文章链接:https://doi.org/10.1063/5.0172805
摘要
薄(100nm厚)疏水聚合物薄膜被用于许多需要防水的应用。然而,由于耐久性差,疏水薄膜的实现受到限制。薄疏水膜在冷凝过程中起泡已被认为是与失效相关的主要机制之一。然而,关于起泡形成的来源还存在着分歧。此外,人们还缺乏对促进蒸汽通过薄疏水薄膜渗透途径的物理缺陷或针孔的了解。这些针孔控制着在疏水聚合物和金属基板之间的界面上的水泡的成核。在这里,我们使用金属电沉积作为一种手段来表征这些固有的针孔在薄疏水聚合物。证明了一种简便的方法来在CFx和聚(聚氯二乙烯)(聚对二甲苯C)薄膜上定位针孔和测量针孔密度。我们的工作不仅有助于理解与薄膜沉积相关的内在缺陷,它也为高效薄膜疏水涂层的选择和开发提供了设计指导。
介绍
薄膜聚合物具有优异的热绝缘性能,气阻隔能力,和化学和热稳定性。因此,这些材料和涂层长期以来被用于有机发光二极管(OLED)中的柔性基底,生物医学设备和包装中的保护膜,和表面冷凝器上的传热增强涂层。特别是,需要防水的连续排水的系统已经广泛使用疏水聚合物。例如,疏水薄膜在蒸汽凝结过程中增加了热传递,在蒸汽凝结过程中,由于这些表面具有的水排斥性产生的引力,液滴成核、合并并从表面脱落。由于疏水薄膜的低表面能而形成的离散液滴有助于液滴的成核和去除。滴冷凝现象克服了经历薄膜冷凝的亲水金属冷凝器的挑战。薄膜式冷凝,即在冷凝器表面形成连续的液体膜,阻碍了离散水滴的进一步成核,并增加了相对于等效尺寸的滴式冷凝器更高的整体热阻。聚合物涂层体系的预期寿命对性能提出了严格的要求,这依赖于这些聚合物薄膜极低的氧渗透性或蒸汽含量。当涉及到冷凝器涂层时,具有商业耐久性的疏水聚合物薄膜尚未实现,因为大多数100纳米薄膜在运行几小时内失效。
薄聚合物薄膜的失效机理已被描述为脱湿、起泡、和分层。薄膜(<10纳米厚)会发生去湿现象,此时水对亲水性基材的亲和力更高,会将涂层推开。然而,对于较厚的膜(>10nm厚),起泡被认为是主要的失效机制。在起泡过程中,水在聚合物表面下滴下单核,并扩散到薄膜从衬底上完全剥离。腐蚀引起的起泡是聚合物涂层金属表面的常见现象,腐蚀产物会导致水泡形成。
由于非腐蚀性衬底上存在离子,因此有人声称会在非腐蚀性衬底上引发水泡。然而,这一机制并不能解释为什么不同的聚合物具有不同的寿命,而不管其衬底的化学性质和粗糙度如何。此外,一些研究人员声称,扩散是水分通过薄膜转移的主要机制,最终导致水泡。与此相反,扩散的时间尺度与分层的时间尺度有显著的不同。例如,考虑100nm厚的聚合物膜,菲克定律的扩散时间尺度为τ≈h2/Dm=10-4∽10-1s,其中h是膜厚度,Dm是聚合物膜中水汽的扩散系数[我们认为值从Dm=10-13m2/s(聚酰亚胺)到Dm=10-10m2/s(醋酸纤维素)]。虽然根据扩散时间尺度,分层应该是瞬时的,并且聚合物薄膜扫描在缩合起始后持续数小时。这种时间尺度的差异暗示了聚合物中的物理缺陷或针孔,它们可以作为蒸汽到达基底的运输途径。过去的研究表明,水泡可以在人工针孔上启动,并且分层是由厚度依赖的静水压力驱动的。然而,不知道聚合物薄膜上固有针孔的本质,这控制着沉积薄膜上的内在泡,减少了开发和改进涂层的过程到严格的试验和错误。
疏水薄膜中针孔缺陷的表征对于制定标称可接受缺陷的标准和设计起泡形成的有效屏障以提高薄膜的耐久性至关重要。由于气泡和污染物的随机缺陷已被观察和报道。然而,在疏水性涂层内的缺陷密度及其空间分布尚未得到研究。针孔缺陷密度可以提供关于涂层的预期寿命的信息,而无需对冷凝器涂层进行长期测试,这可能是耗时和昂贵的。非导电性和非常薄的聚合物薄膜的性质使得针孔缺陷更难以探测。本文报道了疏冰聚合物CFx、疏水聚对二甲苯C的缺陷密度。我们使用固有针孔作为铜微结构的成核和生长通道,使针孔位置在扫描电子显微镜(SEM)和光学显微镜(OM)下可见。我们使用聚焦离子束(FIB)铣削结合SEM进行针化测量。我们的工作阐明了控制薄膜固有缺陷的机制,并为高效薄膜疏水涂层的选择和开发提供了设计指导。
实验部分
我们考虑了两种不同的聚合物薄膜,CFx沉积的振动粒子增强化学气相沉积(PECVD)和通过化学气相沉积(CVD)沉积的聚(2-氯-对二甲苯)(聚对二甲苯C)。选择这两种薄膜可以更好地了解它们的相对缺陷密度和沉积过程对各自薄膜质量的影响。此外,CFx是一种氟化薄膜化学物质,而聚对二甲苯C是一种非氟化分子。图1(a)描述了在CFx上制造Cu微结构的过程。镜面多用途110铜片(McMaster-Carr)用作所有沉积工艺的衬底。适当的处理和清洁抛光的铜基质是至关重要的,以使颗粒污染在沉积过程中引发针孔,保持到最低限度。虽然陶瓷和聚合物的沉积机制不同,但考虑到颗粒仅仅作为物理阻断剂,禁止任何材料在基底上沉积,颗粒导致的针孔形成机制是相似的。因此,陶瓷和聚合物的位置都会形成针孔。
图1.(a)通过针孔制备铜液滴的制备工艺示意图。示意图不能缩放。在薄膜生长过程中,由于制造过程中的缺陷而产生针孔。随后在电沉积过程中,Cu通过针孔生长。接收和清洗的(b),铜上的(c)在铜上的498nmCFx薄膜(d)490nm聚对二甲苯C薄膜的原子力显微镜图像。接收到的Cu、CFx和对苯二甲苯C的表面粗糙度Rq值分别为8.8、7.8和18.5nm
此外,我们还保持了类似的沉积条件(样品在沉积室内的位置和样品数量),以尽可能地消除外部效应。在沉积之前,铜标签通过四个步骤进行清洗。首先,用丙酮清洗标签,然后是异丙醇(IPA),水,最后再次是IPA。清洗后,铜片在丙酮中超声以适当地脱油脂。CFx薄膜通过等离子体深反应离子蚀刻工具(ICPDRIE-等离子体热)沉积,其中C4F8和固化酶作为反应气体。等离子体中存在的CF3+、Ar0和F-自由基形成保形CFx层。具体来说,我们沉积了101±37到4986±15nm厚的非晶态氟化聚合物(CFx,x≈1)氟碳薄膜。
聚对二甲苯C沉积在SCS聚对二甲苯涂布器中,以二对甲苯-二甲苯二聚体作为引发剂。沉积的聚对二甲苯涂层厚度为100±29~501±16nm。
结果与讨论
图1(a)描述了我们的制造方法的示意图。针孔是通过薄膜上的孔或物理缺陷,将底部亲水铜衬底暴露在离子溶液中。因此,针孔和任何裂缝或空隙都是亲水部位,可以被溶液弄湿,而聚对二甲苯C包膜保持干燥。在电沉积过程中,溶液中的Cu2+离子由于应用电位而向样品迁移。这些离子通过针孔扩散,到达导电衬底,引发铜的成核。铜离子通过低缺陷密度的惰性保护膜,如聚对二甲苯C的扩散是非常不可能的,因为聚对二甲苯C膜阻碍Cu2+离子穿透的时间超过了我们研究的研究时间范围。此外,与扩散相关的成核在整个表面都是全局的。然而,在我们的案例中,由于聚合物薄膜中针孔和裂纹的随机和局部分布,铜的成核高度局限于薄膜上。在涂层和铜基底形成的界面上暴露的导电位点上的核酸。最后,铜通过针孔生长,并在薄膜的顶部呈液滴状的形状突出。铜浓度随着时间的推移而生长,随着电沉积时间的延长(>50min),铜浓度可达100μm。电沉积70min后,表面通过涂层被铜生长完全饱和。在电沉积过程中,最初在导电铜衬底上形成的铜岛的演化与时间依赖,并遵循一阶动力学增长。在没有聚合物涂层的导电基板上,Cu以孤立的岛生长,岛的数量随着时间的推移而增加。Cu岛的成核遵循一级动力学过程,可以表示为:Nt=N0(1-exp(Knt)),其中Nt为t时刻的铜岛数,Kn为成核速率,N0为饱和时的Cu岛数。因此,在我们的样品上的铜成核也表现出时间依赖性,并且成核并没有同时在所有的针孔处开始。
在我们的例子中,虽然成核位点或岛的数量受到针孔密度的限制,但仍然可以观察到Cu滴成核的时间依赖性(图2)。而电压和电流影响了铜液滴的形态和生长速率,我们保持了一个固定的电压输出,以保持样品之间的成核动力学近似相似,以抵消潜在效应。在电沉积的初始阶段,铜的微观结构呈圆形,类似于在凝结过程中在非润湿基质上成核的水滴[图2(b)]。然而,根据所用的电压,可能会出现不同的形态。在大量生长之后,由于在可能存在大量针孔的高度局部化区域中的接近,铜液滴可以合并[图2(d)]。
图2.电沉积前(a)、10min后(b)、20min电沉积后(c)、40min电沉积后(d)的光学显微镜图像(10)。图像中的黑圆圈是生长在具有470nm厚度的CFx薄膜上的铜液滴。在(a)到(d)中显示的图像被放大,并没有用于获得数字密度数据。它们旨在显示铜随着时间的推移而增长。(e)铜液滴密度随电沉积时间的函数。45min处铜液滴的密度是CFx薄膜的最终固有针孔密度。x轴的不确定度条小于符号的大小,并且没有显示出来。
在CFx薄膜上,在40min后,Cu液滴的数量没有增加[图2(e)]。由于团聚体的形成,随着液滴的空间扩散,每一个液滴的特征变得复杂[图2(c)]。在这一点上,我们假设铜的成核遍布于暴露的铜活化位点,因此,液滴的数量近似表示CFx膜中针孔的密度。
图3显示了CFx和聚对二甲苯C涂层的总针孔密度与薄膜厚度的函数。薄膜的厚度取决于二聚体(聚对二甲苯C)的质量和沉积时间(CFx)。对于这两种聚合物薄膜,针孔密度均随薄膜厚度的增加而减小。这些聚合物是通过链生长机制沉积的,其中单体被添加到自由基链上,而在阶梯生长机制中,如果满足条件,可以在任何两个相邻的分子之间发生反应。当单体被吸附在表面时,它们可以到达现有的聚合物链,并通过过量的能垒附着在那里,或通过聚合物岛分散,找到另一个活性位点。否则,单体可以与其他单体发生反应,形成一个新的聚合物岛。聚合物的传播、单体分散和新的聚合物引发作用同时发生,这取决于单体的化学、动力学和各自过程的能垒。在这种反应中,空间扩散和分层生长同时以一种依赖于生长动力学的竞争方式发生。因此,随着厚度的增加,表面的聚合覆盖范围增加,导致物理缺陷减少。此外,在聚对二甲苯C中观察到的针孔密度比CFx薄膜低一个数量级以上,这是由它们各自的生长机制引起的。CFx薄膜由PECVD培养,利用等离子体蚀刻和沉积同时生长速度快。由于血浆的化学降解,PECVD鞘酶中功能物种的保留率低于CVD过程。虽然聚对二甲苯C被宣称没有针孔,但在许多情况下,这取决于膜的覆盖率,因此也取决于膜的厚度。当厚度接近∽1μm时,我们观察到总针孔密度显著降低。此外,与CFx相比,聚合物的链传播速率要高得多,这可能决定了观察到的更高的覆盖率。
图3.CFx和聚对二甲苯C的针孔密度随涂层厚度的变化,其固有针孔密度随厚度的增加呈下降趋势。聚对二甲苯的针孔比CFx少,因为在沉积过程中表面覆盖率更高。x轴不确定度条小于符号大小,没有显示。
图4描述了使用ThermoScios2双光束扫描电镜/FIB,在0.1nA电流和2kV电压下获得的铜液滴的扫描电镜图像。图4(a)显示了CFx薄膜(540nm厚)上缺陷分布的扫描电镜图像。在0.15-0.3V的电沉积电位下,沉积的铜液滴具有多孔泡沫样形态。随着电沉积电位的增加,树突的出现和突起的团聚体被观察到。这些封闭的三维结构的出现可以归因于过电位。铜微观结构的形态取决于析氢和铜沉积之间的竞争反应,其中析氢可以抑制铜的沉积。
图4.在500放大倍数下拍摄的局部区域的CFx上针孔分布的(a)SEM图像。(b)铜液滴的横截面,显示液滴中心的针孔位置(5000的放大倍数)。(c)在(b)中确定的针孔的高倍扫描电镜,作为Cu沉积的通道和Cu液滴生长在CFx膜的顶部。CFx薄膜的厚度为470nm,电沉积时间为20min
为了研究针孔的几何形状和尺寸,我们使用相同的Scios2FIB设备,使用50kV和0.1nA离子束对Cu液滴进行了边对边的铣削。FIB图像显示,铜液滴首先填充针孔,然后从薄膜中生长出来,形成一个半球形。铜液滴通过半球形扩散向外生长[图4(b)]。通过连续铣削,可以近似于铜液滴的中心。根上有针孔,这是铜最初生长的途径。图4(c)中指示的红框显示了一个这样的针孔,该针孔大约位于图4(b)中所示的液滴的中心。在某些情况下,由于涂层的不一致,有核的铜碰撞可以在穿透涂层形成涂层之前大量形成最终的半球形结构。铜液滴是多晶的,由大小从几纳米到微米的晶粒组成。随着晶粒向针孔的径向延伸,可以观察到一些各向异性。通过FIB-SEM分析,我们可以确定每个薄膜的针孔尺寸,CFx的尺寸在≈50-200nm范围内,聚对二甲苯C的尺寸在70-150nm范围内。
我们的方法揭示了薄疏水薄膜的失效动力学。在缩合过程中,疏水膜不能从支撑衬底上分层。这种失效机制可以通过两个步骤来描述:(1)泡起始和(2)泡生长导致分层。过去的工作研究了起泡的起始,并建立了起泡(Ω)的标准,它确定了针孔中的凝聚核是否会在针孔顶部以水泡或冠状物的形式生长。
式中,Rb0为初始分层泡罩半径,Rd为松松半径,γ为冷凝物的液蒸气表面张力,E为薄膜的杨氏模量,G为薄膜与基底之间的界面附着力,h为薄膜的厚度。更厚的薄膜,更高的弹性模量,和更高的附着力有助于防止水泡的发生。无论具有优异的物理性能,针孔暴露部位都将开始凝结。生长可以使用更厚和更硬的薄膜来延迟,但由于针孔的存在而不能被阻止。因此,除了材料的热物理性质外,针孔密度是表征耐久性的关键。因此,如果一个水泡开始,其生长表现如下:
其中,Rb(t)是与时间相关的泡罩半径,JV是蒸汽质量通量,被认为是恒定环境条件下的一个常数。针孔半径越大,泡罩越大。此外,水泡的生长导致水泡合并,导致局部分层。更高的针孔密度会增加泡疱聚结的可能性,从而导致疏水膜分层更快。更多的针孔的总面积覆盖将引发更多的分层区域。最终,局部分层区域导致薄膜从衬底上的整体分层。
对于疏水表面单位面积的N个针孔,根据泊松分布,最近针孔之间的平均距离为d=1/(4N)½当半径rb合并时发生分层,因此分层过程中针孔之间的平均距离等于水泡直径d=2Rb。使用这个条件并将其替换为等式(2),我们得到了一个剧烈的退化时间
从等式(3)中,我们看到起泡时间是t∽N-3/2和t∽Rd-2。因此,最小化针孔尺寸和针孔密度对于提高蒸汽凝结过程中的耐久性都很重要。然而,针孔的尺寸对分层时间的影响大于针孔的数量密度。
为了支持我们的论点,我们进行了持久性测试,以确定启动水泡所需的时间。我们使用了两个镀有100和1000nm厚的聚对二甲苯C薄膜的铜片。然后,我们将样品放置在一个定制的蒸汽冷凝室中。100nm厚的样品在蒸汽冷凝不到24小时内失败,而1000nm厚的样品持续时间超过1080小时。从实验结果中,我们可以看到1000nm样品的耐久性比100nm厚的样品高出两个数量级以上。根据等式(3),利用我们的冠状密度数据考虑到泡的直径是相同的数量级,1000nm样品的泡降解时间理论上应该比100nm厚的样品高三个数量级,这与实验结果很好地一致。
从我们的针孔密度和水泡形成分析中获得的基本知识揭示了几种增强疏水薄膜可凝性的策略。一个重要的策略是使用多步沉积过程,而不是单层沉积。沉积过程中形成的多层应具有随机的空间针孔分布,可能导致层间针孔错位,从而形成蒸汽渗透的曲折路径。因此,蒸汽不能通过一个连续的路径来成核并形成水泡。多层应该优化等式(1)中概述的物理性能。基于这一发现,我们使用类似的方法创建了铝层氟化金刚石类碳涂层(FDLC),在铜电沉积过程中发现没有可见的铜液滴。因此,涂层中持续的疏水性可以部分归因于针孔的缺失。我们的方法适用于大多数附着力合理的疏水性涂料。然而,由于使用非常薄的疏水薄膜(<100nm),在液滴生长过程中快速分层,该方法失败了。
结论
总之,我们展示了一种简单的疏水聚合物薄膜的前物理缺陷技术,它控制了冷凝过程中的失效机理。我们的研究结果提供了有关具有各自耐久性的聚合物薄膜的有效性的信息。其他更传统的耐久性测试,如稳定冷凝实验到失败,包括进行数月或数年的实验,这可能是昂贵和耗时的。相反,铜在聚合物薄膜上的电沉积为我们提供了关于薄膜的原始程度的信息,而无需进行耗时的测试。此外,我们的方法可以提供关于理想的加工和沉积条件的信息,以创造无缺陷或最小缺陷的涂层。总的来说,用于针孔可视化的电沉积棒联体可以帮助正确表征疏水薄膜的潜在应用。
-
薄膜
+关注
关注
0文章
293浏览量
29308 -
纳米
+关注
关注
2文章
697浏览量
37025 -
函数
+关注
关注
3文章
4333浏览量
62708
原文标题:纳米级针孔缺陷的性能研究
文章出处:【微信号:深圳市赛姆烯金科技有限公司,微信公众号:深圳市赛姆烯金科技有限公司】欢迎添加关注!文章转载请注明出处。
发布评论请先 登录
相关推荐
Aigtek功率放大器如何帮助制备(1~100nm)级的纳米薄膜
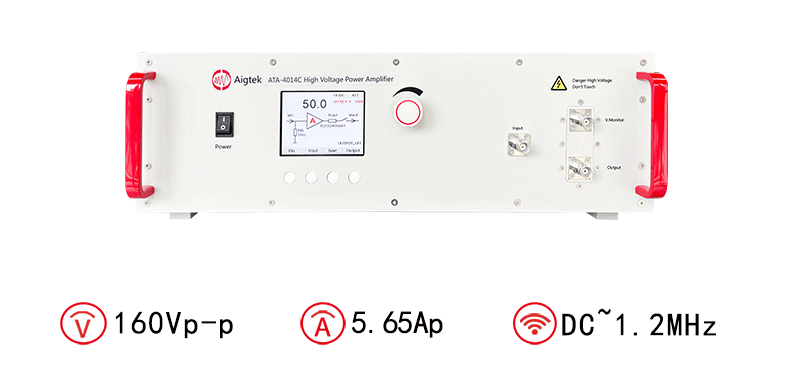
碳纳米管的结构与特性解析 碳纳米管在能源储存中的应用
安泰功率放大器如何帮助纳米材料领域进行创新研发
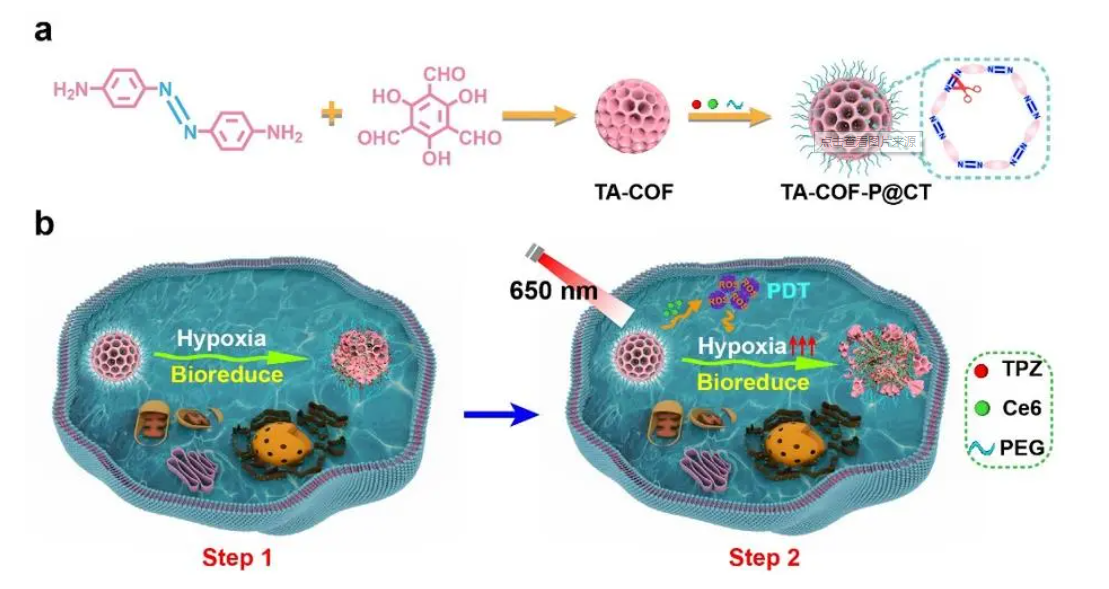
中国科大在纳米级空间分辨红外成像研究中取得新进展
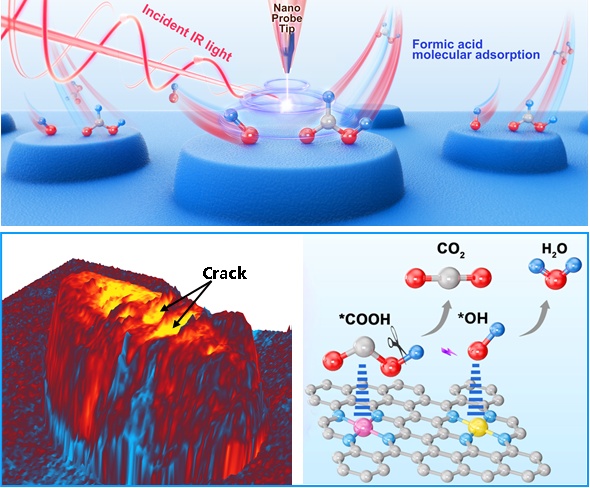
麻省理工学院研发全新纳米级3D晶体管,突破性能极限
中国科大在纳米级空间分辨红外成像及催化研究中取得新进展
SK海力士开发出第六代10纳米级DDR5 DRAM
纳米级材料尺寸测量:从微观到宏观,纳米精度,中图智造
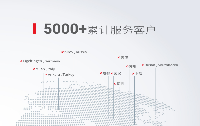
纳米级材料尺寸如何测量?
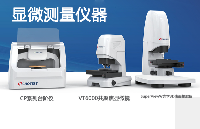
台阶仪:亚埃级垂直分辨率,新材料纳米加工的测量利器!
台阶仪:亚埃级垂直分辨率,领跑新材料纳米加工的测量利器!
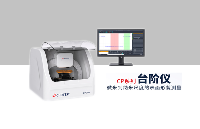
高精度纳米级压电位移平台“PIEZOCONCEPT”!
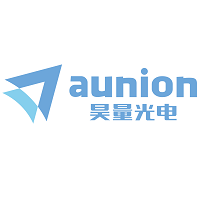
评论