功率模块封装工艺
典型的功率模块封装工艺在市场上主要分为三种形式,每种形式都有其独特的特点和适用场景。以下是这三种封装工艺的详细概述及分点说明:
常见功率模块分类
DBC类IPM封装线路
传统灌胶盒封与双面散热模块
1
常见功率模块分类
一、智能功率模块(IPM)封装工艺
工艺特点:
塑封、多芯片封装,包括ICBT、FRD及高低压IC等元器件。
采用引线框架、DBC(直接敷铜板)、焊料装片、金铝线混打等工艺。
目标市场为白电应用、消费电子及部分功率不大的工业场所。
封装类型:
纯框架银胶装片类:主要用于小功率家电电源、水泵调速变频控制等场合。基于传统IC封装方式,采用铜线内互联和全塑封。
纯框架软钎焊和银胶混合装片类:具有散热片(一般为陶瓷),功率芯片采用粗铝线,芯片控制部分采用金铜线内互联。适用于白电变频调控的大多数场合。
特殊工艺:
散热片安装工艺:采用硅胶黏结陶瓷片后烘干,需控制点胶涂布的均匀性、加热和加压,保证可靠连接并控制气泡及厚度。
绑线夹具设计:先做铝线,因其刚度好,可抗倒伏。
金铜线压板设计:需避开已绑线的铝线区域,抬高打线区域。
二、灌胶盒封功率模块封装工艺
工艺特点:
一般采用DBC、粗铝线或粗铜线键合、铜片钎接等工艺。
焊料装片或银烧结工艺,端子采用焊接压接方式。灌入导热绝缘混合胶保护,塑料盒外壳。
适用场景:
适用于大功率工业品和汽车应用场景。
三、结合前两种优势的功率模块封装工艺
工艺特点:
采用DBC、铜柱、焊料装片或银烧结工艺。打线或铜片钎接内互联,塑封形成双面散热通道。
SiC模块发展趋势:
采用银烧结代替焊料,以充分发挥SiC材料的耐高温优势。采用铜(铜线、铜片)做内互联代替粗铝线内互联。
以上三种功率模块封装工艺各具特色,适用于不同的应用场景。IPM封装工艺以其高效、集成度高的特点,在白电应用、消费电子等领域占据重要地位;灌胶盒封功率模块则以其高功率密度和可靠性,在大功率工业品和汽车领域得到广泛应用;而结合前两者优势的封装工艺,则在未来SiC模块的发展中展现出巨大潜力。在实际应用中,应根据具体需求选择合适的封装工艺,以实现最佳的性能和成本效益。
2
DBC类IPM封装线路
焊料装片DBC类IPM封装线路是功率模块封装技术的一个重要里程碑,以下是对其分点概述:
一、DBC基板的应用与优势
DBC基板:作为功率模块的核心部件,DBC基板既满足了功率器件内互联和导热散热的需求,又因其绝缘性符合安规要求,特别适用于大功率场合。
二、DBC类型IPM的特点
集成度高:DBC类型的IPM采用了SMT(表面贴装技术),将功率芯片和被动元器件(如电容、电阻)有效地集成并封装在一块基板上,提高了芯片集成度。
粗铝线内互联:通过粗铝线实现内互联,提高了功率传输效率。
框架设计:设计抬高的框架联接,便于安装控制芯片,实现智能化功率分配。
三、SPM技术的引入与工艺简化
SPM定义:美国仙童公司开发的此类功率模块称为SPM(Smart Power Module),是IPM封装技术的进一步提升。
工艺简化:与传统的IPM工艺相比,SPM工艺复杂性有所降低,更借鉴了传统EMS(电子制造服务)行业的组装技术,如印刷、贴片、回流、清洗等电路板安装技术。
四、回流焊夹具的设计与优化
热吸收与膨胀差异:在设计回流焊夹具时,需考虑框架、DBC以及回流焊夹具之间的热吸收和膨胀差异,避免封装材料移动和尺寸波动。
锁定与热应力释放:夹具设计需兼顾锁定和热应力释放,避免框架变形翘曲。通过计算和实验确定夹具的最优化设计,保证生产良率。
五、后道工序与尺寸控制
后道工序:DBC类型的IPM后道工序与传统IPM相差不大,但需注意控制尺寸波动。
尺寸控制:由于采用塑封,尺寸波动对塑封模具至关重要。因此,需严格控制框架厚度等方面的变化,确保塑封质量。
综上所述,焊料装片DBC类IPM封装线路以其高集成度、大功率处理能力以及优化的工艺设计,在功率模块市场中占据重要地位。通过不断改进和优化封装技术,可以进一步提高其性能和可靠性,满足更广泛的应用需求。
3
传统灌胶盒封与双面散热模块
灌胶盒封大功率模块封装线路及其相关技术发展可以分点概述如下:
一、灌胶盒封模块工艺特点
内互联键合工艺:根据具体情况选择是否添加。若采用铜片连接技术做内互联,则无需内互联键合工艺;若芯片栅极小,需做细铝线键合,或源极区域也采用粗铝线键合,则内互联键合为关键工艺。
铜片工艺:电阻小、导热快,但生产灵活性不够,需定制化,且对芯片表面纯铝情况不适用,需额外电镀处理。
铝线绑定工艺:在内阻和散热性影响不大的情况下常用,因其工艺相对简单。
粗铜线键合绑定技术:利用铜的电阻小、导热快的特性,开发出的一种新技术。
二、盒装塑封工艺及其难点
提高可靠性:采用盒装塑封工艺以提高功率循环可靠性。
功能端子安装:主要难点之一,需控制端子尺寸波动,确保后续测试端子接触良好。
塑封工艺性问题:塑封压力对盒子选材和盖子密封性提出要求,需研究各工序带来的尺寸波动,优选材质以保证产量和良率。
三、双面散热塑封功率模块
工艺特点:采用双面DBC和铜柱,可选择内互联绑线键合或铜片内互联。塑封后厚度可控,非常薄,又称刀片式功率模块。
优势:电路拓扑简单;可靠性高;功率密度大;散热性优良;安装方便。
四、双面散热模块与传统灌胶盒封模块比较
体积与功率密度:双面散热模块体积更小,三合一模块也比传统灌胶盒装模块更紧凑,因此功率密度更大。
散热效率:双面散热模块散热效率更高。
封装保护:塑封比灌胶封装保护更好,更耐机械冲击,能有效提高可靠性,提升功率循环寿命。
灌胶盒封大功率模块封装线路及其相关技术发展在不断进步,以适应更高功率密度、更高可靠性和更优散热性能的需求。双面散热塑封功率模块作为其中的佼佼者,具有广阔的应用前景。
晶圆 (wafer)/晶粒 (die)/芯片 (chip)之间的区别和联系
晶圆(Wafer)——原材料和生产平台
晶圆是半导体制造的基础材料,通常由高纯度的硅(Si)或其他半导体材料制成。晶圆的形状一般是圆形的薄片,厚度一般在几百微米到几毫米之间,表面经过精密的处理,使其足够光滑,并具备优良的晶体结构,适合进行各种电子器件的加工。
比喻:可以把晶圆比作“原材料”或“纸张”,类似于我们制造一本书的纸张,它本身并不是最终产品,但它是所有后续工艺的基础。
晶粒(Die)——分割后的单个电路单元
在晶圆上,经过一系列的半导体工艺(如光刻、掺杂、蚀刻等),会形成大量的集成电路结构。这些集成电路结构中的每一个独立单元称为晶粒(Die)。晶粒是通过将晶圆切割成多个小块而得到的,每个晶粒代表一个完整的电子组件,通常具备完整的功能,但在此阶段它还未进行封装。
比喻:可以把晶粒比作“书页上的单篇文章”。它是从“整本书”中剪裁出来的每一小部分,每个“文章”都有独立的内容和功能,但它还不完整,尚未加入封面、装订等步骤。
晶粒的外形通常为矩形或正方形,尺寸和形状的具体要求会根据产品的设计、功能需求和制造工艺的不同而有所差异。晶粒的质量直接影响最终芯片的质量,因此,晶粒在生产过程中需要经过严格的测试和筛选(例如,KGD:已知良品晶粒,符合功能和可靠性要求)。
赞助商广告展示
芯片(Chip)——封装后的成品
晶粒经过切割和测试后,会被封装成完整的芯片(Chip)。封装不仅为晶粒提供物理保护,防止其在使用过程中受到损坏,还通过引脚、焊盘等方式将芯片与外部电路连接起来。芯片是最终面向用户和市场的产品,完成封装后的芯片才具备实际的电气功能,能够作为集成电路(IC)的一部分,应用于各种电子设备中。
比喻:芯片就像是一本已经印刷、装订好的书。每一篇文章(晶粒)都被整合成一个完整的图书(芯片),并且有封面和目录(封装),使得读者(系统)可以使用这本书(芯片)的内容。
晶圆、晶粒与芯片的关系
晶圆是生产的原材料,经过精细工艺后会形成许多个晶粒。
晶粒是在晶圆上切割出来的独立单元,每个晶粒可以独立完成指定的功能。它们通常需要经过测试来确保它们是良品(如KGD晶粒),并且满足电学性能和可靠性要求。
芯片则是将晶粒封装后的最终产品,具备完整的外部接口,可以与其他电子设备进行连接和工作。
这三者的关系可以通过一个逐步加工的过程来理解:从大块原料(晶圆),到切割成小单元(晶粒),再到封装成最终产品(芯片),每一步都至关重要,决定了最终芯片的质量和功能。
什么是Dummy Wafer(填充片)
一、Dummy Wafer 的定义与作用
Dummy Wafer,中文称为填充片,是在晶圆制造过程中专门用于填充机台设备的晶圆,通常不会用于实际生产,也不会直接作为成品出售。其主要作用是为满足设备运行的特定要求或约束,确保设备的工艺性能稳定,同时优化资源利用率并减少生产风险。Dummy Wafer 的设计和使用是晶圆厂生产管理的重要组成部分。在晶圆制造的不同工艺阶段,由于设备的特性及工艺要求,Dummy Wafer 在保证设备正常运行、优化资源分配、降低良品晶圆损耗方面起到了不可替代的作用。
二、Dummy Wafer 的具体用途
Dummy Wafer 的使用场景多种多样,根据其用途主要可以分为以下几个方面:
填充设备容量:某些设备(如炉管、刻蚀机)在运行时对晶圆数量有一定要求。例如,炉管设备的热处理工艺需要晶圆在一定数量的情况下,才能形成稳定的气流、温度场和化学反应环境。如果只放置少量生产晶圆,设备性能可能不稳定,最终影响工艺质量。因此,Dummy Wafer 被用来填充设备以达到所需数量。将晶圆设备比作一个烤箱,如果烤箱里只放一块面包,热量可能分布不均匀,但如果放满面包,就能均匀受热。同理,Dummy Wafer 起到了“凑人数”的作用,确保设备在最佳负载下运行。
保护生产晶圆:在某些高风险工艺中,比如离子注入、刻蚀和化学气相沉积(CVD),设备调试或初始工艺阶段可能存在工艺不稳定或颗粒生成较多的情况。如果直接使用生产晶圆(PW),可能造成不可挽回的良率损失。Dummy Wafer 在此类工艺中起到试探性作用,避免生产晶圆直接暴露在潜在风险下。Dummy Wafer 就像探路先锋,先确认前方道路安全,再让生产晶圆“放心通过”。
均匀分布工艺负载:某些设备在进行工艺处理时,需要工艺载体(例如炉管或刻蚀腔体)内的晶圆分布均匀。例如在物理气相沉积(PVD)中,如果晶圆数量或摆放位置不对称,可能导致沉积速率和厚度均匀性受到影响。Dummy Wafer 的加入能够平衡设备内晶圆的布局,确保整个工艺的稳定性和均匀性。
减少设备闲置成本:在晶圆制造中,设备的启动和关闭都会消耗大量时间和资源。如果没有生产晶圆需要加工,设备长时间闲置可能导致资源浪费和设备性能下降。通过加工 Dummy Wafer,可以让设备保持活跃状态,同时为后续生产做好准备。
进行设备验证和工艺调试:Dummy Wafer 通常被用作设备的验证载体。例如,在设备维护、清洗后,需要使用 Dummy Wafer 测试设备状态是否恢复正常。如果检测到异常,可以调整设备参数或进行再次清洗,而不需要直接损耗生产晶圆。设备就像一辆汽车,Dummy Wafer 就像测试用的轮胎,确保汽车性能正常后,再换上“昂贵”的生产用轮胎。
三、Dummy Wafer 的材料选择与使用特点
Dummy Wafer 的材质和规格通常根据工艺要求和设备特性而定。以下是 Dummy Wafer 的主要特点:
材料:大多数 Dummy Wafer 使用与生产晶圆相同的基材(如单晶硅或多晶硅),以保证在设备中的表现一致。对于某些特殊工艺场景(如高温工艺),Dummy Wafer 的材料可能会更耐用,但成本相对较低。
表面处理:Dummy Wafer 的表面通常不需要与生产晶圆相同的精细处理。它们可以是抛光晶圆,也可以是测试级晶圆。部分 Dummy Wafer 可能会重复使用,直到出现较大的损伤或颗粒污染,才会被更换。
使用寿命:Dummy Wafer 通常会被循环使用,但其使用寿命取决于具体工艺和设备要求。例如,在高温、高腐蚀环境中,其寿命会较短。
成本考量:Dummy Wafer 的成本通常远低于生产晶圆,但仍需要妥善管理和维护,以避免不必要的浪费。
四、Dummy Wafer 的管理和优化
在晶圆制造过程中,Dummy Wafer 的管理是一项需要高度关注的任务。以下是相关管理和优化措施:
使用追踪:建立 Dummy Wafer 的使用记录,跟踪其使用次数、使用工艺和损耗情况。通过数据分析优化 Dummy Wafer 的更换周期。
减少污染:Dummy Wafer 的重复使用可能会带来颗粒或化学污染,因此需要定期清洗或替换,确保设备内部环境清洁。
工艺适配:不同工艺对 Dummy Wafer 的要求不同,需要根据工艺特点选择合适的 Dummy Wafer。例如,在薄膜沉积中,Dummy Wafer 表面的光洁度可能直接影响薄膜质量。
库存管理:由于 Dummy Wafer 不会直接用于生产,其库存管理需要考虑成本控制与生产需求之间的平衡。
废弃处理:报废的 Dummy Wafer 应根据环保要求妥善处理,例如回收硅材料或作为低级别测试晶圆使用。
五、Dummy Wafer 的实际案例分析
炉管填充:在氧化工艺中,炉管设备对晶圆数量要求严格,过少的晶圆可能导致温度场不均,影响氧化层厚度。Dummy Wafer 的加入不仅填补了数量要求,还能起到保护生产晶圆的作用。
刻蚀设备调试:刻蚀设备在工艺切换或维护后,需要对刻蚀速率、均匀性进行测试。如果直接使用生产晶圆,可能产生严重损失。通过 Dummy Wafer 验证刻蚀工艺后,可以确保生产的安全性和稳定性。
六、总结
Dummy Wafer 是晶圆制造过程中不可或缺的一部分,其作用贯穿设备维护、工艺调试到资源优化等多个方面。在实际操作中,合理使用 Dummy Wafer 不仅能够降低生产成本,还能提高设备利用率和工艺稳定性。
Wire bonding IMC是不是越厚越好?
谈起IMC这个问题,有点困惑
IMC到底是越厚越好?还是越薄越好?
IMC全称为intermetallic(金属间化合物),金属化合物是两种不同金属原子按照一定比例进行化合,形成与原来两者晶格不同的新化合物。金属化合物的形成是在两种不同金属的接触面上,通过原子的热扩散运动形成的;
在半导体封装中,我们的芯片PAD主要是由金或铝两种金属材料,bonding wire的材料就比较丰富了,有铝、铜、钯铜、金、银等材料;WB焊接四要素:压力((bond force),功率(power),时间(time),温度(temperature),WB的四要素共同加速界面的金属原子的相互扩散,从而形成Au-Al、Cu-Al和Ag-Al等金属化合物,从而达到两种不同材质金属间的键合。
而随着时间的推移,相互接触的两种金属原子将会继续扩散,导致IMC不停地朝着两种金属深处生长;且由于靠近不同材质界面原子浓度的差异,导致各金属间化合物原子数量比不同,从而会同时存在多种不同成分的IMC;其次因其不同金属原子扩散速率的差异,导致Au-Al、Cu-Al和Ag-Al IMC生长方向也各有特点。
我们接下来聊聊
对于如何检验IMC是否接触良好,IMC面积是否满足要求,哪些可靠性实验是检验IMC,失效分析如何检查IMC等问题;
在封装工艺过程中,对于IMC接触是否满足封装要求的快速简单的方法就是打线的推拉力实验,抽检打线的推拉力也是生产线质量管控的重要环节;根据打线材质和线径的不同来参考不同的推拉力值;
IMC面积的要求大于60%以上,不同的类型的器件对IMC的面积要求也是有差异的;
HTSL/HAST可靠性实验是检验IMC的重要手段;
HTSL:高温存储实验,其实验条件为150℃环境下将产品储存1000h,而高温会加速原子扩散,从而加速IMC生长速度,因此HTSL是评估因IMC生长引起失效的重要手段。
HAST:高温高湿实验,其实验条件为85℃和85%湿度的环境金线存储,高温高湿会促进水汽和卤素进入到封装体中,如果有Cl元素就会腐蚀IMC,导致IMC出现高阻。
IMC的物质特性是硬而脆,因此形成了一个相互"矛盾"的概念,IMC的生成代表焊球与焊盘之间形成了有效焊接,但当其生长达到一定厚度时,由于其自身的脆性又会导致使用过程中的热电疲劳在其内部产生裂痕,这种失效风险由IMC生长速度决定,因此Au-Al > Ag-Al > Cu-Al。
所以我们在生产调试过程中会尽量增加IMC的覆盖面积以达到有效焊接,而在可靠性过程中又会想方设法降低其生长速率,通常是在线材中进行掺杂,以抑制原子扩散速率,尤其是金线;
IMC随着时间的增加和温度的增加,IMC会越来越厚,最终会出现柯肯达尔现象,导致一焊点出现高阻失效。
-
封装
+关注
关注
127文章
8200浏览量
144030 -
功率模块
+关注
关注
10文章
494浏览量
45465
原文标题:Wire bonding IMC是不是越厚越好?
文章出处:【微信号:深圳市赛姆烯金科技有限公司,微信公众号:深圳市赛姆烯金科技有限公司】欢迎添加关注!文章转载请注明出处。
发布评论请先 登录
相关推荐
招聘大功率LED封装工程师
【PCB封装工艺】低温低压注塑
招聘人才 封装工艺工程师
新型封装工艺介绍
IGBT功率模块的封装工艺介绍
功率电子器件封装工艺有哪些
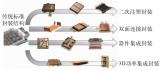
评论