃料电池的效率和性能
燃料电池的应用领域 燃料电池车的优缺点
燃料电池工作原理 燃料电池与传统电池的区别
燃料电池测试负载的工作原理是什么?
冰火两重天!丰田扩厂,日产停产
卫星热控系统的“冰火”两重天
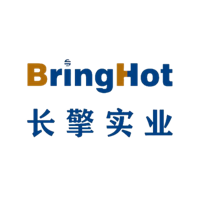
什么是燃料电池?燃料电池和动力电池区别
燃料电池的分类及其特点
全球半导体,冰火两重天
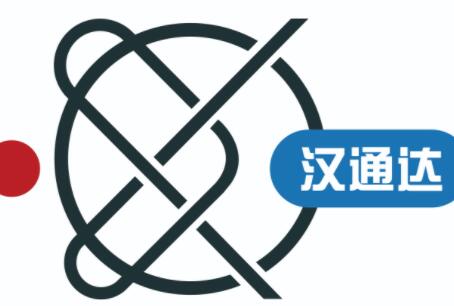
评论