引线键合检测
引线键合完成后的检测是确保产品可靠性和后续功能测试顺利进行的关键环节。检测项目全面且细致,涵盖了从外观到内部结构的多个方面。
以下是对各项检测项目的详细分述:
目检
球的推力测试
拉线测试
键合的失效可靠性
1
目检
目检是在显微镜下对完成品进行的检查,主要关注以下几个方面:
焊球短路:确保金球与相邻的金球或金属引线之间无短路触碰,避免电流异常流通。
焊点的位置偏移:检查金球是否在焊垫有效面积的75%以内,且金球与相邻金球或金属引线之间无触碰,确保键合位置准确。
焊球大小:最小球径不得小于2倍线径,最大球径不得大于5倍线径,避免过大或过小影响键合强度。
第二焊点的鱼尾大小:第二焊点(鱼尾)的宽度和长度需符合规定范围,宽度不得小于1.2倍线径或大于5倍线径,长度不得小于0.5倍线径或大于3倍线径,确保焊点形状符合标准。
错焊:核对实际焊线位置与键合装配图的要求是否一致,避免误焊导致功能异常。
线尾残留:检查线尾是否残留并黏着在铝垫上或手指区、铜板区、连接带上,残留长度需符合规定范围,避免影响后续工艺。
引线受损:检查金属引线本身和球颈部分是否存在受损、刮伤等,受损程度不得超过25%线径,确保引线完整性。
碰线、线距不足、塌线:检查金属引线之间或金属引线与芯片之间是否存在短路,线弧与线弧、线弧与芯片边缘、线弧与其他引脚之间的间距需符合规定,避免短路和塌线现象。
键合线的弧度不良:检查线弧的弧度是否在规格范围内,避免弧度过大或过小影响键合效果和美观。
漏焊线:核对键合装配图,确保规定应该焊线的位置已正确焊线,避免漏焊导致功能缺失。
键合造成晶粒崩角、隐裂:检查作业中是否因外力伤及晶粒实体,导致部分晶粒缺失损坏,影响芯片性能和可靠性。
第二焊点颈部断裂:检查第二焊点的颈部是否存在拉折、撕裂、裂痕等现象,确保焊点强度符合要求。
通过目检,可以及时发现并排除潜在的缺陷和问题,确保引线键合的质量和可靠性。同时,目检也是后续检测项目的基础和前提,为后续检测提供了重要的参考和依据。
2
球的推力测试
球的推力测试,也被称作键合点强度测试,是评估引线键合质量的重要手段。该测试旨在通过精确的推刀夹具和测试平台,模拟实际使用中可能遇到的剪切力,从而检测焊球与芯片或基板之间的结合强度。
测试准备与设备
推刀夹具:选用刚硬且精密的推刀夹具,确保测试的准确性和可靠性。
三轴测试平台:通过三轴测试平台,可以精确控制测试头的移动,确保测试位置准确无误。
测试角度:剪切工具与芯片表面应呈90°±5°的夹角,以确保测试力的均匀分布。
传感器:定期校准的传感器用于测量推力大小,其负载能力应超过焊球最大剪切力的1.1倍,以确保测试的准确性。
光学芯片与显微镜:高功率光学芯片和稳定的双臂显微镜用于辅助观察测试过程,确保测试操作的精确性。
摄像系统:配置摄像系统进行加载工具与焊接对准、测试后检查、故障分析和视频捕获,便于后续分析和记录。
失效模式与判定
焊球在推力作用下的失效模式多种多样,主要包括以下几种:
球脱模式:焊球整体脱离,可能包含或不包含形成的金属间化合物(如铜铝材料的残留)
焊接面残留:经推力作用后,焊球的焊接面会残留铜铝材料或仅残留引线本身材料(如铜材料)
焊垫金属脱离:焊垫金属从焊垫上脱离,严重时甚至会将芯片的基底材料带出
推刀位置错误:推刀位置设置过高可能推断引线颈部,设置过低则可能将整个焊垫层推走
通过球的推力测试,可以及时发现并评估引线键合的强度和质量问题,为产品的可靠性和后续功能测试提供有力保障。同时,该测试也是质量控制和工艺改进的重要依据。
3
拉线测试
拉线测试(Wire Pull)是一种用于监控键合线弧质量和工艺可靠性的重要测试方法。该测试通过施加拉力来评估键合线的强度,并确定其最弱位置。
测试位置与设备
测试位置:拉线测试通常选择在距离第一焊点或第二焊点1/3的位置进行,以模拟实际使用中可能受到的拉力。测试位置的选择应确保能够准确反映键合线的强度。
测试设备:拉线测试需要使用专门的拉线钩和测试设备,如拉力计或拉力测试机。这些设备能够精确控制拉力的施加,并记录测试过程中的数据。
测试方法
将拉线钩移动到焊线下方,并沿Z轴方向(即垂直于芯片表面的方向)向上拉扯。测试可以是破坏性的,即直到焊接被破坏;也可以是非破坏性的,即达到预先定义的力度后停止。
拉力范围与评判标准
拉力范围:拉力的测试范围通常根据具体需求而定,常见的范围包括0~100g、0~1kg和0~10kg等。
质量评判:拉线测试后,需要对键合引线的各个部分进行质量评判。评判内容包括第一焊点的焊垫和焊球、球颈、键合引线、焊接位置以及第二焊点的线尾等。根据评判结果,可以确定键合线的强度和质量是否符合要求。
第二焊点拉线力测试
测试目的:第二焊点拉线力测试是评估第二焊点键合强度的一种方法。它通过观察拉线后残留金属的状况,为工艺分析提供重要信息。
测试方法:进行第二焊点拉线力测试时,拉线钩应尽量靠近第二焊点,以确保线弧在第二焊点处断裂。该测试是破坏性的,通常不作为标准测试项,但在特定情况下可用于分析工艺问题。
4
键合的失效可靠性
在超声波焊键合过程中,焊盘产生弹坑是一种常见的缺陷现象,它指的是焊盘金属层下方的二氧化硅层或其他层次受到破坏。弹坑通常肉眼难以察觉,但其对电性能的影响却不容忽视。
弹坑产生的原因
弹坑的产生源于多种因素,主要包括以下几个方面:
超声波能量过高:当超声波能量超过一定阈值时,会导致硅晶格点阵的破坏,进而形成弹坑。过高的能量输入使得焊盘下方的材料无法承受,从而产生损伤。
键合压力过大:在楔焊键合过程中,如果键合力过高,同样会对焊盘下方的材料造成压迫,导致弹坑的产生。
焊球尺寸不合适:如果焊球太小,坚硬的键合工具在键合过程中可能会直接接触到焊盘金属层,而非通过焊球进行缓冲,从而增加焊盘受损的风险。
焊盘厚度不足:焊盘的厚度是影响其抗损伤能力的重要因素。当焊盘厚度小于一定值时(如0.6微米以下),其抵抗外力破坏的能力会显著降低,更容易产生弹坑。
材料硬度不匹配:焊盘金属和金属引线的硬度如果匹配不当,也可能导致弹坑的产生。硬度差异过大时,较软的材料更容易受到损伤。
铝丝超声波焊键合的特殊性:在铝丝超声波焊键合中,由于铝丝的硬度相对较高,如果工艺参数控制不当,也容易导致晶圆焊盘产生弹坑。
芯片本身的问题:芯片本身的质量问题,如材料缺陷、加工精度不足等,也可能导致弹坑的产生。
晶圆测试时的损伤:在晶圆测试过程中,如果探针操作不当,也可能刺伤焊垫,进而引发弹坑问题。
弹坑对可靠性的影响
弹坑的存在会严重影响键合的可靠性。首先,弹坑会破坏焊盘与金属引线之间的电气连接,导致电路性能下降或失效。其次,弹坑还可能成为潜在的裂纹源,随着时间和环境的变化,裂纹可能逐渐扩展,最终导致整个键合结构的失效。
因此,在超声波焊键合过程中,必须严格控制工艺参数,确保焊盘、焊球、金属引线等材料的匹配性,以及芯片本身的质量。同时,在晶圆测试和后续处理过程中,也需要采取适当的措施,避免对焊垫造成损伤。通过这些措施,可以有效降低弹坑产生的风险,提高键合的可靠性和稳定性。
弹坑缺陷与化学腐蚀分析
弹坑是超声波焊键合中常见的一种缺陷,它指的是焊盘金属层下方的二氧化硅层或其他层次受到破坏。为了深入分析弹坑缺陷,通常需要进行化学腐蚀分析。
这一分析过程涉及将焊区的金属铝腐蚀掉,以观察金属间化合物的覆盖率和焊区金属层下方电路是否有损伤。
键合点的质量与可靠性问题
在实际生产过程中,键合点可能会遇到多种问题,如开裂、翘起、尾部不一致以及剥离等。这些问题可能由多种因素导致,包括引线通道不干净、进料角度不对、劈刀堵塞、引线夹污染、夹力或距离不正确、张力不正确等。此外,金属间化合物的形成、引线弯曲疲劳、腐蚀、金属迁移以及振动疲劳等也是影响键合可靠性的主要原因。
影响键合可靠性的主要因素
焊接面绝缘层未去除干净:如芯片键合区的光刻胶或窗口钝化膜残留,会导致金属间键合不良,形成绝缘夹层,增加接触电阻,降低键合可靠性。
金属层缺陷:如芯片金属层过薄、有合金点或黏附不牢固,会导致键合时无缓冲作用,形成缺陷,或压焊点容易脱落。
表面沾污:各部件在各个环节均可能产生沾污,如灰尘、有机物、钠等,会导致原子不能互相扩散,影响键合质量。
材料间接触应力不当:键合应力过小会导致键合不牢,过大则会影响键合点的机械性能,甚至损伤芯片材料。
引线框架腐蚀:镀层污染过多及较高的残余应力会导致引线框架腐蚀,影响键合可靠性。
-
检测
+关注
关注
5文章
4492浏览量
91522 -
引线键合
+关注
关注
2文章
20浏览量
8210
原文标题:一文了解引线键合检测
文章出处:【微信号:芯长征科技,微信公众号:芯长征科技】欢迎添加关注!文章转载请注明出处。
发布评论请先 登录
相关推荐
有偿求助本科毕业设计指导|引线键合|封装工艺
集成电路封装中的引线键合技术

LED引线键合的检测内容与工艺评价
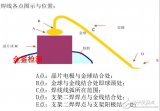
LED引线键合工艺评价
引线键合是什么?引线键合的具体方法
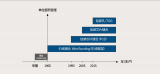
什么是引线键合?引线键合的演变
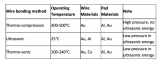
3D 结构和引线键合检测对比
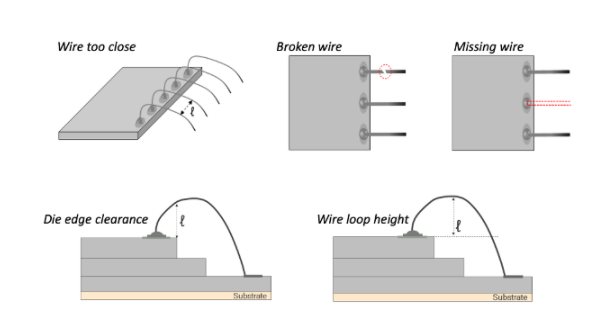
优化关键工艺参数提升功率器件引线键合的可靠性
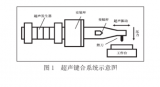
带你一文了解什么是引线键合(WireBonding)技术?
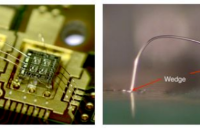
评论