半砖模块电源的散热设计
1、引言
DC-DC模块电源是利用先进的制造工艺构成一个整体的、结构紧凑的、体积小的高质量稳压电源。因模块电源使用简单,构成系统时具有扩容方便、维修性好等优点, 因此,被广泛应用于航空航天、通信电源、汽车电子、电子仪器、电力控制等领域。这些模块电源一般要求工作电源范围较宽(3 6 V ~7 5 V),输出功率大(全砖模块电源可达700W ),功率密度非常高,散热设计是一个大问题。例如,一个输出200W的半砖模块电源,其转换效率为89%,则有24.7w的电能转换成热能,若不加散热措施,半砖模块电源会因过热而损坏。因此,在大功率的模块电源设计中,合理的散热设计变得越来越重要。文中讨论了36V~75V直流输入、3.3V/60A输出半砖电源模块的散热设计,分析了发热器件的特性,给出了三种散热设计方案,并对三种方案的工艺、成本、散热性能等进行了对比。
2、半砖模块电源的主要发热器件
图1给出了该大功率二次DC-DC电源模块常用的有源箝位同步整流变换器电路,采用标准半砖模块结构。这种电路拓朴中发热最大器件是主开关管(Q1)、输出同步整流管(Q3 、Q4 )、平板变压器(T1 )和续流电感(L 1)。要解决这种电源的散热问题,就必须想方设法使这些元器件到外界的散热通道畅通,降低其热阻。
3、200W半砖模块电源在最坏情况下的功耗估算
电源模块应注明最高工作温度,其可靠性和工作寿命都与工作温度成反比。在任何工作状态下, 电源模块不仅不能超过温度极限,并且应留有足够余量。
当电源模块输入电压额定时,转换效率为89%。在实际设计时,将该效率作为最坏情况下的效率。如果电源模块满载工作(Po=200W ),产生热量的功耗Po为
200W半砖模块电源将有24.7w的电能转换成热能,如果工作的环境达到55℃ 以上,又不加任何散热措施,半砖模块电源会因过热而立即损坏。下面将介绍半砖模块电源的散热设计方案。
4、非铝基板散热方案
非铝基板半砖模块电源主要由一块双面贴多层PCB板和铝外壳组成,所有控制芯片和功率器件都放置在这块PCB上,其中平板变压器、续流电感直接嵌入PCB上,PCB的器件布局密度较高。功率器件布局在PCB的顶层,通过导热垫或导热胶与铝外壳进行热传导,最后在铝壳额外加散热器进行散热或直接通过对流方式在空气中进行散热。PCB板厚度约3mm(包括FR-4基板、铜箔、表面处理、绿油在内),层数约为12层,考虑到铜箔的输出较大(达60A),所以采用了4盎司铜箔厚度,满足通流能力的要求。以下给出非铝基板两种散热设计方案。
4.1功率MOS管到变压器和续流电感之间加铜柱进行散热
模块电源中的所有大功率MOS管采用小型POWERpaKSO-8封装(高约1mm),而平板变压器、续流电感的磁芯较高(高约3mm),它们可通过导热胶与顶层铝壳进行散热。因平板变压器或续流电感中走线电流非常大,所以平板变压器、续流电感、功率MOS管的工作温度非常高。这种模块电源的截面图如图2所示。
功率MOS管到平板变压器、续流电感之间通过一段铜皮连接,其通过的电流很大,功率MOS管也不宜太靠近平板变压器、续流电感,所以它们之间留出一段铜皮连接,其目的是为了分散两种发热器件之间产生的热量。而PCB铜皮一般都做了绿油保护处理(防止PCB铜皮在高温、潮湿环境下腐蚀),而绿油的热阻非常大,它与铜热传导系数比较如下:铜的热传导系数为400W/m℃;绿油的热导系数为0.5W/m℃。
功率MOS管、变压器及续流电感产生的热量分别通过功率MOS管外壳、磁芯、续流电感磁芯、PCB铜皮(有绿油覆盖)传递到填充的导热胶上,再由导热胶传递到铝壳上,最后铝壳通过对流或传导方式将热量散热出去。如图2所示,在功率MOS管和平板变压器、续流电感之间的这段铜皮去绿油,并加铜柱处理,可以大大减小变压器或续流电感、功率MOS管到外壳之间的热阻,将变压器、续流电感、功率MOS管产生热量通过铜柱快速传递到上面的铝壳,降低其热应力,提高整个模块电源的可靠性,如图3所示。
功率MOS管到变压器、续流电感之间加铜柱进行散热设计有以下特点:
(1)功率M0s管、平板变压器、续流电感及铜柱通过导热胶传递到铝壳;
(2)功率MOS管采用小型POWERpaK SO-8封装,可减小PCB布局的密度,不需要过多减化电路的设计;
(3)发热器件与铝壳之间需要填充导热胶,不需要填充导热垫,用料成本相对较高;
(4)铜柱的高度与变压器、续流电感的磁芯平齐,尺寸大小约为:3.8mm×3.8mm;
(5)铜柱在PCB板上的焊盘设计大小为(4~4.5)mm左右。
需要注意的是:整个电源模块产生共有24.7w功耗,通过导热胶与铝外壳进行热传导,所以导热胶的导热系数直接影响整个电源模块的散热性能,因此一定要选取低热阻的热胶。
4、2采用D2pak封装的MOS管反贴铝壳进行散热
模块电源中的所有大功率MOS管采用D2pak封装,将功率MOS管反向安装在PCB板,功率MOS管背贴散热铝壳。
功率MOS管和变压器、续流电感通过导热垫与铝壳直接连接,将其热量以传导方式传递到铝壳,最后铝壳通过对流或传导方式将热量散热出去。.与上述方案比较,这种散热设计中的功率MOS管、平板变压器、续流电感到铝壳的接触热阻更小。图4给出了采用大封装的MOS管贴铝壳进行散热设计图示。
采用D2pak封装的功率MOS管反贴铝壳进行散热设计有以下特点:
(1)功率MOS管和变压器、续流电感通过导热垫与铝壳直接连接,散热性能最佳;
(2)功率MOS管采用D pak封装,成本较低。但D2pak封装占大量PCB空间,大大增加了PCB布局的密度,需要简化外围电路设计,减小器件数量才能满足PCB的布局要求;
(3)变压器、续流电感磁芯的高度和功率MOS管的高度大体上要平齐,保证变压器、续流电感,功率MOS管到铝壳接触紧密,减小接触热阻;
(4)发热器件与铝壳之间需要添加导热垫,不需要填充导热胶,用料成本相对较低;
(5)安装D2pak封装功率MOS管之前,需要对其管脚做反向成型处理,增加相关工序和人力成本,如图5所示。
图5D2pak封装功率MOS管的管脚做反向成型处理:
(a)普通D2pak封装功率MOS管及其安装方式;
(b)反向成型后的D2pak封装功率MOS管及其安装方式。
5、铝基板散热方案
5、1铝基板方案有两层PCB结构
铝基板方案具有两层PCB结构如图6所示。
(1)顶层采用散热性能优良的单面铝基板。将发热严重的变压器、续流电感及功率MOS管直接焊在铝基板上,器件与铝基板直接接触,热阻更小。功率器件的电极通过连接铜柱引出到控制板上,以实现层间的电气互连。变压器、续流电感、功率MOS产生的热量通过PcB铜层一介质层一铝板,最后在铝板上通过对流或传导方式将热量传递出去。
(2)底层采用FR-4基板,用以放置控制、驱动及保护电路和辅助电源。采用SMT元器件,通过连接铜柱与铝基板功率部分进行信号传输。
采用两层PCB结构可以提高模块的功率密度,立体散热可提高散热效率;将发热严重的功率器件和驱动、控制电路分开布局,以避免相互之间的影响。
5.2设计需要注意的事项
铝基板的散热效果与铜层、铝板厚度、尺寸及绝缘介质的导热性有关。设计需要注意的是:
(1)铝基板的总板厚度为1.5ram(包括基板、铜箔、表面处理、绿油在内),利于铝壳均匀传热,
(2)铝基板采用4盎司的铜箔厚,满足功率器件的散热和PCB铜皮的通流能力韵要求;
(3)铝基板中的常用介质有HT、LTI、MP、CML四种材料,各介质材料的参数如表1所示(以美国贝格斯公司铝基板为例)。根据应用环境条件来选择采用哪种介质的铝基板,如果要求电源在65℃条件下正常工作,最好采用HT-04503(耐高温材料)介质铝基板。
5.3采用铝基板方案散热设计的特点
(1)功率M0s管和变压器、续流电感直接焊在铝基板上,器件与铝基板直接接触,与非铝基板两种方案比较,铝基板方案的热阻最小。
(2)大电流的功率走线也在铝基板上,PCB铜皮产生的热量能及时传递到铝壳,PCB铜皮的散热性能较好。
(3)功率MOS管采用D0pak大封装,成本较低。
(4) 非铝基板方案采用多层PCB板走线来设计变压器、续流电感,方案简单、生产效率高、成本低。而铝基板方案中的变压器、续流电感单独采用扁平的铜条绕制,制作工序较复杂,增加额外成本,并降低效率。
(5)变压器和续流电感的磁芯与铝基板之间需要加导热垫,降低其接触热阻。
(6)非铝基板方案使用一块多层PCB板,而铝基板方案中功率部分与控制部分严格分开,功率部分布局在单面铝基板上,SMT表贴器件布局在双面控制板上,不需要过多减化电路设计。
(7) 铝基板方案需要一块单面板(铝基板)和一块双面板(控制板),需要增加复杂的组装工序和相关人力成本,对于模块电源的安装和维修带来不便。对于大批量生产的模块电源,非铝基板方案的生产和组装效率远远高于铝基板方案。
6、总结
本文分析了36V~75V直流输入、3.3V/60A输出半砖电源模块的散热设计,给出了三种散热设计方案,并对三种方案的工艺、成本、散热性能等进行了对比。两种非铝板方案和铝基板方案比较,各有优缺点,具体应用需根据模块电源的成本及应用环境等各方面的因素来选择性价比最高的方案,今后这三种方案将同时发展,满足低电压、大电流DC-DC电源模块的需要。
-
散热
+关注
关注
3文章
513浏览量
31803 -
模块电源
+关注
关注
2文章
203浏览量
24347
原文标题:半砖模块电源的散热设计
文章出处:【微信号:Power-union,微信公众号:电源联盟】欢迎添加关注!文章转载请注明出处。
发布评论请先 登录
相关推荐
模块电源的散热应对措施
模块电源的优点
模块电源灌封简介
模块电源的噪声测试技巧介绍
BOSHIDA 模块电源的分类
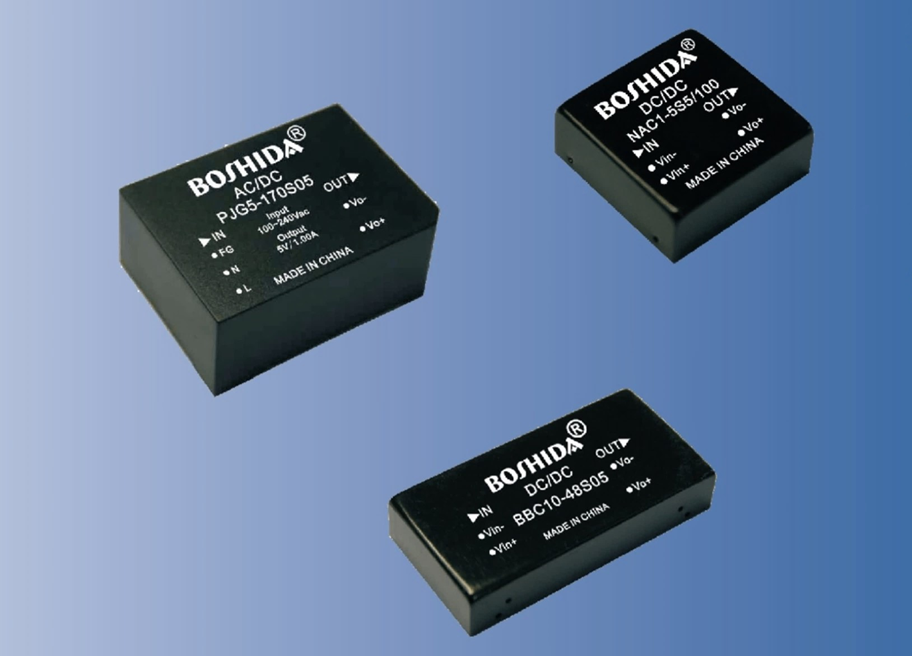
模块电源的工作原理及应用
砖形模块电源典型结构形式对散热性能的考虑
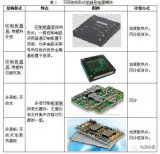
评论