在当今制造业飞速发展的时代,智能技术的蓬勃兴起正以前所未有的力量推动着传统制造行业的变革与升级,而智能 CNC 自动上下料方案的横空出世,宛如一颗闪耀的启明星,照亮了制造业通往高效、智能未来的康庄大道,引领着生产效率与质量迈向全新的高度。
项目背景
在传统的生产模式下,CNC 加工设备的上下料工作完全依赖于产线工人的手工操作。工人需要先将产品精心装配到治具上,接着费力地把治具连同定位台一同搬运到 CNC 加工设备内进行产品加工,待漫长的 4-6 小时加工过程结束后,又要再次手工将加工好的产品从 CNC 设备内取出并转移至成品摆放区18。
在这个过程中,产品种类繁多,尽管零点定位台和载具连接块对于所有产品而言是相同的,对接要求精度极高,需达到 ±1.5mm。这种传统的手工操作方式不仅劳动强度极大,而且效率低下,难以满足现代制造业对于生产速度和质量的严苛要求,人工操作的误差也难以精准控制,成为了制约生产效率和产品质量提升的瓶颈。
方案目标
为了突破这一瓶颈,智能 CNC 自动上下料方案应运而生,其核心是借助复合机器人 AMR 来实现生产工艺中 “产品搬运” 部分的自动化。具体而言,该方案致力于实现以下目标:
1.复合机器人 AMR 能够与生产中心计划紧密配合,实时灵活地调整生产状态,确保生产过程的连贯性和高效性。
2.具备自动确认 CNC 加工完成的能力,并能够迅速、准确地将成品自动转运到成品放置区,减少人工干预,提高生产效率。
3.可以精准判断上料区物料准备状态,自动将待加工产品及时、准确地转入空闲或者加工完成的 CNC 设备中,实现物料的高效流转和设备的充分利用。
核心优势
智能 CNC 自动上下料方案中的复合机器人 AMR 展现出了卓越的性能和显著的优势:
1.高精度操作:复合机器人 AMR 在抓取和放置过程中,误差严格控制在 <±1.5mm 以内,能够确保每一次操作都精准无误,有效保证了产品质量的稳定性和一致性,满足了高精度加工的需求。
2.智能避障与安全防护:在复杂多变的生产环境中,复合机器人 AMR 具备高度的智能性和适应性,会车时能够自动让行,遇到行人或障碍物时会迅速自动停止,极大地提高了生产过程的安全性,避免了潜在的安全事故168。
3.无缝对接与高效协同:复合机器人 AMR 能够与 CNC 设备实现无缝对接,不仅可以精准控制上下料时仓门的自动开关,而且综合放置成功率高达 > 99%,为高效生产提供了有力保障,确保了整个生产流程的顺畅无阻。
解决方案
1.总体布局:根据现场的实际布局情况,精心配置两辆 AMR 复合机器人负责上下料作业。通过人机交互信号以及 CNC 加工中心与 AMR 复合机器人之间的交互信号,实现精准的轨迹运行,确保机器人能够准确无误地完成各项操作任务。同时,为了保障机器人的持续作业能力,AGV 小车配备了专用自动充电桩,满载可持续作业 7.5 小时,并且可根据实际需求设置电量低于 20% 时提前充电,以满足不同生产场景的需求1。
2.视觉识别系统:富唯视觉识别软件 ForwardVision 在整个方案中发挥着至关重要的作用。它能够对 Mark 标进行高精度识别,并快速、准确地输出对应的位置信息,为复合机器人 AMR 的精准操作提供了关键的技术支持,确保机器人能够在复杂的环境中准确地抓取和放置产。品。
智能 CNC 自动上下料方案以其创新的技术、卓越的性能和完善的配套设施,成功解决了传统工艺存在的诸多难题,显著提高了生产效率和产品质量,为制造业的智能化转型提供了强有力的支持和借鉴,成为了推动制造业迈向高效、智能新时代的关键力量。
审核编辑 黄宇
-
CNC
+关注
关注
7文章
313浏览量
35218
发布评论请先 登录
相关推荐
智能柔性制造:AMR 复合机器人赋能 CNC 加工行业
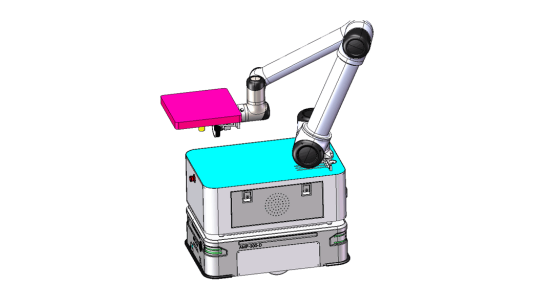
自动上下料机远程监控运维管理系统解决方案
复合机器人CNC柔性上下料
富唯智能复合机器人CNC自动上下料解决方案
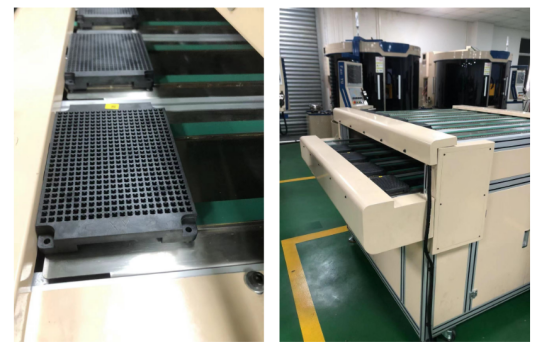
机器人上下料为汽车制造车间实现高效自动化
高效、安全、智能:机器人如何重塑行业内部物流上下料流程?
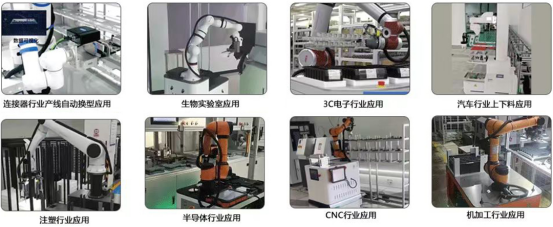
cnc加工中心,机床上下料正面临着自动化转型
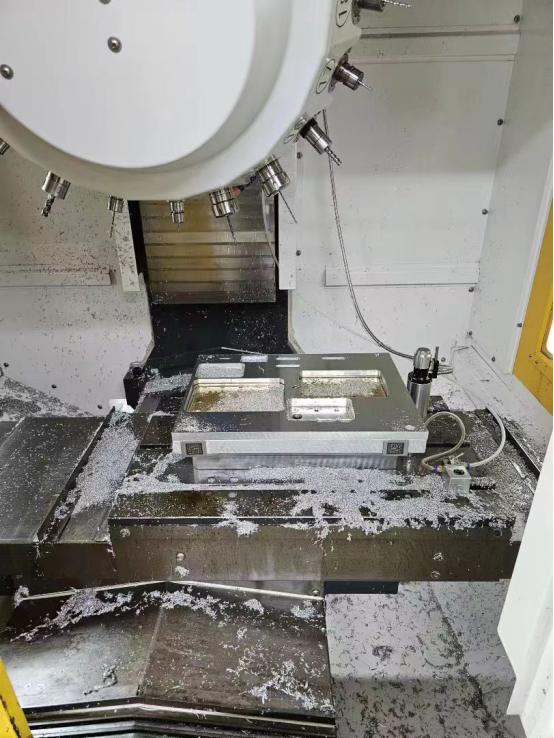
评论