近五年来中国汽车市场发生了重大的变化,新能源汽车的占比逐渐提高,2022 年新能源汽车市场份额超过25%。新能源汽车的电气功能越多,对应的线束插接件越多,线束插接件的故障逐渐成为影响功能实现的一个重要因素。线束插接件的常见失效模式有插接件端子退针、歪针、扩孔,插接件虚接等多种模式,插接件以上失效模式也不能完全被EOL 设备或功能检查所拦截,存在逃逸至客户的风险,所以需要针对各种失效模式从设计、运输、对配、出厂检查多环节去寻找改善方案。
01 绪 论
新能源汽车线束分为高压线束和低压线束,高压线束负责将电池存储的电能传输至各个高压部件,空调压缩机、驱动电机以及PTC模块等。低压线束是整车线束的最主要的部分,主要是将低压供电传递至各个ECU和用电器,传输CAN、LIN 信号、视频线信号等。整车线束中高压线束相对较短,是连接高压部件之间的线束,长度几十米,低压线束长度远远大于高压线长度,例如某款新能源汽车的低压线束长度超过18km。由于低压线束是连接各个用电器之间的纽带,所以线束与用电器之间、线束与线束之间的插接件非常多,线束插接件的对配次数越多,潜在的失效越多。
以某款SUV 车型为例,整车上存在超过1000 个线束插接件,每天装配车间都会反馈线束插接后退针、歪针问题,后续检验车间也有反馈插接不良造成的电器功能问题。总体上看主要分为退针、歪针和虚接的故障模式。
02 常见失效模式及改善对策
本文针对退针、歪针的失效,总结了以下产生原因并针对不同失效讨论了对应改善对策。
2.1物流包装
物流包装在线束插接问题中的影响往往被忽略,但也是其中一个重要因素。对于线束厂商要增加过程防护,从线束与端子压接完成到产品的电检工装测试台增加端子的防护工装,消除端子在零件厂商过程发生歪斜。零件出厂的物流包装要对较大型号插接件重点防护,这些插接件一般开口较大,如果ECU 或者线束在插接件没有增加防护,存在异常情况将插接件内部的端子撞歪,带来插歪的风险。物流环节过程很难杜绝一切异常,并无法做到整个环节的追溯,所以需要在物流包装源头上增加措施。改善措施:针对插接件开口较大的ECU 增加防护罩或珍珠棉对接口进行防护,对线束产品增加胶带,缠绕插接件接口,对内部端子起到防护作用。
2.2匹配设计
2.2.1公母端尺寸匹配设计余量不合理
一般线束插接件端在设计选型时都会考虑公母端为同一家配套产品,公母端护套都是成熟的标准件,从插接导向槽到完全对配的整个过程匹配很好,插歪风险很低。目前存在线束和用电器对配的情况,用电器端的护套都是厂家根据插接件图纸尺寸逆向开发生产的。关键尺寸的设计需要充分考虑导向结构的尺寸,既要能保证合理导向的作用,也要规避难对配的情况。
例如开音量调节开关, 线束母端为MOLEX 标准件,开关为供应商注塑件,公母端导向尺寸配合相差超过0.5mm,加上开关属于盲插插接件,人机工程差,员工无法保证平直对配,造成端子歪斜插入维修孔,如果公端硬碰母端塑壳造成退针,两者失效模式都会产生开关功能失效。
改善措施:对开关Z 向尺寸进行修模,内部导向筋条增加0.2mm,改善了退针和歪针的风险。
2.2.2线束扭转带来的歪针风险未识别
某气囊线束插接件在设计选型时存在线束扭转导致插接件护套内端子明显歪斜的隐患。当前设计上线束端子在护套内部限位不足,导线上的扭转将旋转角度传递至护套内部端子,端子就会出现偏移不居中的现象,最大偏移1mm,母端插接件的插孔壁厚0.5mm,一旦歪斜查过0.5mm 很容易造成插歪。
改善措施:临时在线束上增加波纹管护套,消除装配过程环节扭转线束的风险。永久措施替换新的插接件结构,内部限位更好,即使线束有扭转,内部端子也不会有偏移。
2.3端子保持力
端子保持力的大小取决于插接件内部限位端子挂台的结构的稳健程度。线束端子在插接件内部由限位挂台固定,如果挂台结构薄弱,端子的保持力就偏小。当端子轻微歪斜对接时,公端会插接到母端护套导向结构或者母端端子金属上,整体插接力会偏大,端子保持力不足就会产生退针的现象。另一种情况是线束端子在装配时没有完全导入的限位挂台内,端子保持力几乎为0,对配后就会出现退针的现象。线束厂商装配是有要求端子插入后回拉,但是均为人工装配,人员波动,技能熟练度会影响回拉的检查。出厂的电检台一般是触点检测导通,保持力无法检测,所以主机厂也会发现类似端子未装配到位造成的退针案例。下图为线束母端未装配至护套挂台的案例。
改善措施:产生环节主要在线束厂商装配过程,需要从人员技能培训,人员稳定性入手,减少频繁新人上岗操作的机会。
2.4装配工艺
2.4.1装配工艺布局不合理
一般插接件的装配要求有平直对配的要求,但是部分区域由于工艺布置原因,造成员工很难做到。例如某车型A 柱区域的线束插接件工艺上要求先固定主线束和顶棚线束卡扣,再对配插接件,两个插接件对配时受制A 柱空间影响,平直对配的要求存在无法执行到位的情况,并且插接对配时阻力较大有,容易出现退针的故障。
改善措施:优化工艺装配顺序,先对配顶棚线束和车身线束,对配时线束自由状态存在较大的操作空间,可以按照设计要求,按压塑壳锁止机构装配,然后再固定插接件的钣金卡,这样既减小了对配的阻力,又改善了平直对配的作业环境,有效解决紧靠A柱钣金造成的插接问题。工艺环节要梳理现场实际操作的人机工程、工艺布局等是否合理,并给予改善。
2.4.2装配工艺无自检标准要求
插接失效后需要最早的发现,员工对配结束后就需要有意识的判断本次装配是否合格。当前指导员工作业的标准只有要求平直对配,回拉检查是否虚接,对配合格的判断有缺失。工艺上对所有插接件进行梳理,结合岗位环境噪音,将可以明确通过插接合格“咔哒”音作为判断的标准写入作业指导书。
例如下图是某车型直流充电系统的一个低压控制回路插接件,母端护套有被公端插接的痕迹,判断由于公端有歪斜强行对配将公端对配至母端维修孔内造成的问题。实测歪斜对配阻力38N,正常对配20N 以内。
改善措施:对配完成有明确咔哒音的,写入作业指导书;对于歪斜插接阻力差异明显的,在作业指导书中写入阻力大的后果,固化的内容对员工重新培训。
2.5不合理的电检工装造成退针
线束厂商的电检一般都是伸缩针形式对插接件导通测试,不会对端子造成损伤。但存在一些外包零件,例如保险杠总成是前保供应商将线束固定在前保上,并完成导通检测。前保厂商对线束电检台的选型考虑上未识别电检台与线束对配后可能造成端子歪针的风险,PFMEA 中未能充分识别造成歪针潜在因素和对策,一旦电检设
备端的检具出现问题后会造成批量的线束端子歪斜退针问题。下图是某车型前保供应商因为检具母端存在异物未及时点检维修,线束经过与电检测试设备对配后出现批量前保线束退针的案例。
改善措施:对电测设备改造,需要满足以下条件:一是公端子治具必须佩戴防歪格栅,以保障歪斜的端子无法导通;二是电测探针使用螺纹台阶针,可有效的预防电测过程端子被顶出去,三是根据尺寸链计算出端子在护套内移动量,从而制作探针,并建立探针日常维护保养计划。
2.6人员操作
2.6.1装配人员
插接件连接一般是没有工装辅具保证装配到位的,所以对员工技能熟练度有较高要求,如不做管理就会出现虚插、暴力操作退针、歪针等问题。装配人员在上岗前要做好完整的应知、应会以及实操培训。
插接件的应知:插接件的种类包括拉拔试插接件、二次锁止插接件、高压插接件等认知;插接件基本应会:对各类插接件操作要领应会,同时根据要领可完成独立操作;插接件感知训练:通过线下接插件的实操训练能掌握区分各类接插件在插接过程中正常接插和异常插接不同的感知并能准确判断异常。
2.6.2返修人员
车辆下线之后由于出现功能问题,返修人员需要对导线通断或者总线网络中采集报文数据,需要从接插件处测量,如果测量工具不合理比如使用万用表表笔直接怼线束母端或者暴力操作就会出现怼坏护套造成退针,怼大母端造成扩孔。
改善措施:班组的晨会对歪斜对配、暴力操作等行为进行后果教育,增强质量意识;车间设立定期培训机制,开展道场培训,对插接件正常装配的插入力和声音进行培训,模拟端子歪斜及退针场景培训员工对异常插接阻力的识别,提高员工技能;工厂建立合理的奖惩机制鼓励员工异常举手,增加自互检的方式,在装配或互检岗位及早发现问题。另外管理层需要在人员稳定性方面提出方案,通过减少人员波动,使用熟练工降低人的因素造成插接不良问题。
03 结 语
线束插接件故障是普遍存在的一个问题,影响因素涉及物流包装设计、物流翻包、产品设计、工艺布局和人员操作等多个方面。现阶段解决插接件歪针、退针的问题不能仅靠人员操作上的提前检查,手感检查的方式,还需要从零件端子的垂直度保证是否可靠,产品设计是否稳健,工艺布局、人机工程是否合理,零部件和主机厂人工操作熟练度是否达标等环节考虑。其次主机厂也要在EOL 检验中研究退针、歪针造成间歇性故障的拦截方案,通过EOL 设备程序优化,实现插接件造成的短路开路历史故障码的识别,提高插接件故障拦截成功率,降低逃逸至客户的概率。最后要研究新技术的应用替代线束插接件,产品设计向模块化、集中化的域控制发展,模块内部使用多层PCB、FPC 等技术方案减少线束插接的数量。
-
新能源汽车
+关注
关注
141文章
10519浏览量
99414 -
连接器
+关注
关注
98文章
14476浏览量
136427 -
线束
+关注
关注
7文章
973浏览量
25976
原文标题:连接器常见失效模式及原因分析
文章出处:【微信号:线束专家,微信公众号:线束专家】欢迎添加关注!文章转载请注明出处。
发布评论请先 登录
相关推荐
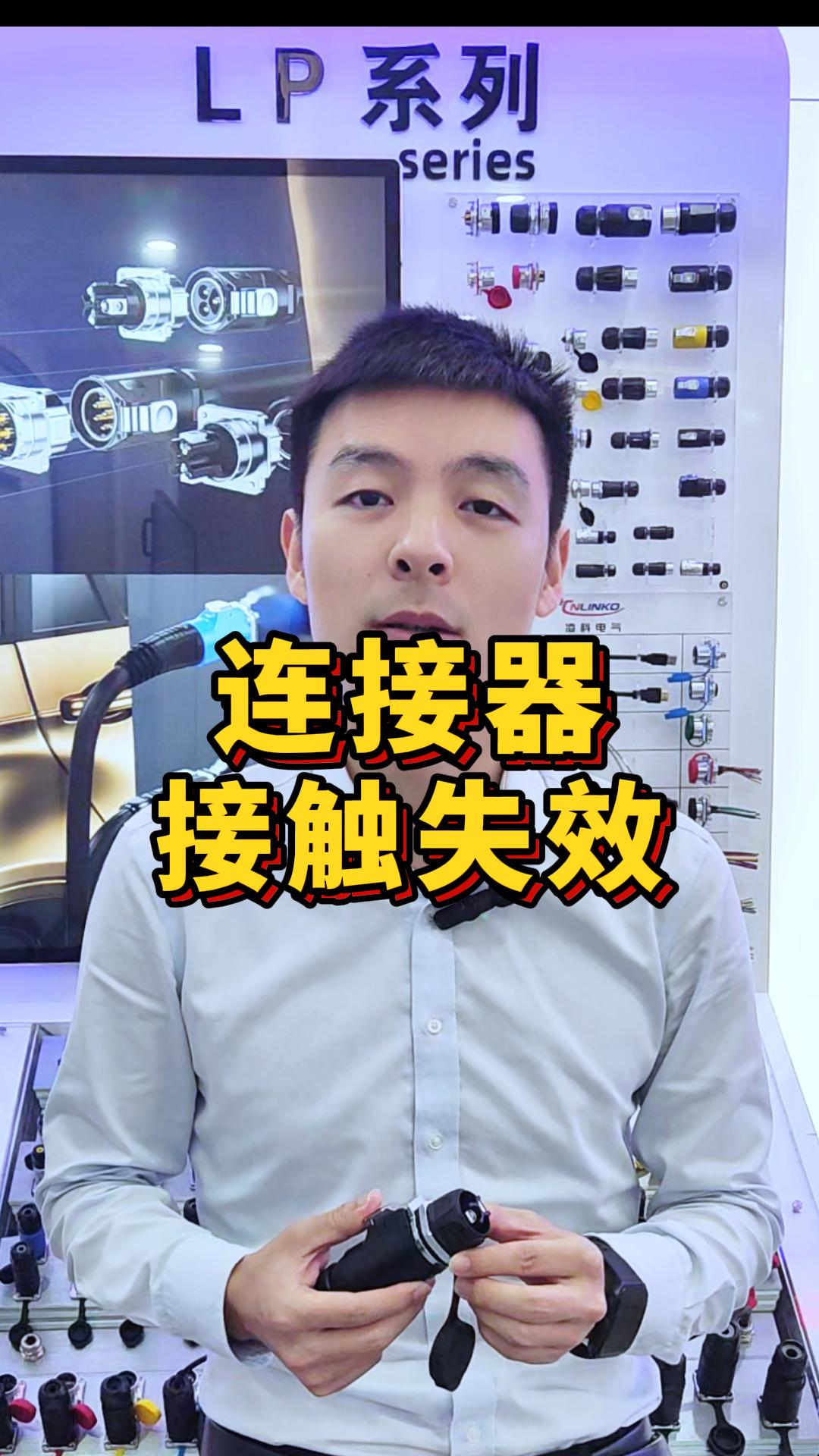
电连接器及其组件(线束)的常见失效模式
连接器退化机理是什么?哪些因数会导致连接器失效?
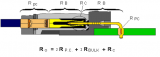
连接器连接失效的原因有哪些
连接器最主要的失效模式是什么?
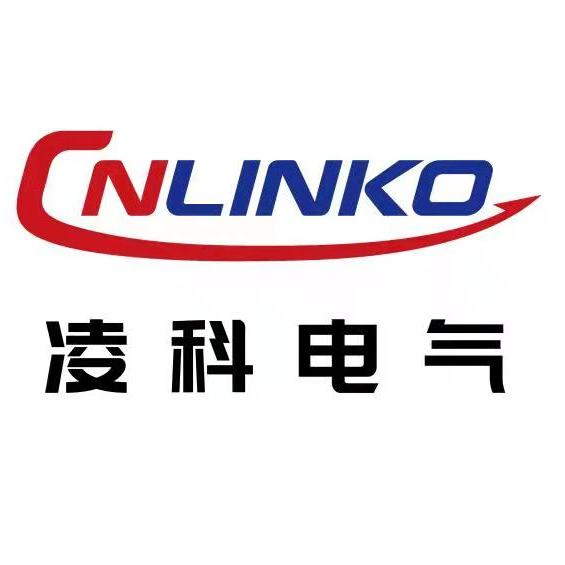
评论