比斯特的BT-2113B-18/21电池组半自动生产线的工作流程是一个高度集成且精细的过程。从电芯的初步放置开始,每一步都经过精心设计和严格测试。生产线上的自动化设备能够精确处理电芯,完成包括自动上料、自动面垫、电压内阻分选、自动分档、储存、自动入盒、正负极CCD检测和自动点焊等一系列操作。这不仅提高了生产效率,还确保了每个电池组的一致性和可靠性。本文将详细解析BT-2113B-18/21电池组半自动生产线的工作流程,展示从电芯上料到电池组性能测试的每一个环节。
一、自动上料
首先,电芯的上料是生产流程的基础。在BT-2113B-18/21电池组半自动生产线上,工人将装满电芯的盒子放在传送带上,传送带自动运作,机械手夹取电芯到下一部位,空盒子通过另一侧输送带运出。这一步提高了自动化程度,降低了工人的劳动强度。
二、自动面垫
接下来是自动面垫环节。该生产线适用于18650和21700电芯,自动贴圆形青稞纸以增强电芯正极的绝缘性能,提高电池组安全性。这一功能可关闭,用户可根据需求选择是否贴纸,提高了生产线的灵活性并降低了成本。
三、自动分选
随后,生产线进入电压和内阻的自动分选阶段。借助高精度传感器,设备自动测量每个电芯的电压和内阻,并据此将其分类到不同的档位。BT-2113B-18/21生产线设有五个分选通道,这一环节对确保电池组的一致性和稳定性至关重要。此外,设备还预留了扫码位置,以便未来增加扫码功能,从而实现对电芯信息的多方位追踪和管理,进一步提高生产效率和产品质量。
四、自动储存和入盒
电压和内阻分选完成后,电芯进入储存阶段,以便更好地进行装盒。BT-2113B-18/21生产线设有五个装盒口,自动取出同一档位的电芯并装入相应的胶盒中。装好电芯的胶盒随后被升降机自动传送到人工装支架位置,实现了电芯的自动化整理和传送,为后续的人工组装提供了便利。
五、CCD检测
在人工装支架之前,生产线还配备了自动CCD检测正负极的功能。通过高精度的CCD相机和图像处理算法,设备自动检测电芯的正负极位置,确保组装的准确性。合格的电芯继续送往下一步,不合格的电芯则通过升降台送出,人工摆正后可继续进入下一步工序。
六、人工装支架和模具
然后是人工组装支架阶段。工人在完成模具组装后,将镍片放入其中,接着进行自动点焊。点焊系统运用了先进的晶体管技术,实现双面自动点焊,确保焊接过程快速且精确。通过精确控制焊接时间和电流强度,设备保障了每个焊点的牢固与可靠。这一环节是电池组组装的关键步骤之一,直接影响电池组的质量与性能。
七、电池组综合性能测试
此外,生产线还提供了电池组性能测试机的选项。用户通过连接性能测试机,可对组装完毕的电池组进行多方位检测,涵盖电压、内阻、容量等指标。这一步骤有助于确保出厂电池组符合质量标准,提升客户满意度和信任度。
经过一系列精密高效的流程,BT-2113B-18/21电池组半自动生产线产出的是高质量、高性能的电池组产品。从电芯上料到电池组性能测试的每个环节都充分展现了自动化和智能化的优势,不仅提升了生产效率和产品质量,还减轻了工人的劳动强度,降低了企业的运营成本。随着新能源产业的持续发展,比斯特的BT-2113B-18/21电池组半自动生产线有望成为众多电池制造企业的理想设备。如有更多需求,请留下您的联系方式,深圳比斯特竭诚为您服务!
审核编辑 黄宇
-
电池组
+关注
关注
5文章
321浏览量
25713
发布评论请先 登录
相关推荐
电池组半自动生产线:高效、智能的生产解决方案
电池自动生产线:智能制造的典范
18650储能电池组PACK生产线:高效、智能、可靠
比斯特自动化:引领储能电池组生产线智能化变革的先锋
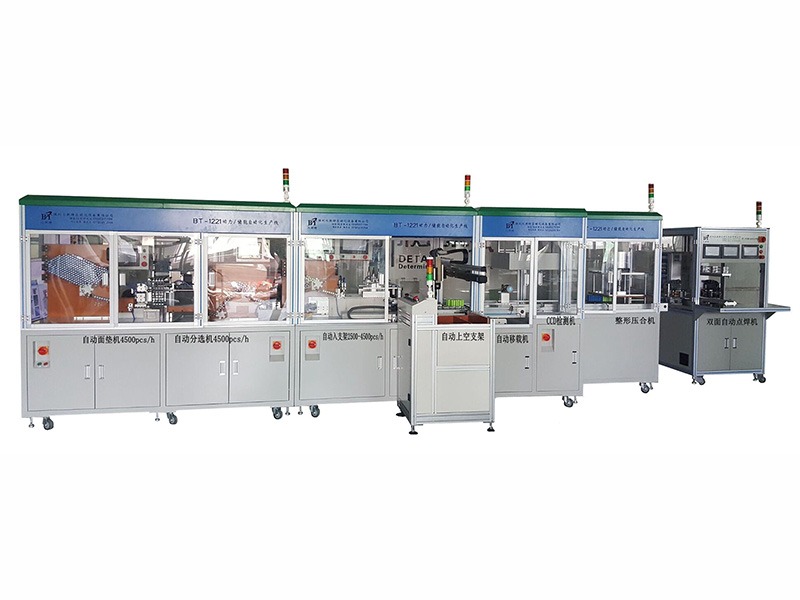
比斯特自动化:引领电池组PACK自动化生产线的创新与发展
智能引领未来:高效电池自动生产线助力绿色能源发展
电池自动生产线:智能化制造的未来趋势
比斯特自动化|电池组全自动生产线:推动电池制造行业的革新与效率提升
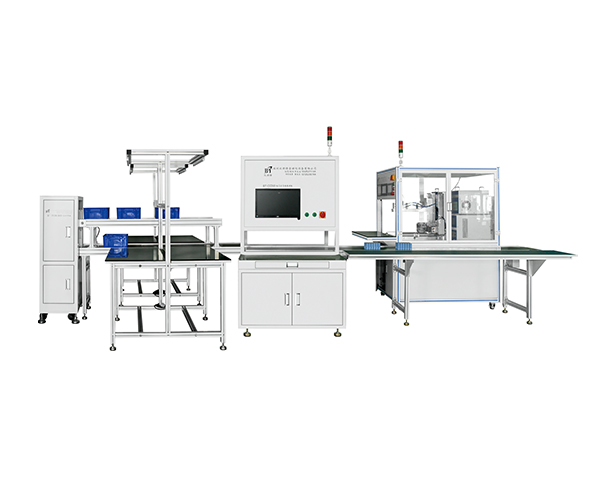
比斯特自动化|电池组PACK自动化生产线:引领能源存储行业的新篇章
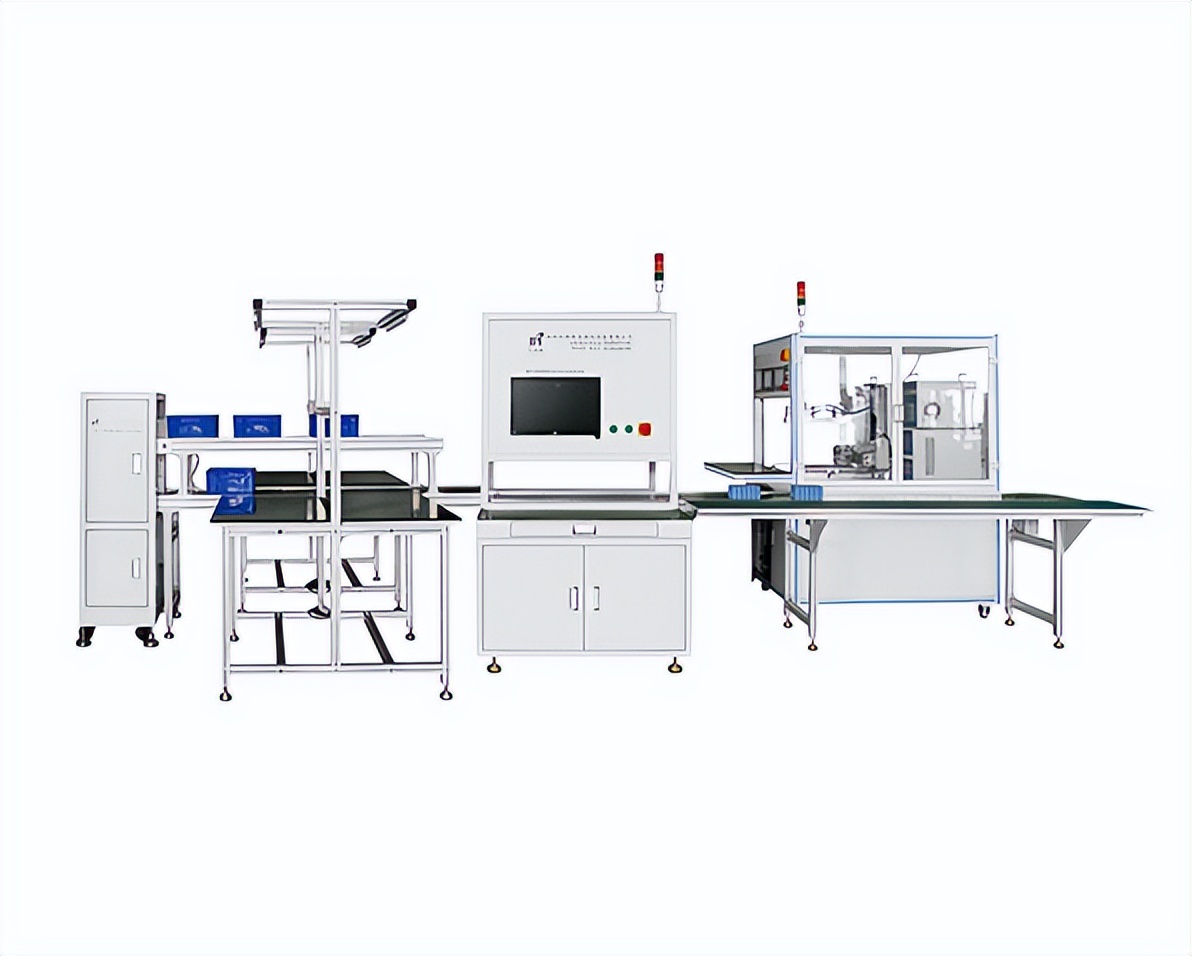
储能电池组PACK生产线:驱动绿色能源未来的核心
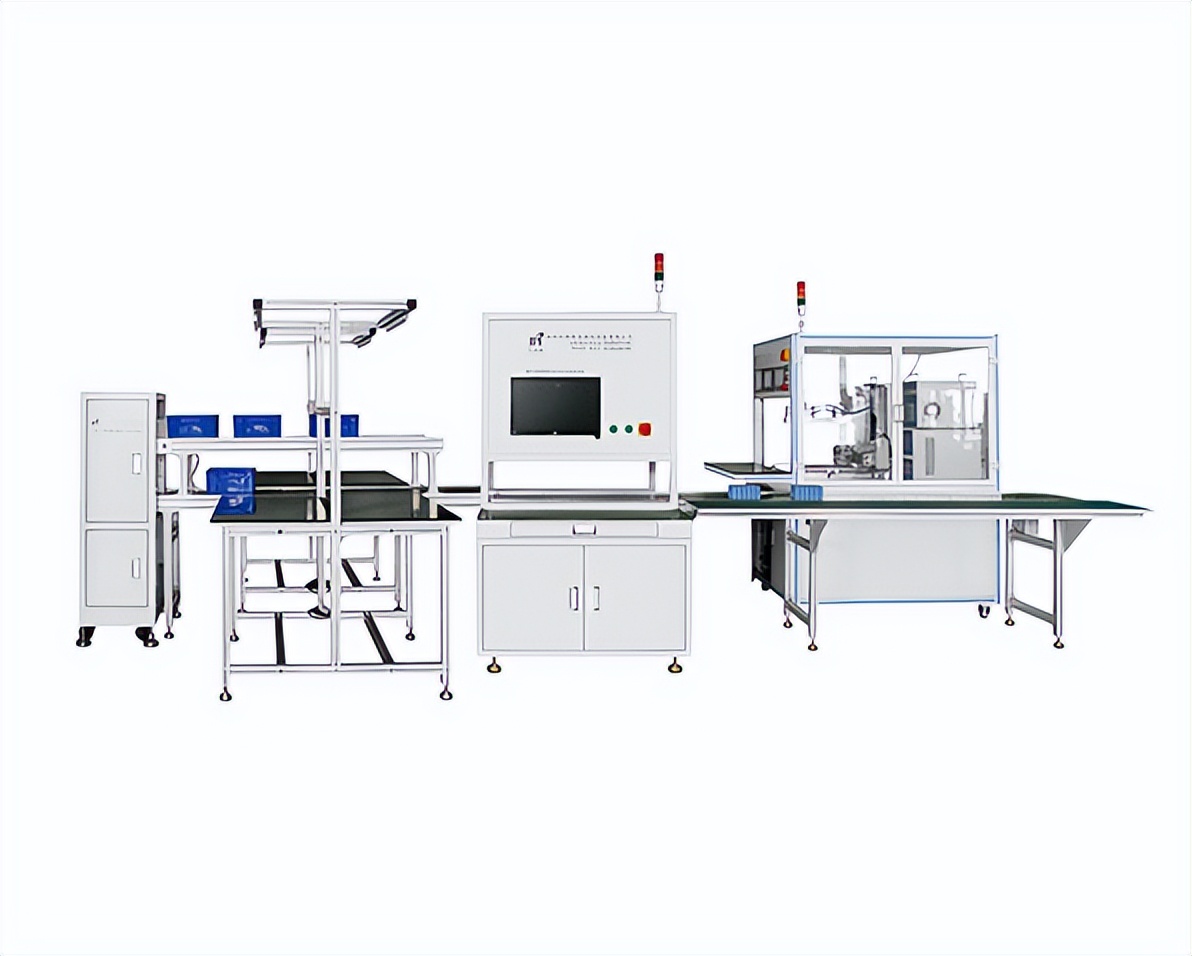
光伏电池片生产线:绿色能源的未来工厂|比斯特自动化
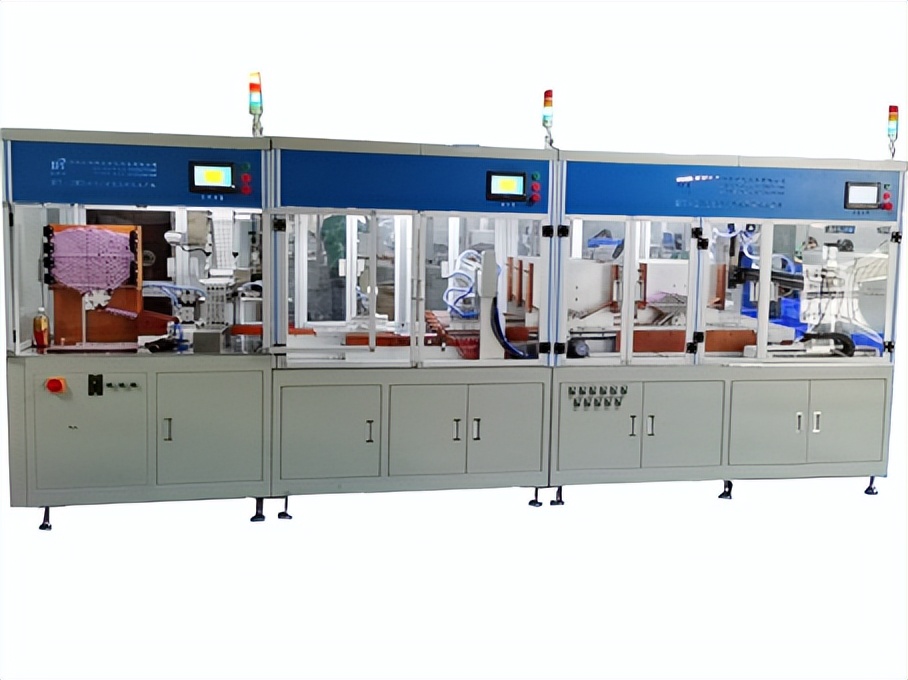
【200个电机驱动】如何快速搭建柔性自动生产线?
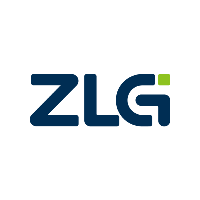
评论