2018-2020年,软包动力电池新增产能超过80GWh,软包电池特有设备价值量约1.68亿/Gwh,即至2020年将有超134亿的新增软包特有生产设备需求。
高能量密度核心优势加持下,软包电池在动力领域的市场渗透率迅速提升,电池形态的演变也给锂电设备企业带来新一轮的发展机遇。
高工产研锂电研究所(GGII)数据显示,根据2018年在建的产能及规划情况来看,软包电池(含方形软包)产能占比上升至29%,超越圆柱,圆柱在建及新增产能比例大幅下降。
目前,主流软包电池企业也相继公布了其扩产计划,根据公开信息整理,2020年国内软包电池产能将超过100GWh。详细如下图:
而由此也将产生软包电池特有生产设备的新一轮爆发需求。据了解,软包电池与方形电池的工艺在生产前段从搅拌到极片模切环节基本一致,工艺差异主要集中在中后段。
依据宁德时代招股说明书披露的数据显示,目前国内电池厂商平均1GWh产能对应设备投资约2.8亿元。其中,前中后三阶段对应的锂电设备价值量占比分别约40%、30%、30%。
由此可推算出,软包电池特有设备价值量约1.68亿/Gwh。则2018-2020年,软包动力电池新增特有设备需求约80*1.68=134.4,即至2020年将有超134亿的新增软包特有生产设备需求。
高端及一体化设备需求突显
据了解,软包和方形电池制造的核心差异在于两方面:一是,软包动力电池电芯普遍采用叠片工艺,而方形电池通常采用卷绕工艺;二是,铝塑膜作为软包电池包装材料,其中后段的注液、封装均与方形电池存在较大差异。
然而当前,叠片工艺在效率、一体自动化程度等方面仍然存在短板。其中,在效率方面,目前国内行业叠片设备以双工位居多,效率普遍在0.5-0.8秒/片的效率,与进口叠片机0.17秒/片的效率还存在较大差距。
高工锂电了解到,目前行业的研发走势是:1、应用新叠片工艺,如:正负极吸附式高速叠片;2、走切叠一体机、制带叠片一体化方案;3、研发四工位、八工位自动叠片机。
与此同时,在软包电池模切和叠片工艺过程中,容易产生毛刺和粉尘,这将为动力电池埋下安全隐患。
业内人士普遍认为,解决毛刺、粉尘最佳的解决方案是采用(激光)模切叠片一体机。因为模切叠片一体机在极片冲切完之后可直接进入叠片平台,避免极片和料盒的碰撞和摩擦,彻底解决极片不良的潜在风险。
值得一提的是,高工锂电近期了解到,由于目前叠片工艺在效率、一体自动化程度等方面仍在存在短板,因此软包动力电池企业也萌生了暂时用卷绕工艺替代叠片工艺的想法。(相关链接:《叠片工艺的“退”与“进”》)
随着软包电池在动力市场的应用提速,卷绕工艺在软包动力电池领域的解决方案应用成熟,卷绕工艺未来两年内在动力软包市场的应用或将增多。
装备巨头入局叠片领域
虽然短期内,叠片工艺存在被替代风险,但从长期发展来看,软包叠片工艺的电池在安全性能、能量密度等方面明显优于卷绕工艺,因此叠片工艺成为未来软包电池的主流制造趋势毋庸置疑。
目前,国内从事叠片设备的装备企业主要有三股势力:一是,行业积淀较深的传统品牌,以格林晟、佳的自动化、吉阳智能、超业精密、超源精密、中天和等为代表。这也是目前市场的主流势力。
二是,中小型潜力企业,包括东莞恒捷、鸿宝、中锂、华创等,其各自均发展以中后端产线一体化为主。
三是,横向扩张的大型卷绕装备企业,如先导智能、赢合科技、兴诚捷等。通过布局卷绕、叠片双管齐下,为市场做两手准备。
值得注意的是,随着大型装备巨头的涉入,当前行业集中度高的叠片设备市场格局或将发生巨变。
一方面,大型装备巨头具备资金、技术、品牌等显性优势,通过提升叠片一体化效率来改善叠片效率慢的弱点,并利用原先产线环节设备进行延伸,往产线一体化发展,可以迅速切入市场。
另一方面,具备核心竞争力、深度绑定战略大客户的设备企业正在占领高地,涵盖动力电池主要制造环节的设备巨头将逐渐成型。随着锂电设备行业集中度正逐渐提升,设备行业的整合也将加速进行。
-
动力电池
+关注
关注
113文章
4536浏览量
77674 -
软包电池
+关注
关注
1文章
175浏览量
7986
原文标题:【鑫东达壳盖•深度】掘金动力电池软包设备130亿“新蓝海”
文章出处:【微信号:weixin-gg-lb,微信公众号:高工锂电】欢迎添加关注!文章转载请注明出处。
发布评论请先 登录
相关推荐
华为入选中国云网安一体化能力领导者
军工领域新宠儿:一体化摄像机机芯模组的应用与突破
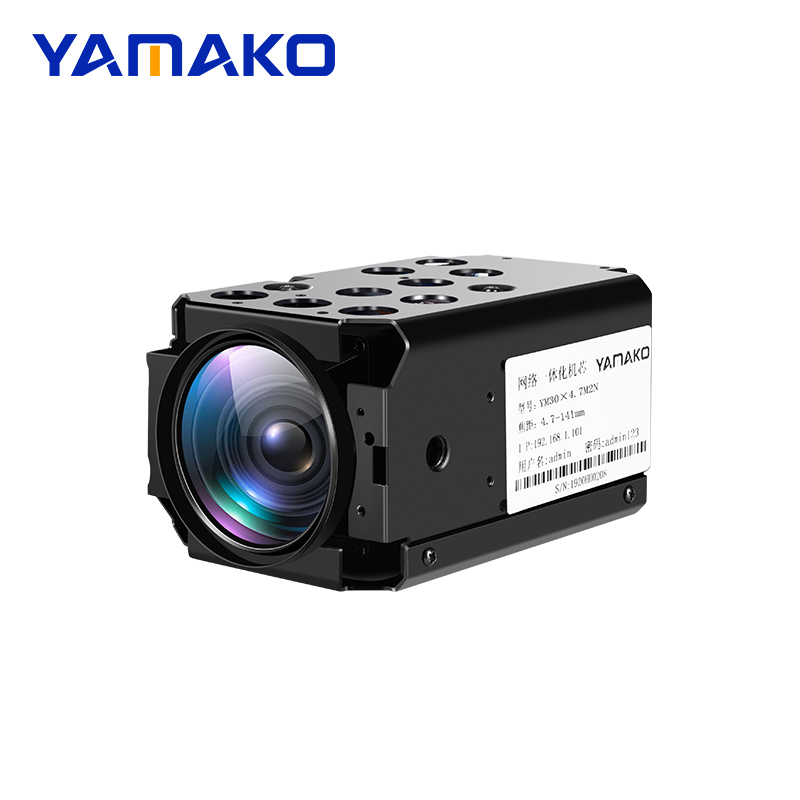
山田光学:一体化机芯在机器人领域的创新应用
《嵌入式机电一体化系统设计与实现》读后感
智慧园区一体化管理平台功能
安消一体化平台建设方案
什么是机电一体化?它有哪些应用?
室内外一体化定位技术的普及和应用
水肥一体化设备运维管理平台有什么功能
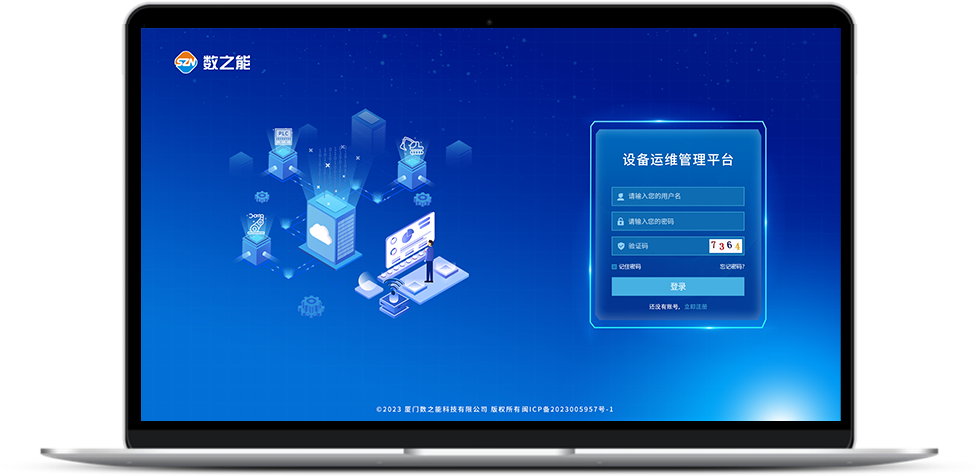
高精度时频一体化设备-陕西风雷仪表
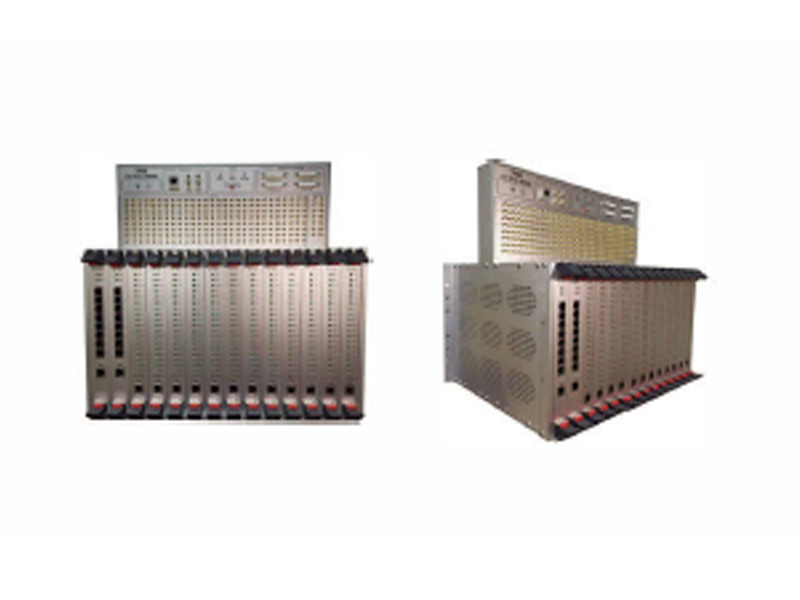
什么是通感算一体化?通感算一体化的应用场景
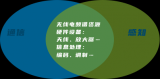
乘用车一体化电池的发展现状和未来趋势
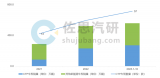
评论