智能工厂是在数字化工厂的基础上,利用物联网技术和监控技术加强信息管理、服务;提高生产过程可控性、减少生产线人工干预,以及合理计划排程。同时集合初步智能手段和智能系统等新兴技术合为一体,构建高效、节能、绿色、环保、舒适的人性化智能工厂。
1、传统工厂:人工统计,效率低且不准确
在中国很多传统的中小型工厂中,对于设备生产数据的采集,几乎依靠人工完成。流动的人员、散落的数据,导致数据的保存成了一个巨大的问题。同时人工统计的效率也非常低,往往都是每天下班或者每周进行一次统计,完全不能进行实时生产数据更新。
此外,数据对于设备而言有着时效性和历史数据参考性的关键作用,从底层操作工的数据记录-数据分析-数据反馈-管理者的决策,中间的环节让数据的时效性大大降低,同时人工的记录统计也会造成数据不准确等问题,而且庞大的数据计算分析,对于人力是一个非常大的耗损。
其次,历史数据对于设备的维护具有参考性的意义,但是传统工厂的数据,靠着一张张的记录纸或者大量的Excel表无疑是给未来的工作又增添了不少难度,而且工厂不能控制人员的流动,每一次的交接都可能导致数据的流失。
2、数字化工厂:设备联网,数据自动上传反馈
而在数字化工厂中,物联网的概念就被运用到每一台设备上。设备与设备之间,早已不是信息孤岛,而是将人、设备,通过数据建立紧密联系。一个工厂管理者可以在手机或者PC终端观测到每一台设备的实时数据,而且可以随时收到设备的状态提醒。异常出现时通过微信/短信/邮件/看板等方式自动警示,包括:Cpk指标/不良件指标/缺陷指标/直通率指标预警等来通知管理者。
比如你设置了注塑机某个模块的注胶温度超过70度,提醒温度过高。当注胶温度接近70度时就会收到预警,当高于70度时,就会立即收到设备报警。进一步实现收集、分析、反馈的同步进行,大大缩短时间,提高决策的效率。
除了收集、计算、反馈等“去工人化”的功能,设备联网以后,还有一大好处就是数据存储。大量历史数据,包括设备损失数据,也给后期工厂设备的很多操作提供了参考意义。之后,再遇到工厂的人员流动,这些数据仍然可以随时调用并妥善保存。
3、传统工厂:设备意外停机频发,造成大量损失
除了数据的管理问题,传统工厂还有一大痛点,那就是经常遭遇设备意外停机。设备的意外停机不仅造成了生产的停滞,而且对于设备造成的隐性破坏不可估量。
为了防止设备意外停机,工厂通常安排了24小时的轮班工人巡检,造成了工厂人力耗损严重。每时每刻的巡检也并不能全面检测到可能导致设备意外停机的各种因素。传统工厂通过手摸、耳听等原始的方式,这样的检查方式不够精准以及无法快速解决问题,导致工厂的损失大大加剧。
其次,由于害怕意外停机带来的严重损失,很多工厂也会购买大量的备用零部件,以防止意外停机的维修需要,而现实情况又是一些设备的意外停机故障周期很长,导致大量的备用零部件并没有派上用场,造成成本浪费。
4、数字化工厂:设备意外停机及时预警通知,让设备时刻保持最佳运行状态
数字化工厂的运转过程中,设备的一切都被随时监控反馈,而意外停机发生之前,设备的某些参数会发生变化,此时设备就能在参数发生变化时及时进行预警通知,让设备故障在发生之前被发现且及时运维。也就是说,在故障发生之前,手机上就能收到相应的提醒,方便操作人员立即作出决定,从而保证工厂设备时刻处于最佳运行状态。
即使是故障已经发生了,也能在过去的设备故障统计分析里立即找到合适的解决方案,把损失降到最低。这也就是数字化工厂实现的重要一步,让预知未来成为智能工厂的一部分。
审核编辑 黄宇
-
智能工厂
+关注
关注
3文章
993浏览量
42397 -
数字化工厂
+关注
关注
1文章
59浏览量
6165
发布评论请先 登录
相关推荐
CNC智能工厂如何实现
如何搭建智能制造工厂
高精度工厂人员定位,打造数字化智慧工厂
智能工厂的优势不包括哪些
智能工厂的架构及ERP的基本功能是什么?
什么是智能车间和智能工厂 它们有什么区别
数字工厂与智能工厂是一回事吗
智能工厂和数字化车间的区别
智能工厂(物联网工厂)是什么
IIoT可以通过多种方式实现智能工厂(还有一些挑战)
格科微临港工厂通过“智能工厂”认定
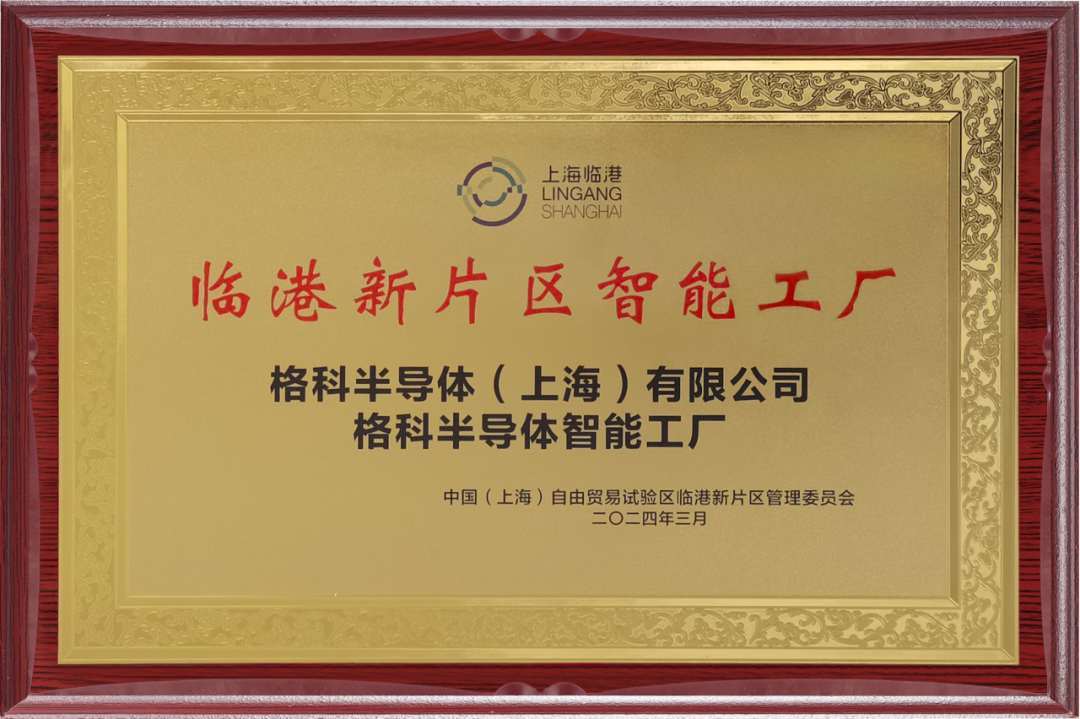
评论