为了消除传统贝塞尔光束的旁瓣引起的烧蚀,利用WOP平面锥镜/平板锥透镜定制飞秒贝塞尔光束。定制的飞秒贝塞尔光束可用于在100μm厚的硅基衬底上制造直径约10μm高深宽比硅通孔的2D阵列,激光加工通孔得到的高深宽比硅通孔深度100μm,顶部底部尺寸分别为10μm和6μm,而不会造成任何旁瓣损伤。通过进一步优化平面锥镜的设计,可以解决定制贝塞尔光束制造速度的问题,实现更快、更高分辨率和更精确的TSV制造。
三维集成电路(3D IC)是传统二维集成电路的有吸引力的替代品,目前加工中存在的主要困难之一是制造高纵横比硅通孔(TSV),这是组装三维硅基IC的关键技术。这篇文章展示了使用飞秒(fs)1.5μm贝塞尔光束进行高质量TSV制造。为了消除传统贝塞尔光束的旁瓣引起的严重烧蚀,使用专门设计的WOP平面锥镜/平板锥透镜(二元相位板)定制了fs贝塞尔光束。我们证明,定制的fs贝塞尔光束可用于在100μm厚的硅基衬底上制造直径约10μm TSV的2D阵列,而不会造成任何旁瓣损伤,这表明在三维硅基IC的3D组装中具有潜在的应用。通过进一步优化WOP平面锥镜/平板锥透镜的设计,还可以对贝塞尔光束进行定制,解决制造速度的问题,实现更快、更高分辨率和更精确的TSV制造。
自1958年集成电路(IC)发明以来,硅蚀刻一直是半导体行业的关键工艺,并且一直在努力提高IC的集成度。近年来,为了实现更高的集成度和运行速度,基于3D组装的三维硅基IC备受关注。目前,硅IC的3D组装关键技术之一是硅通孔(TSV)的制造,高纵横比硅通孔用于垂直穿过硅衬底以互连硅IC芯片的电气连接。与叠层封装技术相比,T高纵横比硅通孔允许以更高的密度和更短的连接长度组装3D IC,从而实现更小的尺寸和更高的性能。
目前对TSV的要求包括直径约50μm、深度约500μm,纵横比约10。开发高通量和具有成本效益的TSV制造技术以实现高纵横比蚀刻、可控的形态和低负载效应,仍然是一个重大挑战。此外,在保持纵横比的同时缩小TSV直径是未来3D IC的要求。
目前使用的典型高纵横比硅通孔加工技术包括湿化学蚀刻和等离子体干法蚀刻。然而,由于TSV制造中常用的单晶硅衬底的各向异性蚀刻速率,这些技术的应用受到限制,这使得创建高纵横比结构本质上非常困难。另一方面,反应离子蚀刻(RIE)方法(最常见的是Bosch工艺)可用于制造各种具有小特征尺寸的深度蚀刻Si结构;无论如何,RIE涉及包括光刻在内的几个步骤,并且蚀刻率非常低。
通过直接激光钻孔进行高纵横比硅通孔制造已被提议作为一种快速且环保(不含有毒物质和气体)的替代方案,由于消除了光刻技术,加工步骤更少。已经有新闻报道利用纳秒紫外激光冲击在250μm厚的Si衬底上制备直径为20μm的孔,但是加工直径小于10μm的孔仍是3D Si IC组装的一个重要挑战。最近,超快激光加工已被证明是材料加工的一种有吸引力的工具,因为它允许在抑制热影响区的情况下进行亚衍射极限加工。例如,使用780nm飞秒(fs)激光器对平面硅器件进行高质量切割已得到成功证明。此外,使用超快激光加工在各种材料上高速、高纵横比钻孔一直是许多重要科学和工业应用中的热门话题。飞秒贝塞尔光束已被用于在各种石英玻璃中制造纵横比高达100-1000的微观结构,由于景深长,无需样品平移。我们已经通过使用波长从400nm调谐到2.4μm的飞秒贝塞尔光束来演示TSV制造。在贝塞尔光束加工中,材料应对激光波长透明,以便贝塞尔光束的旁瓣可以穿过材料传播,从而在材料中产生中心瓣。由于硅的带隙为1.12 eV,因此在使用贝塞尔光束进行硅微结构加工时,飞秒激光的波长应大于1.13 μm。然而,即使是在硅透明窗口中工作的飞秒激光器,由于其带隙窄、双光子吸收强、自由载流子吸收弱,也不容易进行硅的深度刻蚀。此外,最近有报道称,当使用1.3μm飞秒贝塞尔光束时,Si的体积和背面改性存在固有的局限性。因此,使用飞秒激光对透明硅材料进行深度刻蚀仍然具有挑战性。
在这项研究中,我们提出使用1.5微米飞秒贝塞尔光束制造TSV。我们首先优化了TSV的制备条件,包括每脉冲激光能量、激光发射次数和样品位置。为了消除紧聚焦飞秒贝塞尔光束旁瓣引起的烧蚀,实现深刻蚀,我们提出了采用特殊设计的二元相位板对光束进行剪裁。定制贝塞尔光束的副瓣比为0.6%,而传统的飞秒贝塞尔光束的副瓣比为15.6%。提出了基于不同波矢贝塞尔光束干涉的旁瓣抑制方法。然而,该方法采用了双缝环形光阑,大大降低了激光束的利用率。此外,获得的旁瓣比为4.3%,如下文所述,这不足以用于TSV制造,且没有旁瓣损伤。本文设计了利用定制贝塞尔光束制作TSV的实验装置。在此基础上,详细讨论了相板的理论模型和数值设计。更重要的是,通过优化飞秒贝塞尔光束,实现了直径约10μm、间距为50μm的TSV阵列的制备,其对应的TSV密度约为1×10^5cm−2,纵横比约为10。最后,对该技术的工业应用进行了简要的讨论。
实验
在光学参量放大器(OPA)中,将1kHz放大的钛宝石飞秒激光束的800nm脉冲转换为1.5μm脉冲。1.5μm脉冲的能量为550μJ,脉宽为65 fs。为了演示所提出技术的原理,使用了三种不同类型的fs激光束——高斯光束、常规贝塞尔光束和定制贝塞尔光束,分别如图1(a–c)所示。高斯光束由物镜聚焦,景深短,无旁瓣。相比之下,使用WOP平板锥透镜产生的传统贝塞尔光束具有超长的景深,但旁瓣比高达16%。从原理上讲,由于光波的衍射特性,在景深和激光束的旁瓣比之间存在折衷。通过在平板锥透镜前放置优化设计的相位板,可产生具有显著降低的副瓣但足够长景深的定制贝塞尔光束,用于许多重要应用,其中一些将在下文中描述。
图1(d)显示了本研究中采用的实验装置的示意图。采用可调谐圆孔将激光束从直径5 mm截断到4 mm,保证了良好的光束质量。在本次实验中,我们使用了一个基准角为20°的WOP平面锥镜(AX2520-C-20.0°,直径25.4 mm,Thorlabs Inc.)来产生常规贝塞尔光束。为了定制传统的贝塞尔光束,在WOP平面锥镜前5 mm处放置相位板。将硅样品安装在分辨率为0.3μm的XYZ工作台上。为了研究每个激光束的三维强度分布,在WOP平面锥镜后面安装了一个显微镜成像系统,该系统包括物镜(NA 0.3,10x)、管透镜和近红外CCD相机,并固定在可沿激光束传播方向平移的工作台上。为了防止激光对CCD相机的损伤,引入了一个短通滤波器对1.5μm fs光束进行衰减。通过沿激光束轴逐级平移显微成像系统并记录每个位置的光束模式,重建了激光束的三维强度分布。
本研究中使用的硅样品是镜面抛光的,(100)取向,n掺杂(电阻率ρ>20Ω-cm)衬底,厚度分别为50μm和100μm。对于TSV制造,硅样品的前表面设置为z=zmax(轴上最大强度的位置),其位置是通过检查用光束轮廓系统测量的3D光束轮廓来确定的。采用时间分辨率为1ms的可编程快门来改变TSV制造中使用的发射次数,并使用中性密度滤波器调整激光脉冲能量。
结果
二元相位板的设计、制造和表征。目前,通过振幅和/或相位调制的激光束整形为实现超分辨率光斑、均匀照明、景深扩展以及许多重要应用(如显微镜、激光微加工、纳米光刻、光学捕获和数据存储)的多光斑并行处理提供了多种特征。在各种激光光束成形光学器件中,二元相位板由于其高转换效率、低成本和易于制造而受到极大的关注。使用二进制相位板,我们试图消除与传统贝塞尔光束相关的旁瓣烧蚀。贝塞尔光束的旁瓣原则上是由沿“圆锥体”表面传播的所有光束的干涉产生的。使用相位板的效果是引入更多的贝塞尔光束,其旁瓣分布在不同的半径上。通过调谐每个类贝塞尔光束的相位,可以实现相消干涉对所有旁瓣抑制它们之间的强度,而中心瓣的相长干涉仍然保持诱导状态以实现中心瓣的高强度。这种优化非常复杂,因此采用计算机模拟自学习来优化相位板的设计。
图1.(a)高斯光束、(b)常规贝塞尔光束和(c)定制贝塞尔光束的生成方案和强度分布的示意图
(d)TSV制造的实验装置。插图显示了二元相位板的结构示意图。
典型的二元相位板的结构如图1(d)的插图所示,其中黑色和白色区域分别对应于0和π相区。为了设计能为给定的一组要求产生最佳输出光束的相位板,应优化参数,包括环形区域的数量(M)、每个区域的半径(rm,其中M=1,2,…,M,如图1(d)的插图所定义)和圆形凹槽的深度(Δh)。在这里,我们将我们的设计限制在0-π相位板;因此,凹槽深度被固定以产生π-相位差,并且唯一需要优化的参数是环形区域的数量和环形半径。
理想的贝塞尔光束包含无限的能量,在传播过程中是纯非衍射的,但在现实世界中并不存在理想光束。在实际应用中,通过用WOP锥透镜聚焦高斯光束,可以形成贝塞尔-高斯光束,作为理想贝塞尔光束的近似值,如图1(b)所示。我们将此类光束称为“常规贝塞尔光束”,以便将其与本研究中使用的定制贝塞尔光束区分开来。对于一个完美的轴锥,即一个具有完美尖端的轴锥来说,贝塞尔光束的强度分布可以解析导出。
在这项工作中,采用了一种更实用的圆尖平面锥镜模型,其中平面锥镜表面被认为是两片旋转的双曲面,以实现精确的相位板设计。双曲面顶点和理想平面锥镜顶点之间的距离测量为τ=21μm(用光学显微镜测量,更多细节请参见补充材料中的图S1)。为了设计一个合适的相位板来剪裁fs贝塞尔光束,采用了一种基于Hankel变换的数值方法来模拟光束在WOP锥透镜和相位板之后的传播(见方法)。在模拟的每次迭代中,采用模拟退火(SA)算法来优化相位板的参数(M,{rm})(见图S2)。我们选择这种方法是因为它为多个变量的优化提供了最佳拟合,并在收敛速度和优化时间之间取得了良好的平衡。通过在模拟中将搜索窗口的长度设置为100μm,相位板的每个区域的优化半径为rm={146,185,200,1696,1920} μm。
图2显示了传统和定制贝塞尔光束的横向和轴向轮廓,从中得出了束腰(直径)、景深和旁瓣比,如表1所示。结果表明,采用优化设计的相位片可以有效地降低贝塞尔波束的旁瓣比。与传统的贝塞尔光束相比,定制的贝塞尔光束的景深更短;然而,对于激光加工通孔和其他应用来说它仍然过长。需要强调的是,在图2中,为了直观地比较不同光束的旁瓣比,对所有光束强度分布进行了归一化。在我们计算的实际情况中,定制贝塞尔光束的峰值强度是传统贝塞尔光束的1.4倍。这在TSV制造中是很好的结果,因为TSV制造所需的脉冲能量将在使用后文所述的相位板之后减少。
图2:(a–d)分别计算和(e–h)实验测量的常规和定制贝塞尔光束的强度分布。(a)和(b)分别示出了传统贝塞尔光束和定制贝塞尔光束在r-z平面中的计算光束轮廓。它们在z=zmax处的横向强度分布,其中最大强度在激光束轴上获得,平均值分别在(c)和(d)中显示。在(e)和(f)中分别示出了x-y平面中每个光束的实验测量的2D轮廓以及轴上强度分布(橙色曲线)。(g)和(h)分别示出了在z=zmax处测量的常规和定制贝塞尔光束的横向强度分布,以及插图中各个光束的CCD捕获图像。(g)和(h)中插图中的比例尺为20μm。
表1.在常规贝塞尔光束和定制贝塞尔光束的优化轴向范围内,中心瓣的束腰(2w0,以FWHM测量的直径)、景深(zDOF,以沿光轴的FWHM测量)、z=zmax处的旁瓣比(SLRm)和平均旁瓣比(SLR)的比较。
图3.使用不同脉冲能量和不同激光发射次数的传统贝塞尔光束制造的50μm厚硅样品的(a)前表面和(b)后表面TSV的SEM图像。(a)和(b)中的比例尺分别为20μm和5μm。(c)–(e)显示了前表面和后表面TSV直径随脉冲能量和激光发射次数的变化。
使用其他地方详述的传统光刻技术在BK7玻璃基板上制造所设计的相位板(见Methods)。我们从旁瓣抑制的角度对所制造的相位板进行了表现。利用相对较低的脉冲能量来确保线性光束传播。使用图1(d)所示的光束轮廓系统测量和分析激光束图案。常规贝塞尔光束的强度分布如图所示。图2(e),测量的景深约为12mm,还观察到沿纵向的强度调制。如图所示,当考虑圆尖平面锥镜时,结果与理论设计一致。图2(a),定制贝塞尔光束的测量纵向轮廓如图所示。图2(f),对于定制贝塞尔光束,zmax和zDOF分别为2.35mm和420μm。更重要的是,在景深内没有观察到旁瓣。激光功率通过相位板后的总损耗应主要由相位板两侧的菲涅尔反射引起,估计约为8%。这种损耗很容易通过相位板的AR涂层减少。因此,这种量身定制的技术的效率一直很高。应该注意的是,定制贝塞尔光束的测量强度分布与图2(b)所示的理论结果略有偏差。这可归因于OPA产生的1.5μm fs激光束与钛宝石基相相比质量相对较差,以及相位板制造中的有限分辨率(见图S3和S4)。在z=zmax时,传统和定制贝塞尔光束的横向光束轮廓如图2(g)、(h)。相位片显著降低了旁瓣,这对制造高质量TSV是一个有利的结果。
用1.5μm飞秒贝塞尔光束激光加工通孔。首先使用具有不同脉冲能量和激光发射次数的传统fs贝塞尔光束在空气中进行Si钻孔,并且Si样品固定在z=zmax。图3(a)和(b)分别显示了在50μm厚的硅样品中制造的TSV的前表面和后表面的扫描电子显微镜(SEM)图像。在这些实验条件下制造的TSV的直径为5–10μm,纵横比为5–10。图3(c–e)显示了TSV直径于不同脉冲能量的激光发射次数的函数。使用脉冲能量为360μJ的传统fs贝塞尔光束生产单个通孔需要300多次激光发射。有趣的是,通过将激光发射次数增加到约650次,可以产生几乎无锥形的TSV。还观察到,对于280μJ和187μJ的较低脉冲能量,产生无锥形TSV所需的激光发射次数分别增加到约1000和约1500。然而,在187μJ的能量以下,即使激光发射次数显著增加,也不能形成通孔。
图4.在(a–c)50μm和(d–f)100μm厚的Si衬底中制造的TSV的SEM图像。
(a)–(c)分别是使用(a)高斯光束(GB)、(b)常规贝塞尔光束(CBB)和(c)定制贝塞尔光束(TBB)制造的TSV的截面图。
(d)–(f)分别是通过定制贝塞尔光束在100μm厚的Si衬底中产生的TSV的前表面和后表面的截面图像。
(e)和(f)插图中的比例尺为5μm。
尽管可以使用传统贝塞尔光束创建无锥形TSV,但由硅在前表面的强双光子吸收引起的固有旁瓣烧蚀是不可避免的,如图所示。第3(a)段。即使使用187μJ的中等激光脉冲能量或多次激光发射,也不能完全抑制硅前表面的这种旁瓣烧蚀,这在任何情况下都会阻碍TSV的实际应用。进一步的研究表明,即使使用我们系统的最大输出脉冲能量(约550μJ)并增加激光发射次数,也不能在100μm厚的Si衬底中形成通孔。
在空气中使用传统贝塞尔光束制造TSV存在未来的实际应用中必须克服的两个问题。一个是上述旁瓣引起的损伤,另一个是TSV的有限深度。为此,我们建议使用优化设计的相位板来定制传统的贝塞尔光束,如第3节所述。我们首先比较了三种不同类型fs激光束的TSV制造特性:聚焦高斯光束、传统贝塞尔光束和定制贝塞尔光束。对于每种情况,我们将脉冲能量设置为略大于通孔形成的阈值,并优化激光发射次数,以使TSV的锥角最小化。在激光加工期间,再次将Si衬底固定在台架上,使得前表面对应于z=zmax。在高斯光束的情况下,用物镜(NA 0.3,10x)聚焦产生直径约为6μm的光束,zDOF约为16.7μm。高斯光束、常规贝塞尔光束和定制贝塞尔光束的最佳脉冲能量和激光发射次数分别为25μJ和400、196μJ和500、47μJ和800。常规贝塞尔光束和定制贝塞尔光束之间的脉冲能量的显著降低(可归因于相位板将光束集中到中心波瓣中)提高了TSV制造的工艺效率。
飞秒激光消融后,对所有TSV样品进行机械切割和检查。图4(a–c)显示了分别使用高斯光束、常规光束和定制贝塞尔光束在50μm厚样品中产生的TSV的SEM截面图像。高斯光束清楚地产生了前表面直径大于20μm的TSV,对应于小于3的低纵横比,并且具有严重锥形的侧壁。对于传统的fs贝塞尔光束,产生了具有几乎无锥形侧壁的高纵横比(直径为5μm,对应于约为10的纵横比)TSV;然而,波束的高旁瓣比导致TSV周围的严重烧蚀损伤。相反,通过使用定制的贝塞尔光束,旁瓣烧蚀被完全抑制,并且在50μm厚的衬底中形成了直径小于8μm的TSV。
之后我们试图用相同的激光束在100μm厚的硅衬底中制造较深的TSV,并发现这只有使用定制的贝塞尔光束才能实现。由于高斯光束的焦点固定在基板的前表面,由于聚焦激光束的散焦,激光强度不足以在更大的深度引起烧蚀。传统贝塞尔光束相对较高的旁瓣强度在Si表面引起双光子吸收,如图4(b)所示的旁瓣烧蚀所证明。因此,旁瓣不能深入硅衬底。相反,对定制贝塞尔光束的旁瓣抑制阻止了Si的双光子吸收,允许贝塞尔光束穿透整个Si衬底。
在使用定制贝塞尔光束在100μm厚的硅衬底上进行TSV钻孔的情况下,最佳脉冲能量和激光发射次数分别为104μJ和1200。在这些条件下,形成了间距为50μm的直径约为10μm的TSV阵列,其对应于约1×105 cm−2的TSV密度和约10的纵横比。从图4(d)所示的截面图中可以看出,没有观察到可检测的旁瓣引起的损伤,这证明该方法即使对于较厚的硅样品也是有效的。在图4(d)中,可以看到碎片的严重沉积,特别是在Si衬底的前表面上。为了去除这些碎屑,将TSV样品在47%HF、70%HNO3和100%H2O(体积比为51)的蚀刻剂混合物中浸泡(无超声处理)约10 s,然后用去离子水洗涤。在该程序之后,TSV样品表现出干净的前表面和后表面,如图4(e)、(f)。
讨论
我们已经证明了首次使用1.5μm fs定制贝塞尔光束制造高纵横比TSV。使用相位板生成的定制贝塞尔光束不会产生与传统fs贝塞尔光束相同的旁瓣引起的损伤,可以用于进行深度蚀刻。此外,使用定制的贝塞尔光束,可以在100μm厚的Si衬底上制备纵横比约为10的高密度(约1×105cm−2)TSV阵列。与其他现有的TSV制造技术相比,我们的方法大大简化了TSV制造的复杂过程。
关于该技术在TSV制造中的实际应用的一些问题仍未解决。最大的问题是,吞吐量仍远未达到每秒1000个孔的工业要求。目前,单个TSV需要几百到一千个脉冲,对于本研究中使用的1 kHz的重复频率,该TSV对应于每秒1-2个空穴。将激光重复频率增加到100 kHz可以将吞吐量增加到每秒100–200个孔,而不会因热量积聚而导致制造质量下降。此外,采用多波束并行处理将进一步提高吞吐量。为了提高制造效率,减少制造中使用的脉冲能量也很重要。本研究中使用的定制贝塞尔光束的景深仍然显著大于硅衬底的典型厚度。将相位板设计为最佳景深可以减少TSV制造所需的脉冲能量,这也有利于进一步降低旁瓣能量。同时,尽管定制的贝塞尔光束沿景深在轴向方向上是均匀的,但就光斑大小而言,强度并不均匀。这就是为什么TSV的直径在其前表面总是最大的原因(前表面的位置对应于消融期间的z=zmax)。我们期望通过进一步优化相位板的设计,可以对贝塞尔光束进行定制,从而使沿景深的轴向强度均匀,这将实现更快、更高分辨率和更精确的TSV制造。
基于这项研究的结果,我们相信我们的TSV制造新技术可以潜在地应用于3D Si IC的工业规模生产。此外,我们希望可以实现这种定制的贝塞尔光束,以提高其他重要应用的性能,如生物成像和光学捕获。
方法
圆尖端轴锥的特性。图S1显示了实验中使用的圆形尖平面锥镜的侧视图。双曲面顶点和理想平面锥镜顶点之间的距离测量为τ=21μm。所用WOP锥透镜的底角为β=20°。相对于光轴的光线角度可以表示为参考
α=arcsin(n/n0*sin B,)-β;
其中n=1.44是熔融二氧化硅在1.5μm波长下的折射率,n0=1。
用于调整贝塞尔光束的二进制相位板理论。在模拟中,来自孔径和相位板的衍射可以忽略,这对于特征尺寸>>λ的光学元件是合理的。此外,采用基于Hankel变换的数值方法模拟了光束在平面锥镜和相位板后面的传播。因此,正好在圆形尖端轴锥(z=0)后面的光场表示为
E(r,0)=Ein*T(r)exp(inkd)*exp[ik(n0-n)]r^2*tan^2β;
其中exp(Er=−w22/)in是入射高斯光束的场,其束腰为win=2 mm,这与实验条件一致,n和n0分别表示平面锥镜和外侧介质的折射率。应该注意的是,假设一个薄平面锥镜,其中d是平面锥镜的最大(中心)厚度,z=0定义为相应理想平面锥镜顶点。T(r)是相位板的传输函数,可以写成
T(r)=(-1)^(M+1)*circ(r/rM)+(M-1)Σ[(-1)^m+1]*2*circ(r/rM);
其中rm是第M个环带的半径,M是环带的总数,circ(·)表示定义为
circ(r)=1,r<1; circ(r)=0,r>1。
在圆柱坐标系中执行E(r,0)的Hankel变换,得到z=0时场的空间频率谱:
S(ξ,0)=k∫R 0 E(r,0)J0(kξr)r dr;
其中R是WOP平面锥镜的光瞳的半径。然后,我们使用角谱方法在距离为z的空间域中传播光谱,并获得
S(ξ,z)=S(ξ,0)exp(ikz z)
其中kz=k√(1-ξ^2)是传播方向上的波矢量。因此,通过S(ξ,z)的Hankel逆变换,可以得到在圆尖轴锥之后传播距离z的场,从而给出
E(r, z)= k∫1 0 S(ξ,z)J0(kξr)ξdξ
值得注意的是,为了加快数值模拟过程中的计算速度,方程S(ξ,0)、S(ξ,z)、E(r, z)采用抛物线采样。为了获得相位板的最佳结构,应该适当的确定并最小化成本函数。在这项工作中,选择成本函数作为特定轴向范围[zmax−l,zmax+l]上旁瓣比的平均值,并表示为
SLR=1/2l ∫zmax+l zmax-l I1(z)/I0(z)dz,
其中I0(z)=|E(0,Z)|^2是波束的轴上强度(也是中心瓣的峰值强度),I1(z)是最亮旁瓣的峰值强度,2l是优化算法中搜索窗口的长度。
二元相位板的制造。选择尺寸为16 mm×16mm×1.5mm的BK7作为基底用于制作相位板。在玻璃基板上旋涂一层薄薄的光致抗蚀剂(Shipley S1805),并通过电子束光刻法制作相位板的设计图案。使用5%HF的溶液通过图案化光致抗蚀剂蚀刻衬底100秒。最后,用丙酮去除图案化的光致抗蚀剂。
使用阶跃轮廓仪(Taylor Hobson)和白光干涉仪(Wyko NT1000)测量相位板的环形区结构,如图S3-S5,凹槽的平均深度约为1.55μm、 而实现180°相移的理论凹槽深度为
Δh=λ/2(n-1)=1.50μm。
其中n=1.501是BK7在1.5μm波长下的折射率。
-
集成电路
+关注
关注
5387文章
11510浏览量
361538 -
TSV
+关注
关注
4文章
111浏览量
81460 -
硅通孔
+关注
关注
2文章
24浏览量
11836
原文标题:使用平面锥制造100μm深10μm宽的高纵横比硅通孔
文章出处:【微信号:深圳市赛姆烯金科技有限公司,微信公众号:深圳市赛姆烯金科技有限公司】欢迎添加关注!文章转载请注明出处。
发布评论请先 登录
相关推荐
OptiFDTD应用:用于光纤入波导耦合的硅纳米锥仿真
锐骏新款超低导通MOSRUH4040M、80M更适用于新产品研发
INA116测试100M高阻抗,误差很大怎么解决?
THS4302在10M到40M之间为什么失真很严重,怎么解决?
锥透镜和它产生的各种环形光束应用
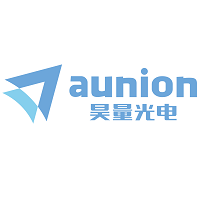
CD100M满杯检测方案的安装指南
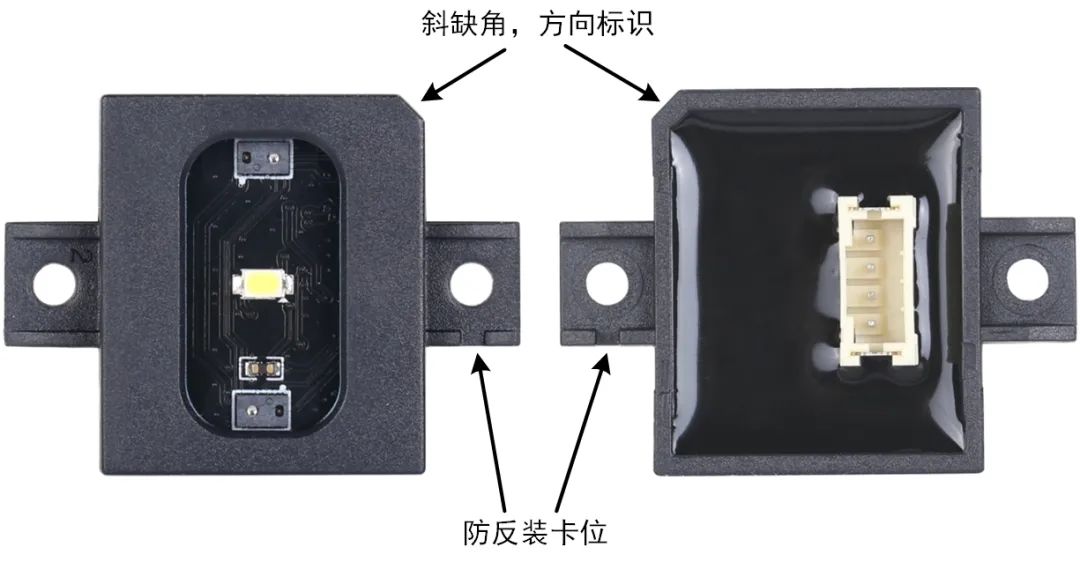
100mΩ,2.5 A 单通道汽车智能高侧开关TPS1HC100-Q1数据表
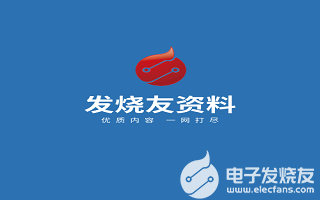
40V、100mΩ 单通道智能高侧电源开关TPS1H100-Q1数据表
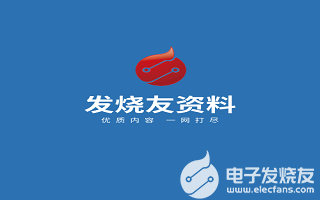
60V、100mΩ、单通道智能高侧开关TPS281C100x数据表
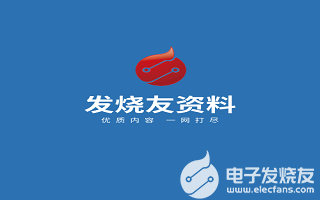
评论