一、当 “传统” 遇上 “智能”
在制造业的长河中,工厂一直是生产的核心阵地。从早期的传统工厂,到如今崭露头角的智能工厂,这一转变承载着科技进步与时代发展的厚重印记。传统工厂,作为工业时代的主力军,曾以规模化、标准化生产推动经济腾飞,为社会积累了大量物质财富。车间里,机器轰鸣,工人们忙碌于流水线,靠着人力与经验,一件件产品被制造出来。然而,随着科技日新月异,消费者需求日趋多元,传统工厂的短板逐渐显现:生产效率提升遭遇瓶颈、产品同质化严重、对市场变化响应迟缓等问题,制约着其进一步发展。
与之相对,智能工厂宛如一颗冉冉升起的新星,在数字化、网络化、智能化技术的簇拥下闪耀登场。它深度融合人工智能、物联网、大数据等前沿科技,为制造业注入全新活力。智能工厂里,自动化设备与智能机器人默契协作,精准高效地完成复杂任务;海量数据实时采集、传输、分析,为决策提供精准依据;生产线能够依据订单需求迅速切换,轻松实现个性化定制生产。这一场景,无疑是科技赋能产业的生动实践,彰显着智能制造的无限魅力。当下,传统工厂与智能工厂并存,它们之间的差异深刻影响着企业竞争力与行业走向。接下来,让我们深入二者内部,一探究竟。
二、生产模式:手工 VS 自动化
传统工厂的生产模式,很大程度上依赖人工操作,是典型的劳动密集型生产。在传统的汽车装配车间,工人们沿着流水线,手工安装零部件,一把扳手、一套螺丝刀,就是他们的主要工具。从车身焊接到内饰装配,一道道工序,都离不开工人的双手与经验。这种模式虽然具有一定灵活性,能随时依据工人经验对产品进行微调,但弊端也十分明显。一方面,人力成本居高不下,随着人口红利逐渐消失,劳动力成本持续攀升,压缩了企业利润空间;另一方面,人的体力与精力有限,长时间高强度工作易导致疲劳、失误,生产效率难以实现质的飞跃,产品质量也会因人为因素起伏不定。
反观智能工厂,自动化生产成为主角。走进智能家电制造车间,映入眼帘的是排列整齐的自动化机械臂,它们精准地抓取、焊接、组装零部件,动作行云流水,误差控制在极小范围内。智能机器人依据预设程序,不知疲倦地运行,不仅生产速度远超人工,而且产品一致性极高。自动化生产线还能根据订单需求,快速切换生产任务,实现不同型号产品的无缝衔接。例如,智能手机生产线上,可迅速从生产 A 款手机调整为生产 B 款,满足市场多变的需求。在这里,人力从直接生产者转变为设备监控者、管理者,大大降低了人力成本,提升了生产效率与产品竞争力。
三、数据管理:滞后 VS 实时精准
传统工厂的数据管理,多依赖人工统计,弊端重重。在许多传统机械加工厂,工人每日手工记录设备运行时长、产量、物料消耗等数据,下班后再汇总上报。这一过程不仅效率低下,往往耗费大量人力与时间,还极易出错。数据更新存在严重滞后性,管理层拿到的可能是昨日甚至上周的生产数据,难以及时把握当下生产动态。而且,人工记录易受主观因素干扰,数据准确性大打折扣,为后续分析决策埋下隐患。此外,大量纸质记录或零散电子表格存储的数据,查询不便,历史数据在人员流动、交接不善时还易丢失,无法为设备维护、生产优化提供可靠依据。
智能工厂则依托物联网、大数据技术,开启数据管理新篇章。车间内,传感器如同敏锐的神经末梢,实时采集设备温度、压力、振动频率等各类数据,通过无线网络即时传输至云端数据中心。大数据分析平台迅速对海量数据清洗、挖掘、分析,将生产状况可视化呈现于管理者眼前。以电子制造为例,管理者通过手机 APP,就能实时查看生产线各环节产量、良率、设备利用率,精准定位生产瓶颈;还能依据数据分析预测设备故障,提前安排维护,避免停机损失。在这里,数据不再是冰冷的数字,而是驱动生产优化、决策科学的 “智慧大脑”,让智能工厂时刻保持最佳运行状态。
四、生产线应变:僵化 VS 灵活敏捷
传统工厂的生产线,往往是为特定产品量身定制,具有高度的专一性。一条传统的食品加工生产线,从原料清洗、切割、加工到包装,各环节设备紧密相连,布局固定,仅适配某几款产品。一旦市场需求有变,如推出新口味、新包装规格,生产线调整起来极为棘手。改造不仅耗时费力,涉及设备拆卸、重新安装调试,还需停产,期间损失大量产能与订单。而且,传统生产线对订单批量要求高,小批量订单生产成本飙升,导致企业在面对小众市场、定制需求时,常因成本顾虑望而却步,错失商机。
智能工厂的生产线则尽显灵活敏捷。以电子制造领域为例,智能生产线借助模块化设计理念,将生产流程拆分为多个独立模块,像乐高积木般可按需组合。当企业计划推出新款智能手机,只需在设计端调整模块参数,生产线上快速更换对应模块,如摄像头模块、芯片主板模块等,即可实现新品快速上线。同时,虚拟仿真技术助力企业在数字世界模拟生产线运行,提前优化流程、排查问题,确保实际调整高效无误。智能工厂还能轻松应对小批量、定制化订单,通过柔性生产系统,在同一条生产线交替生产不同型号产品,甚至实现单品定制,满足消费者日益个性化的需求,为企业开拓多元市场、提升客户满意度提供有力支撑。
五、质量管控:事后抽检 VS 全程把控
传统工厂的质量管控,多依赖事后抽检。在传统服装加工厂,一批成衣生产完成后,质检员依据既定比例抽取样本,检查尺寸是否合规、有无脱线、色差等问题。这种方式覆盖面有限,未抽检产品质量难有十足保障,犹如 “管中窥豹”,易遗漏隐患。一旦抽检发现问题,往往大批产品已制成,返工成本高,还可能延误交货期。而且,抽检结果反馈滞后,难以及时纠正生产过程偏差,质量问题频现,导致客户投诉增多,品牌形象受损。
智能工厂则借助传感器、人工智能等技术,实现质量全程精准把控。在精密机械制造中,智能传感器实时监测零件加工精度,从尺寸、粗糙度到内部应力,数据瞬间传输至中控系统。AI 算法依据海量数据建模,精准预测质量走势,一旦参数偏离标准,立即自动调整设备参数,确保加工精准无误。同时,机器视觉系统全方位 “审视” 产品外观,快速识别划痕、凹陷等细微瑕疵,将次品拦截在生产线内。全程质量管控不仅大幅降低次品率,还能依据质量数据反向优化生产流程,持续提升产品质量,为企业赢得市场青睐。
六、人机协作:简单分工 VS 深度融合
传统工厂里,人机协作模式简单,分工明确且界限分明。工人在生产线旁,从事着诸如零部件组装、物料搬运等直接操作任务,机器则按固定程序运行,辅助工人完成部分重复性、高强度工序。二者如同两条平行线,虽有交集,却缺乏深度互动。工人依据经验判断生产状况,机器无法主动感知工人需求,一旦出现异常,如设备故障、物料短缺,信息传递滞后,易造成生产停滞。而且,工人长期从事单一重复劳动,易疲惫厌烦,技能提升受限,企业也难以充分挖掘人力与机器的协同潜能,生产效率与创新能力遭遇瓶颈。
智能工厂中,人机协作迈向深度融合新阶段。在航空发动机制造车间,工人佩戴智能手环、AR 眼镜等穿戴设备,与智能设备实时互联。工人靠近设备,AR 眼镜自动投射操作指引、设备参数,辅助精准作业;手环监测工人身体状态、动作轨迹,预防疲劳操作,保障生产安全。智能机器人不仅承担焊接、打磨等繁重任务,还能依据视觉识别、力觉感知技术,与工人协同完成复杂装配,如发动机叶片与轮毂的精密对接。当工人手动微调时,机器人实时感知力度、位置变化,自适应配合,确保装配精度。此外,人机协作过程中产生的大量数据,经分析反馈用于优化生产流程、改进机器人算法,促使二者协作愈发默契,工人得以从简单劳动中解放,专注于工艺创新、质量把控等高附加值环节,为企业创造更多效益。
七、成本效益:高耗低效 VS 节能高效
传统工厂成本结构不佳,效益提升困难。能源利用上,设备老旧、工艺落后,能源消耗量大且效率低,如传统铸造厂,熔炉热效率仅 30%-40%,大量热能散失,电费、燃料费居高不下。设备维护依赖人工巡检,故障难以及时发现,一旦突发故障,维修耗时久,停产损失大,还需常备大量备件,占用资金。生产计划粗放,为满足订单需求常过量采购、生产,库存积压严重,占用仓储空间,资金周转缓慢,仓储成本、物料贬值风险高,诸多因素共同挤压利润空间,企业盈利能力受限。
智能工厂则借助科技之力,实现成本效益优化。一方面,节能技术广泛应用,智能照明、变频调速等系统依生产节奏自动调控,降低能耗;能源管理系统实时监测分析,挖掘节能潜力,如某智能玻璃厂,优化生产工艺与设备后,单位产品能耗降 20%。另一方面,设备预测性维护成为常态,传感器实时监测,AI 算法预测故障,精准安排维护,减少突发停机,降低维修成本 30% 以上。智能排程系统依据订单、库存、产能精准规划,优化物料配送,实现准时生产,库存周转率提升 50%,库存成本锐减,企业得以在降本同时,灵活应对市场,资金回笼加速,经济效益显著提升。
八、未来已来,路在何方?
通过对智能工厂与传统工厂全方位对比,二者差异一目了然。智能工厂凭借自动化、智能化、数字化等优势,在生产效率、产品质量、成本控制、市场响应等关键维度全面超越传统工厂,代表着制造业先进生产力方向。在科技浪潮汹涌、市场竞争白热化的当下,传统工厂向智能工厂转型已是大势所趋。传统工厂唯有积极拥抱变革,逐步引入先进技术、优化管理模式、培养复合型人才,方能突破困境,重焕生机。而智能工厂也并非发展终点,持续的技术创新、更深度的人机融合、更广泛的产业协同将推动其迈向新高度。相信在不久将来,智能工厂将成为制造业主流形态,为经济高质量发展注入磅礴动力,助力中国从制造大国稳步迈向制造强国,开启制造业辉煌新篇章。
-
制造业
+关注
关注
9文章
2265浏览量
53891 -
智能工厂
+关注
关注
3文章
1024浏览量
42725 -
智慧工厂
+关注
关注
2文章
414浏览量
27727 -
数字化工厂
+关注
关注
1文章
65浏览量
6276
发布评论请先 登录
相关推荐
以智能制造为导向的数字孪生工厂构建方法与应用
数字化工厂 制造业转型升级的必由之路 珠海先达

珠海先达数字化工厂:制造业转型的新引擎
智慧工厂:制造业数字化转型的新引擎
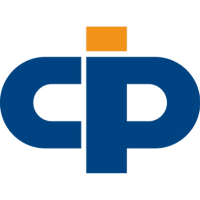
评论