SiC作为宽禁带半导体材料,与Si相比具有击穿场强高、导热系数高、载流能力大、开关速度快、可高温工作等优点,适用于高压、高温、高频等领域的应用。同时,SiC器件能够显著提升电力电子装置的转化效率,有利于节能和环保,装置的高功率密度和轻量化。国家“十二五”和“十三五”都投入了大量的资金来进行SiC材料和器件的技术攻关。SiC模块通常包括全SiC模块和SiC混合模块两种。全SiC模块是采用SiC MOSFET和SiCSBD按照一定的电路结构进行多芯片并联的模块。SiC混合模块是采用SiC SBD替代Si FRD,与IGBT芯片按照一定的电路结构进行多芯片并联的模块。
全SiC MOSFET模块方面,CREE研发了1700V以下的全SiC模块,ROHM研发了1200V以下的全SiC模块,并得到了一定范围的应用。我国对SiC MOSFET的研究尚处于起步阶段,高压大电流SiC MOSFET器件在栅氧可靠性、成品率、测试驱动、性能检测控制等方面还处于机理研究和试验阶段,大规模商业化的应用仍需一定的时间。基于以上状况,高压大功率SiC混合模块在牵引领域的应用是一个折衷且稳妥的方案,它既能体现SiC材料的优势,降低系统损耗,又能在成本方面被接受。富士、日立、三菱及一些科研结构都进行了SiC混合模块的研究,虽然国内也进行了一些高压SiC混合模块的研究,但SiC混合模块在牵引领域的应用研究还没有相关报道。本文基于自主研发的3300V/32ASiC SBD,研制了一种机车牵引用3300V500A SiC混合模块,对性能参数进行了测试与分析,并与3300V500A IGBT模块的性能参数进行对比。采用PLECS软件进行了牵引逆变器PWM工况下SiC混合模块的结温仿真。
模块设计与封装
为了减少变流器系统其他部件的设计变更,本文设计研制的3300V500A SiC混合模块采用130mm×160mm×38mm标准Si IGBT模块的封装接口尺寸,电路结构为双开关电路,每个桥臂的额定电流能力为500A,采用两块衬板并联的方式。由于单颗SiC SBD芯片只有几十安培,模块需要使用多颗芯片并联,以达到所需的电流能力。本设计中采用的IGBT芯片电压电流等级为3300V/62.5A,SiC SBD芯片的电压电流等级为3300V/32.5A,模块共包含16颗Si IGBT和32颗SiC SBD芯片。芯片间采用引线键合的互连方式实现大电流,SiC SBD芯片与IGBT芯片反并联。为了保证模块中使用的芯片性能参数一致性,将SBD芯片的探针测试数据进行梳理,挑选VF与ICES一致性较好的芯片。IGBT芯片目前已经在机车领域得到了广泛应用,性能参数一致性较好,无需进行筛选处理。
寄生电感、寄生电阻、结壳热阻等是模块设计中需要考虑的关键因素[10]。混合SiC模块功率端子采用对称结构来形成互感效应降低模块内部电感;衬板电路及芯片布局采用对称设计使芯片间的寄生电阻一致、电感差异最小化;SiC SBD芯片间进行互连减小键合引线的距离,增大引线的通流能力,达到芯片间的均流。以上因素在IGBT模块中已经得到了充分的优化和验证,本文不做过多的阐述。衬板单元实物如图1所示。
图1 3300V500A SiC混合模块用衬板单元
Fig.1 3300V500Asubstrate unit of SiC hybrid module
SiC混合模块与IGBT模块相比,虽然工艺过程一致,但工艺参数存在一定的差异,如焊接和引线键合参数。SiC SBD芯片尺寸为6.1×6.1mm,在真空回流焊接过程中若焊料多容易产生芯片漂移,焊料少则会使焊层产生空洞,影响芯片的散热,进而影响模块可靠性。SiC SBD芯片与Si FRD芯片厚度不同,表面金属和工艺也略有差异,需要调整引线键合参数,并进行推力测试。通过对混合SiC模块封装工艺进行不断优化,工艺过程检测结果全部达到机车用IGBT模块的参数要求。3300V500A SiC混合模块如图2所示。
图2 3300V500A SiC混合模块
Fig.2 3300V500ASiC hybrid module
特性测试
3.1二极管静态特性
对封装完成的模块进行静态性能测试对比,Si FRD和SiC SBD正向特性曲线见图3所示。IGBT模块中FRD在300A前为负温度系数,混合模块中SBD在25A前为负温度系数。两种二极管的正向电压VF随温度升高而升高,SiC SBD具有更好的正温度系数,利于芯片的并联及器件的并联应用。二极管正向直流电流500A条件下,25℃、125℃、150℃时的二极管正向电压VF分别为2.0V,3.3V,3.8V,该值包括电流回路寄生电阻引入的压降约0.3V。25℃时SiC SBD低于Si FRD的正向电压,高温时则大于Si FRD的正向电压。因此从芯片正向电压来讲,高温工作条件下,仅SiC SBD导通损耗与Si FRD相比没有优势。
图3二极管正向特性曲线
Fig.3 Diodetypical forward characteristics
3.2模块动态特性
SiC混合模块动态性能采用双脉冲测试,电路如图4所示,测试时模块相互陪测,上管为陪测模块,下管为待测模块,测试完成后进行互换。
图4.动态测试原理图
Fig.4 Dynamictest schematic diagram
3300V500A混合SiC模块的动态测试波形见图5所示。在动态测试的评估中,第一个脉冲,被测模块IGBT开通,其电流受负载电感的影响以线性方式上升。当第一个脉冲关断后,被测模块中的SiC SBD芯片进行续流。在第二个脉冲开通时,被测IGBT模块中的SBD芯片处于反向恢复过程。在SBD芯片反向恢复前,电流流过SBD芯片,此时经过负载电感的电流与流经SBD芯片的电流叠加后,全部施加在被测模块的IGBT芯片上。当SBD芯片反向恢复结束时,被测模块的电流再次以线性方式上升。当第二个脉冲关断时,被测IGBT能够正常关断。
图5 SiC混合模块动态测试波形
Fig.5 Dynamictest waveforms of SiC Hybrid module
SiC混合模块集成了IGBT芯片与SiC SBD芯片,工作过程中两者交替开通与关断。宽禁带SiC材料与Si材料相比本身具有一定的优势,SiC混合模块的反向恢复时间较短,将SiC混合模块的反向恢复与IGBT模块反向恢复波形进行对比,如图6所示。SiC SBD芯片反向恢复过程中,几乎不存在恢复电流Ir,拖尾电流短,二极管电压Vr略有波动,但反向恢复损耗非常小。因此,对于3300V500A SiC混合模块,反向恢复能量几乎可以忽略。
图6. SiC混合模块与IGBT模块反向恢复波形对比
Fig.6 Reverserecovery waveforms of SiC hybrid module compare with IGBT module
SiC SBD芯片在反向恢复速度较快,对模块的开通也有一定的影响,将SiC混合模块和IGBT模块的开通波形放在一起进行对比分析,如图7所示。
图7. SiC混合模块与Si IGBT模块开通波形对比
Fig.7Switch waveforms of SiC hybrid module compare with IGBT module
从图7中可以看出,在IGBT的开通过程中,由于FRD反向恢复电流的存在,普通模块会在IGBT上叠加额外的电流。过冲电流会对IGBT器件形成冲击,而SiC混合模块反向恢复电流远小于Si IGBT模块,则不会存在此过冲电流。开通过冲电流的减小,会大大减小器件的开通能量。SiC混合模块由于反向恢复电流小,施加在IGBT芯片上的过电压显著降低,利于模块的可靠性提升。
随着IGBT器件驱动栅极电阻减小,开通速度加快,其开通能量大幅减小。普通IGBT模块会受限于FRD的安全工作区,必需限制其开通速度(开通电流变化率di/dt),SiC混合模块则无安全工作区的限制。SiC混合模块可以加快IGBT的开通速度,从而大大减小应用时的开通能量。
相同测试条件下,将IGBT模块和SiC混合模块的开关损耗数据进行对比,如表1所示。IGBT模块一次开关所产生的损耗为3280mJ,SiC混合模块一次开关产生的损耗为2090mJ,损耗约降低32.6%。
表1 IGBT模块与SiC混合模块损耗数据对比
Tab.1Energy loss comparison of IGBT module and SiC hybrid module
热阻特性
连续正向直流电流IF是模块的重要参数指标,本设计采用的是常规IGBT模块的结构,因此仅需验证二极管的连续正向直流电流。连续正向直流电流IF与模块的最高工作结温、壳温、模块热阻、二极管正向电压(IF及Tj条件下)等参数相关,具体见公式(1)。
按照JEDEC 51-1规定,通过测量SiC混合模块的温度校准系数,加热稳定后的功率,使用T3ster热瞬态测试仪得到瞬态响应曲线,并将结果转化为积分结构函数,得到了混合SiC模块的瞬态热阻抗曲线[11],如图8所示。
图8. SiC混合模块瞬态热阻抗曲线
Fig.8Thermal resistance curves of hybrid SiC module
从8图中可以获取IGBT芯片的结壳热阻为23.5K/kW,SiC-SBD芯片的结壳热阻为36 K/kW。从芯片面积角度分析,单颗Si FRD芯片的面积为13.5mm×13.5mm,IGBT模块的二极管结壳热阻为48 K/kW;4颗SiC SBD芯片的面积总和为12.2mm×12.2mm,在芯片面积减小的情况下,热阻反而降低了25%,充分体现了SiC材料高导热系数的优越性,且增加了二极管的电流裕量。
对于本文研制的3300V500ASiC混合模块,按照Tj=150°C,TC=80°C,=3.8V,根据公式(1)计算出连续正向直流电流IF约为511A,满足技术要求。另外,SiC SBD芯片可以在大于150℃的工况下正常工作,Si FRD则无法与SiC SBD相比,在额定电流能力方面,SiC混合模块具有更大的裕量,因此SiC混合模块更加可靠。
应用工况仿真
5.1仿真模型
为了计算模块在实际工作过程中的最高结温,在PLECS仿真平台上搭建电路仿真,应用工况选用三相两电平逆变器驱动电机负载的电路,仿真电路如图9所示。
图9应用电路仿真模型
Fig.9Application circuit simulation modle
直流电源通过6个3300V500A SiC混合模块或IGBT模块构成逆变器进行逆变输出,电阻、电感、反电动势模拟三相电机负载,模块内部两单元分别作为上下桥臂,采用开环PWM控制方法,热、电仿真参数如表2。
表2仿真条件参数
Tab.2Simulation condition parameters
5.2仿真结果
按照三种工况进行仿真,设定输出电流有效值为250A,最大输出电流350A,最大制动电流360A,每种输出电流下运行30s。根据损耗计算方法[12],计算得到了三种工况下的IGBT模块和混合SiC模块的损耗。
在输出电流有效值为250A工况下,运行30s已达到热平衡,IGBT模块和和SiC混合模块的最高结温见图10所示。
图10 IGBT和二极管芯片最高结温变化
Fig.10 Maximumjunction temperature variation of IGBT and Diode Dies
从图10中可以看出,模块温度先急剧上升,然后温度逐渐下降,原因是电机启动过程损耗较大。SiC混合模块中IGBT和SiC SBD芯片的最高结温都要低于IGBT模块,尤其芯片采用SiC SBD显著降低了二极管的最高结温。模块整体温度降低,二极管电流能力裕量更大,模块可靠性更高。将3种工况下的芯片温度进行汇总,见表3。
表3最高结温仿真结果
Tab.3Simulation results of maximum junction temperature
从表3中可以看出,三种工作工况下SiC混合模块的最高结温都小于IGBT模块,工况越恶劣越能体现SiC混合模块的优势,SiCSBD芯片的温升较小。制动工况下SiC混合模块IGBT芯片温度最高131.7℃,SiC SBD芯片的温度仅为84.9℃,模块能够正常工作。通常机车牵引用IGBT模块的环境温度低于80℃,因此在三种仿真工况下, SiC混合模块的安全工作温度都有一定的裕量,满足系统的要求。
结语
本文设计研制了3300V500A SiC混合模块,使用SiC SBD芯片代替了Si FRD芯片,进行了相关工艺验证,满足机车用模块标准。在模块性能方面,SiC SBD芯片的静态参数具有更好的正温度系数,利于模块的并联使用。SiC混合模块二极管的热阻较IGBT模块显著降低,模块的额定电流能力裕量更大,能够提升模块的可靠性。在模块动态性能方面,SiC 混合模块的反向恢复能量几乎可以忽略,减小了开关过程中对IGBT芯片的电压、电流过冲,IGBT的安全工作区更大。通过PWM工况进行了模块温度仿真,在额定条件下和极端制动条件下,混合SiC模块芯片温度都低于IGBT模块,满足模块正常工作的温度要求。
通过高压大功率3300V500A混合SiC模块的研制,实现了机车牵引用IGBT芯片、SiC SBD芯片及模块的国产化,性能参数满足机车牵引逆变器对模块的参数要求,推动了国内SiC材料在牵引系统中的应用。
-
IGBT
+关注
关注
1266文章
3786浏览量
248828 -
SiC
+关注
关注
29文章
2798浏览量
62592
原文标题:SiC SBD芯片在牵引用3300V500A SiC混合模块中的应用
文章出处:【微信号:iawbs2016,微信公众号:宽禁带半导体技术创新联盟】欢迎添加关注!文章转载请注明出处。
发布评论请先 登录
相关推荐
在电动汽车牵引变频器应用中,磁传感器TLE5309D能否取代旋转变压器?
在功率二极管中损耗最小的SiC-SBD
GaN和SiC区别
降低碳化硅牵引逆变器的功率损耗和散热
使用UCC5870-Q1和UCC5871-Q1增加HEV/EV牵引逆变器的效率
【转帖】华润微碳化硅/SiC SBD的优势及其在Boost PFC中的应用
SiC器件中SiC材料的物性和特征,功率器件的特征,SiC MOSFET特征概述
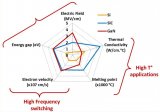
如何通过实时可变栅极驱动强度更大限度地提高SiC牵引逆变器的效率
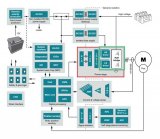
SiC器件在电源中的应用
在汽车SiC牵引逆变器中使用Sitara MCU AM263x
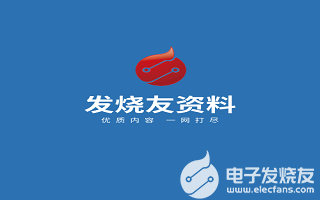
评论