随着工业4.0和智能制造的兴起,PLC控制系统作为工业自动化的基石,正面临着前所未有的发展机遇。
1. 技术革新
1.1 高性能处理器
随着微处理器技术的发展,PLC的处理器性能得到了显著提升。现代PLC通常采用多核处理器,能够处理更复杂的算法和高速数据流,满足高速、高精度控制的需求。
1.2 更大的存储容量
随着控制逻辑和数据量的增加,PLC的存储容量也在不断扩大。这使得PLC能够存储更多的程序代码、历史数据和诊断信息,为系统分析和优化提供了更多可能。
1.3 高分辨率和高精度
现代PLC系统支持高分辨率和高精度的输入/输出模块,能够实现更精细的控制和测量,满足精密制造和质量控制的需求。
2. 通信与网络化
2.1 以太网通信
以太网已成为PLC通信的主流技术,它提供了高速、可靠的数据传输能力,支持大规模分布式控制系统的构建。
2.2 无线通信技术
无线通信技术,如Wi-Fi、蓝牙和ZigBee,正在被越来越多地集成到PLC系统中,以实现设备的无线连接和远程监控。
2.3 物联网(IoT)集成
PLC系统正逐渐与物联网技术融合,通过集成传感器和执行器,实现设备的智能监控和远程控制。
3. 软件和编程
3.1 编程语言的标准化
IEC 61131-3标准为PLC编程语言提供了统一的框架,包括梯形图(Ladder Diagram)、功能块图(Function Block Diagram)等,这促进了不同PLC系统之间的兼容性和互操作性。
3.2 面向对象编程(OOP)
面向对象编程技术的应用使得PLC程序更加模块化和易于维护,提高了程序的可重用性和灵活性。
3.3 软件集成与仿真
现代PLC系统通常集成了高级编程软件和仿真工具,支持离线编程和调试,缩短了系统开发和调试的时间。
4. 安全性与可靠性
4.1 网络安全
随着PLC系统越来越多地接入网络,网络安全成为重要议题。现代PLC系统提供了多层次的安全措施,包括防火墙、VPN和加密通信等。
4.2 冗余和容错
为了提高系统的可靠性,PLC系统采用了冗余设计和容错技术,如双机热备、三重模块冗余(TMR)等,确保关键控制任务的连续性。
5. 集成与兼容性
5.1 与MES/ERP系统的集成
PLC系统正越来越多地与制造执行系统(MES)和企业资源规划(ERP)系统集成,实现生产数据的实时共享和优化。
5.2 跨平台兼容性
随着不同制造商PLC系统的标准化,跨平台兼容性问题得到了改善,用户可以更容易地集成不同品牌的PLC产品。
6. 人工智能与机器学习
6.1 智能控制算法
PLC系统开始集成智能控制算法,如模糊逻辑、神经网络和遗传算法,以实现更复杂的控制策略和自适应控制。
6.2 机器学习
机器学习技术的应用使得PLC系统能够从历史数据中学习,优化控制参数,提高系统的响应速度和效率。
7. 环境与能效
7.1 能效优化
随着环保意识的增强,PLC系统在设计时更加注重能效,通过优化控制策略和减少能耗来降低生产成本。
7.2 环境监测
PLC系统可以集成环境监测传感器,实时监控工厂环境,确保生产过程的环保和安全。
结论
PLC控制系统的最新发展趋势表明,它们正在变得更加智能、互联和高效。随着技术的不断进步,PLC系统将继续在工业自动化领域扮演关键角色,推动制造业向更高层次的智能化和自动化发展。
-
PLC控制系统
+关注
关注
1文章
65浏览量
15819 -
工业自动化
+关注
关注
17文章
2368浏览量
67218 -
工业4.0
+关注
关注
48文章
2012浏览量
118602
发布评论请先 登录
相关推荐
智能密集架控制系统技术发展趋势
黑芝麻智能亮相2024高端芯片产业创新发展大会
PLC控制系统与DCS的区别
飞凌嵌入式受邀亮相TI嵌入式技术创新发展研讨会
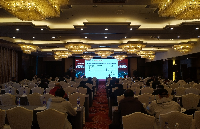
评论