摘要
今年以来,包括四大关键材料及辅助材料在内的材料企业在产品创新方面有了不少新成果,也反映出锂电材料行业发展新趋势。
尽管新能源汽车产销量连年上升,但要想在市场竞争中与燃油车抗衡,新能源汽车还需进一步提升性价比。所谓性价比就是里程成本比,这一提升需要电池性能的改进、整车电耗的下降和效率的提升、充电设施的便利化以及安全管理,其中最重要的是提升电池性能。
国家政策正在引导动力电池产业链企业加大研发力度以提升电池性能,比如设置到2020年,动力电池单体比能量达到300瓦时/公斤以上,力争实现350瓦时/公斤的目标;专门设立新能源汽车重点专项来推动代表性企业进行能量密度的攻坚战;补贴发放与能量密度挂钩等。
在政策的牵引下,动力电池企业正联合上游材料企业,一起共同大力投入研发,通过改进正负极材料、隔膜、电解液等原材料体系及优化PACK结构等,希望尽可能快地提升电芯及电池系统能量密度。其中,提升材料性能被业界视为提高电芯能量密度最根本的途径。
正极材料领域,企业致力于开发各类高电压、高比容量、高性能正极材料,磷酸铁锂提高压实密度、降低成本,三元从NCM523向NCM622过渡;负极材料领域,石墨类负极材料性能提升的同时,硅碳负极、软碳等作为研发重点,部分企业已经量产。
电解液领域,配套三元动力电池电解液已经相对成熟,高镍-硅碳动力电池电解液及相关电解质、添加剂等成为研发重点,部分企业成功研发并量产;隔膜领域,企业为助力电池安全、能量密度的提升及成本的下降,对隔膜产品及生产工艺均有所改进;其他材料领域,6μm高端柔性铜箔、国产铝塑膜加快进口替代、纯度高及管径小的碳纳米管等值得关注。
且看下文这14家材料企业的创新成果:
正极材料
1、金锂科技
金锂科技新研发的磷酸亚铁锂材料技术具备三大创新性:1)开发独特偏磷化材料配方,可以使用氧化钛生产过程产生的无水磷酸铁原材料生产出合格的产品;2)采用新型复合铁源技术,可以将磷酸铁锂粉体压实提高到2.7g/cm3以上,极片压实密度做到2.4-2.5g/cm3;3)利用自主技术解决了粉体密度小、生产效率低的问题,在核心工序烧结中可以提高1倍以上生产效率。
金锂科技称,通过以上技术改进,电池企业可以降低10%左右的制造成本,提高压实密度,能够显著提高磷酸铁锂能量密度。
2、四川富骅
四川富骅高能量密度锂离子电池正极材料镍钴铝酸锂(NCA)及其聚合物锂离子电池的制备方法突破了使用传统固相法生产该材料时性能和批次稳定性差的不足,能够达到甚至超过使用液相法生产该正极材料的水平,在改善产品性能的同时使生产该正极材料的成本大大降低,并且还避免了三废的排放。
在产品性能上,该正极材料是磷酸铁锂正极材料或尖晶石型锰酸锂正极材料的2.5-3倍;体积能量密度可达到900-930Wh/L,实现了锂离子动力电池的高能量密度达到甚至超过300Wh/kg的目标,而且安全性能和循环性能达到甚至超过普通电压正极材料水平。
负极材料
3、正拓能源
正拓能源研发生产的硅碳负极可取代传统的石墨负极材料,具有克容量高(400mAh/g-650mAh/g)、循环性能好等优点。以ZT-SC420为例:该产品首次放电容量≥420mAh/g;库伦效率≥91%,1000周0.5C循环后容量保持率≥80%。
这款硅碳负极材料有三大技术创新点:❶纳米结构化。采用特有的纳米制备技术,从硅材料内部解决其锂离子嵌入导致的体积膨胀问题,从而提高硅碳材料的循环性能;❷碳包覆处理。采用均匀可控的碳包覆技术,解决了包覆不均匀导致硅材料与电解液中HF组分与硅反应导致电性能恶化的问题;
❸二次造粒。采用二次造粒所得的碳包覆纳米硅材料,可存在于一次石墨颗粒之间的缝隙中,为硅材料提供膨胀空间,大大改善了硅-碳负极材料的循环稳定性。
4、深圳斯诺
深圳斯诺成立于2002年02月,是专业研发和生产锂离子电池负极材料的国家级高新技术企业。沉淀多年,深圳斯诺在2017年进入发展快车道。在产品方面,该公司继续发力,比如推出动力电池负极材料MAG-09/10系列产品;加大石墨化加工研发力度,完善产业链布局。
深圳斯诺自主创新的新能源汽车动力电池负极材料MAG-09/10系列产品,具有优异的长循环性能:1C充放10000次容量保持率达80%以上,2C充放1000次容量保持率达95%以上;良好的低温放电性能:-20℃放电容量比85%以上。目前,这一系列产品大量应用于国内各大动力电池企业,受到客户广泛使用和好评。
5、欧铂新材
软碳-PSCAM280是依托欧铂新材和韩国PowerCarbonTechnology公司在先进碳材料领域的技术,设计开发的适用于快充动力电池的软碳负极材料。该材料具有晶面间距大(d(002)=0.348nm),晶粒尺寸小(Lc=2~20nm),便于锂离子的快速嵌入和脱嵌。
其创新性和先进性主要体现在:1、通过原位包覆,提升了软碳的导电性,进一步提高了材料的倍率性能;2、通过原料控制,有效降低了铁、硫等杂质元素的含量,提升了产品克容量和循环性能;3、通过对产品预处理、碳化温度、气氛的细微控制,实现了产品批次一致性的有效控制。相较于目前市场上的同类产品具有克容量高(280mAh/g)、首次效率高(85%)、倍率性能和循环性能优异(客户验证4C循环1200容量保持80%以上)等优点。
电解液/电解质
6、新宙邦
目前硅碳电解液大多是采用高含量的FEC来稳定硅碳负极的SEI,以此来改善硅碳负极的循环性能,但高含量的FEC容易被高镍正极或高电压NMC正极所催化分解,从而劣化电池的高温存储性能和高温循环性能。
在此背景下,新宙邦公司自主开发了新型正极成膜添加剂LDY196,其能明显抑制电解液在高镍正极和高压NMC正极上的氧化分解,从而能有效改善高含量FEC电解液在高镍或高电压NMC电池下的高温不足和循环不足的问题。
通过新型正极成膜添加剂LDY196,负极成膜添加剂VC,FEC,锂盐型低阻抗添加剂等开发了一系列电解液产品,该系列电解液产品用于高镍正极/硅碳负极的动力电池体系中,能满足循环1000周的要求,并能获得优良的高温性能和低温性能。
该系列产品广泛适用于高能量密度NCM811、NCA、高电压三元正极配硅碳负极动力电池,已经在国内外的中高端客户中得到大批量应用。
7、蓝德能源
蓝德能源采用离子液体复合液态电解质代替传统EC基复合溶液/LiPF6液态电解质,实现在电导率不变的情况下,提高溶剂稳定性,同时保护三元高电压电极,抑制其活性物质溶出,抑制电解质溶液与活性物质直接接触,从而提高电池可充放电压,最终实现容量的大幅提高。
加入离子液体复合电解质后,电解质中的保护剂会自主通过静电作用吸附在电极颗粒表面,实现对电极材料的有效保护。离子液体复合电解液在5.5V时都能保持非常良好的稳定性,电解液不发生分解,大幅度提高电解质的使用电化学窗口,从而提高三元电池的能量密度。
离子液体复合电解液可提高15%左右的能量密度,并延长电池的使用寿命,大大提高安全性。
此外,采用哌啶、吡咯类多碳复合离子液体添加剂与传统EC基复合溶液/LiPF6液态电解质混合的方式大幅度提高三元电池的能量密度。由于所需含量较少,通常为1%-3%,可实现电解液性能大幅度提高,同时具备价格竞争力。
隔膜
8、纽米科技
纽米科技是国内首家突破5μm超薄锂电隔膜技术稳定批量生产的企业,同时也开创了超薄锂电隔膜国产化的先河。5μm产品既保证优越的通透性又不失产品实用方面的强度特征。该产品在国内率先实现了进口同类产品的替代,再结合功能涂覆,为电池体系提升容量,为终端锂电产品实现轻薄化提供了完美选择。
纽米科技表示,5μm产品在2017年已开始批量供货,并呈现出供不应求的状态。在建新产线完全以生产超薄湿法隔膜为前提设计,预计在2018年增大5μm出货量。
与此同时,公司经过不断的工艺实验和技术改进,于2017年初成功开发出一款名为HS(高强度)12μm产品。该产品与市场同等厚度的列产品比较,其强度和耐电压击穿能力远高于市场常规产品,同时保持了隔膜内部结构的稳定性和孔均匀性。
据介绍,12μm厚度的产品强度达到了16μm产品级别强度,更薄的隔膜应用在电池体系中在提升了电池掉容量的同时也保证了其安全性能,更完善的结晶度也使隔膜在电池工作时的稳定性增加,保证了电池安全正常的工作。12μm产品已于今年4月份正式批量供货。
9、安瑞达
今年安瑞达推出多款隔膜新产品。7月,安瑞达陶瓷涂覆隔膜开始应用市场,产品采用高纯度(>99.95%)原料,保证电池不引入杂质离子的同时,可通过采用特殊憎水性胶黏剂,对电池装配过程中的水分进行控制。该产品基材具有稳定黏附力,可确保不掉粉及产品透气性的稳定。10月,安瑞达高强度单层涂覆隔膜ASC2024,ASC1614研发成功,并成功应用市场。
值得一提的是,安瑞达自主研发设计了干法锂电池隔膜的生产技术与制备工艺,通过先进地在线热处理装置和精确地温度数字化控制技术,安瑞达突破了批量生产薄膜结晶度控制难的问题,相关产品结晶度能够达到±3%的水平,提高了隔膜孔径、孔隙率、透气度等关键参数的均一、稳定性。
10、顶皓新材
顶皓新材研发的锂离子电池用多层复合功能隔膜采用耐热性能更好的PET、PIB等聚合物多孔膜作为基材,耐热性提升,在200℃高温下加热1h以内,热收缩率小于1%;闭孔层的引入使电池隔膜在不正常充放电过程中,温度升高超过110℃,有机高分子微球通过膨胀实现隔膜孔隙率降低,切断了锂离子的传输通道,提高了电池的安全性。
上述多层复合功能隔膜具备以下良好性能:1)涂层间共同作用改善了聚烯烃类多孔膜的收缩、短路等现象;2)电池隔膜安全性能在原有基础上大幅度提升,可以应用于动力电池大功率充放电;3)成本降低,安全性提高,适用性强。
铜箔/铝塑膜/碳纳米管/极耳
11、诺德股份
诺德股份6μm锂电高端铜箔的面密度仅为52g,比72g的8μm锂电铜箔在重量上更轻。截止至2017年10月份,诺德股份6μm锂电高端铜箔销售额破亿元大关,市场占有率达40%,主要供应国内前几大锂电池制造商。
值得一提的是,多孔铜箔可直接提升锂电池比能量。如同等规格的箔材,孔隙率17%的微孔箔重量建设17%;同等面密度,负极压实性得到提升。多孔铜箔将成为高档锂电池负极材料载体的发展趋势。
诺德股份称,在锂电池体积相同情况下,如果负极集流体使用有孔电解铜箔,可实现以下四大效果:一是孔隙可使表面积增加,能容纳更多负极材料,增加锂电池电容量;二是多孔铜箔和负极材料接触面积增加,铜箔和负极材料粘性提高,能够防止电池充电放电后负极材料出现脱落,以获得更高电容量保持率,延长电池使用寿命。
三是弥补涂布不均问题。锂离子能够利用有孔电解铜箔中的孔隙在其两面之间自由移动,使锂离子由集中区向稀疏地带移动,以补偿涂布不均问题;四是单位重量有孔电解铜箔比无孔电解铜箔更长,单位长度下有孔电解铜箔能分切成更多极片,节省用户使用及购买成本。
诺德股份利用独有工艺生产的电解铜箔孔隙透析率均匀、无毛刺,铜箔物理性能稳定,优于市场上使用激光或机械打孔技术。目前,该产品尚在研发试制阶段。
12、苏达汇诚
立志要成为国产高端铝塑膜缔造者的苏达汇诚将在研发、技术、设备、原料等方面取得突破从而提升国产铝塑膜的品质,充分利用公司的技术优势为电池企业提供优质铝塑膜,替代进口占据高端铝塑膜市场。
具体来看,在制造工艺方面,苏达汇诚设立了千级净化车间,室内生产温度严格控制在(23±2)℃、湿度(55±5)%,确保生产环境最优,减少铝塑膜产品内异物数量。在生产设备方面,苏达汇诚引进成套日本生产设备,采用三菱、富士等一流元器件实现高精度生产,确保产品的稳定性、一致性和高品质。
在技术提升方面,苏达汇诚采用热法工艺,不需要依附日本的CPP从而控制成本和品质,以高温粘结树脂层来粘合铝箔与PP热封层,产品具有优异的耐电解液腐蚀性。与此同时,苏达汇诚还与韩国、日本等铝塑膜生产企业展开技术合作,使得公司产品在冲压成型、耐电解液腐蚀性能和热封性能等方面达到日韩水平。
13、金百纳
金百纳的核心技术是碳纳米管的制备技术,具有纯度高、管径小等优点。用其分散出来的新型碳纳米管导电浆料(GCN168-40H),与同类碳纳米管导电浆料产品相比具有铁杂质含量低,导电性好等优点,能够更好的满足动力电池对安全性和导电性需求。
与传统的铁系碳管对比,未提纯前的铁系碳管铁杂质含量可以达到4000ppm以上,而金百纳碳纳米管的铁杂质含量则为50ppm以下;在改进的碳管生长工艺后,碳纳米管的管径可达到5-12nm,具有比传统的钴系碳管10-25nm更加小的管径。
在应用于同一种正极材料中,GCN168-40H比传统的碳纳米管导电浆料的导电性要好。可以用更小的添加量达到相同的导电性能,而添加更少的导电剂意味着可以添加更多的活性材料,从而提高电池的能量密度。
14、鑫越新材料
鑫越新材料针对圆柱型动力电池(18650、26650、32650)和方形钢壳动力电池的不同属性,针对性地研发了铜镍及镍铜镍系列负极极耳。具体产品型号(以下是鑫越新材料内部代码)包括:CN-2(铜镍比例50%:50%,±2.5%)、CN-3(铜镍比例24%:76%,±2.5%)、NCN系列(镍铜镍比例25%-35%:35%-50%:25%-35%,±2.5%)及产品。
-
材料
+关注
关注
3文章
1229浏览量
27307
原文标题:【桑顿新能源•热点】提高能量密度关键在材料 14家材料企业创新成果显著
文章出处:【微信号:weixin-gg-lb,微信公众号:高工锂电】欢迎添加关注!文章转载请注明出处。
发布评论请先 登录
相关推荐
XRF技术在材料分析中的应用
欣界能源发布全球首创480Wh/kg高能量锂金属固态电池
电子产品结构与导热材料解决方案
导热界面材料对降低接触热阻的影响分析
KLA纳米压痕仪对电池材料的测量
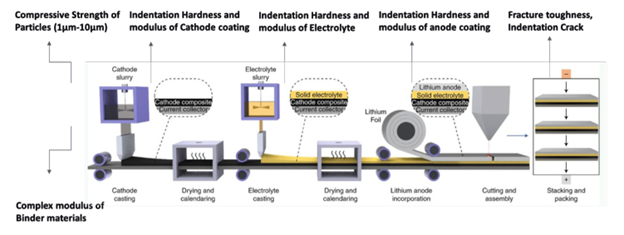
PCB高频材料板:科技创新的坚实基石
vivo即将推出硅碳负极蓝海电池,能量密度显著提升
紫外激光打标机适合在哪些材料表面进行标记
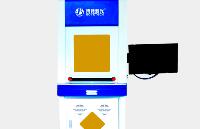
韩国研发出快速充电的高能量、高功率混合钠离子电池
大有用处!柯肯达尔效应诱导超高镍正极材料单颗粒的应力分布
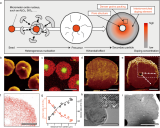
评论