本文介绍载带自动焊接技术所用到的材料与基本工艺流程等。
TAB技术是将芯片组装到金属化的柔性高分子聚合物载带(柔性电路板)上的集成电路封装技术。属于引线框架的一种互连工艺,通过引线图形或金属线连接芯片与外部框架或基板上的焊区。
载带按照层次结构分为单层带、双层带和三层带。实际应用中以双层带和三层带居多。载带宽度有多种标准,包括35mm、70mm、8mm、16mm、45mm、158mm等,不同宽度适用于不同规模的集成电路。
载带的基本材料
基带材料
定义:基带材料是带状绝缘薄膜,其上覆有铜箔刻蚀的引线框架,用于芯片封装焊接。
形状:类似于老式相机的胶卷或电影胶卷。
标准宽度:35mm、45mm、70mm。
厚度:50~100μm。
电路长度测量:以链轮距离为准,每个链轮节距约4.75mm,16个节距约76mm。
特点:耐高温、与铜箔黏结性好、热匹配性好、收缩率低、抗腐蚀性强、机械强度高、吸水率低。
常用材料:聚酰亚胺薄膜(最早广泛使用,价格略高)、聚酯类材料薄膜、苯丙环丁烯薄膜。
组成:冲孔、剪切线、芯片、引线框架、聚酰亚胺薄膜、内引线和外引线。
金属材料
定义:用于制作载带引线图形的材料。
用途:内引线和外引线用于制作载带引线图形。
特点:导电性能好、强度高、延展性强、表面平滑、与基带材料黏结牢固、易于刻蚀精细复杂图形、易于电镀焊接。
常用材料:铜箔(最常用,宽度有18μm、35μm、70μm、158μm,其中35μm应用最多)、铝箔。
凸块材料
定义:用于在芯片焊垫上制作凸块,再与铜箔内引线焊接的材料。
凸块金属材料:金、铜/金、金/锡、铅/锡。
焊垫金属:一般使用铝膜制作,需先沉积黏附层金属和阻挡层,防止外层凸块材料和铝材料互相扩散。
结构:可在芯片铝焊垫层将凸块制作在载带焊接的铜箔引线上,称为BumpTAB(凸块载带自动焊),凸块结构呈梯形或矩形。
载带自动焊接的工艺流程
载带自动焊接是一种高效的集成电路封装技术,其工艺流程主要包括以下几个步骤:
制作引线框架:
在聚酰亚胺薄膜的基带材料上,通过刻蚀等工艺制作引线框架。引线框架包括内引线和外引线,用于与芯片和基板进行电气连接。
芯片对位放置:
将芯片精确地对位放置在引线框架上,确保芯片的焊垫与引线框架的内引线对准。
热电极一次性焊接:
使用热电极或超声波焊接设备,一次性将所有的引线键合完成。这个过程实现了芯片与载带之间的电气连接。
标准化卷轴作业:
使用标准化的100m卷轴长带进行作业,实现自动化的多点一次性焊接。芯片的贴装和外引线的焊接电镀已经实现了自动化,支持大规模生产。
内引脚键合与点胶:
内引脚通过键合工具将内引线与芯片的凸块键合。使用点胶机将芯片点胶完成包封,再经过烤箱烘烤使胶硬化。
外引脚冲压成型与冲断:
当芯片完成了内引脚的键合和点胶之后,将外引脚冲压成型。使用键合工具将载带对位对齐后进行冲断,将封装后的芯片从载带上完整地取下来。
载带自动焊接的关键技术
载带自动焊接的关键技术包括芯片凸块的制作、载带的制作、内外引线的焊接等。
芯片凸块的制作:
凸块是连接芯片焊垫与载带内引线的关键结构。凸块的形状有蘑菇形和柱形(方形或圆形),设计原则需确保压焊区的金属全部被凸块金属所覆盖,避免腐蚀和损伤。
凸块制作形式主要分为在单层载带上制作凸块和在芯片焊垫上制作凸块两种。传统的电镀凸块工艺流程复杂,技术难度高,生产成本也高。凸块转移技术可以简化这一过程。
载带的制作:
载带是承载芯片和引线框架的柔性高分子聚合物。载带的制作需要确保材料耐高温、与铜箔的黏结性好、热匹配性好等特性。载带的宽度和厚度等参数需根据芯片规格和设计要求进行选择。
内外引线的焊接:
内外引线的焊接是实现芯片与基板电气连接的关键步骤。焊接过程需要确保焊接质量,防止虚焊、短路等问题。焊接方式包括热压焊接、超声波焊接等。
凸块转移技术:
凸块转移技术是一种简化凸块制作过程的创新技术。
该技术通过在玻璃基板上先制作完成凸块,然后将凸块转移到载带的内引线上。凸块转移技术可以大大提高凸块制作的一致性和生产效率。
载带的制作工艺
载带作为集成电路封装中的重要组成部分,其制作工艺直接关系到封装的质量和性能。以下是对载带制作工艺的详细分述:
载带材料的选择与设计
铜箔厚度:铜箔厚度的选择主要由图形的精细程度和引线的强度决定。一般来说,单层带选择厚度为50~70μm的铜箔以保持引线在制作和加工中的强度,以及引线焊点的引脚不共面。对于双层、三层或双金属载带,由于有聚酰亚胺的结构支撑,可以选择厚度为18~35μm或更薄的铜箔。
焊接区镀层:载带的焊接区要有良好的镀金层或镀锡层,以提高焊接质量和可靠性。镀层厚度一般为1μm左右。
引线宽度与间距:载带的引线宽度通常为50μm,相邻引线中心线的距离为100μm。这些参数的设计需根据芯片凸块的精确位置、尺寸和间距来确定。
载带类型选择:根据用户的要求及输入输出引脚的数量、产品的性能和成本来确定选择使用单层、双层、三层或双金属的载带。
单层带制作工艺
引线图形成型:利用设计好的制版进行光刻、曝光、显影及刻蚀处理,形成所需的引线图形。
电镀:在引线图形上电镀一层金属,以提高引线的导电性和耐腐蚀性。
双层带制作工艺
制版准备:提前为两面的制作做准备,一面刻引线图形,另一面刻聚酰亚胺。
刻蚀处理:分别进行光刻、曝光、显影及刻蚀处理,形成引线图形和聚酰亚胺层。
电镀与聚酰亚胺层结合:完成电镀引线图形后,与聚酰亚胺层结合,形成双层载带。
PA(Polyacrylate)涂层是聚丙烯酸酯类织物胶,具有防水、阻燃等多种功能,可用于双层带的某些特定部位以增加其性能。
三层带制作工艺
材料准备:由铜-黏结剂-聚酰亚胺三层材料结合而成。铜箔厚度为18~25μm,黏结剂厚度为20~25μm,聚酰亚胺膜厚为70μm。
模具制作:先冲压聚酰亚胺定位孔和框架孔,再涂黏结剂、涂敷铜箔,加热加压以黏附铜箔。
切割与冲压:切割冲压三层带,形成所需的形状和尺寸。
引线图形制作:利用光刻、曝光、显影及刻蚀处理,制作引线图形。
双金属带制作工艺
支撑框架制作:在聚酰亚胺薄膜上冲压出引线图形的支撑框架。
铜箔黏附:在两面黏附铜箔。
双面光刻:使用双面光刻的方法在两面制作出引线图形。
局部电镀:对两个图形聚酰亚胺框架之间的穿孔进行局部电镀,实现上下金属带之间的金属互连。
铜淀积与电镀加厚:在框架的两面先使用铜淀积工艺,再使用电镀加厚法形成双层铜箔。
光刻刻蚀:使用光刻法刻蚀出所需要的引线图形。
载带制作中的注意事项
引线宽度与间距的均匀性:确保引线宽度与间距的均匀性,以避免在焊接过程中产生短路或断路现象。
镀层的均匀性:镀层应均匀附着在引线图形上,以提高焊接质量和可靠性。
材料的选择与匹配:根据具体的应用场景和要求选择合适的材料,并确保各层材料之间的良好匹配。
制作工艺的精确性:在制作工艺过程中,应严格控制各个环节的工艺参数和条件,以确保载带的质量和性能。
-
芯片
+关注
关注
456文章
50929浏览量
424605 -
TAB
+关注
关注
0文章
16浏览量
11562 -
自动焊接
+关注
关注
0文章
28浏览量
6391
原文标题:一文了解载带自动焊接(TAB)技术
文章出处:【微信号:bdtdsj,微信公众号:中科院半导体所】欢迎添加关注!文章转载请注明出处。
发布评论请先 登录
相关推荐
SMT贴装基本工艺流程
倒装晶片的组装工艺流程
印制电路板制作工艺流程分享!
回流焊接技术的工艺流程详解
SMT贴片加工的工艺流程及作用
机器人焊接工艺流程
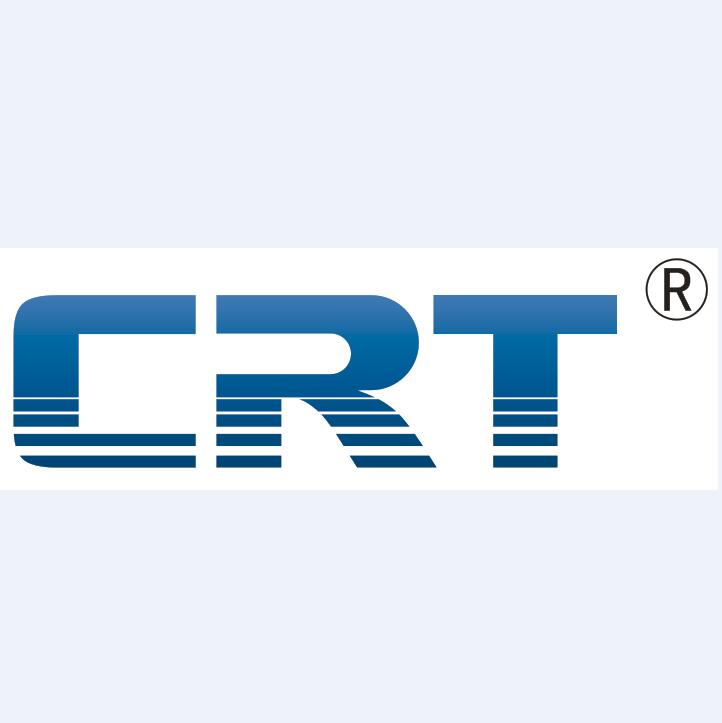
评论