在当前产能相对过剩、行业形势严峻、国内国外形势复杂的情况下,原来产线产能粗犷的复制投资戛然而止。各行业的节衣缩食、广泛裁员、推动节能降耗,已成为制造企业不得不面对的活下去的必经之路。然而当前如何在裁员的浪潮中保障产线效率,甚至提升生产力,成为摆在每一个企业面前的难题。
答案或许就藏在OEE管理体系之中——一种被低估的精益生产工具,它不仅是工厂的显示器,更是加速器,是企业逆境中的生存法宝。笔者根据PreMaint在自动化行业多年的实施经验,总结了一些相关经验给大家参考。
OEE管理体系:不只是报表
在离散制造业,OEE虽然并不陌生,但也被很多误解,认为OEE仅仅是一串数字指标核算,一套报表,甚至通过Excel导入导出的方式,认为实现了OEE功能。实则不然,OEE(Overall Equipment Effectiveness)是衡量工厂资产绩效的核心指标,它代表了设备的综合效率,是推进精益改善、消除异常浪费、改善单位能耗的有力工具。OEE管理体系的构建,是一个全面而深入的工程,它要求企业从多个维度出发,精耕细作,以实现产线效率的最大化。随着设备自动化、智能化程度的提高、AI算法的介入,OEE管理工具可以帮助生产管理者更清晰和准确地看到工厂的异常浪费和瓶颈,在哪些机台、哪些环节,从而更针对性地做出有效改进。
图:OEE指标拆解举例
例如,当不同数控设备,在不同员工的操作下,OEE有明显的差异,就要研究为什么会有这种差异,如何消除差异。再比如,车间反映现场某个工序设备产能不足,需要跟集团审批新增加设备采购,我们需要观察车间线体的OEE分布情况,通过数据分析,有可能得出不一样的结论,通过优化工序和前/后工序产能改善,或者专项维备耗改善,甚至只是简单的物流效率提升,而不是简单的采购设备,即可解决了瓶颈产能不足的问题。
图:OEE损失分类
工厂要运营好OEE管理体系,有下面的四个核心要素。
核心1:设备主体对象的清晰界定,并正确构建母子设备状态映射和OEE核算逻辑关系。这种设备间精益关系的构建,和我们日常资产管理、设备运维管理的关系逻辑并不相同,并且经常混淆。
首先,企业需要根据线体设备工艺关系,梳理清楚面向OEE核算的设备主体对象。这要求企业对生产线上的每一个环节都有清晰的认识和界定,防止在OEE的计算和分析中出现干扰和误导。例如,对于一条不可分割的组件装配线,不仅要关注总线的效率,还要细化到每一个分装站,甚至每一个工位的状态,构建总装线和子工位正确的“或”、“与”等虚拟关系,才能得出正确的母子设备状态承接关系,继而才能准确掌握线体和设备间的效率损失反应关系。
如图,SMT这个线体是不可分割的流式生产,大家可以思考,那么我们应该怎么判定SMT线体的整体状态和计算它的OEE?对丝印机台的Idel状态和贴片1机台的故障停机状态,如何处理?错误的分析逻辑将拿到错误的结果,从而影响OEE的改善。这里需要面向OEE特有的设备组合关系算法。
图:OEE设备关系示意
核心2:机况状态通讯代码的标准化细分与自动化获取。这个是不能省的基本功。
其次,对机况状态通讯代码的细分梳理和标准化至关重要。企业需要建立一套详尽的设备机况切换通信代码体系,以便于对设备的每一种状态进行精确的分类和记录,确保通信数据和实际状态完全一致。同时,通过自动化技术实现这些数据的实时获取和分析,避免无效干扰。例如,PreMaint内置了行业常见的机况标准代码体系和机况数据采集技术,设备的状态可以实时反馈到中央监控系统,从而实现对设备状态的实时监控和机况自动切换,也可以手动模式切换。PreMaint-OEE可以根据细分机况自动归类计算。如果依靠传统手工报表对停机和呆滞原因分析,通常是不可信和不完善的,从而误导改善方向和现场决策。
表:机况状态通信代码标准示例
核心3:OEE改善过程贯穿于工厂的报警管理、履历追溯、生产监控、节拍管理、精益管理、指标分析以及产能管理等制造运营过程的各个方面,需要全场景、集成化的OEE体系管理模块来指导和实现工厂的降本增效。
在当前数据驱动智能制造的运营模式下,全场景、集成化的OEE管理模块是当前数字化精益管理的必然趋势。
例如,当前设备的报警文本定义和报告严重依赖于设备厂商的自定义模式,而且不同厂商的设备无法实现标准统一,我们需要通过系统转换统一标准。
再比如,设备完整的生产状态履历是一切精益分析的源头,现有的EAP、AMS、PMS、MES等系统的设备数据需要直接拧成一条完整的生产状态履历。传统的设备节拍掐表观察计算的方式费人费时费力,而且数据准确度和异常感知度普遍较低。我们需要根据统计算法计算,实现标准节拍全流程自动化管理。
报警、保养、待机、在工、生产进度、生产型号、目标节拍和瞬时节拍等等,这些关键运营数据时刻影响OEE结果和产能实绩,所以,一个统一集成的管理模块可以让运营担当、管理者更快的发现异常减少损失,管理者复盘过往的OEE和产能损失,既要能快速从指标分析中了解结果,也需要快速通过监控履历的验证过程来挖掘隐藏在数据中的管理问题点。
另外,因为设备状态报告错误(人为切换或者作业反复等)或者断续生产(投入不稳定或设备不稳定等),系统必然存在大量的生产履历无效数据,对分析和决策形成很大干扰,我们需要通过数字化的精益管理逻辑和算法,来过滤处理这些无效数据,从而提高分析业务精度。
以上种种场景和解决方案,都是在OEE推行中,企业经常面临的现实问题。
图:OEE闭环体系
核心4:构建完善的设备工程数字化平台,支撑OEE不断完善的闭环体系
很多企业对设备管理,还停留在MES里有一个台账管理、保养管理,EAM里有个资产管理等这样的系统架构认识,远远不能满足设备智能管理的需求。当前设备健康管理、智能工程平台为代表的新一代设备数字化平台,适配设备智能化发展趋势,逐步成为企业现场设备数字化管理的核心架构。
以格创东智的PreMaint设备智能工程套件为例,它包括设备自动化控制(EAS、SCADA等)、加工参数配方管理(RMS)、设备中央监控(CMS)、过程控制优化(APC)、设备综合效率分析(OEE)以及设备预测维护(PHM)、保养及备件管理(PMS)、工装模具管理(MM)等多个模块。这些模块化套件,内嵌AI算法,不仅实现了设备的自动化控制,还提供了设备和制程数据的实时采集监控、制程参数管理、根据机况和工艺的参数寻优、工艺优化和预测维护等功能,从而全面提升了设备的运行效率、制程过程良率,从而提升产线的整体OEE水平。这个也是企业从传统精益,迈向数字化精益的重要标志。
图:PreMaint设备智能工程套件
需要注意的是, 在实施OEE管理体系的过程中,企业应根据自身的实际情况,有针对性地选择重点工作和系统模块。千里之行,始于足下。对于那些生产线自动化程度较低的企业,可以先从自动化控制和数据采集入手,实现工厂数据的精准化管理。百尺竿头,更进一步。对于已经具备较高自动化水平的企业,则可以通过数字化精益管理模式导入来进一步优化制造和运营过程的控制管理,继而实现设备维保效率的提升。
在当前充满挑战的时代,OEE管理体系不再只是一个简单的指标计算和数据报表呈现。根据企业当前阶段,导入设备智能平台不同的模块方案,能够帮助企业提升产线效率的终极武器。通过精耕细作,构建完善的数字化OEE精益管理体系,企业可以在逆境中找到生存和发展的新路径,实现资产投入产出的最大化,顺利穿越行业下行周期!
-
数字化
+关注
关注
8文章
8905浏览量
62316 -
OEE
+关注
关注
0文章
10浏览量
6265
原文标题:OEE管理体系:精益生产的终极武器
文章出处:【微信号:数字化企业,微信公众号:数字化企业】欢迎添加关注!文章转载请注明出处。
发布评论请先 登录
相关推荐
华为通过BSI全球首批漏洞管理体系认证

精益生产如何在数字化时代焕发新生?创新路径全解析
解锁精益生产,照亮LED的智能制造之路!
数字化技术如何加速精益生产策略的实施与成效?
本源量子获得质量管理体系认证证书
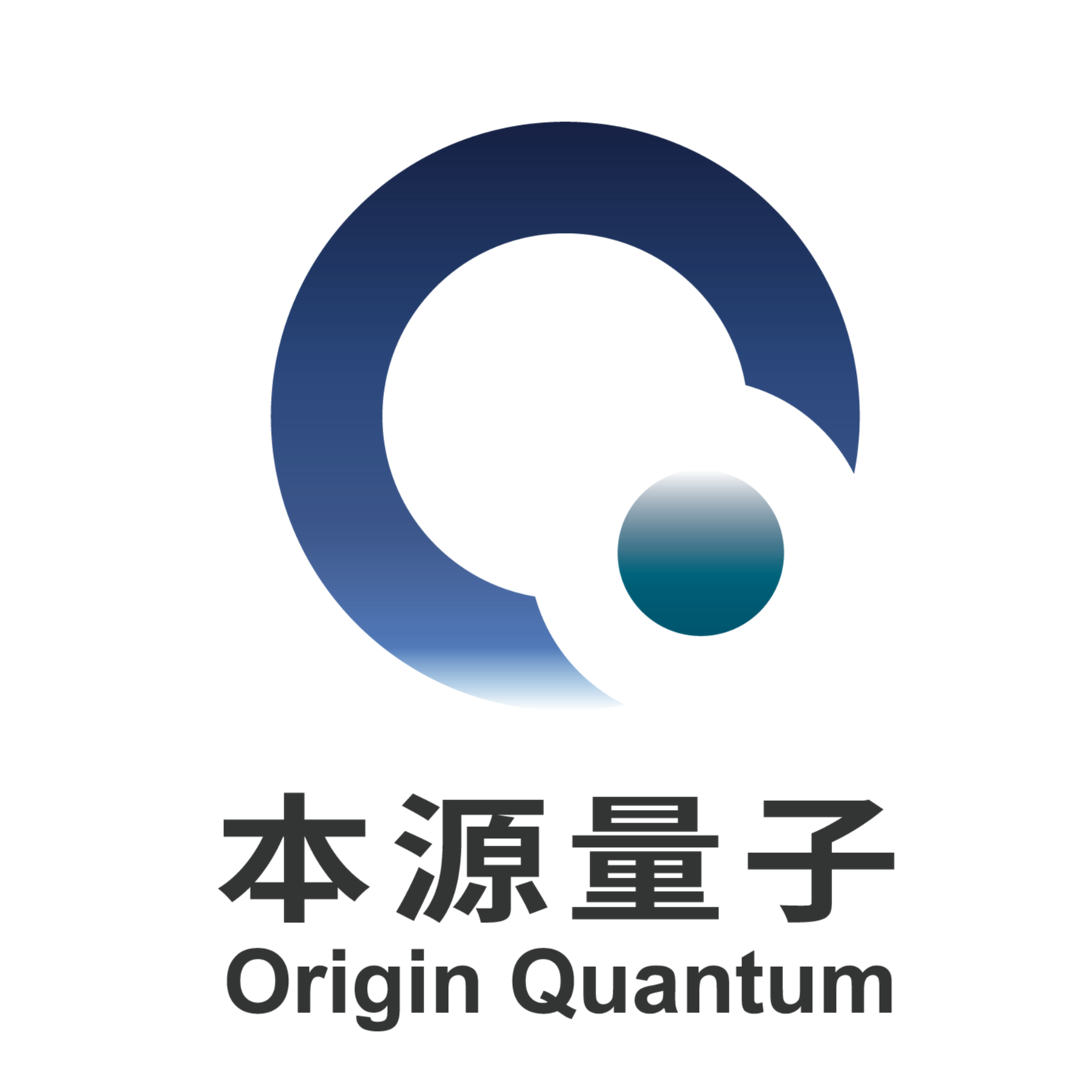
评论