常规PCB基板材料一一覆铜板,目前世界上绝大多数生产方式是间歇式。它主要是通过四道大工序依次完成的:树脂胶液的合成与配制(制胶);半成品的浸、干燥(上胶);层压成型(压制);剪切、包装。
玻纤布基覆铜板生产过程
(一)树脂肢液制造
树脂胶液制造在反应釜中完成。酣醒纸基覆铜板的树脂胶液制造一般要从原树脂的合成反应开始。当原树脂制作成为A阶段的树脂状后,再在反应釜中加入其他树脂、助剂、溶剂等进行配制,最后制成可直接上胶加工的树脂胶液(海外将它称为凡立水,resInvarnish)。它的原树脂的制造,一般为改性酣醒树脂的制造。在这个制造过程中,主要控制的性能检验项目有:树脂胶化时间(又称为凝胶化时间,geltime)、树脂挥发物含量(volatilecontent)、密度、黠度、固体量、游离酣含量等。再对树脂制造过程进行中间控制或一般工艺研究性测定,常见的项目有:pH值、蒙古度、胶化时间、折射率、水数、浑浊度、酣反应率、游离醒含量等。
环氧-玻纤布基覆铜板的树脂胶液制造,主要是树脂配制加工,即将由专业的树脂生产厂所提供的原树脂(环氧树脂)投入反应釜中,再加入固化剂、固化促进剂、其他助剂、溶剂等,进行混合、溶解而制成。
在树脂合成反应加工中,设备设计、选型中的反应釜的蒸发面积(或反应釜的径高比)、真空泵的抽气速率、冷凝器的冷凝面积、冷凝水温度、反应釜夹套的加热及冷却的方式、反应釜的搅拌器效果等,都对合成树脂的性能有着重要的影响。而对制造中各反应阶段温度、真空度、反应时间的正确、合理控制,也是十分重要的。对于树脂配制加工来说,要严制各个组分的投料量以及混合、溶解反应的时间、温度。
(二)半成品浸渍干燥加工
将制造好的树脂胶液注人到上胶机的胶槽中,以纤维纸、玻纤布、玻纤纸等为增强基材,进行浸渍树脂胶液,再经上胶机烘箱,在120~180°C的条件下加热干燥,使树脂处于半固化状态(B阶段树脂),且去除溶剂。这道工序被称为上胶,其制品称为上胶纸(或上胶布)。其中上胶布作为一种用于多层板制造的重要原材料,其商品名称又叫做半固化片(prepreg,简称为PP,或称预浸蒙古结片(preimpregnatedbondingsheet)。
纸基覆铜板的上胶纸加工,一般是在卧式上胶机中进行。而玻纤布基覆铜板的上胶布加工,一般是在立式上胶机中进行。上胶纸(上胶布)的质量控制指标一般有树脂含量(resincontent,RC%)、树脂流动度(resinflow,RF%)、挥发物含量(volatilecontent,VC%)、树脂凝胶化时间(geltime,GT),上胶纸质量控制指标除此以外还有单张质量、可溶性树脂含量(solubleresincontent)。有的生产厂家还对上胶布做熔融蒙古度曲线、双氧胶结晶试验、固化百分率、比例流动度等质量性能的研究、检测。
上胶加工中,半成品上胶纸(布)是利用上胶机连续通过浸渍(impregnation)和干燥(drying)两大加工过程完成。浸溃的过程,实质上是浸渍树脂胶液与增强基材的纤维结构中的空气相互交换的过程。在浸渍过程中,适宜的分子量、黠度、温度的树脂胶液通过上胶机的底涂辐(单方向浸入树脂)、挤压辑〈双方向浸入树脂、控制浸胶均匀度和树脂含量)的机械作用,将增强基材纤维中的空气排走,使树脂胶液占据其空间,并达到一定厚度的涂层。因此,保证存在于浸渍纤维空间的均匀性和树脂占有率,是半成品浸渍干燥加工中所达到的两大重要目的。
上胶加工是保证半固化片、覆铜板产品质量水平的重要关键的加工工序。达到一定均匀的含胶量,是由上胶机的形式、浸胶次数、上胶速度、挤胶辐间隙大小及其精度、其他附属装置的运行质量等所保证的。而上胶纸〈布〉的浸透性,即浸渍纤维材料的吸收树脂胶液的能力和均匀程度扩又取决于被吸收的树脂胶液的性质(分子量、黠度、密度、固体量等),同时,还与浸渍方式、环境温度、上胶速度、胶液循环情况等有关。
浸渍后的湿态上胶纸〈布),在上胶机烘箱中进行干燥加工要完成两个必要的过程:
一是溶剂与树脂中的低分子挥发物(包括溶剂)的蒸发过程;二是树脂分子继续进行一定程度的缩聚过程。前者是物理变化的过程,后者是化学变化的过程。干燥加工完成后,应达到上胶纸(布)内只残留很少的挥发物成分和具有与层压成型工艺相造宜的一定可溶性树脂流动程度。
干燥加工的过程,是载热体的传热和载湿体的传质的相互转化的过程,也是上胶纸(布)树脂结构从A阶段向B阶段转化的过程。随着加热干燥的深入,上胶纸(布)的树脂发生一定的缩聚反应,交联密度和分子量在不断增加。当干燥结束时,可溶解于一些有机溶剂的A、B阶段树脂的成分,一般要减少到75%~95%。严格把握树脂的固化转化程度是上胶加工中的十分重要的工艺控制工作。在上胶干燥的过程中,浸渍树脂在分子量分布结构上也发生了变化。日本有关专家利用凝胶渗透色谱(GPC)技术,对FR-4半固化片干燥加工前后的环氧-双氧胶树脂体系按分子直径不同划分为三个区域,进行测定和数据统计(图2-5、表2-11)。试验结果表明:经过加工的树脂,在低分子量(可看作是单体)部分和中分子量部分的树脂质量百分比均有所减少。其中,低分子量区域的下降幅度,要比中分子量区域大,而高分子量部分的树脂质量百分比增多。其增加幅度在6%~7%。整个树脂的分散系数(Mw/Mn)变化不大。
(三)层压成型加工
覆铜板的层压成型加工的整个阶段,主要包括对上胶布(上胶纸的剪切是在上胶加工时同时完成)的剪切(cutting)、叠层(layup)、层压(lamination)、卸板等几个主要工序。
用配制好的半成品上胶纸(布)的叠合坯料,覆以铜锚,上下放铜板作为模具,然后放置在压机的加热板之间,进行高温、高压的层压成型加工。层压成型加工是通过预温、热压、冷却三个不同的工艺控制阶段而完成的。目前,纸基覆铜板层压成型加工,由于生产技术水平的提高(对树脂制作和上胶加工的质量性能提高),在国内外大多数厂家可达到直接高温、高压的层压工艺法。而玻纤布基覆铜板在层压加工过程中,为提高板的性能一般要采用“二步法”。即在较低温、低压下先进行压制的预温阶段,然后再加高压、提温,完成板的固化成型的加工。
在热压机上的层压成型加工过程,是使上胶纸(布)的树脂首先在纤维增强基材间隙中,进行短时间的熔融再渗透(这种熔融渗透,曾在上胶加工时的干燥过程的初期已进行过)的熔化流动。然后,由树脂的B阶段支链状结构,经过一段时间的加热反应,过渡到C阶段的大分子网状结构,完成固化成型,制成满足各方面性能要求的成品的再熔融渗透和固化成型。因此,在层压成型加工中,所要达到的是上述再熔融渗透和固化成型的两个目的。
前者主要是在预温阶段完成的,此阶段是根据树脂的流动、浸润渗透、熔融中的蒙古度变化、黠稠状向黠弹状的过渡情况等,去确定、把握由预温阶段向高压高温层压阶段转化的“工艺窗口”。层压成型加工过程进入高压高温层压阶段,主要是要完成最后成型的加工,以完成板的完全固化成型。
电路板制作工艺流程
电路板制作流程一:打印电路板用转印纸打印绘制好的电路板,将滑的一面朝向自己,通常在一张纸上打印两张电路板,选择打印效果较好的制作线路板。
电路板制作流程二:裁剪覆铜板,用感光板制作电路板全程图解。覆铜板是两面都覆有铜膜的线路板,将覆铜板裁成电路板的大小,不要过大以节约材料。
电路板制作流程三:预处理覆铜板用细砂纸打磨覆铜板表面的氧化层,从而保证转印电路板时热转印纸上的碳粉能牢固的印在覆铜板上。板面光亮则表明打磨好了。
电路板制作流程四:转印电路板将打印好的电路板裁剪成合适大小,把印有电路板的一面贴在覆铜板上,对齐好后把覆铜板放入热转印机,放入时一定要保证转印纸没有错位。一般来说经过2-3次转印,电路板就能很牢固的转印在覆铜板上。热转印机事先就已经预热,温度设定在160-200摄氏度,由于温度很高,操作时注意安全!
电路板制作流程五:腐蚀电路板,回流焊机先检查一下电路板是否转印完整,若有少数没有转印好的地方可以用黑色油性笔修补。然后就可以腐蚀了,等线路板上暴露的铜膜完全被腐蚀掉时,将线路板从腐蚀液中取出清洗干净,这样一块线路板就腐蚀好了。腐蚀液的成分为浓盐酸、浓双氧水和水,比例为1:2:3。在配制腐蚀液时,先放水,再加浓盐酸、浓双氧水,若操作时浓盐酸、浓双氧水或腐蚀液不小心溅到皮肤或衣物上要及时用清水清洗,由于要使用强腐蚀性溶液,操作时一定注意安全!
电路板制作流程六:电路板钻孔电路板上是要插入电子元件的,所以就要对线路板钻孔了。依据电子元件管脚的粗细选择不同的钻针,在使用钻机钻孔时,线路板一定要按稳,钻机速度不能开的过慢,操作钻机还是比较简单的,只要细心就能完成得很好。请仔细看操作人员操作。
电路板制作流程七:电路板预处理钻孔完后,用细砂纸把覆在线路板上的墨粉打磨掉,用清水把线路板清洗干净。水干后,用松香水涂在有线路的一面,只需薄薄的一层,不光防止线路被氧化,同时松香也是很好的助焊剂,一般来说,线路板表面松香水会在24小时内凝固,为加快松香凝固,我们用热风机加热线路板,只需2-3分钟松香就能凝固。热风机温度高达300度,使用时不能把出风口朝向易燃物、人和小动物,安全始终摆在第一!
电路板制作流程八:焊接电子元件焊接完板上的电子元件,通电功能实现,这样就完成了整个电路板制作流程了。
-
pcb
+关注
关注
4335文章
23237浏览量
402098 -
覆铜板
+关注
关注
9文章
267浏览量
26514
发布评论请先 登录
相关推荐
贴片电阻生产工艺流程解析
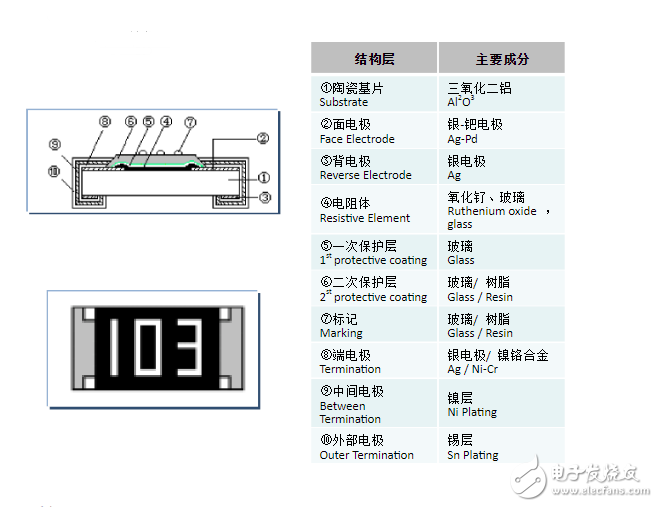
PCB电路板的分类特点及生产工艺流程解析
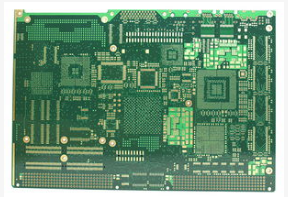
评论