在整个开发流程中,如何将想法草图转变为规范的图纸,供应商能够阅读的文档以便实物的制作,生产厂家能够使用的文档以便最终产品的批量化生产,都是至关重要的。期间主要包含以下几个工作步骤:
电子设计原理图的设计制作
印制线路板(PCB)的设计制作
针对供应商以及生产厂家的需求,输出标准化的文档
在输入了设计的经验,客户的需求,供应商的能力和生产厂商的规范方法之后,形成标准化和系统化的制图方法是提高工程师效率的关键要点。由于硬件工作内容的分工和细化,一般大型汽车电子企业会把这几项内容分别交给元器件工程师,硬件工程师和电路板版图设计工程师,DFX工程师。
负责对元器件的选型的认证和验证实验
输出特殊元器件的需求,比如
是否需要conformal coating,underfill,散热胶和烘焙等等
PCB设计时留有足够元器件间隙便于产品合理化生产
在SJR(solder joint reliability)实验,红墨水实验,切片实验等实验基础上输出焊接盘大小的尺寸以及钢网开孔的需求
2)硬件工程师
完成原理图的绘制工作和相关的元件清单整理工作
为电路板版图设计工程师提供布局布线的产品要求信息
在布局和地平面策略制定时候提供支持
在最后的检查会议中根据通用的规则对PCB文件进行检查
在原理图设计阶段,尽可能多的增加测试点,提高产品在ICT(In-Circuit Test)的测试覆盖率
3)电路板版图设计工程师
在接收到原理图和需要的封装和其他信息以后
完成电路板的设计工作,
与硬件工程师、机构工程师、PCB供应商和DFX工程师确认电路板的功能性、电磁兼容性、可制造性和可装配性等要求
完成电路板版图制作过程
4)DFX工程师 DFX(Design For Excellence)
主要负责降低产品生产,BOM成本,提高产品质量。
保证产品在量产时的产出效率---高的OEE,低的LMPU和DPMU
横跨整个产品的设计阶段的检查,包含器件选型,原理图设计,PCB设计以及和供应商的TFC问题沟通
由于汽车电子是汽车精益化的产物,一段时间内很多设计开发方面的分工和细致的内容会越来越多,这块我可能还需要邀请某些细分项的工程来介绍一下有关PCB的一些查问题的细致内容。我之前遇到的一个案例就是非常细致的事情,弄了很久,一个是发生问题往前追溯,一个是之前精益设计把问题先解决掉。之前解决一个器件内部异常的问题,费了很多的时间和精力,还是往前追溯好一些。
SMD表贴器件的涂层
如果我们采用表贴类元件,在线路板上的时候,特别是表贴类传感器,如应变片、NTC/PTC等,就得非常小心整个涂层对于器件的影响了。特别是基于阻抗影响变化的部件,对整个采集系统构成产生重大的影响。如之前所叙述的那样,本身产生阻抗的变化都会导致实质性的故障。
图 敏感器件的处理
以电阻类为例:
•当电阻被树脂等涂层材料密封并涂覆时,热应力或树脂对电阻器的劣化可能会影响其特性。 提前与器件厂家确认性能和可靠性规格。当树脂吸收水分时,耐潮湿电阻器的腐蚀可能会恶化
•当电阻被树脂材料涂覆或灌封时,固化应力可能会导致保护层剥落和焊点开裂,导致电阻变化和断开
我们考虑到一种复合的失效模式,如果在柔性线路板上使用NTC表贴电阻,主要需要考虑这几个因素:
1)表面的封装材料
2)下面的粘接材料
3)待测对象的温度变化率
4)待测对象膨胀率
图 在柔性线路板上表贴元件情况
如下几个表的综合作用,主要是通过热应力的模式,对不同材料的膨胀进行孔隙的破坏,结构上上产生一些蠕变,然后再通过水分子入侵形成实际的反应。
表1 热应力失效模式
表2 湿度失效模式
表3 结构应力失效模式
遇到这样的问题,我们实质上需要从几个层面去确认:
1)从系统总成来得到不同温度下的工况条件
2)分解到系统层面,环境温度、电压和电流的Profile
3)根据这个来分解得到模组总成的电流、环境温度和振动条件,在特定湿度条件下来作用这个部件
4)到了细节层面进行两部分
分析当时的各种反应机理实际的,温度、工作电压、湿度条件和振动产生的缝隙路径
根据整个实验条件来评估整个机理形成的可现性
图 特定工作条件的分解(多因素应力分析)
实际我们在选用不同的涂层的时候,真是需要仔细去验证和评估,细节的部件层面特性有诸多的变量,需要通过实验进行区分。这真需要调用不同公司层面的知识和设备,需要从技术挖掘到技术导向和领导方面去评估。我们发现,在系统集成的过程中,最重要的是把部件层面供应商的实际所用的测试、方法和已知的各个行业的应用情况综合起来,才能为我们所用。
图 涂层本身评估的特性
原文标题:【书籍动态】电子制图设计以及DFX
文章出处:【微信号:QCDZSJ,微信公众号:汽车电子设计】欢迎添加关注!文章转载请注明出处。
发布评论请先 登录
相关推荐
4种使用带有阶段的前后控制图来衡量改进的方法
科技创新-智旭电子亮相德国慕尼黑电子展
如何以及为何要在EtherCAT®应用中使用DP83826
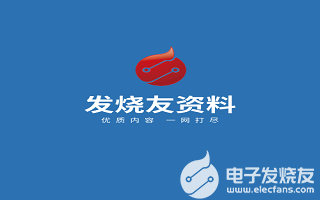
更好的预测方法:使用前后控制图
SPC控制图:告诉你生产过程质量波动的因素(SPC系统)
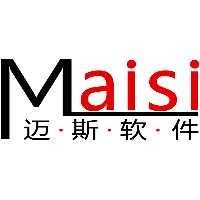
如何在AMD Vivado™ Design Tool中用工程模式使用DFX流程?
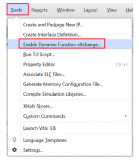
一学就会的SPC
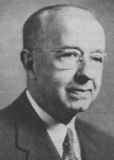
评论