前言
通过一系列的工艺革新的创新,大族激光已经在焊接效率、质量以及质检控制上得到了明显的改善和提升,协助众多动力电池客户有效降低生产成本,提升电池产品的质量可靠性与使用安全性。
激光焊接作为动力电池制造过程中的重要工艺,直接关系到产品的最终性能。
数据显示,在当前整个动力电池制造(电池、模组、Pack)中,约有19个主要构件部位需要焊接,其中11个焊接当前必须用激光焊接,5个焊接可能用到激光焊接,仅一个电池盖板,就有6-8处需激光焊接的点位,毫不夸张的说,激光焊接的质量直接影响到动力电池的质量。
从既有激光焊接在动力电池制造领域的发展历程来看,国内激光技术已走过了“完成功能”阶段,基本完成“自动化”阶段,在锂电池厂对设备要求越来越高的背景下,正在向着“智能化”的方向高速进发。
“从国内动力电池企业的实际反馈来看,其对于锂电设备的要求正在朝着更高效、更可靠、更智能的方向迈进。”在2017高工锂电年会上,大族激光副总裁黄祥虎坦言,客户需求压力下,锂电激光设备企业需要做持续的工艺革新和升级来进行提前应对。
黄祥虎介绍,大族激光在该焊接领域做的技术探索和升级包括焊接技术、焊接速度、焊接质量、过程控制、MES导入等多个环节。
作为国内激光设备领域巨擘,大族激光可以提供包括整套动力电池、电芯封口(侧焊,顶焊)封栓、软连接、电池模组焊接、防爆阀焊接、防爆罩焊接、节流阀焊接、集流体焊接、极柱焊接、封栓焊接、模组和电芯及隔离膜清洗、电芯打标、极耳切割等电池相关部件的生产制造解决方案。截至目前,其已进入包括宁德时代在内的国内一线企业供应链。
通过一系列的工艺革新的创新,大族激光已经在焊接效率、质量以及质检控制上得到了明显的改善和提升,协助众多动力电池客户有效降低生产成本,提升电池产品的质量可靠性与使用安全性。
装备效率显著提高
“随着产能要求不断扩大,大功率激光器、振镜及高自动化流水线等产品应用加大,直接导致改版组件焊接效率也由过去的6-10ppm,提高到20-30ppm。” 黄祥虎介绍。与此同时,激光焊机的另一个领域,电芯封口激光焊接设备也由过去的6ppm发展到12ppm,目前可达20ppm,效率增速惊人。
实际上,焊接效率的提升几乎具备着“牵一发而动全身”的特点,随着模组装配、焊接、检测自动化程度等各个生产、工艺环节效率的不断提高,焊接设备也由过去简单的工作台,向更加自动化集成的设备产品转变。
焊接质量明显改善
在焊接质量攀升方面,模组侧板和电池封口侧焊接表现的十分典型。
模组侧板焊接方面:动力电池模组常用铝合金型材(端板)、板材(侧板)作为模组外框结构件,焊接质量的好坏,直接决定了模组整体结构的刚性。
而通过采用不同的焊接头和工艺,可以获得不同的焊接效果,侧板激光焊接也因此发展出多种工艺方式。具体来看,第一代单光束焊接头,气孔率 10%——第二代双光束焊接头,气孔率 3%——第三代摆动光束焊接头,气孔率 1%。不难发现通过激光焊接设备推新及工艺调整,焊接质量在不断提升,从而极大地降低了焊接气孔率;
电池封口焊接:电芯封口激光焊接作为电池制造的一道重要工艺,极大地影响这电池成品率。电芯焊接速度越来越快的同时,还需要保证焊缝一致性等焊缝性能,由此衍生出第一代普通激光焊接——第二代技术复合激光焊接——第三代技术高频摆动焊接、环形激光焊接以及多层输出光纤激光器高速摆动焊接等激光焊接封口工艺。
大族激光以多层输出光纤激光器高速焊接为例介绍道,该技术通过多包层光纤,可同时输出圆点、环形激光,同时支持由一台激光器取代半导体、光纤激光器组成的复合激光器,可灵活调节功率,光束质量更稳定。
质检、控制更加专业
传统的焊接通过过程质量控制SPC保证焊接质量,通过统计学的方式控制焊接良率,配合传统的CCD焊后检测,虽然可检测出漏焊、断焊等问题,但对气孔、爆点的识别率不够高。但在现阶段,大族激光表示已可以实现在线异常检测,在焊接过程中智能识别缺陷。
资料显示,大族Dragon系列振镜可搭配焊接过程检测系统,通过等离子浓度探测,反射激光能量探测和焊缝温度探测来判定焊接过程稳定及判定焊缝质量,并在软包极耳焊接、BSB焊接等领域取得了良好的应用效果。
-
动力电池
+关注
关注
113文章
4553浏览量
78021 -
大族激光
+关注
关注
1文章
88浏览量
15278
原文标题:【佳的自动化·高工透视】大族激光如何做动力电池工艺革新
文章出处:【微信号:gh_a6b91417f850,微信公众号:高工锂电技术与应用】欢迎添加关注!文章转载请注明出处。
发布评论请先 登录
相关推荐
激光焊接机:新能源动力电池焊接的高效解决方案
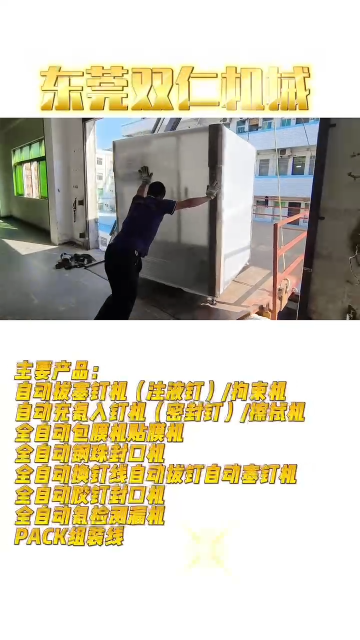
动力电池阻抗分析
激光焊接机:新能源动力电池焊接的高效利器
温度是如何对动力电池的性能造成影响?
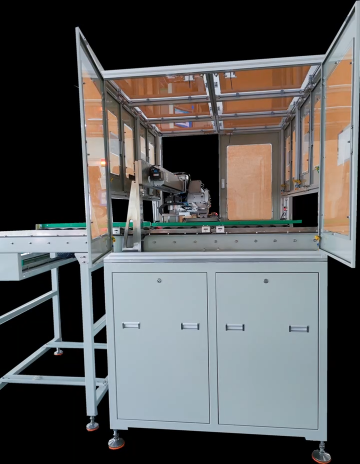
动力电池模组装配线:高效、精准的动力之源
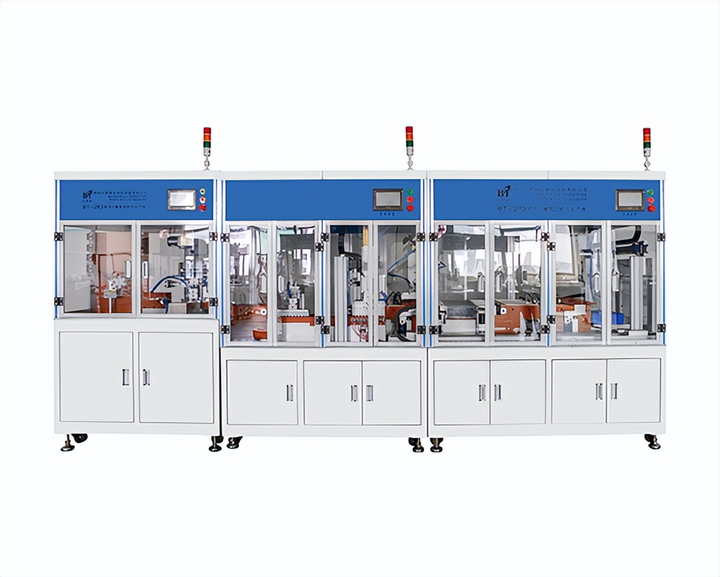
动力电池和储能电池的区别 储能电池与动力电池电芯有区别吗
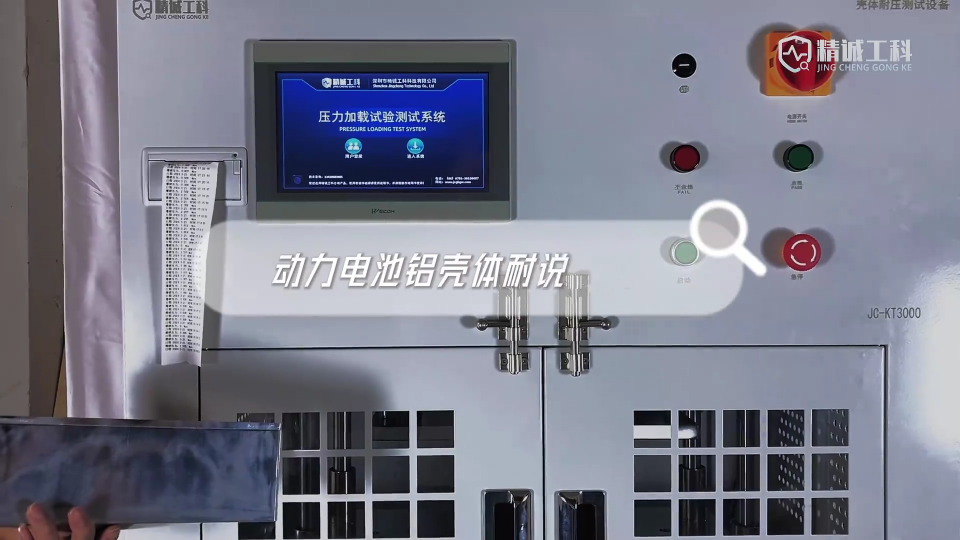
评论