微流控芯片又称芯片实验室,指在厘米级的芯片上,由微通道形成网络,使可控流体贯穿整个系统,以实现常规化学或生物学实验室的各种功能,在生物和化学等领域具有良好的应用前景。微通道内的液滴是近年来在微流控芯片上出现的一种新的流体运动形式,与基于连续流动的微流控芯片相比,液滴微流控芯片大大提升了微流控芯片的低消耗(10”~10”L)、自动化和高通量等优点,是这一领域的重要研究方向之一。每个液滴可以看作是一个密闭的微反应器,基于液滴的反应方式具有更快的传质、传热效率,液滴与液滴之间相对独立,减少了相互污染,已成功用于蛋白质结晶、酶筛选和微纳米颗粒制备等各个方面。
液滴的生成方法主要为多相流法,通过对流体通道结构的设计使分散相流体在通道局部产生速度梯度,利用两相之间的剪切力、黏性力和界面张力的相互作用生成液滴,目前最常用的方法是T形通道法、流动聚焦法和共轴流法”。与T形结构相比,流动聚焦法液滴的生成过程更稳定,生成液滴大小的可控范围更宽,成为研究重点和热点。本文基于COMSOL Multiphysics 4.3的两相流模块,利用水平集法研究了流动聚焦法液滴的形成机制及影响液滴生成的关键因素,揭示了基于流动聚焦结构微通道内液滴的生成机理。
微通道内两相流数值模型
1.1微通道的几何结构与边界条件设置
在研究微通道内油水两相流的问题时,假设两相流动为不可压缩层流,与外界没有能量交换,流动过程中不发生化学反应,两相流体的物理性质为常数,表面张力为主导力,忽略重力的影响。数值模拟采用二维通道。入口宽度均为100μm,主管道总长度为800μm,两侧副通道的长度为150 μm。入口1作为分散相入口,入口2和入口3为连续相入口,右侧为出口。几何结构及尺寸如图1所示。
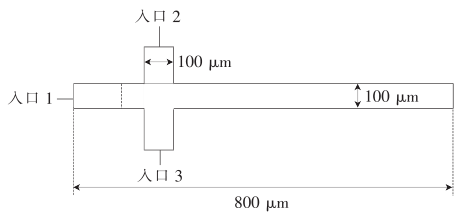
仿真中设定的边界条件为:连续相和分散相入口定义为均匀速度入口,流体出口为自由出口;通道壁均为润湿性边界,其壁面接触角设定为3π/4。本研究采用四面体网格单元,在接近固液界面的边界层流体行为非常复杂,为了更精准的分析,设定网格数为1000000。连续相在上下两侧入口2和入口3通入,分散相在左侧入口1通入,右侧为流体出口。图1中竖线为两相初始位置,初始时刻右侧所有通道充满连续相,左侧为分散相。
1.2控制方程与两相物理参数设置
模拟基于COMSOL Multiphysics多物理场有限元计算平台,相界面的处理采用水平集法,表面张力等效为水平集变量的梯度与化学势的乘积,然后将其作为体积力加入N-S方程,从而实现对两相流动的求解。据此确定了流体力学控制方程组包括:连续性方程、低雷诺数层流N-S方程和水平集方程,即
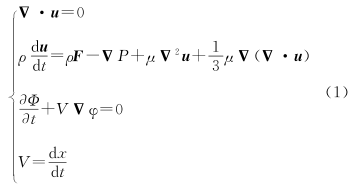
式中:u代表某时刻t下,流体内一点处的流体速度;p为流体密度;μ为流体的黏度系数;F为该点处的微元单位质量力;P为应力;V为运动界面上一点的速度;φ(x,t)为水平集函数,水平集方法描述界面运动时,函数φ(x,t)=0形成的等值面保持与运动界面相对应,可以很容易地表示界面的变化,并且通过g(x,t)可以很容易获得界面法向量和界面曲率等界面几何特征。连续相主要为硅油,并添加了表面活性剂SPAN一80,分散相主要为蒸馏水,并添加了甘油。其中加入表面活性剂是为了降低界面张力,防止生成的液滴相融合。两相物理参数如表1所示。
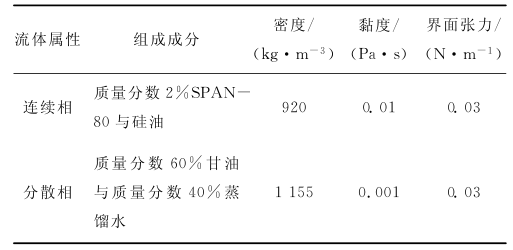
结果与分析
1.液滴的生成
液滴生成的仿真过程中,设定连续相流速为0.6mL/h,分散相流速为0.2mL/h。观察分散相从进入连续相到最终形成分散液滴的过程,液滴的生成过程分为液滴头部伸长和液滴颈部断裂两阶段。图2为聚焦流通道中液滴的生成轨迹。图2(a)~(c)为液滴头部伸长阶段,图2(d)~(f)为液滴颈部断裂阶段。分散相从左部逐渐进入通道并在聚焦流通道交口处与连续相形成两相的交界面,之后液滴的头部逐渐形成并增大,在黏性力和剪切力的共同作用下,液滴的头部被拉伸至临界状态,之后进入到第二阶段。随着分散相不断从左侧流入,液滴形成颈部且颈部越来越细,最终断裂形成一个微液滴。
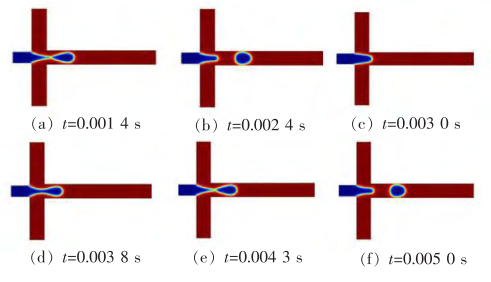
通过仿真分析可知,在微米级通道中黏性流体的雷诺数(Re)远小于1,界面应力占主导,毛细数(Ca)是影响液滴生成的主要因素,两相界面的毛细不稳定性产生液滴。毛细数的表达式为

式中:μ。为连续相黏度;U。为连续相流速;y为两相界面张力。根据芯片的不同结构,临界毛细管数不同,当Ca值小于临界毛细管数时,界面张力引起的应力作用大于黏性应力,液滴界面缩小形成球形,液滴发生破裂,在主通道中形成分散的液滴。
免责声明:文章来源汶颢www.whchip.com以传播知识、有益学习和研究为宗旨。转载仅供参考学习及传递有用信息,版权归原作者所有,如侵犯权益,请联系删除。
审核编辑 黄宇
-
微流控芯片
+关注
关注
13文章
271浏览量
18834 -
微流控
+关注
关注
16文章
526浏览量
18891
发布评论请先 登录
相关推荐
NOVA无误差液滴微流体
Aigtek功率放大器在超疏水表面非接触式操控液滴研究中的应用
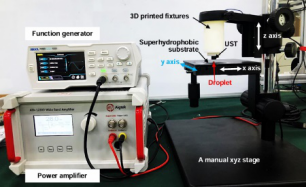
ATA-7030高压放大器在多体系油相液滴交流电场中的应用
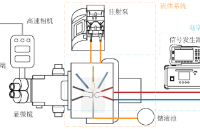
基于轨道电润湿的液滴操控技术,有望用于新一代数字微流控平台
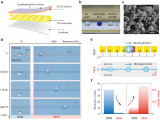
三相微流控系统液滴在液-液界面上的自发转移机制解析
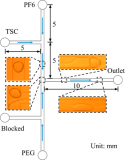
评论